Introducción
Existen tres elementos claves para que un motor de combustión interna funcione, estos son: aire, combustible y chispa. “El múltiple de admisión provee dos de estos elementos al motor y juega un rol fundamental en el funcionamiento final del mismo” (pág. 171) [1]. “En el ámbito de la competición es necesaria una mayor respuesta del motor en torque y potencia a altos regímenes de giro” (pág. 1) [2] es por este motivo que se implementan soluciones; por lo general, la más sencilla es comprar un múltiple de postventa e instalarlo en el vehículo. Una alternativa son los sistemas con cuerpos individuales de aceleración ITB (Individual Throttle Bodies) en los motores. “El múltiple de admisión debe proveer una carga uniforme y fresca a cada cilindro del motor, por lo cual es un factor importante que afecta a la calidad de la combustión” (pág. 1) [3].
La producción de varios prototipos de un elemento se traduce en mayores gastos en la etapa de diseño y más cuando se trata de optimizar un múltiple de admisión para elevar el rendimiento del vehículo. La importancia radica en eliminar la pérdida y evitar incurrir en los costos que representan la producción e instalación de los ejemplares, así como la medición de valores para la optimización requerida. “En los últimos años, la evolución de las herramientas para el diseño asistido por ordenador, en la rama de ingeniería mecánica, no solo tiende al modelaje de geometrías, sino que integra nuevas herramientas” (pág. 15) [4]. Se pretende así realizar un diseño propio del conjunto ITB para observar la ventaja en el flujo hacia el motor.
“El campo del diseño y análisis de motores ha cambiado drásticamente en los últimos años con la tecnología computacional de rápido crecimiento” (pág. 3) [5]. En consecuencia, el diseño mecánico asistido por computadora CAD (Computer Aided Design) se ha convertido en una herramienta para plasmar los inventos de un ingeniero. Hoy en día, las industrias que dependen del diseño están reduciendo costos al utilizar software CAD para tener una ventaja competitiva (pág. 1) [6]. Modificar un diseño CAD permite ejecutar cambios significativos al modelo. “Esta práctica común es ampliamente aplicada por los campos de la ciencia del diseño y la automatización del diseño” (pág. 477) [7]. Con el apoyo de esta idea se recurre al software de simulación computacional de fluidos CFD (Computational Fluid Dynamics), donde se analizará la velocidad de fluido en las modificaciones del CAD.
“Las herramientas de simulación CFD se han utilizado para la ayuda en el diseño de nuevos instrumentos” (pág. 9306) [8]. Mediante la simulación CFD se busca mejorar la técnica para visualizar la dinámica de un fluido dentro de un elemento mecánico. “Gracias a los avances en sistemas computacionales de alto rendimiento, los fenómenos físicos y químicos pueden ser modelados y premeditados por CFD de una manera relativamente eficiente” (pág. 2) [9].
En el estado del arte se observó estudios que analizan el múltiple de admisión de forma general, pero ninguno centrado a un elemento específico como el ITB. En el trabajo Design and CFD Analysis of The Intake Manifold for the Suzuki G13bb Engine (págs. 1259-1260) [10] se realiza una observación de cómo la geometría afecta a la velocidad de flujo. En los resultados de este modelo se puede evidenciar que, con sus respectivas variaciones como variación de diámetros de toberas y longitud de la cámara, existen afectaciones desde 18 a 30 % que sirve de punto de partida para la discusión de resultados. Por ende, el objetivo de este proyecto radica en el análisis, cuantificación y comparación de datos de velocidad arrojados por la simulación CFD en el software ANSYS de distintas geometrías aplicadas al diseño las toberas de admisión pertenecientes al sistema ITB para un motor Honda K20Z3 y la comprobación estadística de resultados mediante el método chi cuadrado.
