Introducción
La determinación de costos de producción en las empresas industriales es esencial para conocer la valoración de sus productos y la rentabilidad de las operaciones que se llevan a cabo. También, tiene un valor especial al contribuir con las funciones de planeación y control en lo que se refiere a producción y ventas. Esta determinación de costos es un tema de relevancia que se ha venido desarrollando a lo largo del tiempo. Aunque se presenten nuevos enfoques y prácticas en el estudio de costos (Ruiz-de-Arbulo-Lopez, 2013) el conocimiento del costo unitario de producción es punto de partida relevante para cualquier complemento en el tratamiento administrativo de costos. En la actualidad existen permanentes investigaciones para determinar sistemas de costeo y herramientas apropiadas que ofrezcan información confiable y oportuna para la toma de decisiones de las empresas. Por ejemplo, Villareal y Rincón (2009) presentan el método matricial FHER como una herramienta sencilla de entregar resultados de los costos por procesos. Por su parte, Crespo (2017) evaluó la implementación del sistema de costeo basado en actividades, ABC (por sus siglas en inglés de Activity-Based Costing) para identificar y mejorar la calidad de la información a generar.
En las empresas industriales la información de costos se genera en los sistemas de acumulación que utilizan, donde la exactitud y fiabilidad de la información dependerá de qué tan bien definidos estén estos sistemas. Por ende, los sistemas de acumulación de costos deben ser determinados, de manera que, considerando las características de la empresa, contribuyan a la toma de decisiones en cuanto a, por ejemplo, establecimiento de precios de venta, decisiones de mercadotecnia, entre otras.
En el caso de Ecuador, la industria de ensamblaje tiene características especiales en cuanto a su modelo de actividad. Este tipo de industria apoya la tendencia de sustitución de importaciones, sin embargo, está expuesta a factores externos que influyen directamente su desarrollo, por ejemplo, las políticas de comercio exterior. Estas políticas, como las medidas arancelarias y tributarias, afectan la industria debido a que el principal insumo de partes y piezas, CKD (del inglés Completely Knock Down) que requieren las ensambladoras es importado. El CKD se refiere a la consolidación de componentes, partes o piezas importadas y destinadas al ensamblaje de bienes intermedios y finales. Además, las ensambladoras deben cumplir con un porcentaje mínimo de componente nacional incorporado a sus productos. En este sentido, las empresas de la industria demandan sistemas de costeo que se adecúen a la naturaleza de sus actividades y su entorno, donde la utilidad del sistema de costeo establecido se vea reflejado en la precisión con la que se tomen las decisiones.
Revisión de literatura
El punto de partida del tema es la contabilidad de costos, que tiene conexión con la contabilidad financiera y la contabilidad administrativa. Por una parte, la contabilidad financiera ofrece información histórica a través de los estados financieros elaborados con base en las normas internacionales de información financiera - NIIF y normas internacionales de contabilidad - NIC. Este tipo de contabilidad se enfoca en el suministro de información a usuarios externos, tales como inversionistas, instituciones gubernamentales, bancos y proveedores (Horngren, Datar, & Rajan, 2012). Por otra parte, la contabilidad administrativa genera información para usuarios internos que permite establecer estrategias para lograr los objetivos organizacionales. De ahí, la contabilidad de costos que emerge, presenta información histórica de costos de producción, indispensable para la toma de decisiones, por ejemplo, en la evaluación del desempeño o la determinación de la utilidad en las empresas industriales.
La información sobre costos se muestra como el resultado del desarrollo de diferentes procesos. Desde el punto de vista de la gestión de procesos, estos se clasifican en: estratégicos, operacionales y de apoyo (Bravo, 2008), siendo los procesos operacionales los que se refieren a la producción en las empresas industriales. Los procesos productivos se desarrollan como una secuencia de actividades encargadas de generar y transformar la materia prima, mediante la intervención de mano de obra y máquinas especializadas (Atehortúa & Gómez, 2008). Estos procesos requieren de diferentes recursos, los mismos que generan el costo de producción.
El costo de producción, por lo tanto, se compone de tres elementos: materia prima, mano de obra y costos generales de fábrica. La materia prima constituye los bienes requeridos para la fabricación de los productos; la mano de obra conforma la fuerza física o intelectual del ser humano; y, los costos generales de fábrica incluyen los bienes y servicios complementarios requeridos para la generación del producto (Zapata, 2015).
El costo de producción se puede clasificar en diferentes categorías, según la necesidad que tengan los administradores, así como también, dependiendo del giro del negocio y del objeto de costo (Sánchez Barraza, 2014); sin embargo, dos clasificaciones son esenciales en toda empresa para la obtención de información útil: 1) según su identidad y 2) según su comportamiento.
