Introducción
La tecnología de fabricación aditiva (FA) surgió como una técnica de prototipado rápido. Aunque inicialmente se centró en el procesamiento de polímeros con técnicas como la estereolitografía (SLA) y la modelación por deposición fundida (MDF) en la década de 1980, posteriormente se extendió al procesamiento de metales, cerámicas y compuestos [1, 2].
La FA surgió de la mente de dos ingenieros químicos que desarrollaron un juguete para su hija, el cual depositaba una capa de polímero capa por capa [3]. Ellos patentaron su invención en 1986 y, unos años después, fundaron una de las compañías de fabricación aditiva más exitosas hasta la fecha, Stratasys. Para la década de 1990, surgieron desarrollos fundamentales en el procesamiento de metales, introduciendo tecnologías como la fusión selectiva por láser (SLM, por sus siglas en inglés) y la sinterización selectiva por láser (SLS, por sus siglas en inglés) [4, 5]. Cabe destacar que todos estos avances se llevaron a cabo de la mano con universidades y centros de investigación, acelerando significativamente el desarrollo tecnológico.
Los últimos años han experimentado avances significativos en el procesamiento de diversos tipos de materiales [6]. Los fabricantes han ampliado sus carteras de productos para incluir equipos, materias primas y consumibles. Además, se ha llevado a cabo una extensa investigación para indagar en los posibles beneficios de la FA en diferentes campos. Por ejemplo, se han identificado varias oportunidades, como posibles reducciones en costos y plazos de entrega, la posibilidad de soluciones de diseño únicas y la consolidación de múltiples componentes [7].
Sin embargo, la fabricación aditiva no es aún una tecnología de plug-and-play. Se requiere un conocimiento exhaustivo del material a procesar, parámetros de procesamiento adecuados y condiciones ambientales, entre otros factores [5]. Además, la FA también demanda trabajo e investigaciones sustanciales para obtener diversas certificaciones y estándares necesarios en diferentes campos para demostrar su eficiencia en la fabricación de piezas complejas y asegurar su repetibilidad y calidad [7].
La tecnología MDF es una de las tecnologías más ampliamente utilizadas, principalmente debido a su facilidad de instalación y operación [8-11]. En contraste, la fabricación de metal requiere equipos más costosos y complejos. La fabricación aditiva de metal se clasifica en deposición de energía dirigida (DED) [12-14] y fusión de lecho de polvo (PBF, por sus siglas en inglés) [15, 16]. Dentro de la DED, la fabricación aditiva con arco de alambre (WAAM) [17-20] se destaca por su versatilidad y capacidades de procesamiento. Por otro lado, en la PBF, la fusión de lecho de polvo basada en láser (LPBF, por sus siglas en inglés) se considera la mejor opción para la fabricación de piezas con una complejidad geométrica significativa y un tamaño reducido [21]. LPBF utiliza un láser de potencia media (100-400 W) para fundir polvos metálicos, los cuales experimentan cambios de fase en microsegundos, generando ciclos repetitivos de fusión y solidificación que producen microestructuras sin precedentes [22, 23].
Una de las características destacadas es la formación de granos más pequeños en comparación con el mismo material procesado de manera convencional. Además, se crean micropiletas fundidas dentro de las cuales se forman subgranos celulares. Estas peculiares microestructuras dan lugar a diferentes propiedades mecánicas [24, 25], que requieren múltiples pruebas mecánicas para evaluar su idoneidad para su aplicación como elementos estructurales de carga o en entornos dinámicos sujetos a cargas variables.
En cuanto a las propiedades mecánicas, se ha observado una mejoría significativa en diversas propiedades mecánicas de las muestras fabricadas mediante LPBF. Por ejemplo, Röttger et al. [26] compararon las propiedades mecánicas de muestras fabricadas con acero austenítico 316L procesado mediante la tecnología SLM y las de muestras fabricadas mediante un proceso de fundición regular. Las pruebas de tracción revelaron un aumento aproximado del 20 % en la resistencia a la tracción en las muestras producidas mediante FA. Además, Kurzynoswki et al. [27] realizaron pruebas de tracción en muestras de acero inoxidable 316L fabricadas mediante SLM con diferentes parámetros de proceso y compararon los resultados con las propiedades mecánicas de muestras elaboradas a partir de planchas laminadas AISI SS316L. Se observó una mejora en la resistencia a la fluencia y el módulo de Young después de las pruebas. Asimismo, Liverani et al. [28] estudiaron el efecto de diferentes parámetros de proceso en la microestructura y propiedades mecánicas de muestras producidas mediante SLM. Después de realizar pruebas de tracción y fatiga, los resultados experimentales sugirieron la posibilidad de una mejora en la resistencia última a la tracción y el porcentaje de elongación de las muestras en comparación con las muestras AISI316L fabricadas convencionalmente.
