Forma sugerida de citación:
Villa, Y.; Vook, T.; Villa, J. L.; Carbajal, P.; Barrera, L. y Florez, M. “Análisis estructural y modal de las placas adaptación para martillos hidráulicos y minicargadores en condiciones reales de operación,” Ingenius, Revista de Ciencia y Tecnología, N.◦ 28, pp. 92-99, 2022. doi: https://doi.org/10.17163/ings.n28.2022.09
1. Introducción
En Sudamérica es común construir carreteras sin redes de servicio instaladas porque los proyectos de servicios ejecutados están limitados por el capital de inversión. La necesidad de mejorar la calidad de vida y de expandir los servicios para residentes abrió un mercado enorme para productos de demolición tales como martillos hidráulicos [1].
Proyectos tales como instalaciones de tuberías de gas requieren la construcción de zanjas, que comienzan con el corte de superficies duras de pavimento de concreto o asfalto para crear aberturas de 20 cm de ancho, en promedio. Para demolición se emplean los martillos hidráulicos montados en un cargador compacto, los cuales también pueden ser usados para limpiar el material de desecho removido y para restauración [2].
En Perú se utilizaron un cargador compacto Case SR220 y un martillo hidráulico SB202 en proyectos de construcción para masificación de gas natural. El martillo tiene características especiales como una estructura sólida del cuerpo, una válvula de recarga de grasa localizada en la parte superior del cuerpo, y la sección más angosta de la caja de 17 cm de ancho, lo cual reduce la energía invertida para varios kilómetros de instalación de tubería de gas [3].
Al mismo tiempo, la demanda de nuevos operadores y contratistas para instalar tuberías de gas estimuló la demanda de sistemas de cargador compacto-placa de adaptación-martillo hidráulico. Debido a las estrategias de mercado de los proveedores, se perdió el énfasis en la importancia de la placa de adaptación y su impacto potencial en el desempeño y tiempo útil de los martillos hidráulicos. La demanda de entrenamiento, nuevas estrategias y diferentes propuestas de solución se incrementó cuando la tasa de reclamos aumentó de 5 % a 35 %, particularmente para daños irreparables en los martillos hidráulicos [4].
Soluciones Barrera EIRL, un importante fabricante local de placas de adaptación, con una participación de 60 % de productos Atlas Copco SB202 y Case SR202 en el mercado cerrado, realizó una investigación independiente usando análisis virtual avanzado. Esta compañía es una de las más innovadoras en el mercado peruano.
Luego de evaluar la naturaleza y la recurrencia de la falla, se detectó una relación entre las pobres habilidades de operación, la resistencia extrema y dureza de la placa de adaptación, y la presencia de otros fabricantes de placas de adaptación, sin adherirse a estándares de ingeniería. De manera similar, el énfasis no estaba en la evaluación y el control de los efectos dañinos [5].
Como resultado, se estableció el objetivo de construir la placa de adaptación como un fusible en el sistema. Se utilizó simulación virtual estática y dinámica para diseñar una nueva placa de adaptación con Inventor Professional. Posteriormente, el análisis Ansys confirmó el comportamiento. Para complementar el registro de desempeño y reclamos, se hizo un grupo de placas de adaptación para mejorar el proceso de construcción y la calidad del producto y, finalmente, reducir el costo.
2. Materiales y métodos
2.1. Panorama general
En 2004, el proyecto de Gas Camisea, que costó 3,9 billones de dólares (USD), comenzó un proceso de masificación de gas en Perú. Debido a la intensidad de esta actividad, se estableció un método para instalar tuberías en el suelo a una profundidad de 30 cm. Esta profundidad creó la recomendación técnica de construir zanjas con una profundidad de 70 cm. Parte del trabajo fue realizado en calles pavimentadas con concreto o asfalto, y por esa razón fue necesario demoler la dura superficie de las carreteras, haciendo previamente cortes de 20 cm de ancho [6, 7] (Figura 1).
Ventas de referencia históricas de 2014 de un grupo de quinces sistemas de cargador compacto, placa de adaptación y martillo hidráulico presentó un número alto de reclamos por garantía debido a fallas en el cuerpo sólido de los martillos hidráulicos. Después de una evaluación exhaustiva utilizando un líquido penetrante, se detectó la formación de grietas en los martillos hidráulicos.
Se realizó una investigación para entender el origen de la falla, que estuvo relacionada con la sobrecarga en el martillo. Una posible explicación fue extrapolada debido a otras fallas en puntos de corte, bujes y pistones. Al mismo tiempo, cuatro cargadores compactos mostraron la formación inicial de microgrietas en sus brazos. En consecuencia, se estableció una hipótesis considerando el sistema cargador compacto – placa de adaptación – martillo hidráulico como una sola unidad donde la vibración y la resonancia durante el proceso de demolición viajaron a través del sistema y produjo grietas en la parte menos resistente del sistema. Como una segunda parte del método, se estableció un nuevo prototipo considerando la placa de adaptación como un fusible, lo cual se explica en esta investigación [9].