Los costos por su identidad se clasifican en recursos directos e indirectos. Los recursos directos a diferencia de los indirectos, son aquellos que pueden ser plenamente identificables con el objeto de costo (Ramírez, 2008). Entendiéndose por objeto de costo “todo producto, servicio, cliente, actividad o unidad organizativa a la que se asignan los costos por algún propósito administrativo” (Blocher, Stout, Cokins, & Chen, 2008). Esta clasificación es valiosa para la presentación del estado de costos de producción y ventas, y el estado de resultados (Zapata, 2015), los cuales son reportes financieros, el primero con información de propósito específico y el segundo con información de propósito general (IASB, 2019), que refieren entre otras cosas al comportamiento de los recursos en un período dado. Los costos según su comportamiento se clasifican en fijos, variables y mixtos. Los costos fijos permanecen constantes independientemente de la variación de la producción, los costos variables se modifican ante cambios en la producción; y, el costo mixto está compuesto por una parte fija y una parte variable (Ramírez, 2008). Esta visión de la clasificación de los costos es útil debido a que sirve de base para el análisis en la toma de decisiones, esencial, por ejemplo, para estudios fundamentados en costeo directo, donde los costos fijos forman parte de los gastos del período y no del inventario.
Partiendo de los costos clasificados, y mediante el establecimiento de métodos y sistemas se determina el costo unitario y costo total de producción. El método de costeo guía la filosofía donde se fija qué elemento se considera dentro del costo del producto y qué elemento pertenece al gasto del período. El sistema de costeo, por su parte, refleja los procedimientos que se realizan para la acumulación y registro de costos durante el proceso productivo (Roldán, Agudelo, & Hernández, 2013). La determinación de un sistema adecuado depende de algunas características como tipo de producto, tamaño de la empresa, disposición técnica, entre otras.
El método puede ser básicamente: costeo absorbente o costeo directo. A diferencia del método directo que por fines administrativos considera tan sólo los costos variables, el método absorbente asigna tanto los costos fijos como los variables a los artículos producidos. En el Ecuador, se utiliza el costeo absorbente que dispone la contabilidad financiera, considerando que todos los recursos (costos fijos y variables) son necesarios para elaborar un producto.
Entre los sistemas de acumulación de costos más conocidos se encuentran el de órdenes de producción y por procesos. El primero, se utiliza en empresas que fabrican cantidades limitadas de productos y donde los costos se registran según la orden de producción. Mientras que el segundo, se aplica cuando la empresa trabaja con grandes y continuos volúmenes de producción, donde los artículos atraviesan diferentes procesos y los costos se van acumulando y trasladando de un proceso a otro (Roldán et al., 2013).
Horngren et al. (2012) manifiestan que aunque los sistemas mencionados sean los más usados, una empresa puede manejar un sistema que sea la combinación de ambos, y no necesariamente sea un sistema puro. Chacón (2016) precisa que el sistema de costeo por operaciones es un sistema híbrido que combina las características de los dos sistemas, acumulando y asignando costos a los productos obtenidos mediante procesos de producción de grandes lotes de productos similares, más no iguales. En consecuencia, se da a las empresas una opción que permite aprovechar las ventajas tanto del sistema por órdenes, como del sistema por procesos.
Además de establecer un sistema de acumulación, es importante determinar un sistema de control para la vigilancia de resultados y establecimiento de estándares. En este sentido, un sistema de control administrativo se define como el proceso a través del cual los administradores se aseguran de que los recursos sean obtenidos y usados de manera eficiente en función de los objetivos planteados (Ramírez, 2008). Un sistema de información específico para el control administrativo se basa en la contabilidad por áreas de responsabilidad; estas áreas pueden ser centros de costos, centros de ingresos, centros de utilidades u otros. Los centros de costos, permiten identificar diferentes variaciones de los costos dentro del área de producción, evidenciando el control mediante el cumplimiento eficiente de los estándares definidos (Ramírez, 2008).
Los sistemas de información mencionados ofrecen a los administradores una variedad de datos, que si se utilizan de manera integrada, apoyan a una acertada toma de decisiones. Con el objetivo de una verdadera coordinación se requiere dar tratamiento específico a la información generada. Bajo este contexto, la contabilidad administrativa da soporte a la gerencia en temas como análisis de cadena de valor, posicionamiento estratégico y análisis de causales de costos. En el campo de la gerencia estratégica de costos se entiende que los costos son causados por diferentes factores que dependen de las actividades de valor que realicen (Artieda, 2015). Considerando que según la contabilidad administrativa, el principal causal de costos es el volumen de producción, resulta ideal el uso de herramientas que giran alrededor del comportamiento de los costos.
Herramientas aplicables en el corto plazo como: costo volumen utilidad (CVU) y mezcla de productos para maximización de utilidades, proporcionan información fundamental en la actividad de planeación. Por un lado, el análisis CVU es un procedimiento estático que estudia la relación de las variables precio, volumen y costo, en donde el costo es un factor que puede ser controlado por la empresa; más, el precio y el volumen se encuentran influenciados por el mercado. Por otro lado, la mezcla de productos, que complementa el análisis anterior, determina la cantidad exacta de artículos a producir y vender para garantizar la maximización de utilidades mediante la aplicación de modelos de programación lineal. Estos son mecanismos matemáticos que dependen de la precisión con la que se puedan definir la función objetivo y las funciones de restricción (Anderson, Sweeney, Williams, Camm, & Martin, 2011).
