INTRODUCCIÓN
A partir de la aparición de las primeras resinas termoestables, surgieron las resinas fenólicas, conocidas como los primeros polímeros sintéticos producidos a nivel industrial. [1] Sus aplicaciones supusieron un boom en la industria debido a sus propiedades adhesivas que las hacen altamente resistentes a los disolventes orgánicos, así como a su resistencia al calor y estabilidad dimensional, características que las posicionan como las mejores resinas del mercado actual.[2].
Las resinas fenólicas forman parte de la gran familia de polímeros, los oligómeros, que se obtienen por reacciones de fenoles con aldehídos. Este tipo de producto tiene una clasificación como “Novolac” y “Resol”, donde se utilizan catalizadores ácidos y básicos para obtener un producto de tipo líquido con alta viscosidad.[3] Dentro de la clasificación antes mencionada, el producto que se implementa en este proceso de elaboración de espumas son las resinas tipo Resol que se obtienen en condiciones básicas, con un exceso de formaldehído [4]. Son resinas oligoméricas termorreactivas que pueden ser catalizadas por condiciones ácidas, básicas o ésteres especiales. Estos tipos de resinas se utilizan sobre todo para compuestos reforzados con fibras [4, 5].
La resina fenólica tiene una amplia gama de aplicaciones en constante expansión, y según Grand View Research en 2018, el mercado global de estas resinas tuvo un valor de 11.17 billones de dólares y se proyecta un crecimiento anual del 5.3 % entre 2019 y 2025. En la actualidad, los principales productores a nivel mundial son Estados Unidos, Alemania, China y Corea del Sur. Dentro de algunas mejoras se busca el reemplazo de tecnologías basadas en derivados de crudo de petróleo por lo que se han iniciado estudios basados en biomasa para obtener la misma resina fenólica enfocándose en la economía circular [6].
Las resinas fenólicas se caracterizan principalmente por su bajo costo de producción, debido a sus materias primas que son de fácil disponibilidad, convirtiéndose en una elección atractiva para las diferentes aplicaciones industriales (ver Fig. 1). Su proceso de síntesis es fácil y rentable, en conjunto con la accesibilidad que contribuye a la amplia comercialización en una variedad de sectores desde la producción de materiales compuestos hasta la fabricación de productos laminados, finalmente los costos de producción son los más competitivos en el mercado.
Los resoles, una variante de las resinas fenólicas, se originan al combinar fenol y un exceso de formaldehído en presencia de un catalizador alcalino, como hidróxido de sodio o amoníaco. La proporción típica de fenol a formaldehído oscila entre 1:1 y 1:1.3 en esta síntesis.[7] Los resoles son resinas con una moderada ramificación y un peso molecular relativamente bajo, lo que los hace solubles en agua. Tienen una vida útil limitada, generalmente de varios meses, y se consideran resinas fenólicas de “una etapa“ y que no requieren agentes de curado adicionales. El proceso de curado se realiza mediante polimerización térmica a temperaturas que oscilan entre 130-200 °C, liberando agua como subproducto [8].
Las resinas novolac pertenecen a una variedad de resinas fenólicas que por lo general resulta de una reacción con poco formaldehído donde la proporción es mínima en el rango 0.75-0.85 moles por cada mol de fenol. Dicho producto cuenta con propiedades termoplásticas en su estado inicial donde se debe adicionar un endurecedor como HMTA (Hexametilentetramina), para que los derivados resultantes sean resistentes al calor, además de ser insolubles e infusibles. Su aplicación más importante es en la industria forestal.[9]
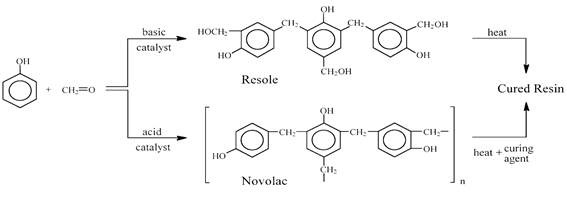
Fig. 1. Obtención de resinas Resol - Novolac. Fuente: Thermosets: Phenolics, Novolacs, and Benzoxazine. [10].
Los materiales termoestables suelen ser quebradizos, lo que dificulta la realización de pruebas mecánicas convencionales como las de resistencia, flexión o tracción. Un ejemplo de termoestable, el fenólico, muestra valores bajos de resistencia al impacto, alrededor de 12 J m-1. Otros termoestables basados en resinas como las de lignina-formaldehído, lignina-fenol- y tanino-fenol-formaldehído también exhiben fragilidad similar a la del fenólico. Sin embargo, cuando se refuerzan con fibras naturales o sintéticas, los termoestables fenólicos experimentan mejoras en su resistencia al impacto, y la magnitud de esta mejora depende del tipo de fibra utilizada. [11, 12].