2.2. Cargadores compactos, una máquina multipropósito
Los cargadores compactos se usan en diferentes industrias como un transportador compacto multipropósito para la construcción, manejo de vehículos de materiales y equipo agrícola [10]. En combinación con martillos hidráulicos pueden implantarse algunos métodos de demolición, usando como recomendación la especificación de tasa de flujo hidráulico, presión estática, y la resistencia del martillo al peso detallada como una referencia [11].
Adicionalmente, la decisión del tamaño del cucharón estaba relacionado con la densidad del material manipulado; en este caso, concreto viejo o asfalto, con un espesor de 5-20 cm y suelo compactado, se levantaron como material de desecho desde la superficie hacia camiones. En esta experiencia, el modelo Case SR220 se montó con cucharones de trabajo pesado de 240 kg con una capacidad de 0,44 m3, reportados por los clientes y respaldado por el catálogo [12].
2.3. Selección del martillo hidráulico de acuerdo con la condición de operación
Las condiciones de borde fueron el ancho mínimo de la zanja, la profundidad de 70 cm y, dado que las operaciones se realizaban dentro de la zanja, la boquilla de lubricación del martillo ubicada por diseño en la parte superior del mismo. Bajo condiciones exigentes se utilizó un martillo con mayor resistencia a sobrecargas y construido con un mínimo número de partes internas. Por esa razón, se seleccionó un cargador compacto Case SR220 equivalente al modelo Caterpillar 236B, con un interruptor hidráulico Atlas Copco SB202 de cuerpo sólido [13] (Figura 2).
2.4. Impacto sobre el cargador compacto y la durabilidad del interruptor hidráulico
Un buen mantenimiento y un diseño adecuado de la placa de adaptación para el martillo hidráulico permite obtener el máximo resultado. Se realizaron pruebas diagnósticas para detectar fallas menores con el fin de arreglarlas, lo cual es una parte importante de un programa de mantenimiento preventivo. Los contratistas reportaron una disponibilidad operativa entre 61 % y 81 % luego que se aplicó un plan estratégico para mejorarla [14].
La configuración estándar fue el uso del SB202 debido a sus características especiales, su diseño patentado, resistencia a sobrecargas y ubicación más alta de la válvula de lubricación. No se midió la confiabilidad del martillo, pero contratistas reportaron que era mayor que la de otros productos.
2.5. Condiciones reales de operación
Li et al. [16] reportaron la formación de grietas como resultado del uso del martillo hidráulico empleando Ansys Workbench, que mostró el comportamiento en la estructura del brazo en un sistema articulado cuando se emplea un martillo hidráulico. Los parámetros fundamentales acerca del impacto potencial y la formación de grietas fueron tomados de forma referencial de las operaciones reales registradas. La hipótesis fue probar la placa de adaptación como un fusible para proteger la integridad del martillo y del cargador compacto, considerando la condición de máxima sobrecarga cuando los operadores utilizan presión hidráulica excesiva con el brazo-martillo sobre la superficie para demolición, y en un ángulo de operación no-alineado de 90° (entre el martillo y la superficie). Esta puede ser considerada la condición de operación más extrema y, por esa razón, se abrió una línea de investigación para optimizar la placa de adaptación (Figura 3).
2.6. Fabricación de la placa de adaptación
Se tomaron mediciones físicas del martillo hidráulico Atlas Copco SB202 y de la región superior de montaje del brazo, considerando las mediciones tridimensionales para conectar ambas máquinas, y posteriormente se hizo un dibujo tridimensional utilizando el software Inventor Professional and Ansys para analizar el comportamiento estructural estático y dinámico bajo una frecuencia de impacto máxima de 1800 golpes por minuto (BPM, Blows per Minute, por sus siglas en inglés). Para el análisis, la placa de adaptación se hizo independiente del sistema del brazo del cargador compacto y el martillo hidráulico. Se aplicaron condiciones de borde tales como la gravedad, el peso de 16 750 N aplicado a la placa de adaptación y la fuerza hidráulica en regiones de contacto con el martillo y cargador compacto.
