1. Introducción
La pobreza se relaciona estrechamente con el bajo consumo de alimentos, especialmente frutas y hortalizas, y con la desnutrición. Ecuador no es ajeno a esta problemática y según el Programa de las Naciones Unidas para el Desarrollo (PNUD, 2016), la pobreza en el Ecuador es alta y se ubica en el puesto 89 de los 188 países analizados, a pesar de los proyectos de desarrollo social que se han implementado en la última década por organismos gubernamentales y no gubernamentales. Asciende a 23,2 % a nivel nacional, pero a 40 % a nivel rural (INEC, 2019).
En la provincia de Santa Elena el índice de pobreza por necesidades básicas insatisfechas hasta el año 2010 fue de 72,2 % según datos del INEC (2010). Este indicador está directamente relacionado con la población rural que es predominante y se dedica a la agricultura tradicional, que no siempre genera rentabilidad.
Por otra parte, el clima semiárido de la provincia Santa Elena provoca un déficit hídrico todo el año. Las precipitaciones no cubren la demanda de los cultivos; por ende se debe promover el uso eficiente del agua (Secretaría Nacional de Riesgos, 2014). La escasa precipitación, que no supera los 200 mm anuales, obliga a los productores a cavar pozos que aportan agua de mala calidad debido a su dureza y alta salinidad. El viento afecta a las plantas exigiéndoles mayor gasto de energía para cubrir la transpiración. El ataque de plagas es otro factor que afecta considerablemente la productividad agrícola. Por estas razones los invernaderos, en los cuales puede lograrse un mejor control de las condiciones ambientales y sanitarias son un elemento que ayuda, en otras latitudes, a los productores a obtener una mayor rentabilidad. En este trabajo se utilizarán los términos invernadero y casa de cultivo como sinónimos.
El cultivo sin suelo aparece como una alternativa tecnológica válida para zonas áridas o semiáridas, suelos contaminados por el exceso de agroquímicos o por residuos industriales, para zonas con suelos marginales (por condiciones físicas, químicas o biológicas), los cuales no cumplen con los requerimientos nutricionales de las plantas. En los cultivos hidropónicos no es necesario el suelo, sólo se utilizan sustratos o soluciones acuosas nutritivas como soporte del desarrollo vegetal (Urrestarazu, 2004). La aplicación de esta técnica tiene ventajas tales como: reduce la pérdida de cultivos disminuyendo los problemas relacionados con proliferación de malezas y enfermedades de la raíz, por lo que desciende drásticamente la aplicación de plaguicidas; favorece un ahorro considerable del agua de riego y fertilizantes; no se necesita de grandes espacios para producir; existe una mayor higiene de la cosecha al no estar en contacto con la tierra; y lo más importante es un mecanismo sostenible y sustentable para luchar contra la pobreza (Irigo, 2010).
La hidroponía permite cosechar en periodos más cortos que la siembra tradicional, se obtienen productos con mejor calidad, mayor homogeneidad y más producción por superficie y se reduce la incertidumbre en la productividad por condiciones ambientales adversas. Además, se han reportado rendimientos 3 a 10 veces superiores a los de campo abierto (Cantiliffe y Vansickle, 2001).
Hace tres décadas Almería, una zona agrícola española de características agroclimáticas similares a la provincia de Santa Elena, transitó de sus principales rubros uva y cítricos a cultivos hortícolas en invernadero. Las empresas, de origen familiar, tenían dimensiones entre 1 y 1,4 ha y se transformaron en los principales proveedores de hortalizas frescas de Europa y luego de EEUU. Un aspecto socialmente muy sensible, la reactivación de la productividad de esos suelos pobres logró la reversión de la emigración campo-ciudad, generando empleo para los jóvenes (Cantiliffe y Vansickle, 2001).
Existen diversos métodos de cultivos sin suelos, algunos de ellos son: raíz flotante, sustrato inerte, aeroponía y el sistema NFT (nutrient film technique). Cada uno implica diversos tipos de infraestructura, materiales y especies vegetales susceptibles de ser cultivadas con manejos diferenciados. En este contexto, en las condiciones actuales donde se desenvuelve el agricultor peninsular, el cultivo sin suelo se perfila como una potencial alternativa productiva. Si bien es cierto que en los últimos años ha habido iniciativas locales de este tipo de producción, no se cuenta con reportes técnicos ni análisis de costos de los mismos. En la provincia de Santa Elena el cultivo sin suelo es una técnica relativamente nueva. Para postularla como alternativa productiva es necesario calcular los costos de inversión que implica la infraestructura, según el sistema a implementar. Es por ello que esta necesidad justifica realizar un análisis económico comparativo con distintos materiales disponibles, que sirva de consulta para eventuales emprendedores agrícolas.
