Forma sugerida de citación:
Aparicio-Carrillo, G.; Ciaccia-Sortino, M. y Jerez G., R. (2021). «Influencia del homogeneizado previo al laminado en frío en la microestructura del AA3003». Ingenius. N.◦ 26, (julio-diciembre). pp. 99-110. doi: https://doi.org/10.17163/ings.n26.2021.09
1. Introducción
La aleación de aluminio AA3003 es utilizada en la industria de fabricación de carrocerías de vehículos de transporte y en el envasado de alimentos y bebidas, entre otras aplicaciones; es producido por procesos de colada continua o semicontinua.
En el proceso de colada continua por enfriamiento directo (DC, direct chill en inglés), un canal transportador lleva el metal fundido a un molino de laminación, al final del cual hay una boquilla que distribuye el metal en todo el ancho de los rodillos. Un sistema de enfriamiento con agua mantiene los rodillos a una temperatura más baja que la del metal fundido, causando la solidificación del material en contacto con el rodillo, con altas tasas de enfriamiento. Por lo tanto, la matriz de aluminio llega a estar altamente saturada con manganeso y muestra una variación de su microestructura con respecto al espesor, debido a que los gradientes de temperatura producen un enfriamiento más rápido en las superficies de la lámina que en el medio del espesor [1].
Después de la solidificación, la microestructura se caracteriza por ser una solución heterogénea con partículas primarias de Al6(Mn,Fe) y cantidades más pequeñas de α-Al(Mn,Fe)Si que se forman en los bordes de la celda de solidificación o en las áreas interdendríticas. Esta microestructura afecta significativamente las propiedades mecánicas de la aleación y su uso potencial en aplicaciones de ingeniería [2].
Para reducir este efecto, se aplica un tratamiento térmico de homogeneizado a temperaturas entre 500 °C y 650 °C, por un mínimo de 8 h [3, 4]. Este proceso reduce la concentración de manganeso y controla el tamaño, la densidad, y la distribución de las partículas primarias y dispersoides, que son algunos de los factores que afectan el fenómeno de recristalización, la textura, y las propiedades mecánicas de la aleación en las etapas de formación [5, 6].
Este trabajo presenta un estudio comparativo de la microestructura de la aleación de aluminio AA3003 producida por colada continua con y sin homogeneización, con la posterior aplicación de trabajo en frío (CW, cold working en inglés) por laminación, utilizando microscopía óptica y microscopía electrónica de barrido en combinación con técnicas de electrones retrodispersados y espectroscopía de dispersión de rayos X, y la evaluación de sus propiedades mecánicas (microdureza y resistencia). Los resultados obtenidos permitirán la comparación de la forma y distribución de las partículas primarias y secundarias (dispersoides) presentes en la aleación tanto en condiciones iniciales como luego de la aplicación del trabajo en frío, para evaluar la relevancia, desde el punto de vista microestructural, de la homogeneización para el posterior conformado en frío de la aleación.
2. Materiales y métodos
2.1. Experimentación
Se utilizó una lámina de aleación AA3003, con un ancho de 1350 mm, una longitud de 250 mm (en la dirección de laminado) y un espesor promedio de 6,2 mm, proveniente del proceso de colada continua de doble rodillo de CVG ALUCASA (Venezuela). La composición química, obtenida por espectroscopia de emisión óptica, fue (% en peso): Mn 1,170, Fe 0,666, Si 0,357, Cu 0,133, Zn 0,012 y Al 97,600.
Se cortaron seis muestras de la lámina. Tres cortes, etiquetados como muestras H, fueron sometidos a tratamiento térmico de homogeneizado en un horno de resistencia eléctrica, a 600 °C por 8 h como se sugiere en [7], y luego enfriados lentamente, mientras que los tres restantes, denominados muestras DC, fueron dejados en la misma condición en que fueron recibidos. Una muestra H y una muestra DC fueron reservadas para referencia y etiquetadas como muestra en condición inicial (CI) (0 % de trabajo en frío). Una muestra DC y una muestra H fueron laminadas en frío con una reducción de 30 % en su espesor, y las muestras restantes fueron sometidas a una reducción de 60 %. El proceso de trabajo en frío fue realizado en un tren de laminado experimental a una velocidad de 1,5 m/min, manteniendo la dirección original de laminado de la lámina y haciendo varias pasadas. Posteriormente, se cortaron las muestras para la preparación de los especímenes de prueba de tracción y se hicieron otros cortes para la evaluación microestructural.
