1. Introducción
El artículo “Parametrización del controlador de flujo para disminuir el consumo del desinfectante para el lavado de garrafones” consiste en la demostración del uso de tecnología orientada a procesos industriales implementado en el sistema de lavado; en nuestra localidad se realiza de forma manual descifrando que la problemática radica en el uso innecesario del desinfectante, aplicar este proceso se obtendrá mejora en su resultado final [1].
Las empresas de producción de aguas envasadas endonde su operación es de forma manual reflejan desperdicio de material en sus procesos, es el caso del lavado de los garrafones, no determinan la cantidad exacta del desinfectante y esto se debe a que no cuentan con un sistema de control de flujo, aplicar este método mejoraría el tiempo de proceso ya que aumentaría la cantidad de elementos lavados evitando gastos innecesarios a la empresa, cabe recalcar que este método de limpieza se direcciona a garrafones que no presenten un alto grado de impureza como lo es el aceite o algún tipo de insecto muerto. [1]
Para la obtención de los parámetros referentes al controlador de flujo se determinará la identificación del sistema del proceso de lavado, de la cual se obtendrá la ecuación denominada función de transferencia que es la que permitirá realizar el análisis mediante el uso de aplicaciones en la plataforma Matlab® en donde se obtendrá los valores analíticos que corresponderán al controlador y que se determinará mediante pruebas experimentales si son los correctos o se deberá calibrar dichos valores. [1]
El diseño de la estructura es un cuadrante en el plano xyz en donde en el eje y corresponde a la altura de un metro, mientras que en el eje x es de 75 centímetros de ancho, el eje z es de 35 centímetros, elaborados con tubos estructurales en donde serán ubicados los soportes para los garrafones (figura 1). [1]
Los soportes para los garrafones fueron diseñados en el programa FreeCAD (figura 2), facilitando la apreciación del real de lo que se desea obtener, para luego enlazar comunicación con el equipo de impresión 3D y cuyo tiempo de duración fue de 9h35 minutos para cada soporte (figura 3).[1]
A continuación, se detalla todo el requerido para obtener la mejora para el suministro de desinfectante.
2. Comunicación entre el variador VFD-EL y el PLC para la adquisición de valores en el proceso de lavado
El arranque del motor depende de las sentencias dadas por la programación en el software TIA Portal, este se comunicará con el variador VFD-EL suministrando la frecuencia necesaria para la rotación del motor.
El enlace se realiza mediante el protocolo de comunicación MODBUS para lo cual se utilizó el módulo CM 1241 RS422/485 conectado directamente con el variador VFD-EL manipulando la velocidad de giro del motor a frecuencias determinadas [3].
De esta forma se logra comandar desde el PLC hasta la bomba por medio del variador de velocidad.
Figura 4. Comunicación MODBUS. [1]
3. Parámetros del variador VFD-EL para la adquisición de datos.
El variador VFD-EL presenta una configuración que depende del uso que se valla a realizar, a continuación, se enlista los parámetros que se utilizaron para el correcto funcionamiento en este proyecto [2].
4. Programación para la adquisición de datos del variador y sensor de flujo del desinfectante.
Se establecen bloques de comunicación, el bloque principal denominado "MB_COMM_LOAD_DB" y el bloque MB_MASTER_DB ambos segmentos contienen diferentes parámetros utilizados en la programación para realizar funciones específicas. Los parámetros utilizados en este bloque están reflejados en la tabla 2 [4 ].
Una vez activado el variador y la bomba se da paso a la lectura de datos y creación del registro, como antes se mencionó el sensor proporciona valores analógicos, la manera correcta de procesar estos valores es llevarlo a un rango medible, es decir, normalizarlos y escalarlos, que consiste convertir valores mediante una estructura lógica para la obtención de datos reales. [5]
Segmento NORM_X (figura 8) delimita el rango de la señal analógica detectada por el sensor de flujo y el segmento SCALE_X (figura 9) asigna el valor detectado en cantidades de litros que fluye en determinado tiempo [5].
