Introducción
La Faja Petrolífera del Orinoco (FPO) constituye la fuente de reservas de hidrocarburos pesados y extrapesados más grande del mundo, se ubica al sur de los estados Guárico, Anzoátegui, Monagas y Delta Amacuro y tiene una extensión de 55.314 km2. De acuerdo a Pasquali [1], es una gran concentración de hidrocarburos que alcanza un volumen in situ de unos 1,3 x 1012 barriles (bbl). Éstos incluyen un 65 por ciento de crudos extra pesados y un 35 por ciento de betún o bitumen natural. Se estima que unos 230 x 109bbl puedan ser extraídos económicamente. En la actualidad, la oferta de petróleos pesados ha ido aumentando en el mercado mundial, pero, esto no le resta la importancia que representa la FPO como factor clave en los planes de desarrollo de la industria petrolera y por ende de la nación [2].
No obstante, dada la necesidad de producción de fracciones más ligeras del petróleo, como crudo mediano y liviano, gasolina, querosén y gasoil; es necesario procesar este petróleo más pesado para satisfacer al mercado consumidor. Como consecuencia de estos requerimientos en el Complejo Petroquímico General de División José Antonio Anzoátegui, actualmente se produce un sub producto denominado coque de petróleo.
El coque de petróleo, resulta del proceso de refinación de crudos pesados y extrapesados en la industria petrolera. Este proceso involucra etapas de craqueo y condensación que descomponen térmicamente los crudos para recuperar derivados de interés, tales como gases y fracciones livianas, produciendo un residuo sólido negruzco mediante reacciones secundarias, que se conocen con el nombre de coquización [3]. Dicho residuo, es la materia sobrante del proceso de refinación de las fracciones más pesadas provenientes de los fondos de las torres de vacío de las refinerías, el cual se recolecta en espacios especiales y previamente determinados para tal fin, por un período de tiempo definido [4].
La producción de coque de petróleo en una refinería no está asociada con el mercado, no se decide producir cierta cantidad de coque de petróleo para satisfacer la oferta y la demanda del producto. La razón de la producción de coque de petróleo está vinculada al incremento de las fracciones pesadas que son convertidas en fracciones ligeras. Actualmente, la acumulación del coque en el Complejo Petroquímico General de División José Antonio Anzoátegui alcanza las 21.000 toneladas diarias[5], lo que lo convierte en el segundo productor de coque de petróleo a nivel mundial, antecedido solo por los Estados Unidos.
En lo que respecta a los fluidos de perforación, los fluidos base de agua dispersa han sido ampliamente utilizados en el pasado y, a pesar de algunas limitaciones, siguen siendo los más utilizados en la industria de la perforación, debido a su bajo costo, flexibilidad y fácil mantenimiento [6]. Uno de los principales problemas de estos tipos de fluidos es su limitada estabilidad reológica a altas temperaturas, donde tienden a un engrosamiento y una gelificación progresiva [7].
Para dar solución a este inconveniente son diversos los aditivos empleados, ellos son agentes de distinta naturaleza que al ser agregado en una concentración definida a un sistema de fluido de perforación controlan el comportamiento real del mismo [8]. Uno de los aditivos mayormente usado en fluidos de perforación es el dispersante o lignosulfonato como se le conoce comercialmente, los cuales son ácidos orgánicos que le proporcionan aniones (iones negativos) al fluido de perforación.
Estos aniones reducen el punto cedente y los esfuerzos de gel al neutralizar los cationes (iones positivos) en las partículas de arcilla, des floculando con ello la lechada de arcilla y haciendo que las partículas se repelan. Los lignosulfonatos no solamente reducen la viscosidad y el esfuerzo de gel, sino que cuando se usan en cantidades suficientes, también reducen la pérdida de agua y proporcionan un ambiente inhibidor [9].