Los especímenes para los ensayos de tracción fueron preparados tal como se especifica en la norma ASTM E8 [8], con una sección transversal rectangular, una longitud calibrada de 25 mm y una longitud total de 100 mm. Dichos especímenes fueron cortados con un chorro de agua para evitar daños microestructurales en la zona de corte.
Finalmente, las muestras para la evaluación microestructural fueron embutidas en polimetilmetacrilato para facilitar su manejo y preparación, así como también para evitar la posible contaminación de la superficie. Estas muestras fueron preparadas de acuerdo con las normas ASTM E3 [9] y ASTM E407 [10], y desbastadas en agua con papel de lija N.° 240, 320, 400, 600 y 800. Posteriormente, fueron pulidas en dos etapas: primero con alúmina de 1 µm y luego en una máquina de pulido electrolítico Buehler Electromet 4 con un electrolito compuesto de 800 cm3 de etanol, 140 cm3 de agua destilada y 60 cm3 de ácido perclórico al 60 %, aplicando una tensión de 17 V por 25 segundos. Finalmente, las muestras fueron atacadas por inmersión en una solución compuesta de 50 cm3 de agua destilada y 5 g de NaOH a 70 °C por 10 segundos.
2.1.1. Microscopía óptica (MO)
En cada caracterización microestructural de materiales es necesaria una exploración preliminar por microscopía óptica, ya que esta proporciona una idea general de la microestructura, distribución y morfología de las fases, y otras características de interés en las cuales enfocarse con las técnicas de microscopía electrónica.
Las muestras fueron analizadas con un microscopio Olympus PMG3 con magnificaciones de 100X a 1000X, y las imágenes fueron tomadas con una cámara Olympus DP12.
En este estudio, la variación esperada de la microestructura debida a los gradientes de deformación fue evaluada en tres puntos de la sección transversal de las muestras. Estas posiciones se designan como «exterior», «medio» y «centro», como se muestra en la Figura 1.
2.1.2. Microscopía electrónica de barrido (SEM, scanning electron microscopy en inglés)
Esta técnica de visualización fue utilizada para localizar en la microestructura fases y precipitados que serán identificados posteriormente. Se seleccionó esta técnica porque es capaz de realizar una mayor magnificación de la imagen (más de 1000X) en comparación con la microscopía óptica.
La superficie de la muestra fue cubierta con polvo de oro, dado que es un material altamente conductor, permitiendo el barrido electrónico de toda la superficie de la muestra y la obtención de imágenes con una resolución mejorada.
Se utilizó un microscopio electrónico de barrido JEOL JSM-6390 en la configuración de electrones retrodispersados (BSE, backscattered electron en inglés), una técnica que resalta el contraste entre las fases, haciéndolas más claras o más oscuras dependiendo del peso atómico de sus componentes. En este método, la energía específica del rayo depende del número atómico del material, esto es, a mayor número atómico promedio, mayor intensidad. La visualización fue realizada de acuerdo con el patrón mostrado en la Figura 1.
2.1.3. Análisis mediante espectroscopía de dispersión de rayos X (EDX, Energy dispersive X-ray spectroscopy en inglés)
Con esta técnica es posible realizar un análisis químico semicuantitativo de puntos o líneas específicas en el área seleccionada de la muestra. Esta técnica da valores de la cantidad relativa de los elementos constituyentes expresada como porcentaje en peso y como peso atómico, y por tanto permite la identificación provisional de la fase observada. Este análisis fue realizado con un dispositivo EDX 7582 de Oxford Instruments.
2.1.4. Evaluación de las fases en la aleación AA3003
Se realizó una evaluación tentativa de las fases con los resultados obtenidos de los estudios de SEM utilizando un detector BSE, y los análisis EDX, juntamente con las investigaciones [6, 7], [11, 12]. Estos autores fueron capaces de identificar, utilizando TEM, dos tipos de fases, tanto en las muestras dejadas en la misma condición en que fueron recibidas como en las homogeneizadas:
La fase primaria formada por la matriz dendrítica de aluminio.
Las fases secundarias Al6(Mn,Fe) y αAl(Mn,Fe)Si, pueden formar parte de las partículas primarias provenientes de la solidificación del líquido con alto contenido de elementos de aleación y de las partículas secundarias (dispersoides, con tamaño menor a 1 µm), que se originan de la descomposición y precipitación de los elementos de aleación en solución sólida sobresaturada en la matriz dendrítica.
2.1.5. Evaluación de las propiedades mecánicas
Los ensayos de tracción fueron realizados a una tasa de desplazamiento de 5 mm/min utilizando un equipo universal de ensayo de materiales MTS de 25 toneladas de capacidad y un extensómetro Instron de 1 pulgada. Se realizaron cinco réplicas para cada condición de prueba, considerando las direcciones longitudinal, transversal y diagonal con respecto a la dirección de laminado, evaluando un total de 90 especímenes. Se realizaron ensayos de microdureza Vickers en las muestras utilizadas en microscopía óptica, aplicando tres penetraciones para cada condición de estudio, de acuerdo con el estándar ASTM E384 [13], con una carga de 50 g y 15 segundos de aplicación. Se utilizó un microdurómetro Buehler Identamet 1104 Vickers – Knoop.
3. Resultados y discusión
3.1. Microscopía óptica
Esta técnica fue utilizada para identificar puntos de interés, así como el arreglo y la morfología preliminar de los precipitados. Por esta razón, solo se presentan los resultados para las muestras CI. En la Figura 2 se ve el barrido de la microestructura de la aleación AA3003 en las posiciones exterior, media y centro del espesor, en la condición inicial DC.
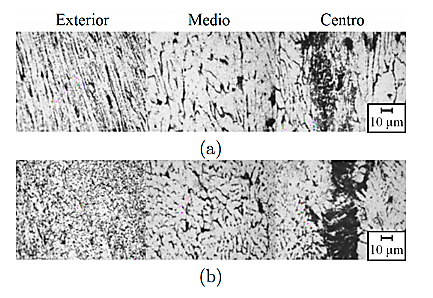
Figura 2. Micrografías OM mostrando la microestructura de las muestras DC CI de la aleación AA3003: (a) dirección de laminado, (b) dirección transversal
Puede observarse en la Figura 2(a) que los precipitados en el área exterior se estiran en la dirección de laminado. En contraste, en la Figura 2(b) se presentan como puntos, lo cual es consistente con el estirado de los precipitados en la dirección normal al plano de la micrografía.
Una característica del proceso de colada continua DC es el gradiente de temperatura a través del espesor de la lámina, causando diferentes tasas de enfriamiento y solidificación y produciendo un cambio en la microestructura, ver Figuras 2(a) y (b). Puede observarse que los precipitados son más finos y están presentes en mayores cantidades en las áreas exteriores de las muestras, mientras que en la zona media los precipitados son más grandes y con menor densidad. Se observó una línea de segregación central (LSC) hacia el área central de las muestras, la cual consiste de una alta concentración de precipitados alineados en la dirección de laminado. Este defecto, característico de las aleaciones de aluminio obtenidas por colada continua DC, ha sido observado por otros investigadores [14, 15].
Un resultado esperado de la homogeneización es la distribución uniforme de las partículas de la segunda fase y la ausencia de la LSC. Sin embargo, a pesar de que la Figura 3 evidencia que la concentración de los precipitados en la LSC se ha reducido, la distribución de los precipitados a través del espesor es similar a la de la condición inicial DC, ver Figura 2. Estos hechos llevan a la conclusión que es necesario optimizar los parámetros del tratamiento térmico de homogeneización.
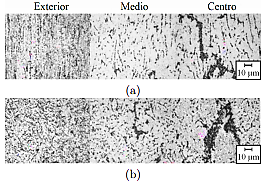
Figura 3. Micrografías OM mostrando la microestructura de las muestras H CI de la aleación AA3003: (a) dirección de laminado, (b) dirección transversal
Un efecto adicional de la homogeneización es un cambio en la morfología de los precipitados. La micrografía de la Figura 4(a) correspondiente al espécimen CI que se mantiene en la condición en que fue recibido, muestra que los precipitados se estiraron en la dirección de laminado, mientras que la Figura 4(b) expone claramente la esferoidización de los precipitados en el espécimen CI homogeneizado.
3.2. Evaluación de las fases por SEM
La evaluación de las fases de los especímenes CI fue realizada utilizando SEM con la técnica BSE. Las regiones más claras en las imágenes indican la posible presencia de la fase α-Al(Mn,Fe)Si debido a su número atómico promedio más alto (rico en Mn, Fe y Si), mientras que la fase Al6(Mn,Fe) tiene una cantidad más pequeña de Mn y Fe y, por tanto, un número atómico más bajo y menor brillo que la fase α. La matriz es la fase más opaca, ya que tiene la concentración más baja de elementos de aleación.
La Figura 5 y la Tabla 1 exponen la microestructura de la aleación en la condición como fue recibida. De acuerdo con [16], las partículas constituyentes Al6(Mn,Fe) y α-Al(Mn,Fe) se forman principalmente como redes interdendríticas eutécticas.
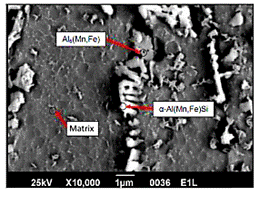
Figura 5. Micrografía SEM mostrando una identificación tentativa de las fases de la aleación AA-3003 en la condición como fue recibida
En la Figura 5 puede verse que las dos fases coexisten en redes eutécticas, que se presume son las sugeridas por [16]. El análisis químico semicuantitativo y el análisis de espectros EDX realizado en los puntos indicados en la Figura 5 proporcionan los siguientes resultados:
La evaluación en el área señalada como la matriz presenta menores cantidades de elementos de aleación en comparación con las otras dos, y ausencia de silicio.
La fase marcada como Al6(Mn,Fe) tiene el más alto contenido de hierro de las tres zonas evaluadas, y no existe la presencia de silicio.
La fase marcada como α-Al(Mn,Fe)Si es la única zona que tiene silicio.
Estos resultados revelan que el material en la condición DC tiene una microestructura que podría estar compuesta de partículas de Al6(Mn,Fe) y α-Al(Mn,Fe)Si.
La Figura 6 y la Tabla 2 presentan la microestructura del material homogeneizado. Las fases secundarias aparecen como partículas individuales, en contraste con las redes eutécticas mostradas en el material en la condición como fue recibido. Estas partículas, de un tamaño alrededor de 1 µm, se clasifican como dispersoides.
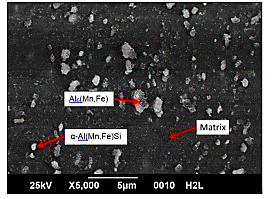
Figura 6. Micrografía SEM mostrando una identificación tentativa de las fases de la aleación AA3003 en la condición homogeneizada con 0 % de trabajo en frío
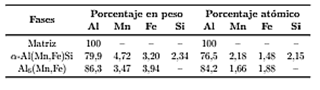
Tabla 2. Microanálisis químico BSE de la aleación AA3003 en la condición homogeneizada con 0 % de trabajo en frío
A través de la evaluación SEM del material homogeneizado, fue difícil localizar partículas cuya composición química correspondiera a la fase Al6(Mn,Fe). Por lo tanto, puede inferirse que la mayor parte de esta fase se transformó en la fase α-Al(Mn,Fe)Si como resultado del tratamiento térmico, como se sugiere en [6] y [11]. Este efecto aumenta la ductilidad de la aleación, mejorando su desempeño en procesos de conformado de plástico [6], [11].
Los resultados obtenidos del análisis químico y los espectros EDX, presentados en la Figura 6, muestran que, al igual que en el caso del material como fue recibido, la fase oscura contiene la cantidad más alta de hierro, y solo la fase brillante contiene silicio. Sin embargo, puede notarse que la matriz está compuesta de 100 % aluminio, lo cual evidencia una disminución de los elementos de aleación en la solución sólida sobresaturada como consecuencia de la aplicación del tratamiento térmico. Por lo tanto, la aleación alcanza un estado de equilibrio a través de la precipitación de manganeso y hierro.
3.3. Estructura y composición de las fases
Durante el calentamiento hasta la temperatura de homogeneización, los dispersoides precipitan en la matriz; posteriormente, la mayoría de las partículas primarias compuestas por la fase Al6(Mn,Fe) se transforman a la fase α-Al(Mn,Fe)Si debido a la alta difusión del silicio contenido en las soluciones sólida y eutéctica [16, 17, 18]. Dado que la transferencia de átomos de silicio no ocurre de un constituyente al otro (desde las partículas primarias a los dispersoides o viceversa), ni intersticialmente ni por sustitución, estos investigadores han propuesto estudiar la evolución de las partículas primarias y dispersoides a través de la relación de los porcentajes atómicos de Mn y Fe, obtenido por los espectros EDX.