En otro estudio, Liverani et al. [29] reportaron una resistencia a la fluencia (σY ) de alrededor de 400 MPa y una resistencia última a la tracción (σUTS) entre 500 y 600 MPa. Larimian et al. [30] obtuvieron resultados similares, resaltando el efecto de los parámetros de procesamiento y la estrategia de escaneo en la resistencia resultante. Los valores más bajos y altos de σY fueron 148 y 462 MPa, respectivamente, mientras que los valores de σUTS rondaban entre 178 y 584 MPa.
Cabe destacar que la obtención de muestras con la máxima densidad relativa es esencial para lograr una respuesta mecánica adecuada. En cuanto a la respuesta a la compresión, Güden et al. [31] examinaron el impacto de la tasa de deformación durante las pruebas de compresión en acero inoxidable 316L fabricado mediante fusión selectiva por láser. Ellos reportaron tensiones verdaderas de compresión últimas en el rango de 1400 a 1600 MPa, con velocidades de deformación que oscilaban entre 2800 a 3250 s−1, respectivamente. Li et al. [32] desarrollaron un modelo constitutivo para predecir la relación de compresión esfuerzo-deformación del acero inoxidable 316L procesado por LPBF y compararon los resultados con muestras fabricadas utilizando equipos SLM a diferentes velocidades de escaneo. Se obtuvo un esfuerzo de compresión promedio de 1400 MPa y una deformación del 23 %.
Por lo tanto, este estudio se enfoca en evaluar la respuesta a la tracción y compresión del acero inoxidable 316L fabricado utilizando la tecnología de fusión de lecho de polvo con láser en condiciones específicas. Dado el papel fundamental que desempeña la microestructura en la comprensión de las propiedades mecánicas resultantes, se lleva a cabo un análisis exhaustivo tanto de las características microestructurales como de la densidad relativa.
2. Materiales y métodos
El material utilizado para fabricar las muestras fue acero inoxidable 316L, cuya composición química nominal se detalla en la Tabla 1.
El proceso de fusión selectiva por láser se llevó a cabo utilizando una máquina Concept Laser (MLAB 200R) equipada con un láser de fibra de 200 W (Nb:YAG) Los polvos se depositaron sobre una placa de soporte de acero inoxidable 316L con un grosor de 16 mm. Los parámetros de procesamiento incluyeron una potencia láser de 160 W, una velocidad de escaneo de 800 mm/s, un espaciado de trama de 60 μm y un espesor de capa de 30 μm (Figura 1). Estos parámetros se seleccionaron para maximizar la densidad relativa, reduciendo la porosidad de las muestras impresas.
Se fabricaron especímenes con geometría plana en forma de hueso de perro, de acuerdo con la norma ASTM E8/8M-21, y se produjeron muestras prismáticas de dimensiones 16×10×7 mm utilizando una estrategia de escaneo en zigzag con una rotación de 67° después de la deposición de cada capa. Tras la fabricación, las muestras fueron cortadas con precisión de las plataformas de construcción mediante mecanizado por descarga eléctrica con alambre.
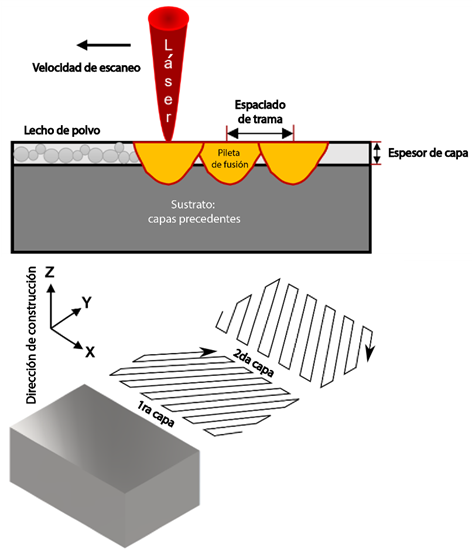
Figura 1 Representación esquemática del proceso de fusión de lecho de polvo basado en láser, identificando los parámetros clave de procesamiento y la estrategia de escaneo
Para la inspección metalográfica, las muestras fueron sometidas a un proceso inicial de rectificado plano utilizando papel de carburo de silicio, desde 120 hasta 2000 granos, para lograr un pulido preliminar de la superficie de la muestra. Posteriormente, se llevó a cabo un paso de pulido fino utilizando alúmina, seguido de pasta de diamante. La microestructura del material fue revelada mediante un grabado químico, que implicó la inmersión en una solución de Aqua regia (20 ml de HNO3 y 60 ml de HCl) durante 30 segundos. La morfología de la superficie del material fue examinada mediante microscopía óptica (MO) (MEIJI IM 7200).