Materiales y métodos
El presente caso de estudio contempla una investigación de nivel descriptivo y enfoque cualitativo. Se realiza un análisis de datos tanto cualitativos como cuantitativos. Estos datos fueron tomados de fuente primaria, de la empresa ensambladora y sus administradores. Se recopiló información documental como, por ejemplo, estados financieros, informes de producción, reportes de nómina, entre otros. Para obtener información específica sobre el tratamiento que se da a los elementos del costo, se realizaron entrevistas al personal y reuniones complementarias.
La metodología empleada para el análisis e integración de información de costos, tuvo como base el estudio realizado por Mejía, Higuita e Hidalgo (2015), el cual se centra en construir una metodología que calcula el costo de servir, una medida de rentabilidad a un nivel más detallado. Para ello, los autores plantean tres fases: definición del objetivo y alcance, recolección de datos y procesos, y medición del costo y análisis de resultados. En el presente estudio, se sugiere una variación a la metodología anterior y se plantean cuatro fases para el análisis de la situación de una empresa en cuanto al tratamiento de costos y la integración de información para utilidad en la toma de decisiones, a través de la determinación de oportunidades de mejora. Las fases que se utilizan son: la definición del alcance y objetivos del estudio en base de la motivación teórica; el levantamiento de datos y revisión de la información; el análisis y diagnóstico, y la aplicación de herramientas para la toma de decisiones.
La primera fase se enfoca en la definición del alcance y los objetivos del estudio. El objetivo principal es analizar e integrar la información de costos de producción en la industria de ensamblaje, de manera que contribuya a la toma de decisiones. El marco teórico sustenta la determinación de sistemas y herramientas que contribuyen con el objetivo. La investigación se orienta al caso de estudio de una empresa de ensamblaje en Ecuador con información de sus operaciones del año 2017. Esta empresa se dedica a ensamblar dos líneas de productos: L1, una clase de equipo de transmisión y L2, una clase de vehículo de dos ruedas. Para ello, estas líneas requieren, de manera general, dos tipos de materiales: el primero es el CKD importado y el segundo es el componente nacional.
La segunda fase se orienta al levantamiento de datos y revisión de la información. Para esto, se realizó la recopilación de datos a través de visitas a las instalaciones, requerimiento formal de documentación y aplicación de entrevistas. La documentación obtenida fue organizada según los pasos del ciclo contable; luego mediante revisión documental se validó la información general con los estados financieros. De ahí, el estudio prosiguió a un nivel más detallado para establecer la información correspondiente a los componentes principales de estudio, en este caso costos de producción y sus causales.
En la tercera fase de análisis y diagnóstico se conoció la situación en cuanto al tratamiento contable que la empresa da a los costos. Primero, se realizó la revisión de procesos y recursos que comprendió el reconocimiento de diagramas de flujo de los procesos de producción e identificación de los diferentes recursos que estos requieren. Luego, se efectuó el análisis de la estructura de costos con los datos del mes de diciembre del 2017, que consideró inicialmente la indagación de los elementos del costo, seguido de la identificación según sus clasificaciones para finalmente reestructurar la metodología de costeo. Es en esta etapa donde a la vez se propuso la integración de información de costos considerando la normativa técnica y legal aplicable, que rige en Ecuador.
Finalmente, en la cuarta fase se realizó la aplicación de herramientas útiles para la toma de decisiones, tomando como base la información generada en la fase anterior. Mediante el uso del modelo costo-volumen-utilidad (CVU) y del modelo matemático de programación lineal, se obtuvo información valiosa para que la gerencia pudiera identificar mejoras en el resultado de sus operaciones.
Resultados y discusión
En el desarrollo de la metodología presentada se describen los resultados obtenidos de la integración de información de costos en tres ejes principales: sistema de acumulación de costos, sistema de control administrativo y herramientas útiles para la toma de decisiones. La identificación de la información dentro del ciclo contable guía la organización documental del estudio. El proceso contable sigue unos pasos desde la identificación de la operación, seguido del registro de la misma en el Libro Diario General, generación del Libro Mayor General, realización de ajustes y emisión del balance de comprobación, hasta llegar a la estructuración de informes financieros (Zapata, 2011). Se considera importante la adición del paso análisis e interpretación de informes financieros como parte de la gestión del contador, pues él se constituye además en un asesor de la gerencia.
En este sentido, la documentación usada en el estudio parte del proceso contable. Reportes de producción, mayores de cuentas de costos, balance de comprobación y estados financieros fueron necesarios para el conocimiento inicial de la empresa y el posterior análisis específico.
Además de la revisión documental es necesario considerar también otros factores que influyen en las actividades de la empresa. Bajo la premisa de la Teoría de la Contingencia, Thomas (1991) considera que las variables que afectan la información financiera son las variables sociales, ambiente interno, atributos organizacionales, características del usuario y otras fuentes de información. Por otro lado, Hammad, Jusoh y Yen (2010) precisan que los factores que influyen en la contabilidad de gestión son la estrategia organizacional, tecnología, estructura, ambiente externo y tamaño. En este sentido, para la adaptación del manejo de costos de la empresa ensambladora se consideran factores de influencia la estructura organizacional y de planta, tamaño y visión de la empresa, el uso de la tecnología y el estilo de toma de decisiones.