Este efecto de dispersante fue constatado al adicionar concentraciones de coque a fluidos base agua cuando el mismo se empleó con éxito como controlador de filtrado en fluidos base agua, provocando disminución de los valores de viscosidad plástica y punto cedente [10]. En tal sentido, la investigación tuvo como propósito corroborar si el coque de petróleo del Complejo Petroquímico General de División José Antonio Anzoátegui actúa como dispersante en fluidos de perforación base agua.
Materiales y métodos
Inicialmente el coque de petróleo obtenido del Complejo Petroquímico General de División José Antonio Anzoátegui - Venezuela, fue sometido a un proceso de molienda en un molino de martillo de escritorio del laboratorio de suelos de la Universidad de Oriente, Campus Los Guaritos; posteriormente con el propósito de obtener una homogeneidad en el tamaño de las partículas del coque de petróleo se realizó un tamizado, con lo que se logró una heterogeneidad entre las partículas que integraron los aditivos sólidos de los fluidos base agua formulados.
La concentración de azufre en el coque se determinó aplicando el procedimiento descrito en la norma ASTM D3177-02[11]. Una vez determinada la cantidad existente de azufre en el coque, se procedió a disminuir su concentración, mediante la aplicación de un proceso de desulfuración por microondas [12].
Con la finalidad de conocer cuáles son los componentes presentes en el coque de petróleo, se analizó el mismo mediante Espectroscopia Infrarrojo de Transformada de Fourier, para ello se utilizó un equipo Perkin Elmer FTIR 1600.
Para el estudio de las propiedades del fluido de perforación, se formularon 4 fluidos de perforación tipo lignosulfonato tal como es indicado por la empresa Samán Tecnología Integral en Petróleo[13] (Tabla 1), en el cual se sustituyó la concentración del lignosulfonato (dispersante) con concentraciones de 1,5 g, 2 g, 2,5 g y 3 g de coque de petróleo; adicional a esto se formuló un fluido patrón (blanco) sin presencia de dispersante, lo que permitió la evaluación de la disminución de reología, asumiéndose como criterio de aceptación si el coque era capaz de disminuir en un 50% la reología inicial de un fluido luego de su aplicación.
En el laboratorio de fluidos de perforación de la Universidad de Oriente fueron realizadas las formulaciones los fluidos requeridos y medición de las propiedades físicas después del envejecimiento dinámico en un horno de rolado a 120°F y 500 lpcm durante 16 horas, fueron realizadas de acuerdo a lo establecido por American Petroleum Institute (API 13B-1) [14], permitiendo así analizar el comportamiento descrito por dichas propiedades.
Posteriormente con el uso de una hoja de cálculo se conoció el porcentaje de disminución de la reología y filtrado API, las fórmulas utilizadas en la aplicación, están basadas en la norma API [14] y la Norma calidad de la Empresa Samán, Tecnología Integral en Petróleo [13]. Dicho programa también permitió el cálculo de la viscosidad plástica y punto cedente.
A continuación, se procedió a comparar estadísticamente las propiedades físicas (viscosidad plástica, punto cedente, geles 10s y 10 min, filtrado y porcentaje de reducción de reología) del fluido formulado utilizando coque de petróleo en sus distintas concentraciones con las de un fluido patrón, formulado con un dispersante comercial (lignosulfonato), para ello se empleó un modelo estadístico aleatorio simple, donde se estudiaron de manera individual los distintos tratamientos (propiedades) dependiendo de la concentración de coque de petróleo utilizada en la preparación de los diferentes fluidos de perforación y se realizaron tres repeticiones (Tabla 2).
Para ello se aplicó una prueba estadística no paramétrica de Friedman con α=0,05, a través del programa estadístico InfosStat, lo que permitió establecer si los fluidos formulados con coque de petróleo presentaban diferencia estadísticamente significativa con el fluido patrón (lignito comercial) en las propiedades o descritas.
Resultados
Molido y tamizado el coque de petróleo se conoció la cantidad de azufre contenida en él, resultando ser de 5,35 % v/v, de acuerdo a este valor se considera como medio y alto azufre (2-8%) los cuales son usados principalmente como combustible en calderas para la producción de vapor en generación eléctrica, procesos industriales y en hornos para la producción de cemento[13].Posterior a la aplicación del procedimiento de desulfuración por microondas, se logró reducirlo a 2,46%v/v, representando una disminución de 45,9 %.