Las microfotografías de MO fueron posteriormente procesadas y analizadas utilizando el software Fiji (institutos nacionales de salud, EE. UU.) para determinar las características microestructurales y evaluar la porosidad mediante análisis de imagen. Se llevaron a cabo pruebas de tracción siguiendo la norma ASTM E8/8M-21 y utilizando una máquina universal de ensayos de tracción (Instron 3368, Zwick) equipada con una celda de carga de 50 kN, una velocidad de 2 mm/min hasta la fractura y una longitud de calibre de 50 mm con un extensómetro. De acuerdo con la norma ASTM E9-09, se realizaron pruebas de compresión en especímenes prismáticos. Cuatro especímenes prismáticos fueron sometidos a ensayos, y se documentaron los resultados promedio. Además, el módulo elástico se calculó de acuerdo con la norma ASTM E111.
Se realizaron mediciones de microdureza utilizando un durómetro Vickers (METKON DUROLINEM) con una fuerza de 500 g y un tiempo de permanencia de 10 segundos, siguiendo la norma ASTM E384.
Los valores medios se determinaron basándose en cinco mediciones y posteriormente se reportaron.
3. Resultados y discusión
La Figura 2 muestra los especímenes de prueba fabricados. Es importante destacar que tanto el polvo como la placa de soporte deben ser fabricados con el mismo material para garantizar una adhesión óptima entre ambos componentes y evitar errores o desplazamientos durante el proceso de fabricación aditiva.
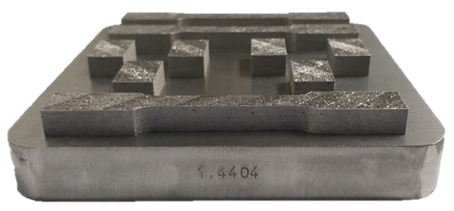
Figura 2 Muestras fabricadas de forma aditiva para la evaluación de la microestructura y las propiedades mecánicas. Dimensiones de la placa base: 100 × 100 × 16 mm
Las imperfecciones superficiales observadas mediante microscopía óptica fueron evaluadas para determinar la densidad relativa (Figura 3). Utilizando el análisis de imagen, se obtuvo una densidad relativa del 99.7 %.
Lograr piezas con una densidad relativa superior al 99 % es imperativo para obtener propiedades mecánicas comparables a las piezas fabricadas mediante métodos convencionales. Como se ilustra en la Figura 3, persisten porosidades circulares, atribuidas a la retención de gas dentro del polvo metálico [33]. Sin embargo, la mayor parte de la superficie carece de poros, asegurando el rendimiento adecuado de las muestras fabricadas y validando la selección adecuada de los parámetros de procesamiento designados.
3.1. Análisis de la microestructura
La Figura 4 muestra el ensamblaje tridimensional de microfotografías ópticas obtenidas en diferentes planos de fabricación. Se puede apreciar que la estrategia de escaneo utilizada es discernible en el plano superior, mientras que en los planos laterales se observa la superposición de micropiletas fundidas. La Figura 5a ofrece una vista más detallada del arreglo de pozos fundidos, indicando una profundidad promedio de aproximadamente 50 μmμm y una extensión de 140 μm. Además, la Figura 5b proporciona un examen más cercano de un pozo fundido, revelando la presencia de subgranos celulares, en concordancia con hallazgos de investigaciones previas [34-37].
