Introducción
La cangahua, es una roca blanda y porosa producto de la diagénesis parcial del material volcánico explosivo fino proveniente de flujos piroclásticos de menor tamaño al de la ceniza (2mm) (Vera & López, 1992). Este tipo de suelo generalmente se compone de vidrio volcánico alterado, cuarzo y feldespato, definiéndose como laminaciones de ceniza, lapilli y suelo limo arenoso compacto, cuya característica es su color amarillento (Boada Espinoza, 2020), ver figura 1.
Este material únicamente existe en formaciones piroclásticas de hace aproximadamente 11.500 años, que en su mayoría, fueron redistribuidas por el viento creando depósitos (Zebrowski, Quantin, & Germán, 1996).
A lo largo del valle interandino, se ubican cientos de centros volcánicos que datan de hace aproximadamente 5,3 millones de años. Se sabe que los volcanes más activos en este periodo de tiempo han sido: El Soche, Chachimbiro, Cerro Negro, Imbabura, Mojanda, Ninahuilca, Pululagua, Chacana, Antisana, Cotopaxi, Tungurahua, Quilotoa, Guagua Pichincha, Sangay, Chimborazo, Cayambe y Chalupas, entre otros (Zebrowski et al., 1996).
Con este antecedente, se afirma que en el Ecuador la cangahua es abundante. El área total que ocupa este suelo es de aproximadamente 181.487 ha, repartidas entre afloramientos superficiales (13.164 ha) y a profundidades de 60cm (168.325 ha) (Jimenes, Loayza, & Metzler, 2018).
En poblaciones rurales cercanas a las zonas de influencia de los centros volcánicos mencionados, se utiliza este suelo como materia prima en sistemas de autoconstrucción. Ejemplo de esto son las viviendas construidas con cangahua moldeada en forma de bloques (ver figura 2), que se han colocado en las dos caras de la pared y rellenado con barro y trozos de cangahua (J. Serrano Acuña, 2020), (Sutter, 1984).
En Ecuador la construcción con tierra es parte de la cultura del país. Su uso data desde antes de la colonia, existiendo indicios de su manejo como materia prima desde 1200 A.C. (“Diario Correo | El Diario de Todos,” 2017).En promedio en la sierra ecuatoriana el 12% de construcciones son de tierra, material más utilizado después del ladrillo y bloque, este porcentaje en algunas provincias alcanza hasta el 35% (J. R. Serrano Acuña, 2020). A lo largo de los años se ha dejado de aplicar este sistema constructivo.
La tendencia actual del país, es optar por materiales altamente comercializados como el cemento y el acero (Paredes Zapata, 2011), cuya producción es causante de grandes cantidades de emisiones de gases de efecto invernadero a la atmósfera. El cemento aporta aproximadamente el 8% de las emisiones mundiales de CO2 (CORDIS, n.d.) y el acero un 5% (Temple, 2018). Las construcciones convencionales con concreto armado o tabique cocido (ladrillo) son responsables en un 39% de emisiones de gases invernadero (Elena Solano Meneses, Antonio, & Moretti Testa, 2021).
Es preciso entonces, en concordancia con la alta disponibilidad y fácil acceso a un recurso como es el suelo, desarrollar un mampuesto que se adapte a la normativa vigente de construcción con tierra (Ministerio de vivienda construcción y saneamiento, 2017).
Una de las características más importantes de la cangahua para el desarrollo de esta investigación es su composición granulométrica. En los estudios realizados de se le identifica como un limo arenoso (ML) o areno limoso (SM), (15%) arcilla, (55%) limo y (30%) arena, de consistencia poco plástica (Chimbo, 2017).
Al tratarse de un material con poca o nula plasticidad, es necesario realizar su estabilización para poder utilizarlo en la construcción (Gaibor & Guano, 2012). Este proceso puede ser de dos tipos: mecánico y/o químico. La estabilización mecánica depende de la granulometría, el grado de compactación y la humedad, mientras que la química se realiza mediante la adición de aglomerantes. Se puede mejorar la granulometría con la mezcla de suelos naturales utilizando una combinación de suelos binarios o añadiendo cierta cantidad de fibras naturales (Lobato Chavez, 2019), como son los residuos agroindustriales o paja de cereales. Estos materiales poseen una mínima cantidad de energía incorporada en sus fases de adquisición, procesamiento y transporte (Borsani, 2011).