El objetivo del estudio fue evaluar las inversiones de infraestructura con dos tipos de materiales, dos dimensiones de las casas de cultivo y tres sistemas productivos hidropónicos, como alternativa tecnológica que oriente futuros emprendimientos en la economía local.
2. Materiales y métodos
El proyecto se llevó a cabo en el Centro de Prácticas de la Universidad Estatal Península de Santa Elena, ubicada en el km 2 ½ de la vía principal La Libertad - Santa Elena, en el cantón La Libertad, perteneciente a la provincia Santa Elena. Su ubicación geográfica es: 2º12’55.83” de latitud sur y 80º52’33.30” de longitud oeste.
La zona posee una altitud aproximada de 32 m.s.n.m.; clima cálido seco, con vegetación de desierto tropical. La temperatura promedio es de 24ºC y con una humedad relativa de 81,6% y precipitaciones de 200 mm anuales (INAMHI, 2017).
2.1. Tipo y tamaño de los invernaderos
Se probaron dos tipos de invernadero tipo capilla a dos aguas, susceptible de cultivarse con los sistemas sustrato inerte, raíz flotante y forraje verde hidropónico. Su dimensión se asumió en 105 m2 con 15 m de largo por 7 m de ancho, 2 m de pared lateral y 3.5 m altura en el centro. Estas son las dimensiones más utilizadas a nivel de pequeños agricultores locales. La segunda dimensión fue de 1.000 m2 con 30 m de largo por 35 m de ancho, 2 m de pared lateral y 4 m de altura en el centro (5 casas de cultivo juntas). Los materiales evaluados fueron caña guadua y fierro galvanizado. Para ambos tipos de estructura se consideró techo de polietileno UV-IR (plástico) y paredes de zarán 50% sombreo.
Las empresas de la Región Sierra ofrecen precios de invernaderos de estructura metálica según el material (fierro galvanizado o aluminio) y las dimensiones de la nave. Si el espacio para el invernadero supera los 500 m2 el precio fue de 10 $.m-2 (a septiembre del 2018). Si el espacio para el invernadero es menor a 500 m2 el valor subió a 12,00 $.m-2.
2.2. Sistemas de cultivo
a) Para el sistema de sustrato inerte se construyeron camas de madera de 3 m de largo por 1 m de ancho y una altura de 20 cm (Figura 1). El mercado local no dispone de las canaletas o mangas de sustrato inerte que se utilizan en otros países para estos fines. La casa de cultivo de 105 m2 tuvo una capacidad para nueve (9) de estas camas, y consecuentemente, para el invernadero 10 veces mayor la capacidad fue para 90 camas. El sustrato utilizado fue 50 % de cascarilla de arroz carbonizado (orgánico) y 50 % arena de río Nº 2 (inorgánico). La estufa para quema de cascarilla de arroz fue de fabricación artesanal.
b) En el sistema de raíz flotante cada cama fue construida en madera con tablas de 3 m x 0,1 m x 1” (largo x ancho x espesor) descansa sobre cuartones que sirven como soporte quedando el borde superior a una altura de 90 cm para facilitar el manejo de las plantas (Figura 2). Al igual que en el sistema sustrato inerte se coloca cartón para proteger el polietileno de las astillas. Cada cama cuenta con una salida de estanque que drena la solución fertilizante cuando ésta sube de nivel, permitiendo la recirculación del agua con la solución. La cama contiene un nivel de agua de 8 cm sobre el cual flota una plancha de espumafon de 1” de espesor y una dimensión de 1 m x 1 m. En cada perforación realizada en dicha plancha (en zig-zag a 20 x 17 cm) se colocó un plantín cuyo cuello estuvo envuelto en esponja para sujeción, resultando en 32 plantas por metro cuadrado.
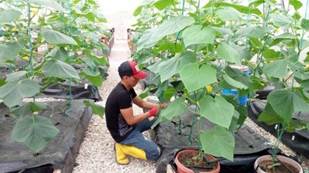
Fig. 1 Estructura de camas en el sistema sustrato inerte para la producción de pepino hidropónico, Santa Elena, Ecuador.