Tabla 1 Estructura de costos
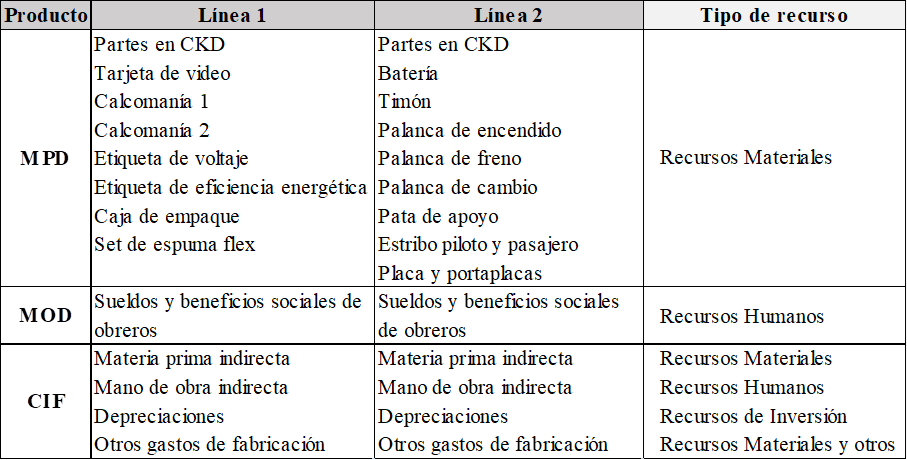
Nota. MPD= materia prima directa: MOD= mano de obra directa: CIF= costos indirectos de fabricación.
Elaboración: Los autores
Para iniciar con el análisis o implementación de un sistema de costeo es clave que se cuente con una estructura de costos bien establecida, es decir, que todos los elementos del costo se encuentren correctamente registrados y clasificados. En este caso, la empresa con sus dos líneas de ensamble intenta una clasificación de los costos en materia prima directa (MPD), mano de obra directa (MOD) y costos in directos de fabricación (CIF). Se reestructuran los elementos del costo (ver Tabla 1), tomando en cuenta una refinación en la ubicación de cada tipo de recurso y una aplicación según su comportamiento dentro del proceso productivo.
Sistema de acumulación de costos
Inicialmente, es preciso identificar cómo se llevan a cabo las operaciones en la empresa. La Figura 1 presenta un resumen del análisis de los procesos de producción aplicados.
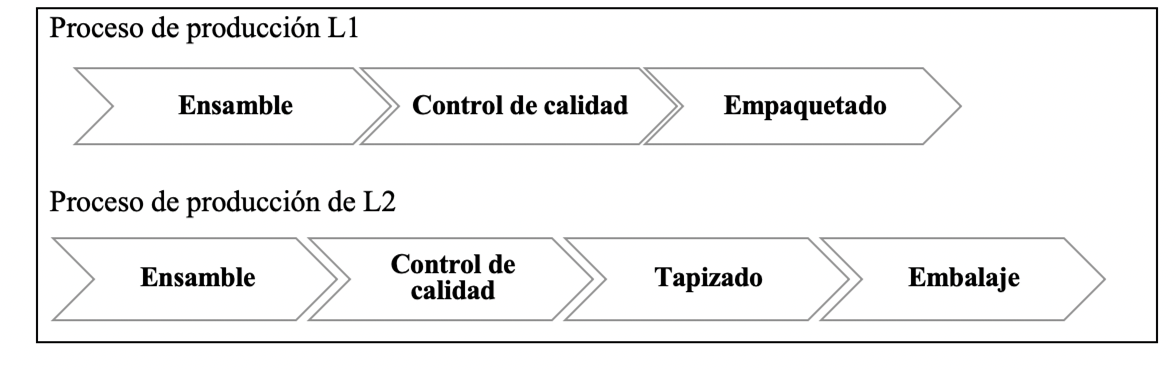
Fuente: Benavídez, E., & Segarra, E. (2018). Levantamiento de procesos en la industria de ensamblaje, Andrade, E., & Elizalde, B. (2018). Levantamiento de procesos de ensamblaje de televisores
Elaboración: Los autores
Figura 1 Procesos de producción
Acorde a la referencia teórica del sistema de costeo por procesos, inicialmente se podría tomar en cuenta este sistema, pues en la empresa, los productos se fabrican en grandes volúmenes y pasan por una serie de procesos. No obstante, el sistema por procesos no denota efectividad a cabalidad puesto que la empresa ensambla productos similares, pero no idénticos, y la diferencia está dada esencialmente por el tipo de materia prima directa, CKD. El conjunto de partes que conforman el CKD es único por tipo de línea y según sus modelos, sobretodo su costo es diferente. De ahí que, para dar seguimiento al costo de MPD por modelo se podría optar por el sistema por órdenes de producción, sin embargo, los valores de MOD y CIF requieren continuas asignaciones y no difieren notablemente entre los modelos. De la necesidad de utilizar los dos sistemas a la par nacen los sistemas híbridos, que según Horngren et al. (2012), las empresas manufactureras que elaboran una variedad de productos estandarizados como televisores, lava-vajillas y lavadoras, tienden a utilizarlos.
