I. INTRODUCCIÓN
La fluidización es un proceso por el cual una corriente ascendente de fluido (líquido, gas o ambos) se utiliza para suspender partículas sólidas con una turbulencia determinada. Dentro de este fenómeno físico, se enfatiza que en la fluidización de sólidos empleando un gas, se observa que las partículas se fluidizan cuando un gas que fluye hacia arriba presenta una fuerza de arrastre lo suficientemente alta como para superar la fuerza de gravedad descendente. La fuerza de arrastre es una clase de fuerza de fricción y presión impuesta por el gas sobre la partícula; la partícula presenta una fuerza de arrastre igual y opuesta sobre el gas. Este efecto es mínimo para las partículas esféricas, pero la influencia de la fuerza de arrastre es más significativa para las partículas de forma irregular 1. Además, se puede vislumbrar que entre las fases sólida y fluido (gas) aumentan considerablemente las tasas de transferencia de cantidad de movimiento, calor y masa, así es que se puede corroborar que los procesos de mezclado por este método son casi instantáneos. Por lo tanto, un lecho fluidizado nos permite conseguir altas tasas de transferencia al procesar un material y así obtener un producto terminado con mejores características, bajo consumo energético, escalabilidad y menor tiempo de proceso.
La fluidización tiene amplias aplicaciones industriales, siendo el caso más conocido en la industria de refinación de petróleo; en el proceso de craqueo catalítico 2. En las últimas décadas la fluidización se está aplicando en otras industrias, tal es el caso de la industria farmacéutica que aplica estas tecnologías de granulación de lecho fluidizado 3.
Los granuladores de lecho fluidizado utilizados en la industria farmacéutica son equipos constituidos principalmente de un procesador FBG (Fluidized Bed Granulator) equipado con una unidad de manejo de aire, una o dos boquillas atomizadoras de fluido, platos de distribución de aire y una bomba peristáltica. Permitiendo realizar un proceso de granulación de polvos y excipientes que se fijan en un aglomerado por el efecto de la fluidización con un gas calentado y que se unen mediante gotas de substancias ligantes originadas en la boquilla de atomización de dos fluidos 4, mejorando las propiedades mecánicas y de transporte de masa (difusión) del principio activo; ya que las partículas fabricadas prometen presentar buena fluidez, compresibilidad y hacen que el espesor de recubrimiento de los gránulos sea más homogéneo, acortando substancialmente los tiempos de producción 5.
Por ende, se recalca la gran importancia de tener un buen diseño de la cámara de fluidización, enfatizando en esta investigación que uno de los componentes más importantes es el plato de distribución de aire con el objetivo de contribuir al mejoramiento del desempeño del granulador farmacéutico de lecho fluidizado. Para su versatilidad se ha adaptado diferentes diseños de platos de distribución de aire, evaluándolos mediante los perfiles de flujo generados.
La viabilidad del uso de los diseños de platos de fluidización propuestos y desarrollados en esta investigación tienen un análisis enfocado principalmente en los patrones de flujo de aire obtenidos con cada diseño alternativo de plato de distribución de aire, aplicando diferentes tipos de partículas en base al criterio de clasificación de polvos de Geldart, como también otros factores como son velocidad de aire, temperatura y presión de operación que se manejan dentro de la cámara de fluidización 6. Si bien, el propósito principal de un plato de distribución de aire es proporcionar una distribución uniforme del gas en el lecho fluidizado, un buen funcionamiento implica también una menor caída de presión posible con el objetivo de minimizar el consumo de energía, en el diseño también se debe tener en cuenta el desgaste de las partículas, la erosión del recipiente y los componentes internos y las limitaciones mecánicas; expansión térmica, hundimiento del lecho durante paradas de emergencia, entre otras 7.