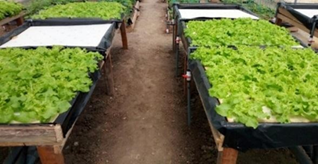
Fig. 2 Estructura de camas en el sistema raíz flotante para la producción de lechuga hidropónica, Santa Elena, Ecuador.
c) Para el sistema de forraje verde hidropónico (FVH) se utilizó una estructura metálica de soporte de las bandejas con una dimensión de 6.50 m de largo, 1.30 m de ancho y 2 m de alto con 4 pisos con 50 cm entre ellos. Esta estructura albergó 26 bandejas de 60 cm x 40 cm (Figura 3). Las bandejas son de plástico termoformado con 11 orificios de 8 mm de diámetro en su cara frontal. En cada invernadero de 105 m2 cupieron cuatro (4) de estas estructuras. En total se utilizaron 416 bandejas por casa de cultivo equivalente a 104 m2 de superficie de producción (4 bandejas por m2). Las bandejas en la casa de 1.000 m2 fueron 4160.
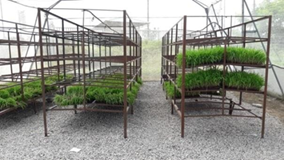
Fig. 3 Estructura de camas metálicas para el sistema de forraje verde hidropónico, Santa Elena, Ecuador.
El sistema de riego contuvo entre sus componentes principales un tanque fertilizante de 500 L y una bomba sumergible, la cual se calculó para los sistemas de sustrato inerte y raíz flotante en 0,5 HP para la casa de cultivo de 105 m2 y 1 HP para la de 1.000 m2. Mientras que para el sistema de FVH se requirió una bomba centrifuga de 1,5 HP.
2.3. Análisis económico
La inversión se agrupó en los materiales y equipos más la mano de obra en construcción e instalación de: a) estructura de nave, b) camas de cultivo y c) sistema de riego. El costo de los equipos y materiales fue determinado considerando todos los rubros que intervienen en el proceso de producción bajo las particularidades de los sistemas hidropónicos y cotizados a nivel local en Santa Elena, Ecuador (dólares americanos a septiembre de 2018).
Los costos directos consideraron semillas o plántulas, fertilizantes y pesticidas, además de la mano de obra (entre 1 y 4 personas según el rubro), un asesor de campo y servicios básicos (luz, agua). En la lechuga producida en sistema raíz flotante se agregaron gastos en gavetas y fundas plásticas (envase de comercialización).
Una vez establecidos los valores de las inversiones, se realizó el respectivo análisis económico - financiero, según Guerra (2012).
Se verificó el impacto de los cambios en los principales componentes de la inversión, según el material, el tamaño del sistema productivo y la estructura final de costos.
Para el cálculo de la depreciación de las naves se utilizaron criterios correspondientes al Art. 28 de Ley Orgánica de Régimen Tributario Interno que habla sobre los gastos generales deducibles (SRI, 2014). Para la casa de caña se utilizó el 10%, y considerando una vida útil a 5 años. Al final del 5to año de vida útil del invernadero se obtuvo una pérdida de USD 368.22 dólares americanos debido a la depreciación de la infraestructura. Para la nave de fierro galvanizado se estimó la depreciación con una vida útil a 20 años utilizando el 5% anual que corresponde al porcentaje de depreciación de inmuebles. El valor a depreciar por cada año fue de USD 70,56 dólares.
Para la inversión total se consideraron los costos de construcción e instalación de los invernaderos, del sistema de riego, la construcción de camas de cultivo, la mano de obra requerida para cada uno de estos ítems y un 5% para imprevistos.
3. Resultados y Discusión
La construcción de un sistema hidropónico consta de dos fases: (1) el levantamiento de la infraestructura de la casa de cultivo, (2) la elaboración y posicionamiento del sistema productivo en sí que contiene las plantas (Senel et al., 2015). Cada una presenta sus complejidades y costos iniciales y de mantenimiento.
3.1. Inversión en infraestructura de invernadero
La construcción de la casa de cultivo en la provincia de Santa Elena se consideró en caña guadua, por ser el material de disponibilidad local. El costo (materiales + mano de obra) ascendió a USD 1.126,43 dólares para un invernadero de 105 m2 y a USD 9.074,77 proyectando una con las mismas características a 1.000 m2 (Tabla 3).
