1. INTRODUCCIÓN
El empaque más empleado por la industria farmacéutica es el tipo blíster, estos empaques son desechados junto con la basura común a pesar de contener material que se puede recuperar, lo cual contribuye al creciente problema de contaminación ambiental por acumulación de desechos sólidos no degradables. En Ecuador, este tipo de desechos están destinados a ser quemados o depositados en sistemas de relleno sanitario, lo cual implica que no se reutilice el material recuperable que en este caso es el aluminio (INEC, 2016).
Empaques tipo blíster
En la industria farmacéutica, se utilizan los empaques tipo blíster como medio de embalaje para los medicamentos con forma de cápsulas, pastillas y tabletas. Los empaques deben conservar la integridad de los productos evitando que interactúen con el medio ambiente y sus factores de humedad o temperatura, por lo que las propiedades de barrera de los materiales que conforman el blíster son muy importantes al igual que su prolongado tiempo de vida útil (Alfipa, 2020).
Existen varios tipos de blíster para medicamentos, los principales son: (1) Push Through Blister, (2) Blíster laminado multicapa de aluminio con papel y/o PET, (3) Peel-Off-Push-Through, mostrados en la Figura 1. De éstos, el primero es el más empleado por la industria, los materiales poliméricos usados para su elaboración son: PE (polietileno), PVdC (cloruro de polivinilideno) y PVC (policloruro de vinilo), siendo este último el más común. (Yu et al., 2016). El aluminio es el otro material principal en los blísteres independientemente de su tipo, el amplio uso de ambos materiales se debe a su bajo costo, alta durabilidad y excelentes propiedades de barrera (Röchling, 2016; Pilchik, 2000).
Degradación de polímeros
Se considera degradación a cualquier alteración en las propiedades de un material debido a las condiciones de servicio o interacciones con su entorno. En este estudio, se utilizó la degradación térmica, la cual consiste en someter a los polímeros a temperaturas elevadas las cuales están entre 150°C y 200°C durante un tiempo, con esto se logra el ablandamiento de los polímeros (Posada, 2012; Serrano, 2010).
Tratamientos de recuperación de materiales asociados con el PVC
La recuperación de materiales metálicos que se encuentran adheridos o embebidos en PVC suele enfrentarse a la contaminación ambiental como una de sus principales problemáticas, ya que generalmente estos procesos involucran la incineración del material plástico para liberar el metálico, lo que genera altos niveles de contaminación y afectaciones a la salud, además de comprometer la integridad de los equipos de incineración debido a la naturaleza corrosiva de los gases emitidos. Por tal motivo se han desarrollado procesos que pretenden eliminar el impacto negativo de la incineración de PVC haciendo que esta no sea necesaria o tratando de beneficiarse de la misma. Un ejemplo es la pirólisis, que se enfoca en darle un uso final al polímero en lugar de recuperarlo, ya que durante la pirólisis el polímero es degradado hasta convertirlo en una fuente energética en forma de gas y coque (Aracil, 2008; Reuter, 2005; Rubinos, 2007).
Vinyloop
El proceso denominado Vinyloop tiene como objetivo reciclar el PVC haciendo uso de una disolución y filtración selectiva, a la vez se recuperan de forma indirecta los materiales que lo contaminan, la calidad del PVC recuperado es prácticamente la misma del material original, ya que no pierde sus propiedades en forma significativa ni se ve contaminado después de ser procesado. Una planta de procesamiento basada en Vinyloop resulta muy costosa, por lo que este proceso se aplica solamente cuando no se puede separar el PVC del agente contaminante por ningún otro método (Vandevyver & Thamm, 2012).
Aluminio
Es uno de los materiales más abundantes en el planeta tierra, pero no está libre en la naturaleza, siempre se encuentra combinado con otros minerales formando silicatos y óxidos, estas mezclas son denominadas bauxita, el proceso para obtener aluminio a partir de la bauxita es de elevado consumo energético e impacto ambiental negativo (Askeland, 1998). En el presente estudio al tratarse de recuperación de aluminio se estudiará el aluminio secundario y no el aluminio primario. (Li, 2008).