2.7. Criterios para el rediseño de la placa de adaptación
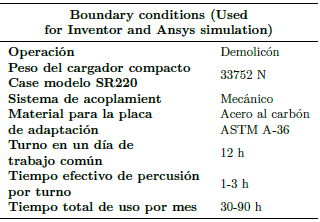
Tabla 1. Condiciones operacionales de borde para el sistema cargador compacto-placa de adaptación-martillo hidráulico
El rediseño de la placa de adaptación fue hecho considerando un material suave en la primera etapa de análisis, y siguiendo los resultados de los primeros seis meses, ellas fueron rediseñadas con un refuerzo que aumentó la vida útil a más de un año de operación estándar. El sistema cargador compacto-placa de adaptación-martillo hidráulico fue usado para la demolición de la cubierta fuerte de la carretera (asfalto viejo, concreto) y para romper la estructura compactada del suelo (Tabla 1).
3. Resultados y discusión
3.1. Análisis estático
Se realizó un análisis estático con carga utilizando Autodesk 2020 Inventor Professional, considerando que el peso del cargador compacto con accesorios es de 33 752 N (Tabla 1); como resultado de la operación observada, se consideró un peso de 16 750 N (Figura 2). Debido a las dos regiones de contacto entre el brazo y la placa de adaptación, se aplicó una fuerza de 8375 N a cada área de contacto y se aplicó una fuerza de 16 750 N a la superficie de contacto entre la placa de adaptación y el martillo hidráulico (Figura 4).
Para el análisis de mallado en Autodesk Inventor 2020 (Figura 5), el tamaño promedio de elemento utilizado fue 0,05, el mínimo tamaño de elemento fue 0.1, el factor de calibración 1.5 y el máximo ángulo de giro 30 grados. Geométricamente, la placa de adaptación fue diseñada considerando formas planas, reduciendo la presencia de curvaturas. La Tabla 2 detalla recomendaciones de referencia.
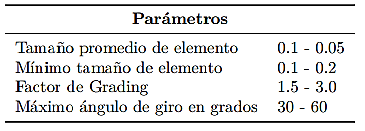
Tabla 2. Autodesk Inventor 2020: Recomendaciones para establecer los parámetros de malla y de control
Para el análisis estático, el límite elástico de tracción del acero al carbono ASTM A36 (Tabla 3) utilizado es 250 MPa, con módulo de Young = 199,959 GPa, y coeficiente de Poisson = 0,3. (Figura 6). Suponiendo un máximo esfuerzo de Von Mises de 31,33 MPa (Figura 6) y un límite de deformación de 0,25 mm, se obtuvo un máximo resultado de desplazamiento de 0,09856 mm (Figura 7).
El esfuerzo máximo de tracción de 11,58 MPa (Figura 8) está por debajo de la condición de Von-Mises (32,38 MPa) (Figura 7), porque el esfuerzo fue distribuido a lo largo de la estructura completa. El esfuerzo máximo de compresión fue 3,32 MPa (Figura 9), que fue observado en las interfaces de la estructura de soporte entre la placa base del martillo y la placa base del cargador compacto. El máximo esfuerzo de compresión del acero al carbono ASTM A36 usado es 152 MPa [18]. El mínimo factor de seguridad fue 7,92 (Figura 7), lo cual significa que se alcanza un alto factor de seguridad con este diseño [19] (Table 4).
3.2. Análisis modal
La frecuencia de impacto al utilizar un SB202 estuvo en un rango de 850-1800 BPM (máx. 30 Hz). La máxima deformación total fue 3.0405 × 10−6 mm en la región de contacto entre la placa de adaptación y el martillo y 0,098 mm en la región central de las áreas de la placa de adaptación (Figura 7).
Se realizó una disminución de esfuerzo para hacer un análisis armónico en Ansys Modal y Harmonic Response. Como un primer análisis, es usual evaluar donde ocurrieron las relajaciones de esfuerzo y la eliminación del pretensado en la placa de adaptación. El esfuerzo estático fue 11,58 MPa (Tabla 4) en la etapa inicial. Cuando se inicia la acción dinámica, esta situación se relaja primero. El análisis de esfuerzo dinámico fue utilizado para compensar la compresión estática y para llevar a cero el efecto estático con el fin de revertir la resistencia desarrollada dentro del material.
El esfuerzo dinámico excluyendo el pretensado fue 12,37 MPa (Figura 11) y el esfuerzo dinámico total fue 23,95 MPa (Tabla 4). Los valores de las diferencias porcentuales entre los resultados estáticos y dinámicos del esfuerzo máximo principal y esfuerzo mínimo principal son 48,34 % y 42,19 %, respectivamente, los cuales son menores de 50 % (Figura 12).
3.3. Análisis de fatiga
La Tabla 5 muestra el análisis de vida de la fatiga resultante reportado por Ansys; se tuvieron 1.00×108 ciclos hasta la falla estructural (Figura 13). Por esa razón, considerando el desempeño operacional del martillo hidráulico de 600 y 1800 BPM y correlacionando con las horas operacionales por día, resulta en un rango de 308,64 a 925,93 días de operación antes de la falla.