PROCESO DE GRANULACIÓN
Un granulador de lecho fluidizado consta de una cámara de fluidización donde se realiza una determinada operación. A la cámara se le alimenta aire que ha sido previamente acondicionado en lo que se refiere a temperatura, humedad, contenido de impurezas y calidad del aire 8. Este módulo de acondicionamiento de aire se le llama AHU por sus siglas en ingles Air Handling Unit. Adicionalmente, en este módulo se incluyen para
la eliminación de bacterias y otros patógenos en aire, filtros HEPA (High Efficiency Particulate Arrestance 9.
A la cámara de fluidización se alimenta una solución ligante para provocar que las partículas en movimiento se peguen entre sí y formen el granulado, para la dosificación del ligante se usa una bomba peristáltica 10. En la parte superior interna de la cámara de fluidización se encuentran un juego de filtros de mangas que impide que salgan los polvos finos farmacéuticos al ambiente; así como también, en la salida de la cámara de fluidización existe otro sistema de filtración adicional. Esto se debe a motivos de seguridad ya que los polvos finos farmacéuticos tienen una alta probabilidad de producir problemas de salud, daños ambientales y biológicos, razón por la cual, deben ser retenidos utilizando este tipo de sistema de filtros 11.
La Figura 1 muestra un diagrama de proceso típico donde se observan todos los componentes de un granulador farmacéutico. El soplador insufla aire sobre la cámara de fluidización, lo cual hace que trabaje a presión positiva. Sin embargo, la industria farmacéutica prefiere a presión negativa debido a que nunca se debe descargar los principios activos y excipientes al cuarto de operación donde se ubica el granulador y de este modo se minimiza el riesgo químico que presenta el material particulado al ser inhalado por los operarios.
1.2 TIPOS DE PLATOS DE DISTRIBUCIÓN DE AIRE
Existen varios tipos de platos que se han desarrollado en la industria de procesos entre los que tenemos: el axial perforado, por borboteo (Wurster), el inclinado y torbellino o rotacional con diferentes diseños (12). Cada uno de estos tipos de plato, define un patrón de flujo característico y son medianamente efectivos de acuerdo con el tipo de operación y material a fluidizar. Actualmente los fabricantes están desarrollando platos universales; es decir, que muestran buen funcionamiento en las diferentes operaciones.
El plato axial perforado fue el diseño original cuando se desarrollaron los primeros lechos fluidizados. En este plato, el aire pasa a través de el en forma transversal. La configuración de las perforaciones puede ser triangular o rectangular y raramente se puede ver en forma circular como se muestra en la Figura 2 (a).
El plato de distribución por borboteo (Wurster) se utiliza principalmente para recubrimiento del granulo. Presenta un patrón de flujo característico como se puede ver en la Figura 2 (b). Dentro de la cámara de fluidización se coloca un tubo de borboteo, donde también se localiza la boquilla de recubrimiento por el fondo de la cámara. Este tubo permite tener dos regiones donde se puede variar el diferencial de presión entre el interior y exterior del tubo de borboteo. Debido a este diferencial se tiene un transporte de masa cíclico. Las perforaciones en el plato de distribución son circulares con orificios de diferentes tamaños para tener diferentes gradientes de velocidad y un diferencial de presión que permita el patrón de flujo deseado.
En los platos radiales con inclinación, al cambiar el ángulo que se suministra el aire a la cámara también cambia el patrón de flujo. La alimentación axial tiene el inconveniente que consume más potencia comparando con los otros tipos de platos de nueva generación, además, es difícil de controlar. Al fijar un ángulo diferente a 90 grados, por ejemplo, como se muestra en la Figura 2 (c), el ángulo es de 45 grados respecto a un eje horizontal radial. Esta configuración presenta un patrón similar al de borboteo (Wurster) 13, entonces los platos de distribución de gas se desarrollaron con modificación del ángulo de soplado de aire, mejorando así la tasa de recirculación.