Entre los procesos de obtención de resinas se encuentra la reacción de condensación entre un fenol y el formaldehído, produciendo agua residual. Aunque estos reactivos empleados, a futuro podrían tener escases debido a la disminución y alto consumo del crudo de petróleo en los últimos tiempos, a esto se puede generar alternativas sostenibles como el uso de lignina o policarbonato reciclado como sustituyente parcial del fenol. El producto final es una espuma floral que tras pasar por la fase de espumación sirve como soporte de flores, además de tener la propiedad de absorber agua y actuar como medio de crecimiento para la propagación de parterres de plantas, ya que tiene un pH adecuado libre de bacterias y hongos.[13] Así, se pretende realizar un estudio técnico para analizar la sustentabilidad considerando un estudio previo del proceso de producción de la resina, basado en procesos que ya han sido implementados en otros lugares.
En el proceso de polimerización de resinas fenol-formaldehído, se emplea un reactor de tipo ”bulk” (Fig. 2). Este reactor está equipado con un revestimiento de vapor que mantiene la temperatura necesaria para que ocurra la reacción entre el fenol y la formalina, generando la polimerización deseada. Además, se incorpora un condensador que facilita la condensación y eliminación del vapor de agua que se forma como subproducto de la reacción entre el fenol y la formalina. La eliminación eficiente del agua del sistema contribuye a mejorar la reacción entre estas sustancias y fomenta la formación de mayores cantidades de resina fenol-formaldehído [14].
El proceso de producción se lleva a cabo en dos etapas. En la primera fase, se genera una resina fenol-formaldehído denominada “resol”. En la segunda fase, esta resina se combina con hexametilentetramina (HEXA) para formar un compuesto moldeable. La mezcla de la resina fenol-formaldehído con HEXA se somete a calentamiento en un molde, lo que resulta en la descomposición del HEXA y en la liberación del formaldehído necesario para lograr la etapa final de curado. Esta combinación de resinas se conoce como resinas “novolac” o resinas “de dos pasos” [15].
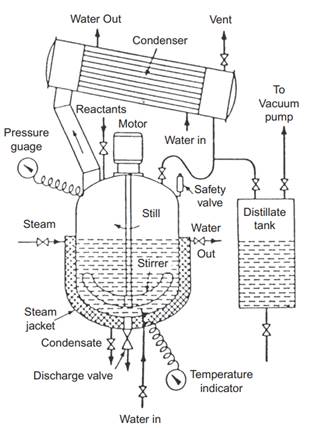
Fig. 2. Esquema de un reactor típico para la polimerización en masa de fenol-formaldehído-resinas. Fuente: Phenol-Formaldehydes. [16].
Las espumas florales se pueden elaborar en base a diferentes procesos a nivel laboratorio donde se implementan técnicas de mezclado a mano, por otro lado a nivel industrial se utilizan técnicas y maquinarias específicas, como se muestra en la Fig. 3 se tiene una máquina para procesar espumas fenólicas, donde se carga el componente A como es el resol, surfactante, agente de celda abierta y el colorante, por otro lado el componente B en este caso es el R-113, finalmente se agrega un catalizador ácido [1, 17].
Otra alternativa para la producción de resinas es la tecnología Laizhou Yuandan (Fig. 4), que se utiliza para obtener como producto final la espuma floral para flores frescas, de tipo automático con mezcla uniforme, entre la configuración que muestran este tipo de equipos tenemos un reactor, máquina de dispersión, máquina de corte, caja de espuma con capacidad de 300 - 4 800 cartones/día, 20 piezas, el tamaño es de 80*110*230 mm y con absorción de agua de 1,5 kg por ladrillo..
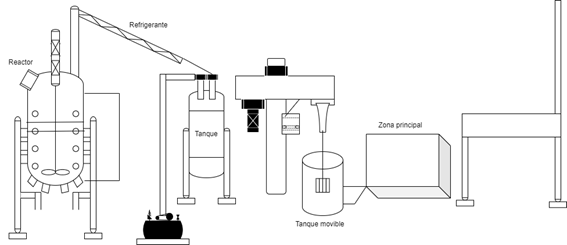
Fig. 4. Tecnología de producción adaptado de Laizhou Yuandan. Fuente: Laizhou Yuandan Chemical Industry Machinery Factory. [18].
Existen varias etapas para la producción de espuma floral, comenzando por la obtención de la resina fenólica, que es un proceso discontinuo en el que se requiere un reactor discontinuo y una torre de destilación, cuando no se dispone de estos equipos, se puede utilizar un reactor de neutralización para realizar la destilación. La segunda etapa es el espumado de la resina fenólica, que consiste en la inyección de resina fenólica con reactivos como surfactantes, humectantes, agentes espumantes, urea y colorante a través de una válvula de aguja sellada, se agrega un molde de espuma para darle la forma deseada al producto para su posterior corte y con el cual se puede reducir el tiempo de secado de la resina con su sistema de calor. Por último, tenemos el corte de la espuma, donde se utilizan dos máquinas, una vertical y otra horizontal para obtener el tamaño estándar requerido de la espuma, que es de aproximadamente 22,5x10,5x7,5 cm. [19].
En Ecuador, la demanda de este tipo de resinas para la producción de espumas fenólicas es muy amplia y no existen empresas que suministren este tipo de productos. Por lo que este proyecto busca el diseño de una planta de producción de resinas fenólicas (espuma floral), que permitan en primera instancia establecer los principales equipos para el proceso, así como las variables y materia prima necesaria para llevar a cabo la producción, utilizando el software de simulación PRO II, para obtener datos de cantidades de materias primas que permita satisfacer la demanda encontrada en el país. Con el fin de generar una iniciativa empresarial dentro del sector de la fabricación petroquímica.
MATERIALES Y MÉTODOS
Este estudio se basó en dos metodologías, la primera es la etapa de búsqueda y revisión de la demanda, características y especificaciones de la resina fenólica, la segunda etapa es la de diseño y modelamiento del proceso para lo cual se realizó la simulación y cálculos manuales para llevar a cabo el proceso.
Para estimar los balances de masa del proceso a ser diseñado, fue necesario determinar la demanda interna anual con información del periodo de 2015 a 2020, no se consideran los años donde se desarrolló la pandemia de COVID-19, en este periodo se estimó un valor promedio de 143.360,37 kilogramos.[20] En base a esta demanda se realiza la especificación del reactor para la producción de la resina fenólica, que dependen de los reactivos como fenol, formaldehido e hidróxido de sodio.
Materias primas
Se requiere de reactivos algunos de los cuales se pueden encontrar en la base de datos del simulador, otros un ingreso manual a través de grupos funcionales, que permiten la introducción de compuestos nuevos y estimando sus propiedades, logrando tenerlas y se mencionan en la Tabla 1.
Diseño del proceso
Reacción de policondensación
Para el proceso de obtención de espuma floral, es necesario conocer los reactivos que intervienen y la reacción necesaria. En la Fig. 5 se muestran los reactivos, se emplea principalmente fenol con formaldehido, en presencia de un catalizador básico (hidróxido de sodio), como productos esperados, son la resina fenólica (tipo resol). Para la obtención de resina fenólica, se preparó una solución de formaldehído al 37 % p/p y se mezcló con fenol de forma que se cumpliera la relación molar de P:F<1. Se alimentó un reactor discontinuo con la mezcla de fenol y formaldehído en presencia de un catalizador básico (hidróxido sódico) [22].
La cinética de la reacción de policondensación se calculó en base a estudios realizados, donde los experimentos fueron desarrollados a temperaturas que oscilan los 60 a 200 °C, en base a regresión lineal, con valores de 0,99, se determinó que es una reacción de orden 1 y 1,5, con un valor de contante de reacción de 0,14 y 0,089, respectivamente a una temperatura de 170 °C. En la Fig. 5, se especifica los valores para los subíndices: x = 1∼3, y = 0∼2 en la reacción de producción de resina fenólica del tipo resol.
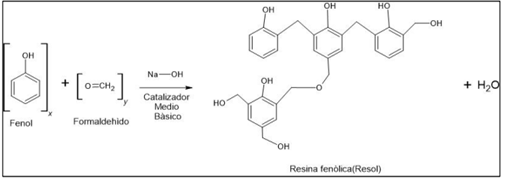
Fig. 5 Reacción química para la producción de resina fenólica. Fuente: Handbook of Plastic Foams. [23]
Diseño del reactor
Para la determinación del volumen del reactor (Ecuación 1), se estableció según el flujo volumétrico obtenido a la salida del reactor, esto multiplicado por el tiempo de residencia, y finalmente se aumenta un 20 % de factor de seguridad en el volumen (Ecuación 2).
Según Fogler, se establece que el reactor intermitente debe tener periodos establecidos de tiempo para la reacción, que en este caso es entre el fenol y el formaldehido, las variaciones de moles de fenol van a estar en función del tiempo y el volumen del reactor
(Ecuación 3)(Ecuación 4).[24]
El tiempo de residencia se calcula según la Ecuación 5, que ayuda a determinar el tiempo necesario para reducir el número de moles de fenoles iniciales a N número de moles de fenoles [25].
Los reactores discontinuos, emplean accesorios que ayuden alcanzar una conversión alta, el empleo de agitadores ayuda a poner en contacto los reactivos en todos los espacios del reactor, minimizando los puntos muertos dentro del reactor, asimismo mejora la transferencia de calor en la reacción [26, 27].
Obtención de resina fenólica del tipo resol
Se debe alimentar el reactor con las materias primas mencionadas, junto con un catalizador en medio básico. Se procede a elevar la temperatura del reactor hasta alcanzar la condensación de la alimentación, manteniendo una agitación uniforme a 2 500 rpm. El producto obtenido en el reactor se condensa hasta alcanzar los parámetros deseados, eliminando el exceso de agua. Finalmente, el producto obtenido se descarga en bandejas y la espuma floral se deja a temperatura ambiente durante dos días [8, 28].
Diagramas del proceso
En la Figura 6, se muestra el proceso simplificado y las principales operaciones para la obtención de espuma floral mediante un BFD y PFD. En el BFD, se muestran las 3 operaciones principales que son. la reacción, destilación y espumación, las corrientes principales de entrada y salida y las condiciones para cada proceso. Dentro del proceso de reacción esta es una de policondensación de fenol con formaldehido en presencia de un catalizado básico, una vez finalizado el proceso de reacción se realiza un proceso de neutralización con ayuda de un ácido (ácido clorhídrico) con el objetivo de llevar los reactivos a un pH neutro, una vez neutralizado se procede a la eliminación del agua producto de la reacción, esta destilación se lleva a cabo a temperaturas bajas (40 a 50 ºC) que van a depender de la presión (10 a 20 mmHg) a la cual opere el destilador. El proceso de espumado es donde se realiza el proceso de adición de surfactantes y aditivos que otorgarán las características principales de la espuma floral.
El PFD (ver Fig. 7), al ser un diagrama más detallado, se incluyen las operaciones auxiliares como bombas o mezclador que se importan para tener un proceso exitoso, en la primera corriente de bombeo de la solución de formaldehído se puede ver que se añade un intercambiador de calor a fin de tener una corriente que ingrese al reactor a una temperatura superior, y adicionalmente para evitar que se forme ácido fórmico a temperatura ambiente, adicional a lo mencionado en el diagrama BFD se tienen tanques de almacenamiento de los aditivos que se emplean en el proceso de espumado, los cuales son: hidratante, surfactante, urea al 1 %, colorante verde, ácido sulfónico y agente espumante [29].
Simulación
La simulación se desarrolló dentro del entorno de PROII, como punto de partida se da el empleo del paquete termodinámico, este permite simular el estado de los reactivos y productos a emplear, en este caso al tratarse polímeros se elige el POLYNRTL, requiere menos datos de atributos y estima los datos faltantes. Al no contar con los componentes dentro de la base de datos del simulador, se ingresa mediante la creación de estructuras de UNIFAC, que facilitan la estimación de propiedades del compuesto deseado [30].
El empleo de un reactor intermitente es necesario, se especifican las corrientes de entrada por lote, se establece el tiempo de reacción por lote, de 3 horas, los respectivos parámetros cinéticos y la relación estequiométrica de fenol/formaldehido de 4/7.
Mediante el proceso de simulación se ejecutaron alrededor de 5 simulaciones que permitieron obtener las condiciones de temperatura y presión que se muestran en resultados, lo que admite que se obtengan valores altos de conversión en tiempos menores.
RESULTADOS Y DISCUSIÓN
Mediante simulación de prueba y error, se determinó la cantidad óptima de reactivos que deben entrar en el reactor para obtener la resina fenólica necesaria para cubrir la demanda de espuma floral especificada en el balance de masas. Con base a la información revisada se determinó que, el proceso de producción por lotes es el más adecuado para cubrir la demanda interna de espuma floral [31].
Para el diseño de la planta de producción de espuma floral se realizó un balance de masa empleando ingeniería inversa, para a partir de la demanda establecer el valor del requerimiento de materias primas, mismas que luego pasarán por los diferentes equipos, en el caso del tanque espumador se obtuvo la siguiente composición:
Para los flujos másicos por componentes del reactor se implementó los datos en la Tabla 2, mismos que fueron estimados a kilogramos por día para satisfacer la demanda calculada de aproximadamente 144 toneladas anuales de resina fenólica.
En un inicio se implementó un reactor discontinuo en el que se introdujeron los valores de flujo en las corrientes de alimentación de fenol, formaldehído e hidróxido sódico, como se divisa en la Fig. 8, se empleó bombas para ayuda al movimiento de fluido de los reactivos (Tabla 3), que se mezclan en un mixer, para finalmente ingresar al reactor, donde se estableció el tiempo y se introdujo la reacción química (Fig. 5) con sus respectivos parámetros cinéticos, como se muestra en la Tabla 4.
Para obtener las composiciones en el reactor en función del tiempo, se obtuvo la masa en kilogramos de cada componente en el reactor discontinuo en función de la duración de la reacción que para este caso se estimó mediante un diagrama de concentración versus tiempo (Fig. 9). Los resultados de la simulación indican que en un periodo de 0,8 a 3 horas la cantidad de resina producida es menor en comparación con la obtenida en el periodo de 0 a 0,8 horas, lo que sugiere que la reacción debe producirse a 70 °C en un tiempo de reacción que debe ser aproximadamente de 1 hora [32].
De la Fig. 9 es evidente que a partir de 0.8 horas todo el fenol se ha consumido por completo. En estudios recientes se indica que el tiempo de reacción para la producción de resina fenólica tipo resol es de 3 horas y según Covarrubias et al (2016) el tiempo varía entre 2-5 horas.[22, 1] Sin embargo, los resultados de la simulación evidencian que en el período 0,8 - 3 horas la cantidad de resina producida es insignificante en comparación con la producida en el periodo 0-0,8 horas.
El volumen operacional del reactor se obtuvo por la ecuación 1, en un tiempo de reacción de 3 horas es de 13,7933 litros, el volumen del reactor se calculó por la ecuación 2, por lo tanto, se obtuvo 63,4552 kg/día de resina fenólica tipo Resol, necesaria para obtener espuma floral y así cubrir la demanda interna de este producto.
La energía utilizada en los diferentes procesos de obtención de resina fenólica del tipo resol, se resume en la Tabla 5, la energía total del proceso es de 15 879,8567 kJ/h, debido a que la planta de producción de resina fenólica trabajará durante un periodo de 24 horas laborables debido a que solo se estima la producción de 6 lotes/día, la energía total para llevar a cabo este proceso es de 381 116,5608 kJ/día laborable.
Estimación de la presión y temperatura de separación al vacío
Los procesos de deshidratación de resinas fenólicas tipo resol operan en un rango de 10 mmHg a 20 mmHg para la presión y de 40 °C a 50 °C para la temperatura, con el fin de conocer las condiciones del equipo implementado en el proceso para eliminar una mayor cantidad de agua, se realizó un análisis de sensibilidad entre la presión del separador y el flujo másico de agua que se eliminaba en forma de vapor.
Para la propuesta de diseño de recuperación de agua, se implementó un proceso de separación en el que se eliminó el 95,2595 % de agua de la corriente de vapor. Con el fin de reutilizar el agua eliminada en otros procesos químicos de lavado, se recuperó el vapor de agua mediante la separación del ácido clorhídrico de la corriente de vapor producida en un separador flash. Las composiciones de las corrientes de vapor (Tabla 6) y líquido (Tabla 7) muestran los valores a la salida del reactor, mostrando el consumo total del fenol, formaldehido y ácido clorhídrico.
La Fig. 10 muestra la configuración diseñada en Pro II, donde se observa generalmente la producción de resina fenólica (espuma floral) en cinco pasos. [33] El primer paso es la reacción de policondensación del polímero en el reactor discontinuo. El segundo paso es la neutralización de la resina. El tercer paso es la deshidratación, en la que se elimina el exceso de agua del polímero. En el cuarto paso, el producto obtenido en la corriente S17 se transporta a un tanque de agitación, donde se añaden los aditivos necesarios para la formación de espuma. En este paso la urea ayuda al proceso de curado y a eliminar el olor generado por los químicos empleados en la reacción de policondensación. [34] Finalmente, la espuma floral se coloca en moldes de 0,8 m•0,8m•0,8 m para que se seque a temperatura ambiente [35].