Materiales y métodos
El estudio se basa en dos metodologías distintas que en conjunto forman la sustentación del tema, en este caso como primera instancia para la etapa de diseño y modificación de geometrías se usó la modelación teórica. “El modelo que como definición se plantea qué es la representación de un objeto real que en el plano abstracto el hombre concibe para caracterizarlo y poder, sobre esa base, darle solución a un problema planteado, es decir satisfacer una necesidad” (11 pág. 8) [11]. El modelo teórico utilizado fue el diseño de un ITB en el software Autodesk Inventor y la forma correcta de caracterizar su comportamiento se lo realizó a través de la simulación CFD en el programa ANSYS.
Posterior a esto, la metodología usada en la fase de cuantificación y análisis de resultados, fue el modelo comparativo, el cual pretende visibilizar los datos obtenidos mediante un estudio paralelo o de propiedades similares, para determinar la calidad significativa de los resultados. Tal como se explica, la primera etapa para conducir una investigación comparativa consiste en la configuración de una estructura teórica para la elaboración de hipótesis, en una segunda etapa, deberán definirse los casos a elegir como objeto de estudio. En una tercera etapa debe procederse al análisis de los casos, fundamentalmente a partir de la comparación de las variables para determinar, según sea el caso y la estrategia, las diferencias o las semejanzas (pág. 230) [12].
El método que se usará para la comprobación de la dependencia entre las variables principales de la hipótesis planteada, en este caso la modificación de la geometría y las velocidades máximas y mínimas de flujo, será la prueba estadística denominada chi cuadrado, mediante el uso de la calculadora Numworks la cual nos indicará si existe y que tan fuerte es la relación entre las variables. Como siguiente paso es necesario explicar la manera en que el software logra predecir el flujo de aire, y esto se lo debe a la resolución de ecuaciones ligadas a la conservación de masa, energía y movimiento.
La solución se da mediante el uso del método de volúmenes finitos FVM (Finite Volume Method) a la ecuación de Navier-Stokes, que son métodos numéricos para resolver problemas de fenómenos de transporte relacionados con el flujo de fluidos comprimibles o incompresibles junto con modelos de turbulencia y ecuaciones de continuidad para sistemas de uno o varios componentes (pág. 3) [13], la cual configura la simulación de la mecánica de fluidos, esta ecuación se define como:
Donde,ɸ es la variable transportada a través de un medio de densidad ρ y constante de difusión Γ que se mueve a una velocidad V con un término fuente Sɸ [14]. Para que se realice correctamente se acude al mallado que se trata de una descomposición de todo el elemento en volúmenes de control, como se observa en la Figura 1, por donde cada uno de estos elementos será un caso de estudio en donde la ecuación se aproximará y resolverá a valores o propiedades del fluido indicadas.
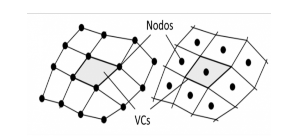
Fuente: Ortiz, D., INTRODUCCIÓN AL CFD. (ESSS Engineering Simulation and Scientific Software), 2022. [14].
Fig. 1: Volúmenes de Control en mallado.
Las variables que se definieron dentro del proceso de simulación fueron cruciales para la obtención de datos fiables, para esto se decidió apoyarse como velocidad del aire en m/s para coches de rally de 55 a 60 m/s (pág. 175) [15], mientras que los valores del fluido se las determinó basándose en las propiedades del aire a 1 atm de presión, que son las condiciones ideales (pág. 908) [16]. Todos los valores con sus respectivas unidades se resumen en la Tabla 1.
Posterior a definir esto, se dará el procedimiento y los materiales usados en las distintas etapas de la investigación, a continuación se presentan los pasos realizados en el estudio, que de manera gráfica se muestran en un flujograma dentro de la Figura 2.
Diseño del ITB
Para el diseño CAD de estos ITB se utilizó el software Autodesk Inventor 2021.4.4 del año 2021 pues es un programa muy completo al cual se accede gracias a una licencia estudiantil. Es importante recalcar que los softwares CAD comerciales, en especial los de diseño automotriz son bastante complejos y el uso de su interfaz no es muy amigable (pág. 340) [17]. Por esta razón, se pretende realizar un modelo donde el diseñador debe conocer el manejo del programa para evitar errores. A la hora de diseñar una pieza o un sistema para un componente que ya existe, uno de los retos más complejos es lograr que la parte o pieza diseñada encaje y funcione correctamente con el componente ya existente. En el caso del múltiple, es fundamental que el cuerpo empalme correctamente con todos los orificios del cabezote del motor. Si los orificios del cabezote y la admisión no coincidan perfectamente, generaría un problema de turbulencia Figura 3.