Existen una gran variedad de configuraciones de platos tipo torbellino como se muestra en la Figura 2 (d). El plato tipo torbellino o toroidal, tiene la característica de crear movimientos giratorios en el lecho, es decir un efecto rotacional sobre las líneas de corriente de aire que se inyectan ya sea por el ingreso por múltiples entradas tangenciales en la parte inferior del lecho creando remolinos de aire o utilizando distribuidores de aire tipo paletas anulares creando fluidización juntamente con remolinos (14. De esta manera, se asegura que las partículas que se encuentren en la cámara tengan un mayor tiempo de residencia 15.
1.3 CONFIGURACIÓN GEOMÉTRICA PARA EL DISEÑO DE PLATOS DE DISTRIBUCIÓN
El diseño de los platos de distribución de gas, está en función de su configuración geométrica, desde el número de orificios, distribución de orificios y diámetro de los orificios que contenga un plato, enfocado en el balance adecuado de estos parámetros para generar un flujo uniforme, constante y eficiente del gas para mantener en fluidización a las partículas en la cámara, minimizando las caídas de presión y evitando la destrucción de las partículas especialmente las más delicadas en concordancia con la clasificación de partículas de Geldart 16. Si la caída de presión en la cámara es demasiado baja, la aerodinámica del lecho determinará el flujo de gas y el gas se distribuirá mal. Esto se debe a que el movimiento de los sólidos y el gas en un lecho fluidizado se compone de remolinos y torbellinos caóticos, y tal movimiento podría crear un camino de menor resistencia para el gas o fluido entrante 17.
El diseño de estos dispositivos se desarrolló considerando los siguientes parámetros:
1.4 TIPOS DE CÁMARAS DE FLUIDIZACIÓN
La configuración geométrica de la cámara como también la ubicación de la boquilla de atomización juegan un papel importante en el rendimiento de las operaciones del procesador de lecho fluidizado como: mezclado, secado, granulación y recubrimiento 19. A más del tipo de plato en análisis se debe considerar la ubicación de la boquilla de atomización para las operaciones de granulación y recubrimiento 20. La Tabla 1 resume los tipos de configuración de cámaras de fluidización.
1.5 CARACTERIZACIÓN DE LA PARTÍCULA
En la naturaleza, las partículas rara vez se presentan homogéneas en su tamaño, forma, densidad y morfología, por lo tanto, es necesario trabajar con valores representativos para garantizar la veracidad de los valores experimentales. Consecuentemente las partículas que son utilizadas en estudios de fenómenos de fluidización es recomendable caracterizar parámetros tales como esfericidad y diámetro de partícula 21 .
La esfericidad (ϕ) de una partícula, es la medida geométrica más útil que nos permite caracterizar la forma de las partículas, determinando cuanto difiere o se aproxima dicha partícula a la forma esférica y se define como la relación entre superficie de la esfera y superficie de la partícula para el mismo volumen ocupado, como se expresa en la Ecuación 1.
Donde:
Si el valor de la esfericidad es más cercano a 1, entonces la partícula tiende a tener forma esférica, y aquellas que se alejan más de 1 tienden a tener formas más irregulares.
El diámetro o tamaño de partícula es el tamaño representativo o equivalente que se le puede definir a una partícula de una forma determinada y está relacionada con la esfericidad de la misma. Dependiendo del tamaño de la partícula hay varias maneras de definir este parámetro 22.
1.6 PATRONES DE FLUJO
El estudio de un flujo bifásico de sólidos en gases, se caracteriza por el flujo de gases con sólidos en suspensión. Este tipo de flujo es fundamental para muchos procesos industriales como el transporte neumático, el control de la contaminación por partículas, la combustión de carbón pulverizado, el secado de productos alimenticios, el granallado, el recubrimiento por arco de plasma y el mezclado en lecho fluidizado 23. Cabe mencionar que estos tipos de sistemas gas-sólido presentan dos tipos de flujos generales que son los flujo diluidos y densos. Un flujo diluido es un flujo de partículas de gas en el que el movimiento de las partículas está controlado por las fuerzas de arrastre y elevación de la partícula. En un flujo denso, el movimiento de las partículas está controlado principalmente por colisiones entre partículas.