El valor cotizado en una empresa de Quito para la construcción e instalación de un invernadero de 105 m2 y otro de 1.000 m2 en fierro galvanizado prefabricado fue de USD 1.411,20 y USD 10.151,20 con IVA incluido, respectivamente. El valor es por obra completa, es decir, instalado (incluye el costo del material, flete y mano de obra utilizada).
Se evidenció que el aumento del costo no es lineal, debido al aprovechamiento de paredes laterales comunes. El costo entre una casa hecha en metal versus una en caña fue superior en 25% a pequeña escala (105 m2) y sólo 12 % a mediana escala (1.000 m2). Si se considera la mayor vida útil y el hecho de que prácticamente no hay necesidad de labores de mantenimiento, la balanza se inclina hacia recomendar invertir en este material antes que en caña guadua.
3.2. Inversión en sistema sustrato inerte
Los costos de insumos y materiales requeridos para la construcción de las nueve (9) camas para el sistema sustrato inerte, que se proyectaron para un invernadero de 105 m2 ascendió a USD 822,78. Para Orellana y León (2011) dentro de los materiales de construcción para un sistema con sustrato inerte, en cultivo de pimiento, el principal ítem de gasto fueron las canaletas metálicas que acogen las plantas. Este material es más oneroso que el usado en esta investigación, pero mucho más idóneo, aunque no estuvo disponible a nivel local.
La Tabla 1 presenta los costos de los materiales que se utilizaron en el sistema de riego y drenaje implementado en cada sistema de cultivo. Los valores totales varían en correspondencia con las características de cada sistema. En el caso del pepino (sustrato inerte) la superficie efectivamente productiva es de un 28%, el resto corresponde a pasillos los cuales permiten el acceso y tránsito del personal para el manejo del cultivo. Sería necesario modificar el diseño para lograr una mayor eficiencia en el uso del suelo, por ejemplo, con mangas de polietileno.
3.3. Inversión en sistema raíz flotante
Los insumos y materiales para la construcción e implementación de nueve camas de madera para el cultivo de lechuga en sistema de raíz flotante ascendieron a un costo de USD 473,51. Estos valores son referidos a precios del mercado local de la provincia de Santa Elena. En la Tabla 1 se presentan los costos de los materiales que fueron utilizados para el sistema de riego con recirculación, que incluye para cada cama una entrada, una salida y tuberías de retorno al tanque fertilizante.
3.4. Inversión en sistema Forraje Verde Hidropónico (FVH)
Los materiales usados en el sistema de forraje verde hidropónico tuvieron un costo de USD 7.237,36 dólares americanos (Tabla 2). Lo más costoso del sistema fueron las bandejas, ya que son importadas y su valor unitario es elevado (USD 5,00). Cabe recalcar que, según la empresa consultada (Termopack, mercado de Sangolquí, provincia de Pichincha), la producción y venta de estas bandejas especiales de plástico termoformado es bajo pedido con una solicitud mínima de 10.000 unidades. Si bien el costo unitario de cada bandeja es bajo, lo más caro es el molde para fabricarlas. Por lo tanto, sólo se justifica el molde para una dimensión de nave de 1.000 m2.
En la Tabla 1 se pueden observar los costos de los materiales que se usaron para el sistema de riego por nebulización, este valor asciende a USD 790,77, correspondiente al mercado local de la provincia de Santa Elena.
La superficie de suelo utilizada en cada invernadero de 105 m2 correspondió a 33,8 m2 usados para la estructura de forraje verde hidropónico. Los cuatro pisos conteniendo 416 bandejas tuvieron una superficie productiva de 104 m2. Los pisos productivos dieron un 100% de aprovechamiento del espacio.
3.5. Inversión Total
La inversión en todos los casos evaluados fue alta. Khan et al. (2018) concuerdan en que el alto costo de partida y de mantenimiento es uno de los principales desafíos para un invernadero hidropónico.
Según Tyson et al. (2004), la dimensión mínima para establecer un sistema hidropónico estándar debe albergar al menos 40 plantas de hortalizas de fruto (ej. tomate, pepino) y 72 plantas pequeñas como las hortalizas de hoja o fresas.
Para la inversión a pequeña escala de 105 m2 existió una diferencia aproximada de sólo USD 300 entre la nave construida en caña y en metal (Tabla 3). Como era de esperarse la mayor inversión corresponde al invernadero metálico. Por esta razón la balanza se inclina hacia el uso del material metálico.