Estos valores son extraídos mediante la configuración de un bloque denominado base de dato esto enlaza los datos obtenidos a la plataforma del dispositivo de control como lo es el PLC [5]
El segmento representado en la
determina la creación del archivo de extracción de datos enlazada con el bloque de escritura "DataLogWrite_DB" por lo que debe enclavarse al momento de ejecutarse.
Los valores leídos por el sistema deberán ubicarse en los filtros correspondientes creados en la base de datos, las variables del proyecto son el flujo y la frecuencia que es donde reflejarán esta información, mostrados en la figura 13.
5. Obtención de la función de transferencia del proceso de lavado en Matlab.
Obtenido el registro de la medición del sensor de flujo se procede a reflejar estos valores mediante un plot los valores en donde indican que cada dato fue de 0.1 segundo de un total de 700 datos en un lapso de 70 segundos, cantidad suficiente para la aplicación de procesos en Matlab® [6].
El análisis inicia mediante el uso de la herramienta System identification que permite importar los valores obtenidos de la medición del sensor correspondiente a la frecuencia y el flujo, variables que deben especificarse en la función de transferencia, determinando cual es la entrada y salida del sistema [6].
El proceso continuo hace referencia a la estimación de valores para la obtención de la función de transferencia determinando parámetros de polos y ceros que refleja un acercamiento a la función principal encontrada, se recomienda realizar varias estimaciones con el fin de establecer la mejor función de transferencia [6]. Cada estimación estaba representada por un porcentaje de acercamiento a la función deseada, el modelo escogido tuvo un acercamiento del 93.58% de igualdad formada por un polo y un cero, determinados de la siguiente manera [6].
6. Parametrización del controladorPID en MATLAB
Tabla 3. Parámetros del controlador en Simulink.
En este apartado obtendremos los parámetros para el controlador PID en Matlab, esto nos indicará los valores analíticos del sistema para ser implementados en el proyecto, la aplicación a utilizar fue diseñada en Simulink realizado por un segmento retroalimentado estructurado por bloques, en donde consta el PID Controller seguido por la función de transferencia y presentando en un scope el comportamiento de la función controlada, este proceso determinará los parámetros proporcional- integral- derivativo [7].
Realizado el diseño en simulink con los parámetros ya establecidos un scope mostrará la respuesta al sistema y su tiempo de estabilidad, siendo esta la apreciación de lo que se desea proyectar en el proyecto de lavado [7].
7. Parametrización del controladorPID en TIA Portal.
Con los parámetros obtenidos del diseño del controlador de forma analítica procedemos a elaborar la programación con estos datos y verificar la respuesta en tiempo real.
Los parámetros resultantes del proceso analítico no fueron los mejores, por lo que se procedió a realizar calibraciones en los diferentes parámetros para obtener el proceso deseado [8].
La respuesta del sistema presenta una mejor resolución para el proceso de lavado disminuyendo el tiempo de estabilidad.
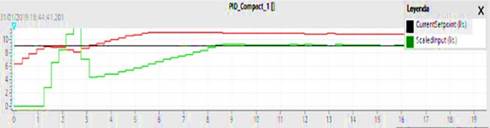
Figura 19 Repuesta en tiempo real con los parámetros visualizados en TIA Portal (Verde: Señal de entrada) [8].
8. Diseño del proyecto en HMI
Para el monitoreo del sistema en tiempo real, se diseñó una interfaz gráfica que represente la ejecución del proceso presentando los valores correspondientes al flujo determinado estabilizado, la frecuencia de operación, y el tiempo de ejecución. La pantalla muestra el arranque del proceso, así como también el pare de marcha en caso de emergencia.
9. Pruebas realizadas para estimar la función de transferencia
Se realizó siete diferentes estimaciones para identificar a la función de transferencia ideal determinada por el porcentaje de acercamiento, escogiéndose la función con polos y ceros con el porcentaje de 93.58 la más cercana.
Se puede visualizar qué tipo de función de transferencia se escogió, y cómo está determinada, en la figura 22.