En esta investigación, para potenciar el uso de la cangahua en la construcción tradicional y restauración patrimonial, se realizaron bloques a base de un suelo binario con cangahua y arcilla, estabilizados de forma mecánica y química con paja de cebada y cal hidratada, respectivamente.
El diseño para la dosificación de los bloques inició con la preparación de varias mezclas de morteros con cangahua, cal y arcilla, que se sometieron a ensayos de compresión simple. Con el objetivo de evaluar la interacción entre estos componentes. Los resultados se ingresaron a un modelo estadístico experimental mediante un diseño de mezclas de vértices extremos (Silva, Rojas, Gamboa, Gordillo, & Delvasto, 2019) en el software Minitab, en el que se impusieron resistencias mecánicas de diferentes normativas referentes a la fabricación de bloques. La validación de este modelo corresponde a la obtención de esas resistencias que, al ser similares, fueron la base para la elaboración de los bloques en los que se adicionó paja conforme a la recomendación de la Norma E.080 Diseño y Construcción con Tierra Reforzada (Ministerio de vivienda construcción y saneamiento, 2017).
Metodología
Metodología diseño de mezclas
La figura 3 detalla la metodología de diseño de mezclas para morteros (junto con sus proporciones detalladas en la tabla 1), elaboración de morteros y adobes según sus respectivas normas.
Materiales
Cangahua: Se recolectaron muestras de cangahua en la provincia de Imbabura y Pichincha. Las formaciones de Cangahua donde prevalecen materiales de origen volcánico en la provincia de Imbabura se localizan en las parroquias: San Francisco, Caranqui, San Antonio, La Esperanza y Angochagua. En Pichincha se pudo obtener en el sector de Tabacundo. Estas localidades se encuentran influenciadas por la presencia de los volcanes Chachimbiro, Imbabura, Mojanda y Cayambe (ver figura 4).
De acuerdo con los resultados de los ensayos granulométricos, la cangahua extraída en los sitios mencionados se identifica como suelo de tipo SM (areno limoso de baja plasticidad) y ML (limo arenoso de baja plasticidad).
Cal: En Ecuador únicamente se puede conseguir cal hidratada para uso en construcción. Se utilizó cal de producción artesanal “La Paz” y de producción industrial “Incoreg”. Estos tipos de cal se producen en zonas cercanas a donde se ubican las formaciones de cangahua. Además, un estudio sobre las propiedades físicas de morteros con adiciones de cal comercializada en Ecuador, concluye que, las muestras con valores promedios de resistencia a la compresión simple más altos se obtuvieron con los tipos de cal mencionados (Viera & Acero, 2022).
Arcilla: Considerando la baja plasticidad de la cangahua se optó por añadir arcilla. La adición de arcilla en porcentajes entre el 2% y 8% genera un aumento de la resistencia en morteros con presencia de cal hidratada (Altamirano, 2019).
En el Ecuador este material no es comercializado. En la provincia de Imbabura, en sitios aledaños a donde se extrajo la cangahua se localizaron afloramientos de suelo arcilloso. Con la finalidad de comprobar su plasticidad, se utilizó la prueba del “rodillo” (Ministerio de vivienda, 2010). La longitud resultante fue de 25cm. El valor mínimo recomendado para la elaboración de adobes es de 15cm (Brito Del Pino, 2021). Se utilizó este material en todas las muestras.
El valor máximo añadido en volumen de cal en morteros fue 20% (Herbas Chircca & Nolasco Juarez, 2021), (Cáceres Vásquez, 2017), (Altamirano Carrasco, 2018), (Quiroz Casanova, 2020), (Garcia Huaynacaqui, 2018), (Quiteño, 2015), (Dobbertin Saldaña & Pérez Rodríguez, 2019). Para mantener un equilibrio, se optó por definir este porcentaje como límite máximo tanto de la cal como de la arcilla.
Diseño de Experimentos
La resistencia a comprensión mínima según la normativa peruana E.080 para adobes es de 1 MPa o 10.2 kg/cm2. Para el diseño de mezclas de mortero se utilizó este valor como referencia.