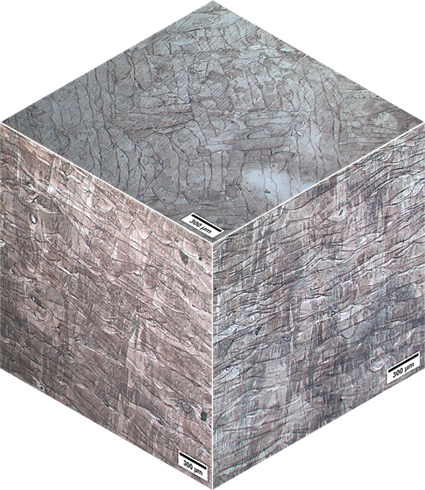
Figura 4 Ensamblaje tridimensional de microfotografías ópticas del acero inoxidable 316L procesado mediante LPBF
Se pueden distinguir granos celulares dentro del pozo fundido (Figura 5b); estos subgranos surgen debido al alto gradiente térmico y a la velocidad de solidificación [38]. En la generación capa por capa del proceso de fusión-solidificación, el pozo fundido experimenta una ligera deformación atribuida a tensiones residuales [39, 40]. La estrategia de escaneo contribuye aún más a la deformación del pozo fundido; la rotación del ángulo de impresión modifica el gradiente térmico, modificando consecuentemente la geometría de los micropozos fundidos.
3.2. Respuesta mecánica
La Figura 6 ilustra la curva de esfuerzo-deformación del acero inoxidable 316L sometido a una prueba de tracción. El esfuerzo de cedencia fue de 512.32 ± 7.84 MPa, el esfuerzo último de tracción fue de 634.80 ± 11.62 MPa y la deformación antes de la ruptura fue del 31.61 ± 1.40 %.
Como se muestra en la Figura 6, el material presenta una respuesta dúctil caracterizada por una notable deformación más allá de la región del límite elástico. Además, la resistencia a la fluencia determinada para el material es aproximadamente de 512.32 MPa, correspondiente a una deformación ingenieril del 0.05. Asimismo, la resistencia última a la tracción es de alrededor de 634.80 MPa a una deformación de aproximadamente 0.32. Para el grupo de especímenes fabricados, el módulo elástico se determina en aproximadamente 229.12 ± 2.14 GPa.
Además, una vez que inicia la deformación plástica, se observa una clara etapa de endurecimiento por deformación estable, seguida de una región de estrangulamiento que conduce a la fractura del espécimen. Aunque la respuesta dúctil está asociada a la ausencia de porosidad, es crucial señalar que, en casos de baja densidad relativa, el material tiende a fracturarse de manera frágil [41]. Esto se atribuye a la presencia de defectos como gas atrapado, piscinas de fusión inestables o fusión insuficiente [42].
La Figura 7 ilustra el estrangulamiento que ocurre en la muestra antes de la fractura. El estrangulamiento y la reducción de área observados son indicadores típicos de la respuesta dúctil exhibida por el material probado. Además, cabe destacar que la fractura se produce a un ángulo de aproximadamente 45°.
El mecanismo de falla del acero inoxidable 316L fabricado mediante fabricación aditiva puede estar vinculado a la fractura por coalescencia de microhuecos. Este fenómeno ocurre cuando el material contiene pequeños poros o inclusiones que crecen y se fusionan bajo esfuerzo de tracción, generando microfisuras internas.
La Figura 8 ilustra la respuesta a la compresión de las muestras de acero inoxidable fabricadas mediante aditivos. La resistencia a la compresión (1511.88 ± 9.22 MPa) es mayor que la resistencia a la tracción (634.80 ± 11.62 MPa). Esta diferencia se atribuye principalmente al endurecimiento por deformación y a las tensiones residuales [39], [43]. Como se muestra en la Figura 8, cuando la tensión supera los 500 MPa, el material experimenta un proceso de endurecimiento. Este endurecimiento por deformación confiere al material la capacidad de resistir elevados niveles de tensión antes de su eventual falla. Además, la estructura cristalina del acero inoxidable austenítico (FCC) generalmente presenta planos de átomos que muestran una mayor facilidad para deslizarse entre sí bajo fuerzas de corte (como en la compresión) en comparación con ser separados bajo fuerzas de tracción. En otras palabras, la estructura cristalina del acero inoxidable 316L muestra una mayor resistencia a las fuerzas de compresión y corte.
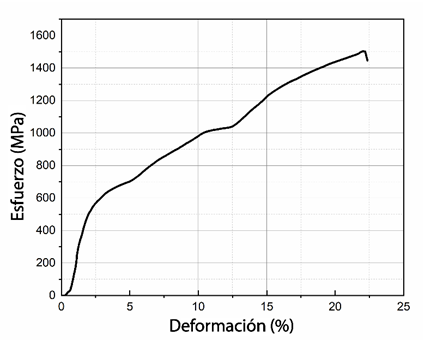
Figura 8 Respuesta a la compresión del acero inoxidable 316L fabricado mediante fusión selectiva por láser (LPBF)
El material experimenta deformación al someterse a esfuerzo compresivo, lo que conduce al endurecimiento por deformación. En consecuencia, se evaluó la dureza antes y después de la prueba de compresión (Figura 9).