Lo que se hizo para realizar el levantamiento geométrico, lo más preciso para obtener la posición de orificios y tamaño del cabezote es hacer una fotocopia del empaque de la admisión a culata. Con este procedimiento se tomó dimensiones al cabezote y se escaló en Inventor para que sea el tamaño real.
Una vez escalada la foto se puede traducir magnitudes en Inventor y generar todas las líneas que deben ser idénticas al cabezote del motor y en el múltiple diseñado. Todas las medidas que se toman como referencia en la imagen importada a Inventor se deben corroborar con un pie de rey en el cabezote físico. Las medidas generales del diseño se resumen en la Tabla 2.
Una vez que el diseño del empaque ya está completo es importante corroborar que son exactamente iguales el modelo al cabezote. La forma más efectiva de hacer esto es exportando el dibujo como un CAD para enviar a un corte con láser en cartulina y comparar el perfil con el cabezote. Esto es una forma de evitar realizar correcciones en la pieza de aluminio ya maquinada al ver que existen desfases o pequeñas cejas entre el cabezote y el diseño del múltiple. Este proceso se repite varias veces hasta que sea una réplica exacta, no puede existir ningún desfase entre el corte láser y la culata.
Después que se obtiene una copia exacta se puede realizar medidas de espacio y de las curvas que deben tener las gargantas del ITB para levantar el diseño. Es muy importante tomar en cuenta el ángulo que tiene el inyector en el sistema de admisión original para asegurar que sea el óptimo al momento de entrar el combustible a la cámara. Así mismo, se deben definir los ángulos que tendrán las toberas en comparación al empaque y el codo entre ambos.
A continuación, se toman las dimensiones de las mariposas que se van a instalar en cada tobera para poder maquinar e instalar los soportes en cada una de las gargantas. Finalmente, se toma como referencia el ángulo de los inyectores para definir los puntos de anclaje del riel en el sistema de admisión. Al terminar el CAD del sistema es importante realizar modelos simplificados tanto de las mariposas como de las cornetas, para asegurarse que todo encaje.
Modificación de geometría
El principal objetivo de este análisis fue determinar qué variaciones en la geometría del sistema otorgaría mayores prestaciones de velocidad al aire que se mueve dentro del sistema. Se realizó dos modificaciones diferentes al diseño para examinar independientemente cada una, y el estudio final será el análisis de las dos variaciones unificadas en un solo diseño. De esta forma determinar cuál de los tres diseños modificados tienen mejores prestaciones en comparación al modelo control. El motivo de las dimensiones utilizadas es no intervenir en el espacio físico de la pieza y su entorno dentro del motor, es decir no escoger medidas que choquen los diámetros de las gargantas y que no sobrepasen el espacio debajo del capó. El diámetro interior original es de 52 mm y se le incrementa a 62 mm, así mismo el diámetro exterior original es de 60 mm que se le incrementa a 70 mm, por lo tanto, en ambos casos hay un aumento aproximado del 19 % en comparación al modelo control. La segunda modificación que se realiza es prolongar las gargantas de 32 mm a 52 mm lo que significa un incremento aproximado del 63 % en comparación al original. La modificación final unifica la geometría del primer y segundo modelo en un solo sistema, por ende, el diseño tiene un incremento del 19 % en el diámetro de los ductos y gargantas 63 % más largas en comparación al modelo control. Al culminar con los modelos es de suprema importancia simplificarlos para evitar procesos innecesarios en el análisis CFD. Lo que se realizó fue retirar todos los orificios, empalmes, soportes y redondeados del diseño y dejarlo en su mínima expresión.