De forma similar, el factor de seguridad resultante del análisis de fatiga reportó un número mínimo de 4,3599 (Figura 14), es cual es mayor que 1; por tanto, este diseño puede considerarse confiable.
Debido al máximo esfuerzo de 31,33 Mpa (Figura 6) con un factor de seguridad de 7,92 (Figura 10), esto sostiene hasta 1.00 × 108 ciclos (Figura 13) antes de la falla estructural. Este desempeño respalda el objetivo de este diseño de alcanzar la máxima durabilidad mientras actúa también como un fusible que protege la estructura del martillo y del cargador compacto en caso de que ocurra una sobrecarga. La carga de esfuerzo reportada todavía está por debajo del límite de resistencia, debido a que a pesar de los 1.00 × 108 ciclos antes de la fatiga, el factor de seguridad está por encima de 1, lo cual significa que se tiene espacio para una optimización futura.
3.4. Proceso de construcción y soldadura
La placa de adaptación se construyó con acero al carbono ASTM-A36, soldadura 6011 y 7018 con tamaño 5/32”, y para el producto final se utilizó una pintura electrostática RAL9005, y cada producto final fue registrado con un número de registro progresivo para el control de calidad del producto y la gestión de calidad (Figura 15).
3.5. Producto estándar para el mercado
Como estrategia comercial, el proveedor ofreció seis meses de garantía estándar e incluyó una optimización actualizada constantemente con alta confiabilidad para usuarios finales, empleando nuevas placas de adaptación como respaldo en caso de problemas de calidad por la presencia de grietas en la estructura (Tabla 2).
Después de catorce meses de uso, un grupo de diez placas de adaptación construidos simultáneamente fueron evaluados físicamente junto con sus reclamos de garantía. Los resultados confirmaron un desgaste normal durante la operación y la presencia de grietas después del período de garantía de doce meses (Tabla 6). Al mismo tiempo, no se observaron grietas en la estructura sólida del martillo o del cargador compacto, y se desarrollaron animaciones y videos de entrenamiento complementarios para explicar el efecto para los consumidores de la operación inapropiada [15]. El entrenamiento y la operación apropiada contribuyeron a reducir el daño de los martillos hidráulicos.
Finalmente, este producto ha sido una solución probada desde 2015 hasta el presente para el sistema cargador compacto-martillo, para aplicaciones de demolición en el mercado peruano; sin embargo, su precio representa un 20 % del precio de adquisición, y por esa razón es recomendable comenzar una investigación de optimización para reducir los costos de producción. Esta placa de adaptación fue estandarizada para ser usada por la mayoría de las marcas que trabajan con martillos Atlas Copco y cuya producción en serie sobrepase las quinientas unidades con un desempeño confiable hasta el presente, de manera de tener, como resultado, menor cantidad de reclamos por garantía y efectos colaterales sobre martillos hidráulicos.
4. Conclusiones
El esfuerzo aplicado a lo largo del sistema (cargador compacto-placa de adaptación-martillo hidráulico) durante la demolición de capas superiores, pavimento y asfalto de carreteras, fue identificado como la principal preocupación de este estudio y el estilo de operación. Por esa razón, como parte del desarrollo de un producto optimizado, se realizaron videos de entrenamiento para mejorar las aptitudes operacionales.
Como complemento se estableció una estrategia de reclamo de garantía para restablecer la confianza en los productos, y se designó un proveedor exclusivo incluyendo una respuesta de garantía confiable, lo cual contribuyó a reintroducir el producto reduciendo los reclamos de garantías por fallas en martillos hidráulicos un 99 % durante los doce meses siguientes.
Existe espacio para un proceso de optimización, porque el factor de seguridad obtenido es mayor a 7,95 y la diferencia porcentual entre los resultados estáticos y dinámicos fue menor al 50 %, y en la industria, se utiliza una referencia del 20 % para obtener resistencia máxima. Sin embargo, los picos de esfuerzo no exceden el límite elástico de tracción del acero al carbono ASTM A36 que es 250 MPa, ni el máximo esfuerzo de compresión de dicho acero que es 152 MPa. La estrategia confirmó el uso de la placa de adaptación como un elemento para proteger el martillo y el cargador compacto de la deformación.
Se demostró que la placa de adaptación actúa como un fusible protector del martillo y del brazo del cargador compacto, confirmando la hipótesis de este trabajo. Se recomienda la innovación continua para mejorar la confiabilidad de la placa de adaptación y el desempeño en los sitios de trabajo, los cual mejorará la reputación del producto en el mercado.