La cangahua al encontrarse naturalmente como un suelo duro (roca blanda), se realizó su extracción y procesamiento mediante maquinaria. Fue necesaria la trituración del material para obtener un material fino y homogéneo. La cangahua triturada se mezcló con agua para ver su comportamiento plástico al corto tiempo, dando como resultado un suelo suelto no consolidado. Por esta razón, se optó por dejar reposar el suelo en agua de tal forma que permanezca saturado. A este procedimiento se lo conoce como dormir el barro (Ministerio de vivienda construcción y saneamiento, 2017). La Norma E.080 sugiere que el tiempo de saturación debe ser de mínimo 2 días, sin embargo, se observaron resistencias mayores en las muestras donde el proceso se mantuvo por 7 días.
Las muestras de mortero fueron realizadas manualmente con el fin de brindar homogeneidad. Se depositaron en cubos de 50 mm de arista según la normativa NTE INEN 488 (INEN, 2009). Los cubos permanecieron 30 días en un lugar seco, cubiertos del viento y sol antes de ensayarlos.
En la tabla 1 se presentan las condiciones para el diseño experimental. El objetivo es obtener la máxima resistencia a la compresión. La resistencia está relacionada con las proporciones de cangahua, cal y arcilla.
Tabla 1: Proporciones de mezclas del diseño de experimentos.
Nomenclatura | Orden estadístico | Arcilla | Cal | Cangahua |
---|---|---|---|---|
M1 | 1 | 0.00 | 0.00 | 1.00 |
M2 | 2 | 0.20 | 0.00 | 0.80 |
M3 | 3 | 0.00 | 0.20 | 0.80 |
M4 | 4 | 0.00 | 0.10 | 0.90 |
M5 | 5 | 0.10 | 0.00 | 0.90 |
M6 | 6 | 0.10 | 0.10 | 0.80 |
M7 | 7 | 0.07 | 0.07 | 0.87 |
M8 | 8 | 0.03 | 0.03 | 0.93 |
M9 | 9 | 0.13 | 0.03 | 0.83 |
M10 | 10 | 0.03 | 0.13 | 0.83 |
Se desarrolló un diseño de mezclas de vértices extremos (Chiluiza Toapanta, 2020). El modelo implica solo una región de la experimentación simplex debido a las restricciones del porcentaje de participación de los componentes, mínimo 80% para cangahua y máximo 20% para cal y arcilla.
El diseño de vértices generó 10 mezclas experimentales, de los cuales 3 son vértices, 3 puntos de doble combinación y 4 puntos centrales como se evidencia en la figura 5. Al ser las mezclas asignadas de esta forma, se mide como resultado la resistencia a la compresión simple.
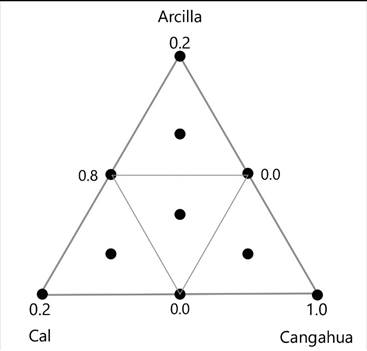
Figura 5: Diseño simplex restringido en proporciones para los componentes de Cangahua, cal y arcilla.
Con la finalidad de simplificar la visualización de los componentes considerados, el programa MINITAB proporciona esta imagen en la que se pueden apreciar las restricciones mencionadas, que coinciden con un triángulo dentro de la región del análisis simplex y que posteriormente nos generará una superficie de respuesta (Hernández Cruz, 2007).
Resultados del diseño de mezclas
La resistencia a la compresión a los 30 días de las muestras oscila entre 1.36kg/cm2 hasta 41.58kg/cm2 para las mezclas que se realizaron con la cal “La Paz” mientras que para la cal “Incoreg” se obtuvieron valores similares entre 0.43kg/cm2 y 41.58kg/cm2.