El coque de petróleo se analizó mediante Espectroscopia Infrarrojo (IR) de Transformada de Fourier empleando el Módulo de Reflexión Total Atenuada. En el espectro (Figura 1) se observó vibración de alargamiento de enlace OH o agua en el intervalo entre 3100-3700 cm-1 que no son representativos en el estudio realizado. En el intervalo 3000-3100 cm-1 se percibió la presencia de alargamientos aromáticos C-H; en el intervalo 2800- 3000 cm-1 se apreció marcadamente la representación de alargamiento C-H alifático, es decir, gran presencia de compuestos completamente parafínicos.
El intervalo 1680-1790 cm-1 marcó de manera definida la presencia de alargamiento C=O de grupos carboxílicos, principalmente de ésteres en el coque de petróleo objeto de estudio. El intervalo de 1500-1680 cm-1 representa la zona de coque (C=C).
Debido a presencia de agua observada durante el análisis del espectro IR (Figura 1), se hizo uso de otra unidad del espectroscopio de infrarrojo, conocida como unidad de transmisión; requiriéndose de la preparación de una pastilla de coque de petróleo con Bromuro de Potasio (KBr). El espectro obtenido con la utilización de este procedimiento es mostrado en la Figura 2.
En ella se observa la presencia de la vibración de alargamiento del enlace C-H en el intervalo 3000-3100 cm-1 el cual corresponde a compuestos aromáticos. En el intervalo 2800-3000 cm-1 existen las vibraciones de alargamiento C-H típicas de los compuestos parafínicos y por último se evidencia la banda característica de grupos carbonílicos, específicamente esteres en el intervalo 1700-1800 cm-1. La información sobre aromáticos, olefinas y parafinas es de suma importancia en los estudios que siguen la evolución del coque, a raíz de los cambios aplicados en las condiciones de la conversión catalítica y en las propiedades del catalizador [15].
La zona de absorción para el coque está localizada alrededor de los 1600 cm-1, de acuerdo a esto el coque puede considerarse como coque II (coque negro, o de alta temperatura) debido a que está constituido por poliolefinas, alquilaromáticos y aromáticos que dan fuertes señales en ≈1600 cm-1 y en ≈3040 cm-1 [16].
Se aprecia en ambos espectros IR la existencia de grupos funcionales aromáticos, parafínicos y carboxílicos en la muestra de coque de petróleo estudiada, lo que ratifica que estos elementos conforman el coque de petróleo. Asimismo, se obtuvo un coque de petróleo con importante presencia de grupos carboxílicos principalmente esteres, lo que permitió asumir que puede ocurrir con él algo similar a lo que sucede durante la saponificación de éster; de acuerdo a García [15], consiste en una reacción química entre un ácido graso (o un lípido saponificable, portador de residuos de ácidos grasos) y una base o alcalino, en la que se obtiene como principal producto la sal de dicho ácido y de dicha base. Estos compuestos tienen la particularidad de ser anfipáticos, es decir tienen una parte polar y otra apolar (o no polar), con lo cual pueden interactuar con sustancias de propiedades dispares.
Continuando con la metodología propuesta se formularon cuatro (4) fluidos de perforación utilizando el coque de petróleo como dispersante variando las concentraciones, tal como se planteó en la Tabla 2, además de un fluido blanco, luego de ser envejecidos se conocieron y estudiaron sus propiedades físicas descritas a continuación.
Con respecto a la densidad de los fluidos, basado en la concentración de aditivos y la cantidad de agua agregada en la formulación de los fluidos, la densidad debería corresponder al valor de 13 lpg; observando la Figura 3, se tuvo que para el caso del fluido blanco el estudio se adapta correctamente al valor requerido, pero con la posterior adición de coque se inician variaciones en función de décimas en cuanto a los valores obtenidos, situación que es más notorio para los fluidos 3 y 4 donde hay un incremento en la cantidad de coque utilizado.