Por lo anterior, se plantea que el sistema de costeo por operaciones sería adecuado para las empresas de la industria de ensamblaje. Este sistema combina las características del sistema de costeo por procesos y por órdenes de producción de la siguiente manera (ver Figura 2). Por un lado, el costo de materia prima directa es atribuido mediante el sistema de costeo por órdenes de producción; se da seguimiento a la cantidad, modelo y costo de MPD según el tipo de artículo y de acuerdo a un lote de producción definido, para el traslado al costo unitario, aunque este lote corresponda a varios pedidos. Por otro lado, el costo de MOD y CIF conocido como costo de conversión, es asignado según el sistema de costeo por procesos. El ensamble de cada producto sigue el mismo ciclo de producción, se tratan como unidades iguales y permite la acumulación del costo de conversión para luego determinar un costo unitario promedio de conversión que es asignado indistintamente del modelo. En consecuencia, el sistema de costeo por operaciones identifica claramente dos categorías de costos: materia prima directa y costos de conversión. Los materiales directos ingresan al inicio del proceso de ensamble y los costos de conversión se van agregando durante el ciclo productivo.
Zapata (2015) propone algunas actividades previas para el diseño de un sistema por procesos y que pueden ser factibles al caso; por su parte Chacón (2016) explica la operatividad del sistema de costeo por operaciones. De ahí, se propone una metodología que considera la aplicación en dos fases: actividades estructurales iniciales y actividades operacionales recurrentes.
Las actividades estructurales iniciales comienzan con la identificación de los procesos productivos; seguidamente, de los procesos de servicio que apoyan a los productivos, en este caso de integración de información con propósito específico para toma de decisiones. Estos procesos son: almacenamiento de equipos y almacenamiento de vehículos. Posteriormente, para simplificar la distribución de los gastos de fabricación y tomando en cuenta la teoría de distribución por actividades (Crespo, 2017), se opta por separar los CIF que son plenamente identificables según los procesos (como es el caso de los costos por depreciación), de aquellos que no lo son. Por último, en esta primera fase se prepara el cuadro de distribución de CIF con bases de asignación específicas según el tipo de costo.
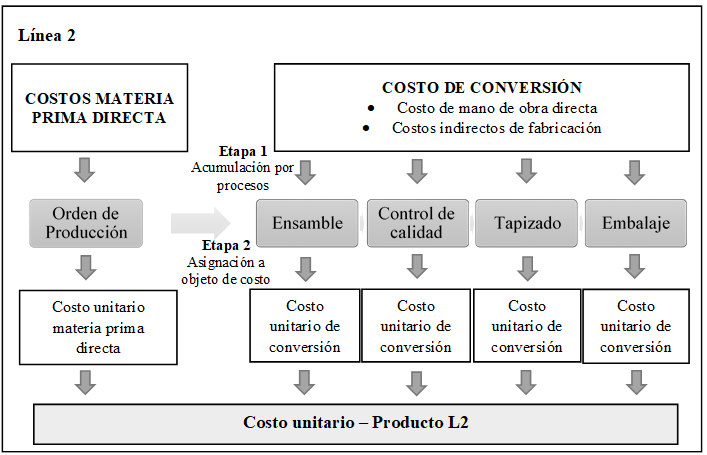
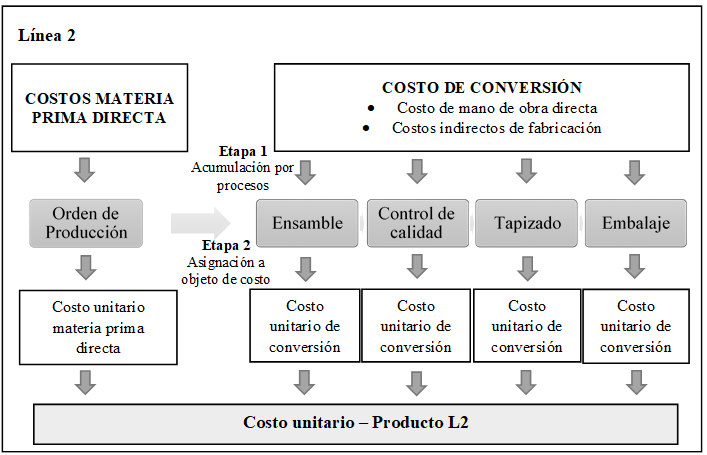
Elaboración: Los autores
Figura 2 Flujo de acumulación de costos por operaciones. Acumulación en dos etapas
Las actividades operacionales recurrentes deben realizarse con cierta periodicidad con el fin de contar con información oportuna, preferiblemente de manera mensual. En esta fase, se realiza un Informe de Cantidad de Producción que presenta información del número de unidades fabricadas por cada modelo de producto (ver Tabla 2). Identificar el ciclo de producción es importante, pues determina el procedimiento de costeo de las unidades terminadas y las parcialmente terminadas. En este caso, el ciclo de producción es corto, por lo que no es necesario realizar el cálculo de unidades equivalentes, característico en el sistema por procesos.