Con el fín de medir estos efectos y valores se ingresaron al programa las resistencias obtenidas con cada dosificación y en la tabla 2 se muestra el análisis de varianza, ajustado a un modelo cuadrático utilizando la técnica de regresión de mezclas. El análisis cumple con los supuestos sobre el error de modelo, dando como resultado ajustado un valor R2 = 86.00% considerandose un valor alto tomando en cuenta la variabilidad de este tipo de ensayos. El valor de R2 demuestra en qué porcentaje se ajustan o explican los factores de acuerdo al modelo planteado (Larrea Molinari, 2017). Conjuntamente se evidencia el valor de significancia (p-valor) de un 0.036, valor menor al máximo establecido (p-valor = 0.05), mismo que indica la significancia en el modelo y delimita la región de aceptación (Erazo Sánchez, 2019), proporcionando como resultado favorable la interacción de segundo orden Cal*Cangahua. Definido esto, podemos argumentar que los términos siguientes contribuyen a la explicación de la resistencia a la compresión presentada por la mezcla.
Tabla 2: Análisis de varianza para Resistencia a la compresión (R2 = 86.00%).
Fuente | GL | Suma cuadrados | Cuadrados medios | F | P-Valor |
---|---|---|---|---|---|
Regresión | 3 | 2180.6 | 726.88 | 12.29 | 0.006 |
Lineal | 2 | 1753.2 | 190.38 | 3.22 | 0.112 |
Cuadrático | 1 | 427.4 | 427.38 | 7.23 | 0.036 |
Cal*Cangahua | 1 | 427.4 | 427.38 | 7.23 | 0.036 |
Error residual | 6 | 354.9 | 59.15 | - | - |
Total | 9 | 2535.5 | - | - | - |
En la figura 6 se observa que las mayores resistencias se obtuvieron en muestras donde no se incluyó cal en su composición (M1, M2 y M5). La combinación cangahua-cal hidratada presenta las menores resistencias (M3 y M4). Al adicionarse arcilla la resistencia tiene un incremento mínimo (M2 y M5), con resultado similar a la mezcla M1 compuesta únicamente por Cangahua. Esto indica que, la adición de arcilla en porcentajes menores a 20% no genera cambios significativos en la resistencia de la Cangahua.
En la figura 7 se presenta el gráfico de contornos de la resistencia a compresión generado por el programa MINITAB, que muestra de manera más clara y predecible el comportamiento que tienen los componentes de la mezcla una vez ingresadas las resistencias obtenidas de cada dosificación. Existen infinitas interacciones entre las variables que nos llevarán a un resultado de resistencia. De forma general se observa que la región cercana al vértice superior, vértice derecho y punto medio entre ambos, comprenden las combinaciones con mayor posibilidad de alcanzar una resistencia superior a 40kg/cm2. En la región más próxima el vértice izquierdo, donde existe mayor interacción con la cal, las resistencias de las combinaciones que se generen serán menores.
Comprobación Experimental - diseño de mezclas
Para una mejor compresión de los resultados estadísticos, se procedió a determinar combinaciones de los componentes cangahua, cal y arcilla, que permitan obtener valores predictivos de resistencia. Los valores se encuentran referenciados en la figura 8 y están comprendidos en el diseño simplex. Las mezclas realizadas con estos serán evaluadas bajo los mismos criterios que las muestras iniciales.
Las dosificaciones establecidas para determinar si el comportamiento de los componentes está comprendido y explicado mediante el análisis de varianza se denominarán “Muestra Objetivo” (MO). Según las normativas correspondientes serán las siguientes:
MO1: Normativa peruana E.080, establece resistencia mínima para un adobe de 10.2kg/cm2, ver figura 8.
MO2: Normativa ecuatoriana NEC-SE-Vivienda, determina que la resistencia mínima para un Bloque perforado de arcilla es de 30kg/cm2, ver figura 9.
Estos valores son menores a la resistencia máxima obtenida de las mezclas (M5=41.5kg/cm2), es decir, se encuentran dentro del área de estudio (figura 7), por lo que pueden generarse nuevas dosificaciones que se ajusten a las “MO”.
En las figuras 8, 9 y 11, se observan las restricciones de cada variable: alto, indica el máximo contenido del componente que se añadirá en la mezcla y bajo el mínimo. Act, muestra el porcentaje óptimo de participación necesario para obtener la resistencia establecida Obj. Esto es resultado de la intersección de las funciones que representan el comportamiento de la cangahua, arcilla y cal con la función objetivo.
Una vez determinadas las dosificaciones de los componentes (Act), se realizaron las mezclas correspondientes para determinar su resistencia a la compresión. Los resultados se compararon con las “MO” antes mencionadas.