La densidad de los fluidos de perforación es una propiedad importante durante las actividades de perforación, la misma debe ser la adecuada debido a que es la que permite el control de la presión hidrostática y ayuda a mantener la seguridad en el pozo, evitando el flujo de los fluidos de la formación hacia el pozo [8 ], Se observa con los resultados obtenidos, que con la utilización de coque de petróleo en los fluidos de perforación base agua, éste altera el valor de la propiedad solo en décimas, por lo que se considera aceptable en esta fase. No obstante, el estudio estadístico aplicado más adelante permitirá conocer si el cambio en decimas es significativo o no.
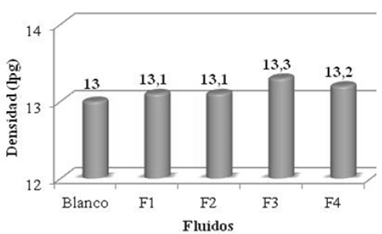
Fig. 3: Densidades de los fluidos de perforación base agua utilizando diversas concentraciones de coque de petróleo, después del envejecimiento.
Al analizar la propiedad de viscosidad plástica de los fluidos formulados (Figura 4), se consideraron con mejor desempeño los fluidos 1 y 2, en los cuales se obtuvo menor valor que para el fluido blanco, pese a que se estaba incrementando la cantidad de sólidos de la fase dispersa del fluido, infiriéndose que el coque de petróleo posee características de dispersante que permiten un alejamiento entre las partículas, disminuyendo la resistencia que podría oponer el fluido para desplazarse.
En el caso del fluido 3 se observa que aun cuando se adicionó mayor cantidad de sólidos se obtiene una disminución de viscosidad plástica con respecto al fluido blanco, pero se incrementó con relación a los fluidos 1 y 2, lo que pudiera indicar que se alcanzó el punto de saturación del fluido. En el fluido 4, la viscosidad plástica se incrementó incluso por encima del fluido blanco, mostrándose entonces que ya existe una excesiva cantidad de sólidos en la fase dispersa que aumenta la resistencia al flujo del fluido de perforación base agua tipo lignosulfonato.
Examinando los valores de punto cedente obtenidos en comparación a un fluido no tratado con coque de petróleo (blanco), se observó que en el caso de los fluidos 1, 2 y 3 se logró una disminución apreciable de la propiedad, lo que indicó que pese a no obtener el valor adecuado podría asumirse que el coque de petróleo si aporta aniones que repelen las cargas negativas de la superficie externa de la bentonita. En el caso del fluido 4, se observa un incremento del valor de punto cedente y la viscosidad plástica con respecto a los fluidos anteriormente descritos, debido a que luego del valor de 2,5g de coque de petróleo el fluido pasa a un estado de saturación donde sus valores se incrementaron por el contenido de partículas sólidas en la fase dispersa.
Es importante resaltar que ninguno de los fluidos formulados (Figura 4) cumplió con dos premisas básicas para la viscosidad plástica y el punto cedente. Así según M-I Swaco [10], establece que el límite práctico del valor de viscosidad plástica para fluidos de perforación base agua corresponde al doble del peso del fluido. Con respecto al punto cedente el mismo autor expone que los sistemas de fluido-arcilla de Lignosulfonato disperso deben ser típicamente mantenidos a un nivel aproximadamente igual al peso del fluido.
Con las lecturas obtenidas del viscosímetro a las velocidades de 600, 300, 200, 100, 6 y 3 RPM se procedió al cálculo de porcentajes de reducción de reología, se observa en la Figura 5 que en el caso del F2, se obtuvo un valor de 47,76% cercano a lo esperado indicando dicha concentración como la más aceptable para la formulación con coque de petróleo como dispersante en fluidos base agua tipo lignosulfonato.
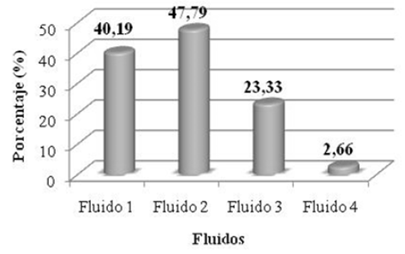
Fig. 5: Porcentaje (%) de reducción de reología de los fluidos de perforación base agua utilizando diversas concentraciones de coque de petróleo, después del envejecimiento
El F1 presentó una disminución apreciable de la reología (40,19%), pero distante del valor establecido, lo que conllevó a deducir que la concentración de coque de petróleo no fue suficiente para lograr el porcentaje de reducción requerido. En el F3 pese a que hay disminución de la reología, ésta es menor en comparación a la obtenida en los fluidos 1 y 2, se asume nuevamente que el motivo de ello es que se está acercando al punto de saturación, lo que le resta propiedades de dispersante, situación corroborada con el análisis del F4, en el que la dispersión es casi imperceptible debido a la gran cantidad de sólidos presentes.
Con respecto a los geles (Figura 6), en el caso de los fluidos formulados utilizando el coque como dispersante, se muestra que los fluidos 1 y 2, son los que obtuvieron menores valores de esfuerzo de gel a 10 s manteniéndose en el rango de 3-5 lb/100pie2. En el caso del F1 (menor concentración de coque) se obtuvieron valores entre 4-6 lb/100pie2. Para el F4, donde la concentración de sólidos es mayor, el esfuerzo de gel a los 10s está en el rango de 5-6 lb/100pie2.
De acuerdo a Lummus [18], a nivel de la industria petrolera siempre se busca que los fluidos de perforación no presenten esfuerzos de geles a 10s y 10 min bajos debido a que esto se traduce en una tixotropía poco eficiente, así como tampoco es conveniente una similitud entre los valores obtenidos. Conforme a los valores obtenidos, se considera que en el caso del fluido blanco el tipo de gel formado es invariable, debido a que existe similitud, pero además los valores obtenidos son altos en ambos casos. Para los fluidos 1, 2 y 3 se obtuvieron geles favorables debido a que se tienen valores bajos a los 10 s que van incrementándose progresivamente a casi el doble a los 10 min. En el F4 por otra parte, el gel se puede catalogar como progresivo por tener valores intermedios a los 10s e incrementarse rápidamente a los 10 min.
El estudio del filtrado API permite conocer la pérdida de fluido a través de la membrana permeable conocida como revoque, cuando el fluido de perforación es sometido a una presión diferencial [19],. Según los datos obtenidos se percibe en la Figura 8, que al agregar coque tabde petróleo aumenta el volumen de filtrado API, quizás pueda atribuirse a que se incrementa la dispersión que impida el paso de la fase continua del fluido a través del revoque, pero cabe destacar que el fluido no cuenta con un agente controlador de filtrado en la formulación (Tabla 2).
En todos los sistemas estudiados el valor de filtrado API se encuentran por debajo del máximo valor aceptable a nivel de laboratorio (15 cm3/30min) [13], incluso para el caso del F2 que muestra el mayor valor de filtrado API en comparación con los demás fluidos formulados. Sin embargo, en futuras formulaciones deberá aplicarse un controlador de filtrado que permita reducir la filtración por lo menos en un 30% con respecto al obtenido en el fluido blanco.
Procediendo con la metodología aplicada, se formuló un fluido base agua tipo lignosulfonato agregando un dispersante comercial en la concentración establecida por la Empresa Samán Tecnología Integral en Petróleo [13] (Tabla 2). Con respecto al estudio estadístico y específicamente a las densidades obtenidas (Figura 8), se observa que existen diferencias estadísticamente significativas entre los fluidos al ser estudiados como grupo (pobtenido < pvalor).