Otra característica importante de los flujos de gas-sólido, es la interacción entre fases. Si el gas afecta al movimiento y a la temperatura de las partículas, pero las partículas no cambian la velocidad del gas o los campos de flujo térmico, entonces el flujo es unidireccional. Por otro lado, si hay una interacción mutua entre las fases, el flujo se acopla en dos sentidos 24.
La Figura 3 muestra los diferentes tipos de flujo que se pueden formar, esto depende tanto de la geometría de la cámara, del diseño del plato, del comportamiento del material particulado a procesar así como también, de las condiciones de proceso. Cuando el caudal es mínimo, apenas se puede ver que las partículas comienzan a fluidizar; por otro lado, una cama burbujeante se produce debido a la presencia de partículas grandes como son los granos. Sin embargo, este tipo de comportamiento de los polvos se ve principalmente en platos perforados (axiales), claro que tambien dependen de la naturaleza del polvo.
II. MATERIALES Y MÉTODOS
Para la producción de diseños alternativos de platos de distribución de aire propuestos se utilizó un software de diseño 3D, fijando las dimensiones y parámetros geométricos, para posteriormente imprimir el prototipo con la ayuda de una impresora 3D en base de un material polimérico; ácido poli láctico (PLA). Para la evaluación de los patrones de flujo se establecieron condiciones operacionales equivalentes, con el uso de una cámara de fluidización que también fue diseñada y construida como se puede ver en la Figura 4.
La cámara de fluidización se diseñó para acoplar los platos de distribución de aire de diferentes diseños; los cuales presentan dimensiones y
geometrías específicas y totalmente definidas, y estas a ser constantes durante toda la experimentación, como son: el ángulo de entrada del cono del tazón de producto, el diámetro interno del lecho, la altura definida de la cámara y la altura del lecho estático. Así como los parámetros de operación que se manejaron y controlaron como: velocidad de fluidización, humedad relativa del aire de entrada al lecho fluidizado el cual fue un parametro constante. Obteniendo como resultado principal los diferentes tipos de patrones de flujo producidos con cada tipo de plato de distribución de gas en el sistema bifásico de aire en contacto con partículas sólidas en corriente paralela. Para observar las líneas de corriente y de forma global el patrón de flujo que describe cada plato se utilizó como una herramienta de ingeniería similar en escencia al tunel de viento. En este caso, en vez de usar humo, se usó partículas de poliestireno de diferentes colores, para facilidad en la observación y descripción del fenómeno, hacia la determinación de los patroles de flujo y con ello caracterizar cada plato diseñado.
2.1 DISEÑOS ALTERNATIVOS DE LOS PLATOS DE DISTRIBUCIÓN DE AIRE
Para definir los parámetros geométricos de cada plato se basó en patentes americanas e información técnica de fabricantes de este tipo de equipos de procesos 25.
Para los diseños alternativos de los platos de distribución de aire que se realizaron en función del flujograma indicado en la Figura 5, se determinó y caracterizó el tipo de partículas a ser estudiadas. Siguiendo con la especificación de dimensiones y definición de parámetros geométricos, considerando los siguientes como preponderantes: ángulo, número de ranuras, geometría de la ranura.
2.2 DISEÑOS ALTERNATIVOS DE LOS PLATOS DE DISTRIBUCIÓN DE AIRE
Para evaluar el desempeño de un nuevo diseño de plato se debe analizar el consumo energético expresado como caída de presión, el tipo de particula y la velocidad de flujo, como variables significativas para el estudio.
La velocidad mínima de fluidización calculada mediante la ecuación de Ergun resulto 0,84 m/s, la misma que se aplicó a la experimentación, con cuyos resultados se muestran en la Tabla 2.
En la Figura 4 se muestra el uso del cono, el cual es para evitar segregación del material, el cono es un tipo de difusor, bastante conocido en la industria aeronáutica para el diseño de turbinas de avión.
Debido a que las partículas de ajonjolí son de gran tamaño y revisando la clasificación de Geldart es de tipo D, las cuales son de fácil borboteo.
2.3 IMPRESIÓN 3D Y PROTOTIPAJE
El desarrollo de un prototipo como el que se propone en esta investigación, puede ser un proceso lento y costoso, pero afortunadamente existen algunas técnicas que permiten hacer prototipos de alta calidad a un costo menor. Esta técnica ofrece el uso de la impresión 3D, lo que permite generar partes físicas de geometría compleja de diferentes características y dimensiones a partir de un modelo digital 3D, utilizando un software de modelado 3D, permitiendo de esta manera acceder al uso de una amplia gama de materiales para impresión 3D, resultando procesos rápidos, de bajo costo y más eficientes. El material que esta dominando el mercado es el PLA. Este polímero es de origen natural, y sus residuos no causan problemas de salud cuando son incinerados.
2.4 PARÁMETROS EN GRANULADORES DE LECHO FLUIDIZADO
Como se dijo anteriormente el plato de distribución de aire es un elemento importante en el desempeño de un granulador de lecho fluidizado en relación con los siguientes parámetros de equipo, formulación y proceso. Por tal razón en este estudio se los verifica detalladamente en función a lo que se describe a continuación:
• Los parámetros de equipo corresponden principalmente a la geometría de sus elementos o su configuración que incluyen: plato de distribución de aire, tipo de boquilla de atomización y configuración y la unidad de manejo de aire (AHU).
• Los parámetros de formulación corresponden principalmente a las características o naturaleza de la materia a tratar: partícula, polvo, ligante y su solución.
• Los parámetros de procesos corresponden a las propiedades termodinámicas, de transporte que se tiene que definir o controlar como son: comportamiento hidrodinámico, dispersión y tamaño de gota del ligante, contenido de humedad del hecho, altura del lecho y presencia de finos.
2.5 EXPERIMENTACIÓN
Para determinar el patrón de flujo que genera cada diseño de plato de distribución de aire propuesto se utilizaron dos tipos de partículas según la clasificación de Geldart que fueron respectivamente caracterizadas, como se nombran en la Tabla 3, juntamente con las condiciones experimentales siendo constantes en tiempo de análisis de 10 a 15 minutos. Se denota que en la cámara de fluidización no se ensambló con boquilla de atomización, sino que se reemplazó un cono central.
2.5.1 Diseño de Experimentos
Las variables a considerar en el diseño de experimentos son: caudal de aire (factor cuantitativo), temperatura de entrada de aire (parámetro), plato usado (factor cualitativo nominal, 3 valores), patrón de flujo (respuesta cualitativa ordinal): (insuficiente, pobre, bueno, excelente), tipo de lecho fluidizado (según Figura 3), material a fluidizar (2 tipos), carga inicial, las demás variables de formulación y equipo se mantienen constantes (parámetros) y variables aleatorias no controladas (Ej. humedad ambiental). Las condiciones experimentales se encuentran contenidas en la Tabla 3.
2.5.2 Platos Diseñados
Las variables a considerar en el diseño de experimentos son: caudal de aire (factor cuantitativo), temperatura de entrada de aire (parámetro), plato usado (factor cualitativo nominal, 3 valores), patrón de flujo (respuesta cualitativa ordinal): (insuficiente, pobre, bueno, excelente), tipo de lecho fluidizado (según Figura 3), material a fluidizar (2 tipos), carga inicial, las demás variables de formulación y equipo se mantienen constantes (parámetros) y variables aleatorias no controladas (Ej. humedad ambiental). Las condiciones experimentales se encuentran contenidas en la Tabla 3.
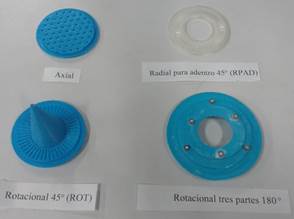
Figura 6 Platos diseñados: plato axial, radial para adentro 450 (RPAD) sin cono central, rotacional 450(ROT) con cono central) y rotacional en 3 niveles.
Los platos diseñados presentan las siguientes dimensiones de ranura según se indica en la Tabla 4, siendo dimensiones flexibles a escalamiento dependiendo del diámetro interno de la cámara de fluidización ya sea proyectando al aumento o disminución de su escala.
2.5.3 Caracterización de la materia prima
Para la caracterización de los tres tipos de partículas (semillas de ajonjolí, bolas de colores de poliestireno y arena) utilizadas en la experimentación, se determinaron las condiciones ambientales promedio (542 mmHg y 18 ºC)
Para las semillas de ajonjolí se caracterizaron aproximándolas a la forma de ovoide, bolas de poliestireno como esféricas y arena de forma elipsoide, determinando para cada una de las partículas el tamaño, esfericidad, diámetro de partícula equivalente, densidad real y densidad aparente, como se observa en la Tabla 5.
2.5.4 Evaluación del Rendimiento de los Platos
Se evaluó el rendimiento de los platos diseñados a través de la medición de la caída de presión utilizando un manómetro diferencial variando el caudal del flujo de aire obteniéndose la Figura 7. Cuyas caídas de presión fueron corroboradas mediante la aplicación de la ecuación de Ergun.
III. RESULTADOS
Al comparar la operación de fluidización en el granulador de lecho fluidizado bajo condiciones de operación específicas como se indica en la Tabla 3, los diferentes tipos de platos de fluidización de gas diseñados conjuntamente con los tres tipos de partículas propuestas, se determinó que en los patrones de flujo generados no existen cambios significativos, pues al utilizar semillas de ajonjolí, bolas de poliestireno y arena, los patrones observados fueron semejantes, pero con la particularidad que los patrones de flujo aunque fueron los mismos estos se producen a diferentes alturas dentro de la cámara de fluidización.
La mejora del diseño de los platos se presenta en el análisis de variación en el vector del flujo de aire al observar mejores propiedades de transporte en el procesamiento de los gránulos, evidenciada por la altura alcanzada por el lecho. En base al concepto de equilibrio de fuerzas reflejada indirectamente mediante la valoración de densidades de las partículas, pues a bajas densidades la altura de formación de los patrones de flujo resulto ser más alta, es decir la altura de formación del patrón de flujo es inversamente proporcional a la densidad de la partícula estudiada.
Esto se debe que se genera un mayor arrastre de las partículas hacia la parte superior de la cámara de fluidización al existir una rotación sobre las partículas haciendo que se produzca un desplazamiento de las partículas, sobresaliendo las partículas de poliestireno, seguidas de las semillas de ajonjolí y finalmente la arena, siempre evitando que exista un transporte neumático, como se observa en la Figura 8.
Experimentalmente y mediante observación se determinó que el patrón de flujo es similar en cada material independientemente de las características individualizadas de las partículas, resultando una ventaja para el procesamiento y escalamiento del proceso, dependiente únicamente del tipo de plato 13.
El patrón de comparación establecido para el análisis fue el generado por el plato axial ya que este resulta en un diseño estándar y base para el desarrollo de los demás diseños. Sin embargo, conforme se ha desarrollado la tecnología han aparecido platos mucho más eficientes. Los platos RPA y ROT muestran las siguientes diferencias comparados con el plato patrón, como se detalla en la Tabla 6.
En el análisis de los patrones de flujo producidos por los diferentes diseños de platos fabricados, sobre las diversas partículas sólidas destaca lo siguiente:
• El patrón de flujo de lecho burbujeante, caracterizado por la presencia de burbujeo, se desarrolló al utilizar el plato de tipo axial, cuando se manejó las partículas de semillas de ajonjolí y arena observándose un flujo de sólidos con presencia de gas que forman burbujas de tamaño pequeño pero inestables.
• El patrón de flujo de lecho en ebullición con una forma de tipo volteo, caracterizado por representar un movimiento de las partículas que se asemeja a un movimiento dentro de un tambor giratorio con una capa superficial irregular y con un ángulo de inclinación de 30º al formar una turbulencia homogénea.
• El patrón de flujo a manera de lecho de borboteo y en forma de torbellino, se caracterizó por manejar flujos más homogéneos con alta estabilidad, pues se observó que las burbujas formadas por el gas ayudan al control y movimiento de las diferentes partículas a lo largo de toda la cámara de fluidización evitando la aglomeración entre ellas.
• El patrón de flujo del tipo lecho burbujeante y acanalado tendió a producir elutriación (choque de partículas y rompimiento), únicamente cuando se utilizó las partículas con baja densidad como son las bolas de poliestireno, pues se obtuvo un movimiento heterogéneo, presentando alta separación entre ellas hasta alcanzar un perfil inicial para el desarrollo del transporte neumático de partículas.
Los resultados obtenidos se resumen en la Tabla 6, producto de haber realizado un análisis cualitativo basado en la observación focalizada de video-grabaciones que fueron reproducidas y analizadas en detalle que permitió el correcto análisis sector por sector de la cámara de fluidización, proporcionando mejor información del movimiento de las partículas; semillas de ajonjolí, bolas de poliestireno y arena como se puede ver en la Figura 6. Los experimentos se realizaron por duplicado y triplicado para su verificación. El escoger diferentes partículas con diferente tamaño nos permite entender la mecánica que produce el aire sobre las partículas. Se verificó los patrones de flujo al comparar con la información bibliográfica de platos comerciales.
IV. DISCUSIÓN
La industria ha desarrollado nuevos diseños de platos, los cuales han sido declarados en patente 25. Por otro lado, las investigaciones realizadas hasta la fecha se enfocan principalmente en el estudio del fenómeno sin considerar parámetros mecánicos o geométricos, por lo cual en este estudio se enfocó en el desarrollo y diseño de platos de distribución de aire, para evaluar el tipo de plato hacia el desarrollo de los patrones de flujo que indirectamente dan a conocer el fenómeno de transporte de masa y energía, dependientemente en las operaciones que se enfoque como por ejemplo mezcla, secado, entre otras.
En este estudio se utilizó un lecho fluidizado estándar, donde se logró acoplar los tipos de platos diseñados y construidos, con la finalidad de fijar una versatilidad en la operación para evaluar los patrones de flujo, manteniendo contantes las dimensiones del equipo variando únicamente el tipo de plato de distribución de aire y consecuentemente evaluar la calidad de flujo según cada plato empleado.
En la presente investigación los patrones de flujo resultantes se verificaron mediante determinación visual cualitativa en sentido al movimiento del fluido en cuestión, pero para la comprobación y validación del método visual cualitativo, es indispensable realizar un análisis más exhaustivo mediante el empleo de mejores tecnologías e instrumentación como por ejemplo la aplicación de velocimetría por imagen, cuya tecnología permitiría validar al 100 % los patrones de flujo y consecuentemente la calidad de los platos de distribución, cuyas tecnologías son aplicables principalmente cuando se pretenden sistemas de fluidización con equipos a gran escala.
Consecuentemente, el presente estudio de los platos de distribución se considera totalmente valido pues el análisis se realizó a pequeña escala o escala de laboratorio con factores dimensionales estandarizados y con criterios de diseño fijos y justificados como se indica en el apartado de metodología y experimentación.
El análisis para el mejoramiento en el rendimiento de un plato de distribución está sujeto a una función multivariable, considerándose un proceso complejo, el mismo que debe analizarse en cada etapa de aplicación, desde la etapa de investigación en laboratorio hasta las diferentes etapas de escalado. Considerando una de las variables principales para dicho análisis la caída de presión como punto de partida para el estudio de más variables objetivas como la velocidad mínima de fluidización las mismas que permitan definir adecuadamente los diferentes platos de distribución al momento de ser aplicados en equipos de fluidización a pequeña, mediana y gran escala. Notando que los datos entregados en esta investigación resultan reproducibles y aplicables principalmente a pequeña escala.