La resistencia obtenida fue superior al objetivo en ambos casos (ver figura 10), pero muy cercanos al valor original con una variación máxima de 4.71kg/cm2. Demostrando que, con un valor R2 = 86.00% del análisis de varianza, se explica la interacción de las variables cangahua, cal y arcilla. Esto se comprobó mediante los resultados del diseño experimental.
Elaboración de Adobes
La elaboración de adobes se basa en la normativa peruana E.080. Se establecen dimensiones de 40x18x10 cm aproximadamente. Considerando las dosificaciones objetivo antes planteadas y adicionando la que menciona la normativa ecuatoriana NTE INEN 3066 para mampostería no estructural con una resistencia de 40 kg/cm2 (MO3) (figura 11), y con la incorporación de un porcentaje de paja igual al 5% del peso seco del suelo (Anibal Marcelino Bendezu Barreto, 2019), se elaboraron los adobes para ser evaluados a compresión y flexión.
El suelo con mezclas de cangahua y arcilla se dejó reposar durante 7 días en agua, posterior a este tiempo se adicionó cal hidratada “La Paz” y paja (relación 2:1 de suelo-paja) y con una longitud de 5cm. Se mezcló durante 15 minutos hasta obtener una consistencia homogénea. Los adobes se dejaron secar durante 3 días a la sombra y 27 días más al sol, para poder realizar los ensayos a los 30 días.
Con la adición de paja de cebada se evidenció un ligero incremento en la resistencia a la compresión simple de las dos unidades evaluadas en la figura 10, mientras que, para el caso de la mezcla MO3 que se esperaría un aumento de la resistencia, esta permaneció muy cercana al valor inicial planteado (ver figura 12). Cabe recalcar que esta mezcla no contiene cal y está compuesta de un 86.7% de cangahua y un 13.3% de arcilla como se evidencia en la tabla 1.
Módulo de rotura a flexión
Con la finalidad de determinar si la adición de paja incrementaba la resistencia a flexión en los bloques, se realizaron los ensayos correspondientes según la normativa ASTM C67. Se estableció una muestra “Patrón” compuesta exclusivamente de cangahua para su comparación.
Como expone la tabla 3, la muestra patrón presentó mejores resultados de resistencia a flexión y mayor homogeneidad. Los valores de las muestras MO1, MO2 y MO3 varían considerablemente, esto se asume, es consecuencia de la falta de uniformidad en la distribución interna de la paja en los adobes.
Por otra parte, al realizarse los ensayos se pudo observar que, si bien el adobe patrón presentó una mayor resistencia, su falla fue frágil. En las MO estudiadas la falla fue dúctil, presentándose una deformación al centro del bloque considerable (25mm) (figura 12). Se evidenció que, al fallar el suelo, la paja absorbe la carga produciendo una mayor deformación, manteniendo unido al bloque hasta la finalización del ensayo.
Tabla 3: Resistencia a la flexión.
Resistencia a Flexión (Kg/cm 2 ) | Patrón | MO1 | MO2 | MO3 |
---|---|---|---|---|
1 | 14.99 | 4.59 | 8.56 | 9.17 |
2 | 14.37 | 5.81 | 2.94 | 11.31 |
3 | 16.82 | 2.94 | 3.98 | 3.96 |
Promedio | 15.39 | 4.45 | 5.16 | 8.15 |
Discusión
La resistencia a la compresión de los morteros de cangahua como único material (41.19 kg/cm2) y de los morteros compuestos con cangahua, arcilla y contenido de cal inferior al 10% de tipo La Paz (M6, M7, M8, M9), ver figura 6, son mayores a la resistencia mínima establecida en la normativa peruana E.080 - 2017 de 10.2 kg/cm2 para la elaboración de adobes utilizada como referencia.
La adición de cal en porcentajes mayores al 10% en morteros elaborados con cangahua de tipo ML de baja plasticidad, genera reducción en la resistencia a la compresión simple. Sin embargo, se pudo observar que al incorporar arcilla en las mezclas, existe una mejora significativa de las características mecánicas, pasando de una mezcla M4 con un 10% de cal y 90% de cangahua con resistencia de 1.65kg/cm2, a una mezcla M6 con dosificaciones de 10% de cal, 10% de arcilla y 80% de cangahua con resistencia de 27.41kg/cm2.