Enseguida, se dispone la preparación del Informe de Costos de Conversión de cada línea, como se presenta en las Tablas 3 y 4. La estructura del informe, según Chacón (2016), considera la asignación de costos a los procesos productivos y a los de servicio, y en él, el proceso de asignación de costos es de dos etapas según la literatura de Drury (2008):
Etapa 1: la acumulación de costos por unidad organizacional, en este caso por procesos. Los costos de MOD son cargados a cada proceso y los CIF distribuidos entre los procesos productivos y de servicio en función del cuadro de distribución de CIF previamente establecido. Luego, se asignan los costos de los procesos de servicio a los productivos. Considerando que los procesos de almacenamiento brindan servicio únicamente a ensamble y empaquetado/embalaje, sus costos se asignan de manera equitativa mediante el método directo.
Etapa 2, la asignación a los objetos de costo. El sistema por operaciones obtiene el costo unitario de conversión promedio para cada proceso productivo, dividiendo el costo de conversión total obtenido en la etapa 1 entre el número de unidades obtenidas en el proceso (Horngren et al., 2012).
Luego, se determinan los costos unitarios para cada modelo, según el objetivo de un sistema de acumulación de costos. En este caso, se obtiene de la suma de MPD más los costos unitarios de conversión, como se presenta en las Tablas 5 y 6. Finalmente, esta fase se cierra con la emisión del estado de costos de producción y ventas para dar información a los gestores y de esta manera, puedan evaluarse los costos del período. El estado debe presentar costos diferenciados por línea de producto, facilitando la interpretación de la información.
Sistema de control administrativo
Como parte del control administrativo, se propone la contabilidad por áreas de responsabilidad, específicamente el sistema por centros de costos. A través de él, se ofrece información sobre el uso de los recursos en cada centro; además, permite realizar un diagnóstico de la situación real donde actúa como sistema de prevención de situaciones críticas. De igual forma, este sistema evalúa la actuación de los responsables cuantificando las fallas y tomando acciones oportunas, así también muestra los aciertos realizados y los capitaliza en planes futuros, lo que resulta en la mejora continua de la empresa (Ramírez, 2008).
El control de costos se lleva a cabo mediante el establecimiento de estándares y presupuestos; así, los responsables cuentan con una guía clara a seguir y la verificación periódica será útil para identificar oportunamente debilidades y aciertos. En la práctica, se procede con la vinculación del sistema de operaciones y el sistema de control en función de los centros de costos identificados para su acumulación en el sistema por operaciones (ver Figura 3).
Para el diseño de un sistema de control administrativo Ramírez (2008) precisa las siguientes etapas: definición de los resultados deseados, determinación de las predicciones, determinación de los estándares, especificación del flujo de información, y evaluación y aplicación de acciones correctivas. En la etapa 1, se deben definir los resultados deseados en términos cuantificables. Este objetivo debe ser socializado con las personas responsables de manera que participen de forma activa en su cumplimiento. En este caso, por ejemplo, se determina aceptable una variación de hasta el 20% con relación al valor estándar de cada centro de costo. En la etapa 2, se determinan los elementos de predicción que son aspectos que pueden modificar los resultados deseados, estos deben considerarse con anterioridad para detectar desviaciones oportunamente. En el caso de la empresa, esta puede verse afectada por la variación en costos de CKD, los cambios de políticas económicas para las importaciones y la variación en el nivel de demanda de los productos.
En la etapa 3, se determinan los estándares con los cuales se compararán los resultados. Los costos por centros no tendrán significado si no se comparan con un estándar. Estos deben ser flexibles y adaptables ante cambios en los elementos predictivos. La empresa debe establecer presupuestos de costos mensuales. La etapa 4 establece el flujo de información, donde se debe definir la autoridad y responsabilidad de cada persona. Es importante ubicar en el organigrama de la empresa a las personas responsables de cada centro de costo y los niveles a los cuales darán cuenta. Finalmente, en la etapa 5 se realiza la evaluación y aplicación de la acción correctiva en caso de ser necesario. La evaluación en un mes se presenta en la Figura 4, ahí se observa que las variaciones producidas se encuentran dentro del 20% planteado como aceptable. Sin embargo, es importante identificar los aciertos realizados en almacenamiento de L2 que llevaron a cumplir exactamente con el estándar, y por otro lado, determinar la causa de las variaciones de los otros centros de manera que se puedan aplicar acciones correctivas de ser necesario.
La aplicación del sistema por centros de costo permite evidenciar la relación entre las funciones de planeación y control. Los objetivos a cumplir se establecen con anticipación, se consideran los elementos predictivos y finalmente se evalúan los resultados. Así, los responsables de cada centro tienen un límite o meta que cumplir y pueden identificar variaciones de manera oportuna. Sobre todo, los directivos logran conocer sobre la actuación y resultados de cada área promoviendo el uso eficiente de los recursos. Al integrar el sistema de acumulación de costos con el sistema de control administrativo se consigue el objetivo de calcular el costo de producción manteniendo el conocimiento del proceso de manufactura y el control a fin de mantener o reducir los costos en nuevos períodos.