La microdureza inicial fue de 206.24 ± 11.96 HV0.5 en la condición de fabricación. Después de la prueba de compresión, la microdureza aumentó a 253.32 ± 11.12 HV0.5.
La Figura 10 ilustra la deformación producida después de la prueba de compresión, mostrando claramente la deformación de las piletas fundidas. El proceso de compresión actúa como un tratamiento de endurecimiento por deformación. Se puede observar una deformación de las piletas fundidas, generando un tratamiento de trabajo en frío. Internamente, los granos se comprimen, reduciendo su tamaño y aumentando la dureza. Es importante destacar que ha habido un aumento del 23 % en la microdureza.
La Tabla 2 resume la respuesta mecánica del acero inoxidable 316L fabricado mediante fabricación aditiva. Los resultados obtenidos en este estudio concuerdan con los reportados en la literatura [24], [26], [28], [30], [32], [41]. Por lo tanto, es plausible afirmar que la tecnología SLM está alcanzando la madurez, lo que indica la necesidad de esfuerzos para establecer estándares para su aprobación.
Tabla 2 Propiedades mecánicas del acero inoxidable AISI 316L fabricado mediante procesos de fabricación aditiva
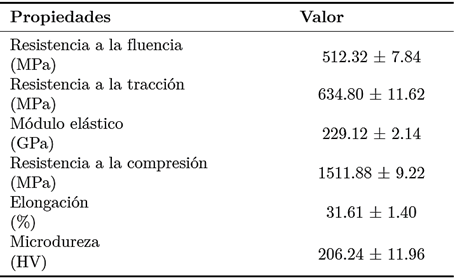
Las respuestas a tracción y compresión del acero inoxidable 316L procesado mediante SLM mostraron un rendimiento mecánico superior al de su contraparte procesada convencionalmente [24]. Esta resistencia aumentada se atribuye a la microestructura. Dentro de la pileta fundida, se observaron subgranos de menos de un micrón debido al alto gradiente térmico generado por la interacción cíclica del láser con los polvos metálicos.
La fabricación aditiva ofrece numerosas ventajas en términos de diseño y flexibilidad. No obstante, para su aplicación fiable en contextos de ingeniería, es imperativo realizar investigaciones exhaustivas sobre sus propiedades mecánicas, abarcando variaciones en los parámetros del proceso y las estrategias de escaneo.
4. Conclusiones
En este estudio se ha evaluado la respuesta a la tracción y compresión del acero inoxidable 316L procesado con láser. Las principales conclusiones extraídas se detallan a continuación:
La selección adecuada de parámetros de procesamiento es esencial para obtener piezas con porosidad mínima. A una mayor densidad relativa le corresponden propiedades mecánicas mejoradas, debido a que los poros actúan como concentradores de tensiones, reduciendo así la resistencia mecánica. En este estudio se logró una densidad relativa del 99.7 %.
La fabricación aditiva ofrece la oportunidad de controlar la microestructura, permitiendo la personalización de propiedades mecánicas específicas, como las dimensiones de la pileta fundida o la densidad relativa. Es válido destacar que la estrategia de escaneo y la geometría de la muestra afectan el gradiente térmico, influyendo así en la microestructura resultante. Se requiere llevar a cabo investigaciones adicionales sobre estos parámetros y su impacto en las propiedades mecánicas.
Las pruebas de tracción y compresión revelaron el comportamiento dúctil del material obtenido de forma aditiva. En el caso de la prueba de tracción, se registraron los siguientes resultados: una resistencia a la fluencia de 512.32 ± 7.84 MPa, una resistencia última a la tracción de 635 MPa y un módulo elástico de 229.12 ± 2.14 GPa. Además, la curva de esfuerzo-deformación ilustra la respuesta dúctil del material, atribuida a una alta densidad relativa y a una baja porosidad.
Se observó una resistencia a la compresión de aproximadamente 1511.88 ± 9.22 MPa en las pruebas correspondientes. La diferencia significativa entre la respuesta a tracción y compresión se podría atribuir a la presencia de tensiones residuales producidas durante el proceso de fabricación y a un mecanismo de endurecimiento por deformación causado por la deformación de la muestra, confirmado por la distorsión observada en las piletas fundidas después de realizar la prueba de compresión.
La prueba de microdureza corroboró un incremento de alrededor del 23 % en los resultados obtenidos después de someter una muestra a una prueba de compresión, en contraste con los resultados de las muestras en su estado original de fabricación.