El análisis de varianza de R2 = 86.00%, demostró el comportamiento real que tienen los diferentes componentes de la mezcla. Las variaciones mínimas de resistencia entre los resultados obtenidos pueden encontrarse inmersas en la serie de incertidumbres y variables externas que consiguen alterar estos resultados, entre ellas la falta de control de calidad de la arcilla y de la cal que son materiales con características que pueden variar entre cada muestra obtenida.
Una correcta relación limo - arcilla permite una mejora en las características mecánicas mientras más se acerque este valor a la unidad (1:1) (Barrios, Alvarez, Arcos, Marchant, & Rosi, 1986). Al tener la cangahua un alto porcentaje de limo, la adición de arcilla no generó una diferencia considerable en los valores de resistencia ya que se mantuvo la relación mencionada. Esto se evidenció en las mezclas M2 y M5.
La gráfica de contorno de resistencia a la compresión (figura 7) nos permite denotar que las mayores resistencias obtenidas en este estudio son las que menos participación de cal hidratada presentaron y esto es debido a la cantidad de arcilla que tiene la cangahua. Al ser un suelo ML (limo arenoso de baja plasticidad) las muestras M3 y M4 perdieron sus características de resistencia original con respecto a la muestra M1.
A pesar de que la cal “Incoreg” es industrializada, los resultados obtenidos con la cal artesanal “La Paz”, al estar en presencia de arcilla, fueron mayores (figura 6). Demostrando que el uso de la cal “La Paz” es óptimo únicamente cuando se encuentre con un suelo con contenido de arcilla.
La adición de paja generó un aumento mínimo en la resistencia de los adobes MO1 y MO2, mientras que para MO3 este valor se mantuvo. Hay que considerar el hecho de que la diferencia de la geometría de una muestra de mortero y de adobe es significativa, en concordancia con investigaciones existentes donde mencionan que la resistencia depende no únicamente del material, sino de sus dimensiones (Pichazaca, 2020).
No se evidenció incremento en la resistencia a flexión, esto debido a la flexibilidad aportada por la paja, la cual incrementó la capacidad de absorber los efectos de tensión en el adobe y así aumentar la deflexión manteniendo unido al bloque.
Conclusiones
Los adobes elaborados con cangahua, cal, arcilla y paja presentaron características mecánicas acordes a las normativas mencionadas en esta investigación. Pueden ser utilizados en la construcción tradicional de tierra y restauración patrimonial.
Los mayores resultados de resistencia en morteros se obtuvieron al utilizar solo cangahua, así como al añadir arcilla en porcentajes de 10% y 20% en volumen. Estos valores superaron la resistencia mínima requerida para elaboración de adobes en la normativa peruana E.80 (10.2 kg/cm2).
La cal hidratada, tanto de procedencia artesanal como industrial, al ser combinada con cangahua originaria de la provincia de Imbabura reduce la resistencia a la comprensión de los morteros elaborados con estos materiales.
El proceso de molido de la cangahua y el aumento del tiempo de saturación de la misma, ocasiona incrementos de resistencia en los morteros elaborados con este material.
La elaboración de adobes en comparación a los morteros debido a su volumen y dimensiones de ensayo debe tener un cuidado especial ya que se puede alterar su forma al momento del desmoldado por su propio peso, este efecto se pudo controlar al colocar paja de cebada, que mantuvo la estabilidad geométrica del adobe.
La validación de la metodología experimental demuestra que podemos obtener resultados confiables sobre el comportamiento de los elementos de un diseño de mezclas y su interacción entre sí.
Para trabajos futuros, se buscará determinar la resistencia final con dosificaciones determinadas con la metodología experimental para la obtención de mampuestos, lo que implica considerar las características granulométricas de cada material en particular para mejorar su resistencia y comportamiento global. Es de gran importancia aplicar una profunda búsqueda bibliográfica para establecer las restricciones adecuadas y obtener una región de aceptación más real.
Contribución de los autores
En concordancia con la taxonomía establecida internacionalmente para la asignación de créditos a autores de artículos científicos (https://casrai.org/credit/ ). Los autores declaran sus contribuciones en la siguiente matriz: