Forma sugerida de citación:
Morales, Y.; Zamora, Y.; Vásquez, P.; Porras, M.; Bárzaga, J.; López, R. (2018). «Comparación entre redes neuronales artificiales y regresión múltiple para la predicción de la rugosidad superficial en el torneado en seco». Ingenius. N.° 19, (enero-junio). pp. 79-88. doi: https://doi.org/10.17163/ings.n19.2018.08.
1. Introducción
El acero inoxidable es uno de los materiales metálicos más utilizados en el sector industrial, esto se debe a la favorable combinación de las propiedades mecánicas, resistencia a la corrosión y costo. Este material ha sido ampliamente usado en el campo aeroespacial y militar, donde existe una demanda creciente en los requisitos de calidad superficial [1].
Las características de la superficie mecanizada afectan directamente la resistencia a la fatiga, la resistencia a la corrosión y las propiedades tribológicas de los componentes mecanizados. Obtener un valor elevado de calidad superficial aumenta la vida a la fatiga del producto. En consecuencia, el control de la superficie mecanizada es esencial para asegurar un correcto proceso de corte. El aspecto más importante en los procesos de manufactura es la medición y la caracterización de las propiedades superficiales. En el proceso de torneado, la rugosidad superficial es un parámetro que tiene gran influencia en el comportamiento y la funcionalidad de los componentes mecánicos y en los costos de producción [2].
La rugosidad superficial es afectada por varios factores, tales como: el avance, las propiedades del material de trabajo, la velocidad de corte, la profundidad, el radio de la punta, las condiciones de la máquina, los fluidos de corte, los materiales de las herramientas de corte y los ángulos de la herramienta de corte, entre otros. Dentro de ellos, son fáciles de ajustar los parámetros de corte con el objetivo de lograr el rendimiento esperado [3].
Los aceros inoxidables austeníticos son considerados materiales difíciles de mecanizar, característica relacionada con su baja conductividad térmica, alto coeficiente de expansión térmica, alta ductilidad y alto endurecimiento por deformación. Las operaciones de acabado efectuadas en estos aceros son comúnmente ejecutadas con insertos de carburos recubiertos. El rango de las velocidades recomendadas para el torneado de estos aceros son muy conservadoras (200-350 m/min) [4].
La utilización de bajas velocidades de corte, conduce a una baja eficiencia en la producción y consecuentemente altos costos de producción [5]. Al ser este rango improductivo en las condiciones actuales de la tecnología, es necesario determinar el comportamiento de la rugosidad superficial durante el proceso de mecanizado de alta velocidad (HSM).
La rugosidad superficial generada en los procesos de mecanizado ha sido estudiada desde [6] por Sata y en [7] por Dickinson. El efecto del avance de la herramienta, del radio de la punta y del ángulo del filo sobre la rugosidad superficial generada en el torneado fue descrita por Groover y nombrada «rugosidad ideal», enunciada como la mínima rugosidad que se genera en una pieza torneada [8].
La rugosidad superficial es uno de los parámetros de calidad más estudiado por los investigadores que analizan la maquinabilidad de los aceros austeníticos. Por ejemplo, Korkut y colaboradores realizaron un estudio de la rugosidad superficial y el desgaste del flanco para determinar la velocidad de corte optima con el uso de insertos de carburos recubiertos. Los mayores valores de rugosidad superficial durante el torneado se alcanzaron a bajas velocidades (< 180m/min) atribuido a la presencia del crecimiento del filo de corte [9]. Similar resultado fue alcanzado por Ciftci durante su estudio experimental para analizar la influencia de la velocidad de corte (entre 120 m/min y 210 m/min) sobre la rugosidad superficial y las fuerzas de corte [9].
Cuatro años más tarde, Galanis y Manolakos desarrollaron un modelo matemático empírico para predecir la rugosidad superficial con la aplicación de una metodología de superficie de respuesta. Esta investigación fue desarrollada durante el mecanizado de cabezas femorales con una herramienta recubierta de (TiN/Al2O3/TiC) [10].
En el 2012, Çaydas y Ekici implementaron una red neuronal artificial para predecir la rugosidad superficial. La validación de este modelo fue desarrollada mediante un estudio experimental que consideró los parámetros de corte involucrados en el torneado en seco del acero inoxidable AISI 304 [11].
Ese mismo año, Ahilan y otros realizaron una investigación con el propósito de desarrollar un modelo basado en redes neuronales artificiales para predecir las condiciones de corte en tornos CNC. Ellos utilizaron el diseño de experimentos (método Taguchi) para entrenar y validar el modelo neuronal propuesto [12]. En este caso la velocidad de corte máxima utilizada fue 150 m/min.
Selvaraj y otros, desarrollaron una investigación para optimizar los parámetros de corte con el objetivo de minimizar la rugosidad superficial, la fuerza de corte y el desgaste de la herramienta. Los experimentos son analizados usando el método Taguchi, la operación de torneado fue ejecutada en seco y a una velocidad de corte máxima de 120 m/min [13].
En la Figura 1 se puede observar un resumen de las velocidades de corte utilizadas en los principales estudios desarrollados durante el torneado de los aceros austeníticos. Estas investigaciones incluyen no solo el estudio de la rugosidad superficial, sino también investigaciones de desgaste de las herramientas de corte, integridad superficial, fuerzas de corte, potencia de corte y formación de la viruta.
La literatura revela (Figura 1) que existen pocos estudios relacionados con el torneado en seco de los aceros inoxidables austeníticos a velocidades de corte superiores a los 400 m/min. Solo cuatro autores sobrepasaron esta velocidad de corte.
Lin evalúa el comportamiento del desgaste de la herramienta (desgaste del flanco) [14], Fernández-Abia y colaboradores no realizaron el mecanizado en seco [15], Maranhão y Darvim estudiaron la influencia del coeficiente de fricción de la interface herramienta-viruta [16] y por último, Galanis y Manolakos estudiaron el efectode las condiciones de corte en la rugosidad superficialdurante el mecanizado de cabezas femorales de aceroinoxidable AISI 316L, para este estudio la longitud decorte fue de 28 mm [17].
El objetivo de este trabajo es comparar dos métodos para predecir la rugosidad superficial en el acero inoxidable AISI 316L con velocidades de 400 m/min y 450 m/min, uno basado en regresión múltiple y otroen las redes neuronales artificiales del tipo perceptrón multicapa.
Para este propósito fue preciso implementar un diseño factorial completo para investigar el efecto delas condiciones de corte (velocidad, avance, tiempo)en la rugosidad superficial. Los modelos de regresión múltiple son validados mediante los supuestos básicos. Una arquitectura de perceptrón multicapa con algoritmo back-propagation es usado para desarrollar la red neuronal y el criterio para la actualización de los pesos es gradiente descendente. La efectividad de ambos modelos se determina comparando los coeficientesde determinaciones y el error medio absoluto.
2. Materiales y métodos
2.1. Modelos de rugosidad superficial
En el torneado existen muchos factores que afectan la rugosidad superficial como son la herramienta de corte, el material de trabajo y los parámetros de corte. Los factores relacionados con las herramientas son el material, el radio de la punta, el ángulo de ataque, la geometría de la arista de corte, la vibración de la herramienta, etc., mientras que entre las variables relacionadas con el material de la pieza de trabajo se tiene la dureza, las propiedades físicas y mecánicas, entre otras. Por otro lado, las condiciones de corte que influyen son la velocidad de corte, el avance y la profundidad [18].
La selección adecuada de los parámetros de corte y de la geometría de la herramienta resulta compleja y difícil para lograr la calidad superficial requerida [19]. Por tanto, está claro que la selección y obtención de un modelo que describa este proceso es esencial para el mecanizado de los aceros [20].
La rugosidad superficial (Ra) es generalmente definida basada en la Norma ISO 4287 como la media aritmética de la desviación del perfil de la rugosidad desde la línea central a lo largo de la medición. Esta definición es dada en la ecuación (1).
Donde: L es la longitud de medición; y es la distancia entre dos puntos del perfil. La relación entre la rugosidad superficial y las variables de mecanizado puede ser definida como (ecuación 2):
Donde, Ra es la rugosidad superficial medida en μm; V, f, d, r son velocidad de corte (m/min), avance (mm/rev), profundidad (mm), radio de la punta de la herramienta (mm), respectivamente. C, m, n, l son constantes y ε es el error aleatorio [21]. La ecuación (1) puede ser vista como la ecuación (3) para facilitar la representación de las constantes y los parámetros. La rugosidad media aritmética (Ra) y la altura del pico máximo (Rt) de las superficies torneadas pueden ser determinadas por las ecuaciones siguientes (3) y (4):
Donde r, es el radio de la punta (mm) y f, es el avance de corte (mm/rev). Las ecuaciones (3) y (4) muestran que la rugosidad superficial incrementa proporcionalmente con el avance y, además, el aumento del radio de la punta de la herramienta de corte reduce la rugosidad superficial en el torneado.
2.2. Modelación por regresión múltiple
La regresión múltiple es una técnica estadística que permite determinar la correlación que existe entre variables independientes y dos o más variables dependientes.La regresión múltiple se puede utilizar para analizar datos ordinales y categóricos [22]. Por lo general,se realiza primeramente un análisis de varianza (Anova) para determinar los factores importantes involucradosy luego con el uso de la regresión se obtiene un modelo cuantitativo que relaciona los factores más importantes con la respuesta [23].
2.3. Estrategia de predicción usando redes neuronales artificiales
Las redes neuronales artificiales (RNA) son ampliamente usadas en muchas aplicaciones de la industria. Estas son muy populares en la modelación de sistemas debido a su alta eficiencia en la adaptación y en el aprendizaje mediante el reconocimiento de patrones [3].
La red instalada en esta investigación es una red perceptrónica multicapa la cual corresponde en equivalencia a la regresión no lineal múltiple [24]. La red perceptrónica multicapa está compuesta por la asociación de neuronas artificiales organizadas dentro de la red formando niveles o capas.
En este caso corresponde una capa de entrada en la que se introducen los patrones en la red (parámetros de corte), una capa oculta con algunas neuronas y una capa de salida con la variable respuesta (rugosidad superficial). La estructura de la RNA que se muestra en Figura 2 fue utilizada para modelar y predecir la variable dependiente.
La determinación del número óptimo de neuronas de la capa oculta se realizó mediante un proceso de ensayo y error en el que se probaron diferentes variantes. En todo caso, el objetivo fue dotar a la red de un número adecuado de neuronas en la capa oculta para garantizar la capacidad de aprendizaje de las características de las posibles relaciones existentes entre los datos de la muestra.
2.4. Ensayos experimentales
El torneado experimental fue ejecutado en condiciones secas, con el uso del torno multifuncional tipo Okuma Multus B200-W con potencia del motor de 15 kW y rotación del husillo entre 50 rpm y 5000 rpm (Figura 3).
El acero inoxidable AISI 316L fue el material seleccionado para las probetas, este acero es utilizado en la fabricación de productos resistentes a la corrosión y resistentes a altas temperaturas [25]. La composición química es C 0,015 %, Si 0,58 %, Mn 1,50 %, Cr 16,95 %, Mo 2,05 %, Ni 10,08 %, P 0,031 %, S 0,029 % y N 0,059 %.
Las probetas de 100 mm de diámetro y 200 mm de longitud fueron torneadas con insertos recubiertos con calidad Sandvik, GC1115 y GC2015. Los recubrimientos de (TiCN–Al2O3–TiN) con un espesor de 15 μm correspondieron al inserto GC2015 y para el inserto tipo GC1115 su recubrimiento fue de TiN con 5 μm de espesor. Después de la operación de torneado, la rugosidad superficial (Ra) fue medida mediante un rugosímetro CARL ZEISS modelo SURFCOM 1500SD2 (Figura 4).
La geometría de los insertos fue CCMT 12 04 04-MF con rompevirutas, el portaherramienta marca Sandvik de código C6-SCLCL-45065-12 y un adaptador con código C6-391.01-63 060. El ángulo de incidencia principal fue de 7°, el ángulo de ataque de 0 y el radio de la punta de 0,4 mm.