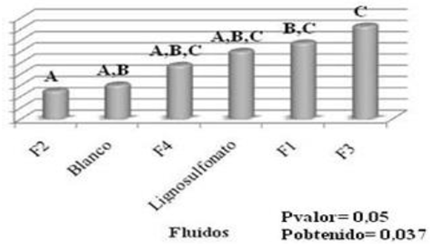
Fig. 8: Análisis de varianza no paramétrica de la densidad de los sistemas base agua tipo lignosulfonatos. (Letras distintas expresan diferencia estadística significativa)
También se detalla, que los fluidos F2, blanco, F4 y el fluido formulado con un dispersante comercial (Lignosulfonato), no presentaron diferencias estadísticamente significativas entre ellos (letras iguales). De igual forma se muestra que los fluidos F1 y F3, pese a no relacionarse con los demás fluidos formulados con coque de petróleo no presentaron diferencia significativa al compararse con el fluido formulado con el dispersante comercial (Letra C). Permitiendo considerar a los sistemas formulados con coque de petróleo como sistemas favorables.
Al analizar la propiedad de viscosidad plástica (Figura 9), se precisa que existen diferencias significativas entre los fluidos en estudio, sin embargo, el F2 y el formulado con lignosulfonato no presentan diferencia significativa entre ellos. Entre los fluidos 2, 3 y 4 sí existen diferencias significativas, lo que demuestra que al variar las concentraciones de coque de petróleo afecta la viscosidad plástica, igualmente en los resultados se aprecia, como a medida que se incrementa la adición de coque de petróleo se alejan en mayor medida a los obtenidos con el Lignosulfonato (dispersante comercial), demostrándose que el coque de petróleo deja de ser eficiente cuando se supera la adición del mismo en 2 g.

Fig. 9: Análisis de varianza no paramétrica de la viscosidad plástica de los sistemas base agua tipo lignosulfonatos (Letras distintas expresan diferencia estadística significativa).
Efectos similares también se obtienen al estudiar el punto cedente (Figura 10), donde igualmente existen diferencias significativas entre los fluidos en estudio. Pero individualmente, no existen diferencias entre los fluidos 1, 2 y el formulado con dispersante comercial, reafirmando que el coque de petróleo puede ser utilizado preferiblemente hasta un máximo de concentración de 2 g, porque permite obtener resultados similares a los que se tienen con un dispersante comercial.
Asimismo, en el caso del fluido 4 en el cual se presume existe una saturación de sólidos en la fase dispersa que se traduce en una floculación del fluido, y una disminución del valor de la propiedad, conllevando a que no existe diferencia significativa entre él y el fluido blanco.
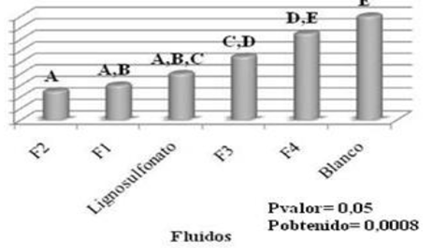
Fig. 10: Análisis de varianza no paramétrica del punto cedente de los sistemas base agua tipo lignosulfonatos. (Letras distintas expresan diferencia estadística significativa).
Concerniente al volumen de filtrado API (Figura 11), existe la mayor diferencia significativa entre los fluidos en estudio, así se obtuvo la mayor diferencia entre el P obtenido y el Pvalor (pobtenido < pvalor). Además, todos los fluidos al estudiarse individualmente y compararse entre ellos muestran letras distintas.
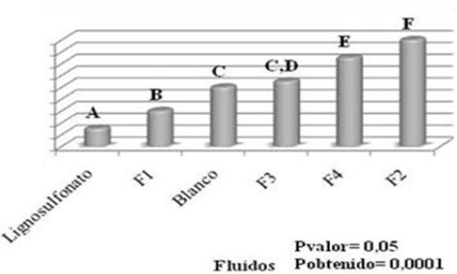
Fig. 11: Análisis de varianza no paramétrica del filtrado de los sistemas base agua tipo lignosulfonatos. (Letras distintas expresan diferencia estadística significativa).