Li y Arnberg [19] encontraron que esta relación varía de acuerdo con la temperatura y tiempo de homogeneización, debido a que los átomos de hierro y manganeso se sustituyen mutuamente en las partículas primarias y dispersoides. Sobre la base de esta metodología, los análisis químicos EDX y semicuantitativo fueron realizados a partículas primarias y dispersoides ubicadas en las posiciones centro y media (ver Figura 1) de ambas muestras en condición inicial. Las Figuras 7 y 8 ofrecen ejemplos de los espectros EDX obtenidos, y la Tabla 3 presenta la composición de elementos químicos y la relación Mn/Fe promedio.
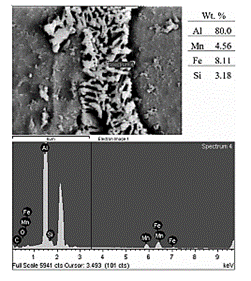
Figura 7. Micrografía SEM y espectro EDX de una partícula primaria en la condición como fue recibida
Estos resultados son similares a los encontrados por [15], quienes obtuvieron relaciones Mn/Fe, para las partículas primarias, de 0,57 en la condición DC, y 0,79 para el material homogeneizado; en el caso de los dispersoides, se encontró un valor de 1,70.
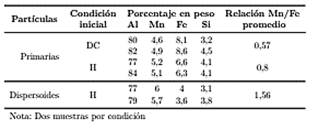
Tabla 3. Composición de elementos químicos obtenida por EDX de las partículas primarias y dispersoides de la aleación AA3003 en las condiciones iniciales DC y H
En función de la similitud entre los resultados obtenidos en este trabajo y los encontrados en la literatura, se presume que existen dos tipos de fase α-Al(Mn,Fe)Si en la condición homogeneizada:
La fase α primaria, que proviene de la transformación de Al6(Mn,Fe) y de la ruptura de las redes eutécticas durante el calentamiento, la cual, al igual que las partículas primarias en la condición DC, tiene un alto contenido de hierro.
La fase α secundaria, proveniente de la precipitación y subsecuente engrosamiento de los dispersoides, se diferencia de la fase α primaria por su menor contenido de hierro, relación Mn/Fe más alta y menor tamaño. En este trabajo, los pocos dispersoides que pudieron observarse tuvieron un tamaño que siempre fue ligeramente mayor a 1 µm debido al proceso de engrosamiento durante la homogeneización.
Dado que el hierro tiene muy poca solubilidad en aluminio sólido, la disminución del contenido de hierro en las partículas primarias para el material homogeneizado podría indicar que no todos los dispersoides en contacto con las partículas primarias son disueltos y absorbidos, sino que algunos de ellos pueden estar intercambiando átomos de manganeso por átomos de hierro con las partículas primarias. Esta podría ser la razón por la cual algunos dispersoides crecieron hasta un tamaño mayor a 1 µm e incluso se convirtieron en partículas primarias.
El compuesto identificado tentativamente como α-Al(Mn,Fe)Si fue la fase con la fracción en peso más alta encontrada en la aleación en la condición H, como fue verificado a través de la evaluación SEM así como en la condición DC. Esto podría deberse a la alta cantidad de silicio (0,357 % en peso) contenido en la aleación empleada en este trabajo comparada con las usadas por otros autores (0,1 % a 0,2 % en peso), dado que un contenido de silicio que exceda un porcentaje en peso de 0,07 favorece la precipitación de la fase α; en contraste, un menor contenido de silicio promoverá la precipitación de la fase Al6(Mn,Fe) [16]).
Otro hallazgo en algunas áreas de las muestras en la condición DC fue la presencia de precipitados de forma rectangular, que fueron identificados, con la ayuda de análisis EDX, como Al6−7Mn, ver Figura 9. Precipitados similares, en forma y composición, fueron observados por [15] y [18] en muestras de láminas de AA3003 obtenidas por colada continua. Por lo tanto, este podría ser una morfología de precipitado característica de este material.
Adicionalmente, en la Figura 9 se nota que la longitud de estos precipitados es menor que 1 µm; por o tanto, pueden ser clasificados como dispersoides. Estas partículas precipitan en las zonas dendríticas durante el proceso de colada continua a aproximadamente 350 °C, temperatura a la cual se inicia la precipitación de los dispersoides.
3.4. Variación de la microestructura con el trabajo en frío
Las láminas de aleación de aluminio obtenidas por colada continua exhiben una concentración más alta de elementos de aleación en solución sólida sobresaturada, y partículas intermetálicas (eutécticas) más pequeñas, en comparación con otros tipos de colada. Estas características afectan el comportamiento termomecánico de la aleación durante los procesos de conformado. Las micrografías SEM de las muestras DC y H, sometidas a trabajo en frío como se describe en la sección experimental, fueron adquiridas para investigar este fenómeno y determinar la influencia tanto del trabajo en frío como del tratamiento térmico de homogeneización en la distribución de las fases. En la Figura 10 se observan las micrografías SEM para el material DC, con y sin trabajo en frío, de las posiciones externa y central de las muestras.
En la Figura 10(a) puede apreciarse la formación de redes eutécticas, en su etapa inicial, y estructuras dendríticas columnares, ambas elongadas en la dirección de laminación, en la zona exterior de la muestra. Esto es causado por el contacto directo de la superficie de la lámina con el rodillo durante el proceso de colada; por lo tanto, es la zona sometida a la tasa de enfriamiento y presión más altas.
La variación de la distribución de la microestructura con la cantidad de trabajo en frío aplicada se muestra en las Figuras 10(b) y (c). A medida que aumenta la deformación en frío, también aumenta la separación de las partículas primarias y secundarias contenidas en las regiones interdendríticas y dendríticas, respectivamente. Además, el número de partículas primarias también se incrementa, pero su tamaño se reduce.
La Figura 11 muestra una imagen de la zona central en una muestra DC, donde puede notarse una LSC. Esta línea fue observada en todas las muestras del material DC, lo cual confirma un control apropiado del proceso y una buena eficiencia en la extracción del calor por ambos rodillos. En un análisis EDX de perfil de línea realizado a la LSC, se encontró que a medida que se acerca a la zona central, existe una reducción de la concentración de aluminio y un aumento de los elementos de aleación, principalmente hierro, debido a su baja solubilidad en aluminio sólido.

Figura 10. Micrografías SEM mostrando la variación de la microestructura en las posiciones externa y central de la muestra de AA3003 tal como fue recibida, con trabajo en frío: (a) 0 % CW, (b) 30 % CW, y (c) 60 % CW
La Figura 12 muestra la LSC luego de la homogeneización, confirmando la disminución en el número de segregados, en comparación con la Figura 11.
La Figura 13 presenta las micrografías SEM para el material homogeneizado, con y sin trabajo en frío, de las zonas externa y central de las muestras. En este caso se observaron partículas con un tamaño promedio de 2 a 3 µm en la posición externa de la muestra, mientras que en el centro estas tienen mayor tamaño, de 3 a 5 µm. Esto ocurre porque las primeras se originan de la ruptura de redes eutécticas que son mucho más pequeñas que las observadas en las posiciones media y central.
En la Figura 13(a) las partículas se agrupan en la forma de lo que previamente fueron las redes eutécticas localizadas en las regiones interdendríticas. A medida que se incrementa el nivel de trabajo en frío, estas partículas son desplazadas por el efecto del movimiento de los planos de deslizamiento, produciendo la pérdida de estos clústeres y mostrando alineamiento posterior de los precipitados con la dirección de laminación (ver Figuras 12, 13(a) y 13(b)).
Nótese en la Figura 13 que, en contraste con la variación de la microestructura para la condición DC, no se observó un cambio sustancial en el tamaño de las partículas de la fase secundaria con el aumento del trabajo en frío en las muestras homogeneizadas. Esta condición contribuye a la homogeneidad de las propiedades mecánicas, lo cual es una evidencia de la efectividad de la aplicación del tratamiento térmico de homogeneización previo al proceso de formación en frío.
Torres et al.[20] determinaron que una tasa de difusión más alta, que se incrementa con el tiempo de homogeneización, induce una mayor disolución localizada de la LSC y, al mismo tiempo, una redistribución de los segregados en la matriz de aluminio, produciendo una microestructura más uniforme.
3.5. Propiedades mecánicas
La Tabla 4 muestra la media y la desviación estándar de las propiedades mecánicas obtenida de los ensayos de tensión y microdureza. Se reportan límite elástico (S0,2), resistencia a la tracción (S u ), ductilidad como función de porcentaje de reducción en el área (RA) y microdureza Vickers (MV).