El análisis factorial completo fue el procedimiento utilizado para determinar la relación entre las variables independientes (parámetros de corte) y la variable dependiente (rugosidad superficial (Ra)). Un total de 64 ensayos para dos réplicas fueron desarrollados con dos niveles de velocidades de corte (v), cuatro niveles de tiempo (T), dos niveles de avances de corte (f ) y dos niveles de material de la herramienta, en la Tabla 1 aparecen las variables estudiadas.
3. Resultados y discusión
La rugosidad superficial es ampliamente utilizada como parámetro para indicar la calidad de un producto y en la mayoría de los casos, un requisito técnico importante en el diseño mecánico.
En consecuencia, lograr la calidad de la superficie deseada es de mucha importancia para el comportamiento funcional de un producto [26]. También tiene un impacto en las propiedades mecánicas, específicamente en la resistencia a la fatiga y en la resistencia a la corrosión [19].
Las industrias manufactureras son las encargadas de garantizar al consumidor las demandas crecientes en la calidad superficial y a su vez en obtener productos menos costosos. Por tanto, conocer el efecto de estos parámetros es importante para evaluar la efectividad y productividad del proceso de corte [27].
En esta sección serán comparados y discutidos los resultados obtenidos mediante regresión múltiple y por redes neuronales artificiales.
3.1. Análisis mediante regresión múltiple
Los modelos obtenidos como resultado del análisis de regresión múltiple con la velocidad de 400 m/min se muestran en las ecuaciones (5) y (6) para los insertos GC1115 y GC2015 respectivamente. Los modelos con la velocidad de 450 m/min se muestran en las ecuaciones (7) y (8) para los insertos GC1115 y GC2015 respectivamente.
El coeficiente de determinación (R2) representa la correcta medida de la bondad del ajuste en la línea de regresión determinada por el modelo. Para estos casos los R2 fueron en la velocidad de 400 m/min, 0,92 (GC1115) y 0,80 (GC2015) y para 450 m/min fueron 0,97 (GC1115) y 0,97 (GC2015).
En todos los casos, con el objetivo de validar los resultados de regresión obtenidos se comprobó el cumplimiento de los supuestos básicos de regresión como: la homocedasticidad (Test White), la no autocorrelación de los residuos (Test Breusch-Godfrey), la normalidad ((Test Jarque-Bera) y media nula.
En las Figuras 5 y 6 se muestran las comparaciones entre los valores medidos de manera experimental y los valores estimados de la rugosidad superficial por los modelos correspondientes a las velocidades de 400 m/min y 450 m/min, respectivamente. En estas Figuras se puede observar una fuerte relación entre las variables estimadas y la variable respuesta.
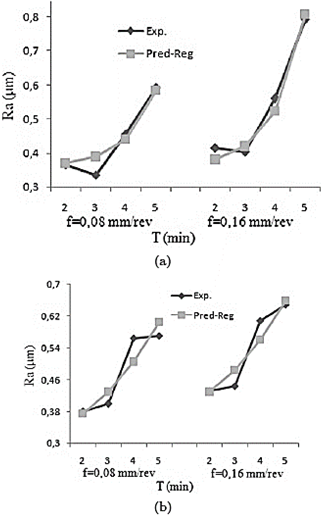
Figura 5. Valores medidos y estimados por regresión múltiple para v = 400 m/min, a) inserto GC1115 y b) inserto GC2015
3.2. Resultados de las redes neuronales artificiales
La estructura de la red aplicada para modelar y predecir la rugosidad superficial en la operación de torneado corresponde al perceptrón multicapa del tipo feedforward Backpropagations. Los datos experimentales fueron utilizados para construir el modelo de las redes neuronales artificiales.
El entrenamiento fue desarrollado a través del algoritmo Levenberg Marquardt. Los mejores resultados fueron obtenidos con la estructura 3-5-1, tres neuronas en la capa de entrada, 5 neuronas en la capa oculta y una en la capa de salida. El software de redes neuronales fue codificado utilizando el Neural Networks Toolbox de Matlab. Los parámetros de la estructura de la red propuesta son mostrados en la Tabla 2.