10. Demostración del consumo del desinfectante.
Al establecer los parámetros del Setpoint se realizó la prueba de lavado, para determinar el tiempo ideal y considerar como limpio o sin impurezas al botellón, en las cuales el consumo del desinfectante se refleja en un cuadro comparativo entre el proceso realizado manualmente y el proceso usando con el controlador, como se observa en la tabla 5.
En la primera prueba experimental tomada en un minuto, se determinó que el proceso de lavado realizado en este tiempo sin el uso de controlador consumió diez litros y medio, observando que el desinfectante nocubrió en toda la superficie del botellón y en cambio seaplicó el proceso con controlador la medición del desinfectante, donde se utilizó 9 litros, de tal forma que se obtuvo el mismo resultado en la segunda y tercera prueba.
El tiempo que se estableció como ideal para el proyecto fue de un minuto treinta segundos, cabe recalcar que este tiempo es el que se utiliza en las empresas locales existentes y fue comprobado en la visita técnica. De igual manera se demuestra que el controlador regula el uso del desinfectante, ya que las muestras en que se tomaron donde el proceso es de forma manual, demostraron desperdicio del elemento principal de limpieza y al utilizar el equipo con el controlador implementado disminuyendo el flujo de desinfectante, reduciendo el desperdicio tanto de agua como de desinfectante.
11. Resultados.
De los valores presentados en la lectura de datos que representan el flujo de salida con respecto a la entrada, se ha determinado que su caudal es de 9.5 a 10 litros por minutos, esto se pudo reconocer realizando la prueba, en donde el porcentaje de error es presentando el 1.1% [1]
A pesar de que las respuestas obtenidas en las estimaciones para la función de transferencia presentaron gran acercamiento, se pude apreciar en la gráfica (figura 22) donde sus componentes necesarios para la función de transferencia son un polo y un cero, la tabla comparativa muestra los valores y el modelo que mayor aproximación tendría, de las estimaciones la que mayor porcentaje de acercamiento representó el modelo con el 93.58% la más cercana a la función establecida, permitiendo apreciar que por solo el 6.42% no se determina como ideal, pero si la recomendada para elaborar el diseño del controlador PID. [1]
El diseño del controlador PID presentó dos respuestas, los parámetros encontrados mediante la simulación por medio de Simulink y el diseño realizado en la programación de TIA Portal, determinando que el diseño obtenido mediante programa fue la mejor opción ya que la respuesta en tiempo real se estabiliza en los dos segundos (figura 20), en donde los parámetros identificado para el controlador son; Kp:0.9520075, ki: 0.4228511; kd: 0.051909, a diferencia de los valores encontrados por la simulación dando: kp: 09, ki: 5.9, kd: 0.01y presenta un pico de 1.3, por lo que el diseño elegido fue el controlador PID con parámetros del programa.[1]
El proceso ejecutado en la pantalla HMI, demostró ser de gran ayuda, presentando los procesos para control de forma digital, el diseño presenta condición de inicio y pare de manera que empieza el proceso siempre que tenga desinfectante, esta información será proporcionada del proceso de mezcla, así como también el botón de pare que detiene el proceso en cualquier instancia.[1]
12. Conclusiones
El proceso de identificación de sistema para este proyecto determinó, que la planta compuesta por un polo y un cero demuestra mayor proximidad dando un 93.58% considerada la óptima del sistema.
El flujo empleado para el proceso de lavado dependió de la regulación realizada al chorro, determinando que la cantidad de desinfectante que pasa por el sensor es de 9.8 a 10 litros por minuto.
El control PID diseñado para la planta presenta un consumo de 13 litros y medio en comparación al proceso de lavado manual que consume 15 litros, obteniendo un ahorro de litro y medio en 1 minuto con 30 segundos, demostrando que el proceso aplicando control disminuye el desperdicio del desinfectante.
El diseño implementado en HMI para el proceso de lavado de botellones representa un excelente método de control y monitoreo, permitiendo apreciar el correcto funcionamiento, así como también las interrupciones que puedan presentarse y tomar correcciones oportunas.