En la Tabla 4 se observa el aumento en la resistencia y dureza, y la disminución en la ductilidad, a medida que aumenta el trabajo en frío, independientemente de la condición inicial del material. Esto se debe al mecanismo de endurecimiento por deformación de esta aleación y está relacionado con la generación, movimiento y apilamiento de dislocaciones en los bordes del grano o diferentes obstáculos que pueden estar presentes en el cristal.
Las diferencias en resistencia y dureza entre los materiales tal como fueron recibidos y los homogeneizados se deben principalmente a dos mecanismos: el primero y más dominante es la restricción de movimiento de las dislocaciones por la presencia de más átomos de los elementos de aleación en solución sólida sobresaturada en la condición DC, lo cual fue confirmado por el espectro EDS mostrado en la Figura 7; el segundo mecanismo es el endurecimiento por la dispersión de partículas pequeñas en la matriz, tales como los precipitados Al6−7Mn encontrados en la condición DC y mostrados en la Figura 9 los cuales, de acuerdo con algunos investigadores son incoherentes con la matriz y promueven la formación de anillos de dislocación alrededor de ellos, endureciendo aún más la matriz de aluminio [18], [21].
La Tabla 5 ofrece la diferencia porcentual de las propiedades mecánicas en relación con la máxima cantidad de trabajo en frío, que fue 60 %. Comparando estos resultados, para el material homogeneizado antes del trabajo en frío (H) se obtuvieron incrementos más altos en la resistencia (320 % en comparación con 138 % para el material DC) y dureza (62,1 % en comparación con 48,5 % para el material DC), y una reducción más pequeña en ductilidad (–27,8 % en comparación con –46,9 % para el material DC).
Estos resultados indican que la homogeneización previa al trabajo en frío mejora considerablemente la capacidad de deformación plástica en frío de la aleación, debido a que la disminución en la ductilidad, medida como una función de la reducción en el área, es mucho menor que la obtenida sin homogeneización previa. Por otra parte, a pesar de que el material homogeneizado no alcanza la resistencia y dureza de la aleación directa de colada, comparando para los mismos porcentajes de deformación, los incrementos en estas propiedades son más significativos, lo cual indica que, al continuar el proceso de deformación plástica en frío, se obtendría un material con una mayor resistencia y dureza, además de la más alta capacidad de deformación en frío.
Estos resultados están correlacionados con los obtenidos en la sección 3.4, mostrando que el proceso de homogeneización de la aleación AA3003 obtenida por colada continua mejora su capacidad de deformación plástica y disminuye la probabilidad de agrietamiento durante el trabajo en frío posterior.
4. Conclusiones
Basándose en los resultados obtenidos para las diferentes condiciones evaluadas, las fases secundarias fueron identificadas tentativamente como Al6(Mn,Fe) y α-Al(Mn,Fe)Si, las cuales variaron en cantidad, tamaño y forma. Una identificación conclusiva requiere un análisis TEM, el cual no fue posible al momento de hacer esta investigación.
Las fases secundarias están compuestas de partículas primarias y secundarias, que difieren en su contenido de Fe y Mn, resultando en una menor relación Mn/Fe para las partículas primarias (0,57 para la condición como fue recibida y 0,80 para la condición homogeneizada), mientras que los dispersoides tienen una relación Mn/Fe más alta (1,56 después de la homogeneización).
La homogeneización debe ajustarse a un tiempo de exposición más largo, debido a que las partículas de la fase secundaria alineadas en la dirección de laminación, todavía pudieron observarse en la microestructura.
La homogeneización produce la descomposición de la matriz sólida sobresaturada a través de la disolución y precipitación de los dispersoides, además de la esfereoidización de las partículas primarias contenidas en las zonas interdendríticas. Debido a estos efectos, se espera que aumente la ductilidad del material, produciendo así condiciones favorables para la aplicación de procesos de conformado en frío.
La aplicación de trabajo en frío al material no homogeneizado causó la división y separación de las partículas de las fases secundarias. En contraste con este comportamiento, las partículas del material previamente homogeneizado mostraron menor variación en su tamaño. Esta es una condición deseable para aplicaciones posteriores de conformado, debido a la menor probabilidad de agrietamiento del material durante el trabajo en frío.
Lo anterior fue confirmado por los resultados obtenidos de resistencia, dureza y ductilidad. Hubo un incremento de 320 % en el límite elástico y una disminución de 27,8 % en la ductilidad para el material homogeneizado, en comparación con 138 % y 46,9 %, respectivamente, para el material no tratado, demostrando así que el material homogeneizado tiene una mayor capacidad para la deformación plástica en frío.