Para los sistemas de sustrato inerte y raíz flotante en 105 m2, independiente del material de construcción de la casa de cultivo, el ítem de mayor relevancia en la estructura de costos fue el sistema de riego, variando entre 36,21 y 46,43 % (Tabla 3). Esta constatación justifica aumentar la escala de producción para aumentar la eficiencia de la inversión en riego.
Tabla 2 Costo de materiales en sistema de producción de FVH (maíz) para 105 m2.
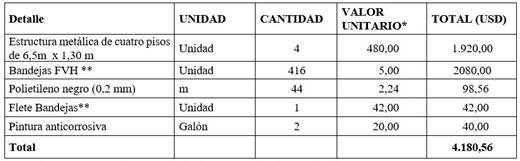
Nota: * Valor en mercado local (provincia de Santa Elena) a septiembre 2018.
**Valor mercado Sangolquí (Provincia de Pichincha) a septiembre 2018.
El sistema de riego en raíz flotante tiene mayor costo y porcentaje de participación en la inversión, debido a que se necesita un sistema de recirculación de la solución fertilizante, lo cual redunda en más metros de tuberías y se requiere una tubería gruesa de retorno. En este caso el sustrato inerte no tuvo un sistema de drenaje integrado y adecuado. La recolección y reutilización del drenaje (agua con nutrientes) marca la diferencia en la rentabilidad de un sistema hidropónico (Grewal et al. 2011). Al construir un sistema más tecnificado y eficiente, es probable que los costos se acerquen al de la raíz flotante.
La información referida a costos de inversión en cultivos sin suelo es escasa. Costos de inversión para invernaderos de cultivos en sustrato inerte reportado por Córdova (2005) indican que los ítems de mayor importancia para un sistema de sustrato inerte se dieron en la construcción del invernadero de madera, la construcción de contenedores y el sistema de riego con aportes del 30-30-12 %, respectivamente. Los dos primeros valores fueron levemente superiores y el tercero muy inferior a los encontrados en el presente estudio en caña guadua con 28,21-28,11-38,92%, en el mismo orden de los parámetros mencionados. Esto pudo deberse a diferencias entre materiales usados, dimensionamiento de bombas, distancias a cubrir por las tuberías o a diferencias de precios entre países.
El uso de metal en la construcción superó en la inversión total en sólo 7,58% y 5,50% al emplear caña (material orgánico, degradable, sensible al ataque de plagas y a la humedad) para la pequeña escala 105 y 1.000 m2, respectivamente. Debe tenerse en cuenta este aspecto relevante al momento de elegir el material de construcción del invernadero. En la medida que los cultivos protegidos se han ido masificando en la Sierra ecuatoriana los precios han bajado y hoy tienen una mayor y más asequible oferta para esta tecnología.
Para invernaderos con un sistema de raíz flotante reportado por INIA (2016) el ítem más significativo en la inversión total fue la construcción de camas para el cultivo con un 35%, superior a lo encontrado en este proyecto en el invernadero de caña en que la construcción de cama representó 19,87 y 28,49% de la inversión para casas de cultivo de 105 y 1.000 m2.
La tecnología de FVH presentó una situación diferente, ya que aquí la construcción de las camas de cultivo superó con creces a los otros dos ítems de gastos, oscilando entre 60 y 70 % en todos los escenarios planteados (Tabla 3).
En este sistema la inversión total es mayor a los anteriores y supera los USD 6.000 y 45.000, para los modelos de 105 y 1.000 m2, respectivamente. Las estructuras que soportan la producción son metálicas, lo cual encarece mucho el sistema (Tabla 2 y 3). Es necesario verificar la factibilidad de reemplazar esto con diseños en postes de concreto y alambre. No hay restricciones en este sentido. La habilidad del agricultor para diseñar y confeccionar sistemas alternativos que cumplan con los requerimientos técnicos (drenaje, pendiente) permitirá disminuir costos.
En este sistema cobran aún más relevancia las consideraciones respecto a la vida útil, necesidad de mantenimiento y la sensibilidad de la estructura a la humedad, ya que parte del manejo consiste en la nebulización del forraje cada dos horas (Villavicencio, 2014; Acosta, 2016), es decir, el ambiente se satura periódicamente de humedad y esto hace acortar aún más la vida útil del invernadero de caña. Frente a esto la estructura de fierro galvanizado, la cual no se oxida, representa una clara ventaja para la inversión.