Aluminio secundario
Comúnmente llamado aluminio reciclado, tiene varias ventajas sobre el aluminio primario, una de ellas es el ahorro energético, para producir una determinada cantidad de aluminio reciclado; se requiere solo el 5% de la energía necesaria para producir la misma cantidad de aluminio primario a partir de la bauxita (ARPAL, 2015; Frees, 2008; Millán et al., 2015).
Estado de la técnica
Actualmente se han desarrollado procesos de recuperación del aluminio de empaques tipo blíster, mediante la interacción de procesos químicos, usando la lixiviación de PVC con algunos solventes orgánicos y también implementando la fusión de las láminas de aluminio con sales de cloro y flúor. Otro método empleado es la fusión completa del PVC (Saeed, 2004), pero al realizar este proceso se genera una gran cantidad de contaminantes, debido a que es un proceso que requiere de agentes químicos; en este estudio se busca recuperar el aluminio sin la necesidad de utilizar químicos y utilizar procesos mecánicos y térmicos sin llegar a la fusión del PVC.
2. METODOLOGÍA
El proceso planteado para recuperar el aluminio consistió en dos etapas; clasificación, procesamiento, reprocesamiento de los blísteres y fusión del aluminio recuperado (ver Figura 2).
Clasificación de los empaques tipo blíster
El proceso de clasificación se realizó para garantizar que en la muestra a procesar solamente se encuentren blísteres del tipo Push Through Blister, en adelante mencionado como blíster tipo (1). La clasificación consistió en separar los blísteres tipo (1) de cualquier otro tipo de estos empaques, los cuales no fueron utilizados en este estudio debido a pruebas iniciales realizadas y por presentar una mala recuperación como se observa en la Figura 3a. Los blíster tipo (2) poseen varias capas de plástico y los tipo (3) presentan varias capas de papel. La presencia de dichas capas hizo prácticamente imposible la separación del aluminio, para lograr la separación de las capas de plástico y papel fue necesario incrementar la temperatura alrededor de 280°C, lo cual deterioró la delgada capa de aluminio al ser expuesta a contaminantes formados por la degradación de los polímeros y resinas presentes en los blísteres.
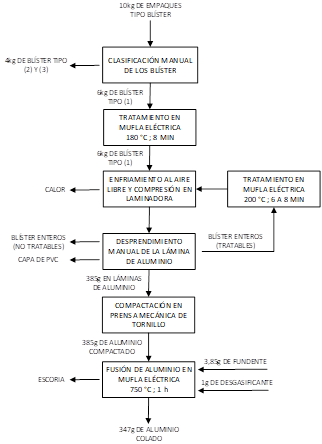
Figura 2 Diagrama del proceso de recuperación de aluminio de los empaques tipo blíster por medios térmicos y mecánicos
Procesamiento y reprocesamiento de los empaques tipo blíster
Tanto el procesamiento como el reprocesamiento se dividieron en 4 etapas: Calentamiento, enfriamiento, compresión y desprendimiento de la lámina de aluminio. Estas etapas se ejecutaron en el orden mencionado, en algunos casos la compresión no fue necesaria para la separación de la lámina de aluminio del plástico.
En la fase de calentamiento, se introdujeron los blísteres tipo (1) en una mufla eléctrica precalentada a 180°C, el volumen introducido fue tal que permitió colocar la mayor cantidad manteniéndolos correctamente espaciados entre sí durante un período de 8 minutos. En la fase de enfriamiento, las muestras tratadas se enfriaron hasta la temperatura ambiente en el aire; el desprendimiento de la lámina de aluminio fue manual y relativamente sencillo. Se obtuvo la lámina casi entera, sin embargo, en algunos casos no fue posible este desprendimiento, por lo que requirió una fase de compresión que consistió en pasar las muestras tratadas entre los rodillos de un laminador dúo de laboratorio. Este proceso ayudó a romper ciertas capas adhesivas que se cristalizaron por efecto del calentamiento y enfriamiento previos, también sirvió para aplanar los relieves presentes en los blísteres que contribuyen en la adherencia de la lámina metálica al polímero.
Las muestras en las que fue difícil obtener la lámina de aluminio fueron reprocesadas siguiendo los mismos pasos, incrementando la temperatura de la mufla a 200°C con un tiempo de calentamiento de 6 a 8 minutos. Después de los procesos descritos se compactaron las láminas de aluminio obtenidas utilizando una prensa mecánica de tornillo de 10 toneladas de capacidad.
Fundición del aluminio recuperado
La fundición se llevó a cabo en un crisol de acero siguiendo un proceso estándar para fundir aluminio reciclado. El proceso se realizó con una mufla eléctrica precalentada a 600°C con el crisol en su interior, se introdujo el aluminio junto con una carga de fundente equivalente al 0,5% y desgasificante al 0,125% del peso del material a fundir; se incrementó la temperatura de la mufla hasta 750°C durante una hora, finalmente se agregó una segunda carga de fundente y desgasificante en las mismas proporciones iniciales antes de colar el metal fundido.
Caracterización del material obtenido
Se realizaron ensayos de caracterización tanto al aluminio recuperado como a las muestras del PVC que forman parte del blíster. Para la caracterización del aluminio colado se realizaron ensayos de dureza, ensayos de espectroscopía por chispa y ensayos metalográficos para revelar su microestructura, mientras que para analizar el PVC se realizaron ensayos de calorimetría diferencial de barrido.
Ensayo de espectroscopía por chispa
Este ensayo se realizó bajo la norma ASTM E1251-17a (2017), las probetas (Figura 4) se maquinaron para cumplir las exigencias del equipo que se utilizó para el ensayo (espectrómetro BRUKER modelo Q4TASMAN). Estas exigencias son dimensionales para probetas de sección circular el diámetro y el espesor mínimos deben ser de 12mm y 3mm respectivamente, por lo que las probetas finales tuvieron un espesor de 4mm.
Ensayo metalográfico
La elaboración de las probetas de aluminio colado, requeridas para realizar los ensayos metalográficos, se basó en la norma ASTM E3-11 (2017), donde se establecen los procedimientos para la extracción, montaje, desbaste grueso, desbaste fino y pulido de la muestra. Para este último paso se utilizó una suspensión de alúmina y luego otra de diamante de 1μm. Posteriormente se realizó el ataque químico para revelar las microestructuras de la muestra, aplicando el reactivo KELLER y una mezcla de 1ml de ácido fluorhídrico en 200ml de agua destilada de acuerdo con la norma ASTM E407-07 (2015).
Análisis por microscopía electrónica de barrido
El análisis de la muestra se realizó utilizando el microscopio electrónico de barrido Vega II LMU (Tescan), con analizador de rayos X Bruker, se utilizó 10.0 kV y D. imp. de 22.41 kcps.
Ensayos de dureza
Estos ensayos se realizaron con base en la norma ASTM E18-20 (2020), con una carga de 60 kgf y el indentador de 1/8 in.
Calorimetría diferencial de barrido (DSC)
Los ensayos DSC se realizaron a las láminas poliméricas para complementar la interpretación de los resultados obtenidos al procesar y reprocesar las muestras durante el desprendimiento de las láminas de aluminio. El ensayo se realizó utilizando el calorímetro diferencial de barrido TA Instruments DSC Q2000 en un rango de temperatura de 70°C a 220°C, empleando gas nitrógeno y una velocidad de calentamiento de 10°C/min.
3. RESULTADOS Y DISCUSIÓN
Resultados de la aplicación del método de recuperación planteado
En la Tabla 1, además de los resultados obtenidos, se presentan los tratamientos aplicados a los blísteres para lograr separar la lámina de aluminio del PVC. En la columna Al, se indica el número de láminas de aluminio recuperadas de cada muestra, dichas muestras constaban de 20 unidades de empaques tipo blíster, y cada porcentaje de láminas obtenidas fue calculado promediando los resultados de tratar tres muestras, por ejemplo: de la muestra 1, se obtuvieron 12 láminas de Al (60%), de la muestra 2, se obtuvieron 15 láminas de Al (75%) y de la muestra 3, se obtuvieron 13 láminas de Al (65%); promediando las 3 muestras, el porcentaje de aluminio obtenido es del 66,7%, este valor corresponde a uno de los tratamientos durante 8 min.
El tratamiento considerado como más idóneo es el de 180°C durante 8 minutos, esto teniendo en cuenta el porcentaje de láminas de aluminio obtenidas y el grado de descomposición presentado por el PVC, si bien se pueden recuperar más láminas a mayor temperatura, la contaminación generada es mayor. Bajo las condiciones de tiempo y temperatura seleccionadas, existieron algunas marcas de blísteres en particular que presentaron resultados excepcionalmente buenos, ya que además de ser muy fácil desprender el aluminio de estos, también fueron los que resultaron menos degradados (Figura 5), debido a que necesitaron temperaturas un poco más bajas que los otros blísteres (de 160°C a 180°C). Al trabajar a 180°C durante 10 min, se obtuvo buenos resultados para separar la lámina de aluminio del plástico, los blísteres presentaban un mayor grado de degradación y producían una mayor cantidad de gases por la permanencia en el horno.
Resultados del proceso de fusión del aluminio obtenido
Antes de ser fundido, el aluminio fue compactado debido a que el rendimiento al fundir el papel de aluminio es muy bajo a causa de que el espesor del material es mínimo, dicho problema se soluciona con la compactación. Esto se evidencia con el rendimiento obtenido de la fundición, de una masa total de 385 g en láminas de aluminio, se recuperaron un total de 347 g de metal colado, lo que significa que el rendimiento fue del 90%. Los 385 g en láminas de aluminio que fueron fundidas se obtuvieron de aproximadamente 6 kg de blíster.
Caracterización del aluminio recuperado
Los resultados de los ensayos realizados al aluminio recuperado fueron comparados con los resultados arrojados tras aplicar los mismos ensayos al aluminio colado que se obtuvo del papel de aluminio, esta comparativa se hizo por la similitud entre ambos, el papel de aluminio siempre se fabrica de determinadas aleaciones.
Resultados de los ensayos de espectroscopía por chispa
El análisis se realizó con el espectrómetro de la marca BRUKER modelo Q4TASMAN. En la Tabla 2 se indican los resultados, en la cual MA presenta la muestra de aluminio recuperado de los blísteres, y MB la muestra del aluminio del papel de uso doméstico. Los resultados de este ensayo revelaron que en ambas muestras analizadas el elemento más abundante después del aluminio(Al), es el hierro (Fe), luego de observar todos los demás elementos presentes en cada muestra y las proporciones de los mismos, se hace una comparación con el Metals Handbook de la ASM (ASM, 2004), evidenciándose que el aluminio extraído de los blísteres puede clasificarse como una aleación de la serie 1XX.X (Al > 99,0%), y se encontró que las muestras analizadas presentan variaciones respecto de los valores de los contenidos de impurezas de Silicio y Hierro.
Tabla 2 Elementos presentes en las muestras ensayadas por espectroscopía por chispa (porcentajes en peso)
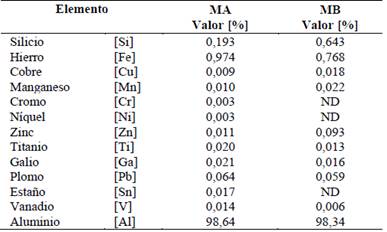
El material recuperado de los blísteres se puede clasificar como un aluminio puro que presenta un alto contenido de Fe, pues la cantidad de aluminio presente es muy cercana al 99%.
Ambas muestras de aluminio tienen varios elementos en común, pero los porcentajes de estos siempre son diferentes en el aluminio obtenido de los blísteres, en la muestra recuperada de los blísteres existen elementos que no se encuentran en la otra muestra como el cromo (Cr) y el níquel (Ni), los cuales se suelen encontrar en el aluminio en cantidades muy bajas. Existen otros elementos como el galio (Ga), plomo (Pb), vanadio (V) y estaño (Sn) que pueden ser considerados contaminantes ya que además de no ser común su presencia en el aluminio (Al), son empleados en la producción de ciertos medicamentos, incluso se utiliza estroncio (Sr) en la elaboración de resinas y colorantes como las utilizadas en los mismos blísteres.
Ensayos metalográficos
Las microestructuras de las muestras A y B corresponden a una aleación de Al solidificada. El silicio se aprecia precipitado como partículas gruesas tipo placa y angulares. La fase secundaria de Si se representa como partículas de color negro (flecha), en la Figura 6 y Figura 7, se aprecia la distribución del microconstituyente intermetálico Fe3SiAl12, el cual se presenta con forma de escritura china de color gris, distribuida de manera no homogénea en la matriz de α-Al.
Ensayos SEM-EDS
El análisis SEM realizado en la muestra A, presenta los resultados como se puede observar en la Figura 8, se identifica los materiales con mayor concentración con diferentes colores, aluminio (Al) color rojo, hierro (Fe) color rosado y silicio (Si) color azul.
Ensayos de dureza
El objetivo de realizar los ensayos de dureza es cuantificar una de las propiedades mecánicas que permite evaluar la resistencia mecánica del material obtenido, se realizó 5 mediciones de dureza al aluminio obtenido de los blísteres y al papel de aluminio, esto con el fin de poder comparar sus valores entre sí. El ensayo reveló que el papel de aluminio de uso doméstico es más duro que el recuperado de los blísteres, las durezas obtenidas se muestran en la Tabla 3, la diferencia entre las durezas se debe al contenido de hierro de las muestras analizadas.
Ensayos de calorimetría diferencial de barrido (DSC) aplicados al PVC
Para realizar estos ensayos, se empleó el calorímetro diferencial de barrido TA Instruments DSC Q2000, con una sensibilidad calórica de 0,2 μW, precisión calorimétrica de +/- 0,05 % y apreciación de temperatura de +/- 0,01 °C. En la Tabla 3, se numeran las muestras ensayadas y los tipos de resultados que estas entregaron durante el proceso, ya que fueron elegidas en función de cómo respondieron ante la aplicación del método planteado. En la Figura 9, se presentan las curvas calorimétricas obtenidas como resultado de ensayar las 4 muestras poliméricas de la Tabla 4, las cuales pertenecen a cuatro casas comerciales que distribuyen medicamentos en los hospitales públicos de Quito.
Las curvas DSC obtenidas revelan que el material base de las muestras es el PVC, ya que tienen en común la temperatura de transición vítrea (Tg) muy cercana a los 70°C, y la temperatura de degradación térmica (Td) cercana a 220°C.
Las muestras 1, 2 y 4 presentan un comportamiento muy similar. Se observan características de un material amorfo, ya que en las curvas no se aprecia un pico que indique que el polímero se fundió en algún momento. Se debe tener en cuenta que solo los polímeros cristalinos y semicristalinos pasan por un proceso de fusión antes de llegar a la degradación.
La curva de la muestra 3 presenta dos picos, de estos el que se encuentra alrededor de 120°C, indica que el material pasó brevemente al estado líquido (inicio de fusión), dicho comportamiento significa que en la muestra 3, la porción semicristalina del material es mayor que en las otras muestras, pues el PVC es un polímero principalmente amorfo que no suele superar el 20% de cristalinidad (Balart, 2011).
4. CONCLUSIONES
La metodología desarrollada entregó excelentes resultados para la recuperación de aluminio de los blísteres tipo Push Through Blister. La obtención del aluminio resultó más factible para estos blísteres que al presentar menor porción semicristalina en la composición del polímero, no se fundieron frente a los incrementos de temperatura. Por otra parte, con los otros dos tipos de blísteres mostrados en la Figura 3, no se pudo obtener resultados que justifiquen la aplicación de esta metodología debido a que las muestras se fundían o se requería realizarse un reproceso una y otra vez volviendo más lenta la recuperación de aluminio.
El rendimiento obtenido del proceso seguido para la separación de la lámina de aluminio del PVC resultó ser relativamente alto, ya que en promedio tiene un valor de 66%, lo que pudo llegar a ser aún mayor, además en las muestras que menor rendimiento se obtuvo, no fue inferior al 50%.
El aluminio que se recuperó en base al análisis químico realizado pertenece a la serie 1XX.X (Al > 99,0%), la dureza obtenida está dentro de lo esperado para este material, al presentar una dureza similar a la dureza del papel de aluminio de uso doméstico.
Se demuestra la importancia de la acción mecánica de compactación previa del aluminio recuperado para que el rendimiento de la fundición sea elevado (90%), mientras que sin la compactación y debido al bajo espesor de las láminas de aluminio más las resinas poliméricas presentes en ellas, el material en su mayoría se oxida volviéndose una especie de escoria.