Todos los flujos del proceso simulado se presentan en la Tabla 8, donde se muestran los flujos másicos óptimos de cada componente a la entrada y salida de cada unidad, al inicio de la simulación del proceso se tenía problemas con la alimentación de formaldehido debido a la generación de ácido fórmico, dentro del reactor, problema que fue resuelto con la implementación de un intercambiador de calor a 50 ºC.
Análisis de sensibilidad
Se realizó un análisis de sensibilidad para determinar el valor de la presión requerida para condensar la corriente de vapor generada en la separación, en la Tabla 8, se tabula cómo varía la presión en el condensador en función de la fracción de líquido. Cuando se determinó la fracción líquida, la presión introducida fue de 18,70 mmHg, para recuperar el agua eliminada en el proceso (Fig. 11).
Obtención de la espuma floral
Para la obtención del producto final, el flujo másico de resina fenólica tipo resol obtenido en la simulación es de 63,4552 kg/día, junto con el resto de los flujos másicos calculados mediante balance de masas, en un tanque de espumación. Los caudales másicos se han obtenido en la Tabla 9 siguiente, que a diferencia de la Tabla 1, donde obteníamos las composiciones.
Finalmente, los datos obtenidos son 787015 kg/día de espuma floral, por lo tanto, se producirán 10,5758 kg de espuma floral en las 4 horas que dura el proceso, por lo tanto, el diseño propuesto satisface la demanda estimada de espuma floral en Ecuador para satisfacer la demanda requerida en el país.
Propiedades de la resina obtenida en la simulación
Una de las características principales es la densidad, que se encuentra en un rango de 1,28 - 1,32 g/cm3, la resina obtenida en la simulación presenta una densidad de 1,09 g/cm3. Covarrubias en 2016, menciona que la reacción de policondensación de fenoles con exceso de formaldehido en medio básico produce resinas fenólicas de peso molecular de 300 - 700 g/mol, la obtenida tiene un peso molecular de 532,59 g/mol [1].
Tiempo de operación de la planta
Para la obtención de resina fenólica tipo resol, la planta de producción opera por 24 horas diarias. Ya que la producción es por lotes, se estimó obtener 6 lotes de espuma floral con un periodo de duración de 4 horas por lote.
Propuesta de un reactor con mayor volumen
Mediante balances de masa y simulaciones, se determinó que, para cubrir la demanda interna de espuma floral, se necesita un reactor con un volumen aproximado de 17 litros para procesar 63,4522 kg/día de resina; sin embargo, debido a los altos costos de operación y limpieza, un reactor con un volumen menor a 17 litros es poco rentable; por lo que se propuso aumentar la capacidad del reactor a 100 litros para obtener una mayor cantidad de resina fenólica. La Tabla 10 muestra los caudales másicos del nuevo reactor [27].
CONCLUSIONES
A través de la simulación del diseño propuesto, se determina que para cubrir la demanda de resina fenólica (espuma floral) en Ecuador, es necesario un reactor batch de aproximadamente 17 litros. Adicionalmente, se propuso aumentar la capacidad del reactor a 100 litros para producir una mayor cantidad de resina fenólica, la cual puede ser utilizada en diferentes aplicaciones.
Se determina que el tiempo de reacción para obtener resina fenólica, a partir de fenol y formaldehído en medio de un catalizador básico es de 0.8 h, considerando que en este periodo el fenol se consumió completamente, al triplicar el valor de la alimentación se fija el tiempo de reacción en 3 horas, se identificó como óptimo para obtener la cantidad deseada de resina.
La demanda de resina fenólica presenta un panorama significativo ya que, al no existir oferta en el país, la demanda aumenta debido a la presencia de una gran variedad de industrias florícolas; del 2016 al 2020 existe la demanda de alrededor de 143 toneladas anuales, que pueden ser cubiertas con este diseño, y a través de los cálculos del nuevo reactor demuestra una mentalidad proactiva hacia la mejora continua y la optimización de procesos, que promoverían no solo la demanda local, si no su exportación a los países de la región. Se propuso un proceso de separación para recuperar el agua eliminada; esta medida no solo reduce el desperdicio de recursos, sino que también contribuye a la sostenibilidad ambiental de la operación.
Financiamiento.Conflicto de intereses.{ label (or @symbol) needed for fn[@id='fn3'] }