Proceso de simulación CFD
Para la simulación CFD se utilizó el programa ANSYS Fluent versión R1 del 2021 que permite realizar un análisis de flujo con diferentes condiciones y variables a estudiar. “Mediante el análisis y simulación con herramientas de Ingeniería Asistida por Computador CAE (Computer Aided Engineering), se pueden validar los Diseños Modelados por Computador CAD” (pág. 189) [18]. Este programa va de la mano con el software Work Bench de ANSYS versión R1 del 2021, mismo donde se unifica el diseño, mallado, configuración, simulación y los resultados del proyecto. Para empezar todo el proceso se crea un nuevo proyecto en Work Bench y empezamos arrastrando un proceso de Fluent a la pantalla.
El proceso de simulación empieza desde la exportación del documento de Autodesk Inventor al modelador de ANSYS denominado Design Modeler. En este espacio se deben realizar algunas tareas para que el software entienda cuáles son fluidos y cuáles son los sólidos o cuerpos del diseño. Para esto se utiliza la función “Fill” donde se le indica al programa cuáles son las caras por las que debe simular el flujo del aire. En este caso se seleccionan las caras internas de las cuatro gargantas individualmente, posteriormente se las agrupan y se denominan como “fluido”.
La siguiente etapa del proceso es el mallado del diseño, para esto se utiliza el mismo sistema de mallado del Work Bench. El área de estudio se divide en volúmenes de control, los cuales son discretizados, a efectos computacionales, por el método de volúmenes finitos, que es el procedimiento convencional; mediante esta aproximación, las ecuaciones se resuelven y son validadas en cada elemento computacional. (pág. 1) [20] Para obtener el equilibrio y análisis de cada célula. Por tanto, el número de estos elementos influyen considerablemente en el proceso de resolución numérica. (pp. 33-35) [21]En este caso el ANSYS estudiantil permite analizar hasta 512.000 partes, por esta razón se optó por realizar piezas de 2 mm que equivalen a aproximadamente medio millón de partes.
Para empezar esta fase se debe indicar al programa una vez más los sólidos, fluidos, entradas y salidas de aire, seleccionándolos individualmente. Una vez especificado todo se puede configurar el mallado, para esto se utilizó el método llamado “Hex dominant method” para el sólido y “tetrahedrons” para el fluido, generando un mallado mixto. Este mallado combinado genera triángulos en las áreas de análisis y cuadrados en áreas donde no vamos a realizar el estudio, de esta manera siendo eficiente y preciso para la solución de elementos/volúmenes finitos Figura 6
El siguiente paso es la configuración y simulación del proyecto, estos dos procesos se generan en una sola etapa en la aplicación de “Fluent” donde el computador realiza los cálculos. Para empezar, se introduce los materiales, aluminio como el sólido y aire como el fluido a simular. Posterior, se procede a ingresar variables como la gravedad, velocidad de partida, punto de referencia del inicio y el rango de la simulación. Los programas CFD trabajan con iteraciones que es el proceso que la computadora utiliza para encontrar los valores reales y correctos de la simulación (pág. 45) [19]. Por ende, se le debe indicar al programa cuántas iteraciones correr para que los resultados sean más precisos. Después en la fase de método de cálculo se ingresa la cantidad de iteraciones que se registran en la simulación. En este caso se realizaron 500 iteraciones de cada modelo, y se guardan cada 30 iteraciones para evitar tener un exceso de información.
Una vez configurado se realiza un proceso de inicialización donde le indicamos al sistema desde donde va a analizar el flujo, en este caso desde la entrada del sistema. El paso final antes de empezar a simular y calcular los datos es la especificación del trayecto que va a simular el sistema. Se le debe especificar al software qué es lo que queremos analizar, en este caso tanto la entrada y salida como todo el cuerpo interno de las toberas. Una vez seleccionado el programa indicará qué es exactamente lo que se va a simular y el flujo o dirección en el que se realizará el CFD. Especificado todas las variables y trayectos se genera la simulación y los cálculos respectivos en la ventana de “Run calculation” que da paso a los resultados. Para el paso final se indica al programa qué es lo que se quiere observar, por esta razón es importante conocer la zona de análisis Figura 7.
Para empezar a configurar los resultados primero se debe visualizar el modelo físico, para esto se le aumenta la transparencia para poder observar el interior. La velocidad en el estudio se la graficó como un vector, por esta razón se utiliza la función con el mismo nombre para reconocer mediante colores los distintos resultados. Se le debe indicar la cantidad de puntos o vectores que deseamos visualizar dentro de cada tobera, en este caso se indicaron 500 puntos para tener una mejor figuración de los efectos en los modelos. Ya con los vectores configurados se pueden observar la regla de las diferentes velocidades que existen dentro de las toberas.
Resultados y Discusión
En la Figura 8 se observan los resultados de las velocidades en este modelo de control y de las 3 iteraciones que se crearon para el estudio. En la parte superior de cada imagen se indica el nombre del modelo ya sea el control o una de las tres modificaciones.
En la regla de escala de colores en el lado izquierdo de cada imagen se visualizan las diferentes velocidades que se presentan en los análisis, empezando desde las bajas en azul hasta las altas en rojo, estas velocidades son medidas en metros sobre segundo. Finalmente, en la parte inferior de las capturas se puede ver una pequeña regla que está a escala que permite tener una idea de la dimensión del objeto.
Al realizar el análisis de control se observa que nuestra regla de velocidades indica un rango entre 13,050 m/s hasta una velocidad máxima de 100,593 m/s dentro del modelo. La media de velocidad en el modelo es de 56,821 m/s pues gran parte del modelo se encuentra en el color de la escala. Las velocidades más altas del sistema se encuentran en el centro del modelo, precisamente donde el ducto tiene una pequeña curvatura que genera un alza en la velocidad de los gases. Con este estudio de control podemos realizar comparaciones de resultados entre diferentes modelos.
En la primera modificación se varió la circunferencia de la tobera de entrada, generando una fuerte ganancia en las velocidades del fluido. A diferencia del control la velocidad promedio de este es casi la velocidad máxima del control, la velocidad promedio es de 99,457 m/s igualmente en las gargantas del diseño. En el segundo modelo se puede observar una mayor escala de colores por las ganancias de velocidad mayormente agresivas que el modelo inicial.
La segunda modificación parece ser una réplica del objeto de control, en este caso lo que se realizó fue un alargamiento de las gargantas. Como se observa, la ganancia con estas modificaciones es mínimas, la velocidad promedio también es muy cercana a la original con apenas 57,267 m/s que es una ganancia mínima.
Finalmente, la última variación de este estudio tiene la mezcla de las dos primeras modificaciones, tiene una garganta de mayor circunferencia y también son más largas. En esta es donde se puede evidenciar la mayor ganancia de los tres, pero asimilándose mucho a la modificación dos. Este diseño al tener gargantas más largas podemos ver que a lo largo de estas existen rastros de pérdidas de velocidad, pero aun así su velocidad promedio es la mayor de todas con 100,673 m/s lo que nos indica que es el más eficiente de los cuatro. Todos los resultados se muestran en la Figura 9, mientras que los porcentajes se encuentran en la Tabla.
En la sección de resultados y discusión del artículo “Design and CFD Analysis of The Intake Manifold for the Suzuki G13bb Engine” (págs. 1260) [10] se habla sobre modificaciones en todo el múltiple de admisión, variando la longitud, diámetros de las toberas y agregando elementos, esto expresándolo en 3 modelos distintos. Obteniendo como resultados una variación máxima de velocidad de 30,03 % en su modelo 2 el cual incorpora toberas adicionales de mayor longitud, mientras que en su modelo 3 en el cual aumentan el diámetro de toberas llegan a alcanzar un 18,8 % de ganancia en velocidad. Al basarse en este análisis se demuestra que una ganancia del 52 % en un sistema de alto rendimiento si es viable y significativa, el porcentaje elevado se traduce a las dimensiones del elemento, en este caso el ITB al ser una pieza más pequeña, al realizar limitadas modificaciones se obtiene consecuencias significativas. Con el fin de determinar la fiabilidad de los datos se realizó la prueba estadística de Chi-Cuadrado, “un método que mide la diferencia entre los valores esperados y los valores observados en una distribución entre dos variables” (pág. 822) [22]. Se usó la calculadora Numworks versión software 18-2022, con un nivel de significancia del 5 % el cual indica que, al rechazarse la hipótesis nula, sí existe una dependencia entre las variables propuestas. Los resultados de esta prueba muestran que la velocidad del aire dentro del ITB depende directamente de la geometría de las toberas de admisión, corroborando la premisa inicial de este estudio. El proceso automatizado de la calculadora se demuestra en la Figura 10.
Conclusiones
Durante el proceso de estudio del presente artículo se dedujo que la geometría en un colector de admisión específicamente del sistema de cuerpos individuales de aceleración (ITB), tiene una relación directa con la velocidad de aire que fluye en el interior de este. El procedimiento de la simulación fluido dinámica acompañada de un análisis estadístico Chi cuadrado demostraron el enlace dependiente de estas dos variables.
La consecuencia principal de la modificación en las geometrías del elemento fue la ganancia exponencial en velocidades bajas, y ganancias significativas en velocidades altas de flujo. Lo que determina esta premisa se justifica en cada modelo. En la modificación 1 y 3, el aumento del 19 % en el diámetro de las toberas a la entrada genera un efecto Venturi en el segundo tramo con diámetro sin modificar, provocando una mejora del 50 % y 52 % respectivamente en comparación al control, equivalente a una velocidad máxima promedio de 152 m/s en contraste a la velocidad máxima del elemento control que alcanzó los 100 m/s. Mientras que en el modelo 2 que únicamente incorpora un aumento del 63 % de longitud del colector, se generó una ligera pérdida del 0,9 % que equivale a 1 m/s más lento, esto debido a una mayor área de rozamiento, pero al tener un perfil similar al elemento de control, se considera a sus cambios no considerables.
La mejor modificación después de realizar la simulación es el tercer modelo, esto se debe a que es la incorporación de ambas variaciones en un solo sistema en donde se generan los mayores porcentajes de ganancias en velocidades máximas y mínimas.
Demostrando así que un rendimiento elevado en un elemento de preparación como el ITB dependerá de hasta cierto punto del incremento de diámetro en el primer tramo de la garganta. El concepto fundamental detrás de la ganancia de velocidad es mantener una diferencia de diámetros que provoque el efecto Venturi, el modelo propuesto no solo implementa esto sino además un ángulo que provoca velocidades altas en el tramo medio de la pieza.
Es fundamental tomar en cuenta que, en la etapa de diseño el modelo tiene que ser realizado como un solo cuerpo para que el software logre comprender las zonas de análisis para la simulación y existan menos regiones de contacto que confundan al programa en etapas como el proceso de mallado. El paso esencial radica en disponer adecuadamente las distintas variables en la aplicación Fluent pues sin esto los resultados no serían fiables ni comparables.
Esta investigación es el primer paso al estudio práctico de todo el sistema de admisión no únicamente de manera general como se pudo observar en distintos estudios citados a lo largo del trabajo, sino también de los distintos elementos específicos, tratándolos por etapas, por ejemplo, segregándolos desde la entrada principal hasta el orificio de la válvula de admisión. O incluso simulando más variables como temperatura y presión que son aspectos que afectan a la geometría de los elementos y que tienen como objetivo final el mejorar el rendimiento del auto interviniendo en los factores que favorecen a la combustión dentro del motor.
Gracias al estudio realizado y los resultados obtenidos, se enfatiza en la ejecución de este tipo de simulaciones fluido-dinámicas computacionales. Pues la importancia de disminuir reprocesos y tener consecuencias significativas como se demostró en este estudio, ayudan de manera notable en las etapas de desarrollo y producción de un elemento o sistema mecánico para su posterior implementación en el vehículo, incidiendo directamente en la mejora de rendimiento de este.