Herramientas para la toma de decisiones
Ramírez (2008) manifiesta que para lograr el desarrollo integral de las empresas se debe contar con herramientas que contribuyan principalmente a las funciones de planeación y control. Herramientas aplicables a corto plazo, como el modelo CVU y la mezcla de productos para maximización de utilidades se convierten en apoyo fundamental para la administración al momento de gestionar los costos y tomar acciones que permitan cumplir los objetivos planteados.
La información generada por los sistemas de costeo, como se mencionó, alimenta los datos requeridos por estas herramientas. Se recaba información de costos de producción, específicamente los costos unitarios de las Tablas 5 y 6; y de costos clasificados por su comportamiento, esta clasificación proporciona datos de costos variables para determinar el margen de contribución y de costos fijos para conocer el margen operacional. Además, se requieren datos de volumen y precio, factores que a diferencia del costo, son menos controlados por la empresa. La aplicación y éxito del modelo CVU va a depender de la identificación de estas variables: costo, volumen y precio, al seguir los siguientes pasos: cálculo del margen de contribución, cálculo del punto de equilibrio, cálculo del margen de seguridad, cálculo del apalancamiento operativo y planeación de utilidades.
El margen de contribución (MUC) es considerado un indicador de los productos que aportan a cubrir los costos fijos, viene dado por la diferencia entre el precio de venta y el costo variable, como se puede observar en la Fórmula 1. Este indicador permite obtener una visión detallada del nivel de aporte de los productos, incluso si algún modelo resulta con margen de contribución negativo denota que está siendo subsidiado por otros productos más competitivos. Según el cálculo, cada vez que se venda un equipo de transmisión M5 se obtendrá $42,63 para cubrir los costos fijos. Al comparar el MUC de cada producto se tiene conocimiento de los productos que generan más aporte y en los cuales se debe enfocar la fuerza de ventas.
Por su parte, el punto de equilibrio (PE) según la fórmula 2, se logra donde los ingresos totales igualan los gastos totales permitiendo conocer la cantidad mínima de cada modelo que la empresa debe producir para cubrir esos costos. Para ello, se requiere del cálculo del margen de contribución ponderado, el mismo que se obtiene de la suma de los márgenes de contribución unitarios multiplicados por el porcentaje de participación en ventas de cada producto.
El punto de equilibrio se logra al vender 51´421 unidades al año, donde 38´566 son productos de L1 y 12´855 son productos de L2, considerando el porcentaje de participación en ventas que tiene cada línea, 75% y 25% respectivamente. Este es un dato importante porque actúa como referencia para los administradores ya que refleja el nivel mínimo para no tener pérdidas. Entonces, la empresa debe operar por encima de este punto para obtener utilidad, sin menoscabar recursos hacia los productos que le generen mayor utilidad.
Luego, el análisis del margen de seguridad viene dado por la diferencia entre las ventas reales o presupuestadas y las ventas en el punto de equilibrio, observable en la fórmula 3; este análisis da a conocer la posibilidad de disminución en ventas antes de que se origine una pérdida. Ramírez (2008) recomienda que el margen de seguridad se encuentre por encima del 50% del punto de equilibrio. Siguiendo con el análisis del equipo M5 se observa que su margen de seguridad es $389440,86 al año, y en términos porcentuales representa el 20% (margen de seguridad/ventas). A pesar de no cumplir con el margen de seguridad ideal mantiene un margen que permite generar suficientes utilidades para no entrar en pérdidas.
El grado de apalancamiento operativo (GAO) indica la variación de la utilidad operativa a partir de la variación en las ventas (fórmula 4). La empresa cuenta con un grado de apalancamiento operativo de 1,22 veces. Esto indica un apalancamiento operativo bajo, es decir, por cada cambio porcentual en el nivel de las ventas, la utilidad operativa disminuirá o incrementará 1,22 veces ese cambio porcentual. Esto se debe principalmente a los bajos costos fijos en relación a los costos variables. El grado de apalancamiento operativo bajo se considera bueno, siempre y cuando, los administradores mantengan una ideología conservadora, por el contrario, si desean asumir mayores riesgos este grado no sería ideal.
Finalmente, el modelo CVU no sólo permite encontrar la mezcla de productos en el punto de equilibrio, sino también ayuda en la planeación operativa al obtener la mezcla ideal para conseguir un nivel de utilidad deseado. La utilidad deseada se expresa en términos de utilidad neta como se muestra en la fórmula 5, por lo que el presente análisis considera por disposición legal los valores correspondientes a participación de trabajadores en utilidades (15%) e impuesto a la renta (25% tarifa actual). Estos valores representan generalmente el 36,25% de la utilidad operacional. Entonces, la empresa debe vender 69´090 unidades al año, 51´817 unidades de L1 y 17´273 de L2 para lograr el nivel de utilidad deseado.
De esta manera, el modelo genera una guía de acciones a llevar a cabo por parte de los administradores, donde según sus objetivos sabrán que productos y de qué líneas vender, a que costo y a qué precio.
Si bien, el modelo CVU permite referir los productos más rentables de la empresa; no es posible fabricar cantidades infinitas de dichos productos, con el fin de obtener altas utilidades, porque lógicamente existen algunas restricciones como la capacidad de producción y los niveles de demanda del mercado (Morillo, 2003). Por consiguiente, es apropiado considerar otra herramienta denominada mezcla de productos. Esta herramienta actúa como un modelo de optimización donde con el uso de programación lineal, se obtiene la cantidad exacta que se debe producir y vender de cada producto, con el objetivo de maximizar de utilidades. Esta herramienta tiene la capacidad de considerar cuantas restricciones tenga la empresa.
Para la ejecución del modelo, es necesario definir las variables inmersas en la problemática de producción, la función objetivo que relacione dichas variables y sus funciones de restricción, en este caso de forma mensual. La cantidad de cada modelo de L1 y modelos de L2 serán las variables de decisión definidas como L1 (𝑥i) y L2 (𝑦i). La función objetivo del presente estudio, Fórmula 6, es la función de utilidad operacional, la misma que contempla la sumatoria de la contribución marginal por cada modelo menos los costos fijos del período.
Z: Utilidad operacional
MUC i : Margen de contribución por modelo
𝑥i: Cantidad de productos L1 por modelo
𝑦i: Cantidad de productos L2 por modelo
CF: Costos fijos del período
Las restricciones que se identifican para la empresa ensambladora son las siguientes: el tiempo del personal disponible para producción medido en minutos requeridos para la fabricación de cada producto, el nivel mínimo de existencias que mantiene la empresa, el nivel de demanda de los productos y las restricciones de no negatividad.
Haciendo uso de la herramienta Solver con el método Simplex, se ingresa la función objetivo, las funciones de restricción y se obtiene la solución óptima para maximizar las utilidades de la empresa, presentado en la Tabla 7. Los resultados del modelo indican la cantidad óptima de las variables de decisión, es decir, la empresa debe producir 6.793 unidades de L1 (xi) y 906 unidades de L2 (yi) y que multiplicadas por el MUC se obtiene el margen de contribución total, finalmente al restar los costos fijos se maximiza las utilidades mensualmente en $ 172961,33.
De esta manera, la gerencia puede conocer el rendimiento de sus productos, enfocar la fuerza de ventas a promover los modelos que presentan mayor número de unidades y cumplir también con los que tienen menor cantidad. Así, se ofrece diversidad de productos a los clientes y se obtiene una guía clara de lo que se quiere lograr para obtener mejores resultados.
Conclusiones
Al hablar de costos e integración de su información se pueden mencionar varios temas como: elementos, clasificaciones, métodos, eficiencia, calidad, sistemas, entre otros; sin embargo, concretar cada uno y combinar según la literatura para darle utilidad a esa información es oportuno. Por ello, al utilizar cada uno de estos elementos de manera conjunta e integrada permite lograr impactos positivos en el resultado económico de la empresa gracias a la obtención de costos más precisos para los productos, a la opción de control de costos según los diferentes centros y a la información resultante de las herramientas administrativas.
El sistema de costeo por operaciones se establece como un proceso de acumulación y cálculo de costo de los productos adecuado para una empresa ensambladora debido a que considera sus características específicas de uso de materia prima diferenciada según modelos de productos sin restringir o modificar procesos de sus líneas. Esta adaptación de fundamentos teóricos lleva a la obtención de costos más exactos y por lo tanto fiables para la toma de decisiones, lo cual genera una ventaja competitiva.
La aplicación del sistema de control administrativo, según la teoría, es importante porque conoce la participación de cada uno de los centros con respecto al costo total. Los centros de costos deben ser permanentemente monitoreados, se debe establecer estándares o presupuestos de manera que pueda ser medible la gestión de los responsables de cada centro y en el caso correspondiente, implementar acciones de corrección. En este sentido, se promueve el manejo eficiente de los recursos, los responsables darán cuentas a la administración por los costos generados y las variaciones producidas de ser el caso. Sin embargo, la falta de estándares es una restricción significativa al momento de evaluar la actuación de los responsables de la empresa. Estándares definidos a través de un estudio técnico son necesarios para comparar los resultados obtenidos en cada centro de costo.
Las herramientas administrativas son consideradas esenciales para el proceso de toma de decisiones; donde, la información obtenida de los sistemas es llevada a análisis e interpretada para un diagnóstico oportuno y medidas correctivas. En el corto plazo, se prepone el modelo CVU y la mezcla de productos para maximización de utilidades como herramientas principales para apoyar las funciones de planeación y control. El análisis CVU permite tomar decisiones en cuanto a, por ejemplo, aceptar o rechazar una orden específica, eliminar o continuar la fabricación de un producto, entre otras. Luego, se complementa el análisis con el modelo de mezcla de productos para maximización de utilidades mediante programación lineal, donde la administración obtiene el resultado óptimo, considerando restricciones en cuanto a capacidad de producción y demanda. Al decidir la mejor mezcla de productos se cuenta con una guía clara para la operación de la empresa. Finalmente, en un entorno en donde el objetivo es lograr la integración efectiva de información se requiere de un análisis por centros de ingresos que complemente el estudio de costos. Así se puede evaluar resultados integrales de cada una de las áreas y líneas de producción de las empresas.