Los datos de entrada fueron divididos por las velocidades, por tanto, solo se consideraron el tiempo de maquinado, el avance de corte y el tipo de herramienta de corte. Estos datos fueron distribuidos aleatoriamente de la siguiente forma, para el entrenamiento fueron seleccionados el 70 % (22 datos), 15 % (5 datos) para la etapa de prueba y para la validación el restante 15 % (5 datos).
Los resultados obtenidos fueron analizados por métodos estadísticos, los criterios utilizados fueron el error medio absoluto (Emedio, (%)) y el coeficiente de determinación (R2).Las ecuaciones 9 y 10 son utilizadas para calcular estos criterios respectivamente.
Donde N, es el número de ensayos; ti, valores experimentales y t0, valores estimados.
En las Figuras 7 y 8 se puede observar una comparación entre los valores experimentales y los valores estimados de la rugosidad superficial por el modelo desarrollado mediante redes neuronales artificiales.
Los resultados de las redes neuronales demuestran que los modelos propuestos en este estudio son adecuados para la predicción de la rugosidad superficial.
Los valores de los coeficientes de determinación y de los errores medios absolutos están en los rangos aceptables (Tabla 3).
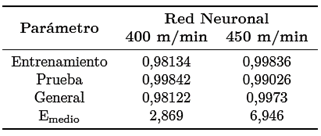
Tabla 3. Valores de coeficientes de determinación (R2) y errores medios absolutos para cada red neuronal desarrollada.
3.3. Evaluación general
Un diseño de experimento factorial completo fue aplicado para determinar los efectos de las variables independientes (velocidad, avance, tiempo y herramientas de corte) del proceso de torneado en seco en la rugosidad superficial. Después de cada ensayo de torneado, los valores de rugosidad superficial fueron registrados para su posterior análisis. En esta investigación fueron desarrollados modelos mediante redes neuronales artificiales y por regresión múltiple. La Tabla 4 muestra una comparación de los resultados según la precisión de los valores obtenidos mediante regresión múltiple y por redes neuronales artificiales. Los resultados se encuentran cercanos a los medidos de manera experimental para todos los modelos. Por tanto, los modelos propuestos pueden ser utilizados para predecir la rugosidad superficial en el torneado en seco del acero AISI 316L. Sin embargo, como se puede observar en la misma tabla, los modelos obtenidos por redes neuronales artificiales producen mejores resultados comparados con los modelos por regresión múltiple.
4. Conclusiones
En esta investigación se ha realizado un estudio para predecir la rugosidad superficial en el torneado en seco del acero AISI 316L. La influencia de variables como la velocidad, el avance y el tiempo de mecanizado fueron analizadas a través de un diseño factorial completo. Los modelos para predecir la rugosidad superficial fueron desarrollados a partir de los datos experimentales. De acuerdo con los resultados obtenidos en este trabajo se plantean las siguientes conclusiones.
Los modelos desarrollados fueron evaluados por sus capacidades de predicción con los valores medidos experimentalmente.
Los modelos propuestos pueden ser utilizados para predecir la rugosidad superficial en el torneado en seco del acero AISI 316L.
El coeficiente de determinación mínimo alcanzado por los modelos fue de 80 % y el máximo de 99 %, indicando la proporción de la variabilidad de los datos explicada por los modelos de regresión, en el caso del error medio absoluto el mínimo fue de 2,869 % y el máximo de 22,78.
Los menores errores medios absolutos fueron obtenidos con los modelos implementados con redes neuronales artificiales.
En investigaciones futuras se podrían desarrollar modelos basados en las redes neuronales y en la regresión múltiple que permitan un estudio de la economía del proceso de torneado en seco.
Agradecimientos
Los autores agradecen a la Secretaría de Educación Pública por proporcionar la beca de investigación en la Universidad Autónoma de Nuevo León (UANL) en México. También al Centro de Investigación e Innovación en Ingeniería Aeronáutica (CIIIA) por el apoyo financiero y tecnológico, además, por todas las facilidades brindadas para el desarrollo del trabajo de investigación.