La razón a este comportamiento, como se explicó anteriormente, se debe a que la formulación utilizada no contiene controlador de filtrado, por ende, no logra formar una membrana delgada y no permeable que reduzca filtración. Esta propiedad es de suma importancia porque permite evitar la pérdida de circulación cuando se trabaja en campo, lo que conlleva a no contaminar la formación o generar fracturas que afecten la actividad de perforación [19].
Finalmente, al estudiar el porcentaje (%) de reducción de reología obtenido (Figura 12), existen nuevamente diferencias significativas al ser estudiado y otra vez F2 no difiere del fluido comercial, reflejando ser la mejor concentración de coque a adicionar.
En el caso de los fluidos 1, 3 y 4 las medias sí poseen valores significativamente diferentes a los obtenidos con el dispersante comercial (Lignosulfonato) por lo que la utilización del coque de petróleo en esas concentraciones se considera desfavorable e ineficiente para la dispersión del fluido y mejoramiento de reología, según el criterio aplicado.

Fig. 12: Análisis de varianza no paramétrica del porcentaje (%) de reducción de reología de los sistemas base agua tipo lignosulfonatos. (Letras distintas expresan diferencia estadística significativa).
De acuerdo a lo planteado en la investigación y a los resultados obtenidos, principalmente se buscaba evaluar si el coque de petróleo lograba aportar aniones que permitieran la ruptura de los enlaces generados y de esta manera evitar la floculación de moléculas que representaban una restricción al flujo. De acuerdo a esto se infiere que con el coque de petróleo ocurre algo similar, donde al someterse a temperaturas entre 50- 56°C (120°F - 150°F) la parte polar del coque de petróleo integrada por sus grupos funcionales reaccionan con el agua en un medio alcalino y se inicia entonces la dispersión del coque de petróleo en el fluido de perforación, donde las partículas comienzan a repelerse y disiparse en el fluido evitando la floculación del mismo.
De manera general se puede afirmar que el coque de petróleo sí posee características de dispersante, que permiten una disminución de la floculación de partículas en la fase dispersa, evitando así la resistencia al flujo por las fuerzas de atracción electroquímicas de las partículas. La condición de dispersante de un aditivo cualquiera en un fluido de perforación se estudia basándose principalmente en la disminución de los valores de viscosidad plástica y punto cedente obtenidos con la adición del determinado producto.
Para el caso específico de estudio de coque de petróleo, se observó que los valores obtenidos mostraron una dispersión de las partículas de 47,76% cercano al 50% que fue el criterio asumido por los autores, pero a pesar de no ser iguales los valores, estadísticamente el fluido 2 (F2) no presentó diferencias significativas con respecto al fluido comercial en las propiedades de viscosidad plástica y punto cedente. Asimismo, el valor obtenido es superior a la reducción entre 25-27% de las propiedades obtenidas con el uso de ZRC (Citrato de circonio) [6].
El criterio asumido establecido puede considerarse excesivo, pero no existe un criterio normado para ello en la industria para decir si un lignosulfonato es aceptado o rechazado para ser empleado para reducir la reología. Los mismos pueden ser de tipo cualitativo, como el decir que pase de floculado a disperso [9] o como el de colocar un porcentaje de reducción [13]. Asimismo, a nivel de campo las exigencias conllevan a aceptar valores por debajo de lo establecido, por lo que, los resultados obtenidos de las propiedades en estudio debido al uso del coque de petróleo como agente dispersante se consideran aceptables.
Conclusiones
El coque de petróleo del Complejo Petroquímico General de División José Antonio Anzoátegui se considera como un agente dispersante en fluidos de perforación base agua tipo lignosulfonatos.
La acción dispersante del coque de petróleo solo es activada cuando el fluido es sometido a temperaturas entre 120 - 150 °F.
La concentración adecuada para la utilización de coque de petróleo como agente dispersante a nivel de laboratorio es de 2 g (lb/bl).
Entre el coque de petróleo y el dispersante comercial (lignosulfonato) no existen diferencias significativas en cuanto al porcentaje de reducción de reología a una concentración de 2g (lb/bl)