A pesar de que en el presente estudio no se realizó un referente de escalamiento, se tiene el material inicial necesario para la proyección de comportamientos de patrones de flujo a mayor escala o escala productiva, logrando con ello posteriormente identificar la influencia de los patrones de flujo de distribución con en la calidad del producto, además de la relación de energía consumida en un proceso. Por lo cual, posteriormente se ha planificado la construcción de los platos de distribución en acero inoxidable para ser aplicado en granuladores de lecho fluidizado sofisticados, como aquellos que se utilizan en la industria farmacéutica, realizando análisis mediante el software de simulación de dinámica de fluidos o por sus siglas en inglés (CFD).
V. CONCLUSIONES
El software de modelamiento 3D (AutoCAD) utilizado, permitió diseñar los diferentes prototipos de platos de distribución de aire propuestos para el análisis de patrones de flujo a ser utilizados en granuladores de lecho fluidizado para la industria farmacéutica, los mismos que posteriormente y con la ayuda de una impresora 3D en base de un material polimérico, se lograron obtener de manera física, resultando una buena alternativa para la evaluación dado que acortó el tiempo de fabricación de los platos, obteniéndose prototipos más exactos, principalmente en sus dimensiones y geometría, además de tener costos de producción menores al comparar con métodos de fabricación convencionales.
Para la evaluación y correcto análisis de los patrones de flujo, se manejaron condiciones operacionales equivalentes como se presentan en la Tabla 3, para alcanzar este cometido adicionalmente se diseñó una cámara de fluidización que garantizó la replicabilidad de los experimentos y disminuyó los errores de operación al tener un error máximo del 3,2 % concebido principalmente por el control de velocidad de flujo de gas y temperatura.
Al observar y analizar la incidencia del funcionamiento de los platos de distribución de aire diseñados, en la generación de los patrones de flujo y la relación con partículas de diferente tamaño, forma y comportamiento según la clasificación de polvos Geldart, los platos que mostraron mejores características en las diferentes operaciones presentaron un efecto combinado de tipo axial, radial y rotacional, encontrándose el patrón de flujo mejorado en los platos que causan un efecto rotacional sobre las partículas a procesar, concordando con la tecnología de punta que se aplican en equipos comerciales.
Los prototipos de platos diseñados y utilizados en esta investigación, aunque fueron fabricados en base de PLA, ofrecieron resultados prometedores a ser aplicables en granuladores de fluidización, pues presentaron gran versatilidad al manejo de diferentes tipos de partículas en un rango de densidades como se describen en la Tabla 6, al no presentar grandes cambios al tipo de patrón de flujo generado.
El uso de PLA como material para la fabricación de los platos de distribución de flujo de aire presentó gran facilidad para obtener diseños precisos, pues se notó que las ranuras que exigían los modelos propuestos en este estudio fueron exactamente construidas a pesar de ser menores a 1 mm y tener ángulos menores a 90º, a diferencia si se hubiese utilizado acero inoxidable 316 que exige el uso de técnica y tecnologías más costosas y con tiempo de producción más largos. A pesar de que el acero inoxidable 316 es el material de fabricación definitivo de un granulador farmacéutico, los platos fabricados en PLA son aceptables pues cumplieron con el objetivo de esta investigación.
Con respecto a los tipos de platos de distribución de flujo, se observó que dependiendo del diseño se puede tener diferentes expansiones en la cámara de fluidización, pues al evaluar con las mismas condiciones de operación y con un tipo de partícula, se generan diferentes alturas de fluidización en el interior de la cámara. Así, se determinó que al utilizar el plato rotacional se logró controlar fácilmente la expansión del lecho, en comparación con el plato axial que se observaba la tendencia de llegar a generar el fenómeno de transporte neumático de las partículas, específicamente en aquellas que presentan densidades más bajas como el caso de las bolas de poliestireno.