Villavicencio (2014), quien trabajó con invernaderos de madera para forraje verde hidropónico, determinó que cada uno de los ítems considerados para el análisis (casa, estantes para bandejas, riego y mano de obra) aportó alrededor de un 25%. Esta diferencia radica en los materiales usados para la estructura de soporte de las bandejas.
El sistema de riego, principal gasto en los otros sistemas analizados, en el sistema FVH fue de menor importancia y a mayor dimensión del sistema productivo más decreció su peso. Esto indica que es prioritario rentabilizar al máximo la inversión en riego. Por lo que se justifica proyectar la inversión a una superficie de escala media para aprovechar al máximo el sistema de riego presupuestado.
Por tanto, se asumió un tamaño construido de 1.000 m2 y aun siendo una superficie 10 veces mayor los costos aumentaron en una proporción de cinco veces, por economía de escala. Dicho aumento de superficie generó que la inversión en riego representara en la mayor escala alrededor del 41, 59, 89 % respecto de la menor escala de 105 m2, sin importar el material seleccionado para la casa (Tabla 3). Los equipos de riego (bomba y programador) pueden ser optimizados, instaurando sectorización y ciclos de riego.
Durante el funcionamiento operativo del sistema, aunque los costos directos fueron considerables, sus montos son de menor relevancia comparado con un sistema en clima templado, debido al clima cálido y la alta intensidad luminosa locales, que no exigen gastos en calefacción e iluminación. Éstos son los principales costos de este tipo de producción en el hemisferio norte (Senel et al., 2015).
En este trabajo se han analizado los costos de inversión en tres sistemas productivos para dos tipos de casa de cultivo. El próximo paso en la investigación es la valoración del riesgo de cada alternativa estudiada con el empleo de la simulación de Monte Carlo. De esta manera se podrá predecir la incertidumbre de cada propuesta.
Tabla 3 Participación de los ítems de costos en la inversión total de las distintas escalas de producción (m2) según material de la casa de cultivo y sistema de producción.
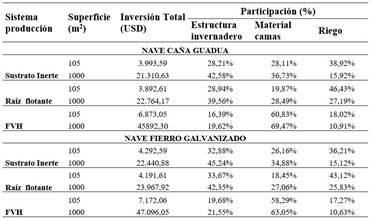
Este paso es clave, ya que ante las características propias del sector hortícola como lo son perecibilidad, estacionalidad, localización, baja diferenciación y estandarización del producto e informalidad (Irigo, 2010) se debe minimizar el riesgo de la inversión. Generalmente los costos no se corresponden con los precios de mercado, haciendo de este un rubro de mucha incertidumbre en los resultados económicos.
Por otra parte, los desafíos que enfrenta un productor hortícola en la Sierra ecuatoriana declarados por Zaruma (2009) pueden hacerse extensivos a la realidad costeña, a saber: baja oferta productiva y afrontar los puntos críticos que afectan la competitividad, relacionados con niveles de asociatividad, correlación de actores, aplicabilidad y conocimiento tecnológico, baja capacidad de gestión y gerencia empresarial agrícola. La competitividad debe solucionarse mediante volúmenes de producción, encadenamiento de la producción y comercialización.
4. Conclusiones
El análisis económico comparativo de los costos de inversión de tres sistemas de cultivos sin suelo, tanto para 105 como 1.000 m2, determinó que el de menor inversión fue el sustrato inerte, mientras que al forraje verde hidropónico correspondieron los mayores valores. La elección de la inversión a realizarse debe complementarse con la productividad anual, los rendimientos y precio esperado para cada especie vegetal, según el sistema seleccionado.
El uso de metal en la construcción de la casa de cultivo superó en la inversión total en sólo 7,58% (USD 300) y 5,50 % (USD 1.200) al uso de caña para la escala de 105 y 1.000 m2, respectivamente. Esto estimula a elegir este último en caso de una inversión por su durabilidad y bajo costo de mantenimiento.
Para los sistemas de sustrato inerte y raíz flotante, con independencia del material de construcción de la casa de cultivo, el ítem de mayor relevancia en la estructura de costos fue el sistema de riego. Al aumentar la superficie construida disminuye de forma considerable esta participación, ya que éste puede ser optimizado mediante sectorización y ciclos de riego.
En el modelo productivo de FVH el mayor gasto en la inversión total lo representaron las camas de cultivo, incluyendo las estructuras metálicas y las bandejas plásticas donde se desarrolla el forraje, sin importar del tipo de casa de cultivo.