1 Introduction
In the last years, several types of alloy coatings have been developed, in order to improve the performance of the traditional zinc-based metallic coatings, so as to have a better corrosion resistance while reducing the cost, thanks to the reduction of the total mass of the coating per unit of surface. Some authors already anticipated this evolution like CSIC in Spain: “It can be considered that zinc as anodic material has practically reached its limit of development, being currently displaced gradually by aluminium alloys of equal current efficiency (90%), but with the advantage of having a greater real current supply ... and best electrochemical equivalent" (González & CSIC, 1984).
Manufacturers recommend this type of alloys in applications where traditionally, zinc-based coating protection was used, with high thicknesses coating (post-galvanized) to be able to withstand corrosion effects in a harsh environment (road/civil engineering, housing, farming, construction, rail-roads, electric power and equipment, automobile parts, etc.), and in electric equipment such as metallic cable trays and trunkings for cable routing. Other arguments for this alternative have been claimed, like better energy efficiency in the production, aesthetics, better self-healing protection in cuts and hem flanges, etc. In addition, from a safety point of view, the typical cutting edges of traditional hot-dip galvanizing coating disappear.
At present, there´s a large amount of scattered information around this type of alloys, such as specific international normative, qualities and designations for purchasing purposes, many types of corrosion tests (field tests and accelerated tests), as well as large numbers of manufacturers and types of end users.
The aim of this article is to gather, classify and structure all this scattered information in order to facilitate engineers and other users, a complete summarized review of all the key aspects of these alloys. At the same time, a dedicated analysis has been done about long-term corrosion resistance, since at present, there is no specific guideline which provides all the findings of the actual corrosion tests or values of reference to determine the right thickness of the coating for a specific application.
2. Methodology
Structure characterization
Structure characterization of the zinc-aluminium-magnesium (ZM) alloys, according to Salgueiro (Salgueiro et al., 2015a) is represented in figure 1, where the ternary eutectic microstructures system is based in Zn-Al- Zn2Mg and binary eutectic in Zinc-Zn2Mg.
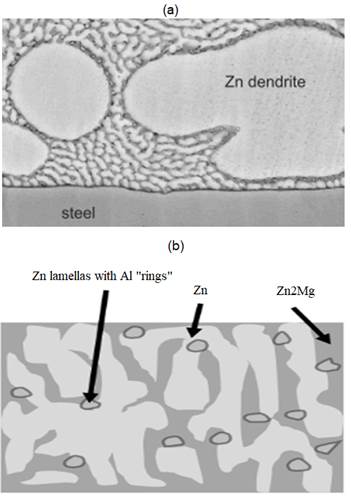
Figure 1: Characterization of the uncorroded Zn-Mg-Al coating: (a) General structure. (b) High resolution figure representing the detailed microstructure of the ternary eutectic. Source: Own illustration based on reference (Salgueiro et al., 2015b).
Corrosion behaviour
Companies producing zinc-aluminium-magnesium (ZM), zinc-aluminium (ZA) and aluminium-zinc (AZ) alloys claim its good corrosion performance in front of zinc (Z), mostly based in Neutral Salt Spray tests (ISO, 2015), like Stahl(, shown in figure 2 (Stahl, 2013).
According to this manufacturer, the zinc-magnesium complex, forms a solid barrier layer. Reaction of oxygen and iron is slowed and creates a barrier effect on cut edges, as can be observed in figure 3 (Stahl, 2013):
Arcelor Mittal(, one of the most relevant manufacturers of these types of alloys, claims those features in a similar way as well:
“Aluminium corrodes more slowly than zinc in most atmospheres because of its barrier layer of very passive aluminium oxide. However, this passive layer prevents aluminium from adequately contributing towards cathodic (sacrificial) protection. Cathodic protection is the strong point of zinc coatings, so if the coating is cut or scratched, the zinc near the exposed area will corrode first. The zinc-aluminium alloy combines the strength of both zinc and aluminium, giving better passive barrier protection than regular galvanize, and better sacrificial protection than alloy coatings with lower zinc composition” (Arcelor Mittal, 2013b).
In this sense, also crucial in the corrosion process is the protective effect of the corrosion products. Their composition and appearance along the process are key in determining the corrosion resistance. According to a specific research work to investigate corrosion products on ZM alloys (Prosek et al., 2014a; Schürz et al., 2010).
It was determined that corrosion products on ZM coated steel consist mainly of hydrozincite, Zn5(OH)6(CO3)2; zinc carbonate, ZnCO3 and zinc hydroxide, Zn(OH)2; with additions of simonkolleite, Zn5(OH)8Cl2 .H2O and a carbonate-containing magnesium species.

Figure 2: NSST corrosion resistance of Z and ZM materials. Source: Own illustration based on reference (Stahl, 2013).
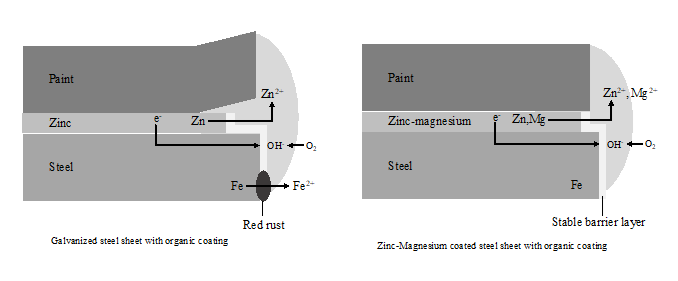
Figure 3: Barrier layer effects creation in ZM materials. Source: Own illustration based on reference (Stahl, 2013).
In the same line, other research works (Hosking et al., 2007; Keppert et al., 2014; Prosek et al., 2008; Prosek et al., 2014a; Salgueiro et al., 2015b; Schuerz et al., 2009a), stated that “magnesium accelerates the formation of a dense corrosion product, Zinc chloride hydroxide monohydrate, also called simonkolleite, which is extremely stable”. It plays a key role as a corrosion inhibitor for the base metal.
It is proven that ZM alloys have a very good performance in sodium chloride-containing atmospheres, due to the transformation of the ZM coating into a stable aluminium-rich oxide layer, which adheres on the steel substrate and protects it against corrosive attack (Schuerz et al., 2009b). Autocoat®, in a specific research work (Autocoat, 2013), also demonstrated this fact by carrying out accelerated corrosion tests based on different standards from the automotive sector and the regular ISO 9227 neutral salt spray test (ISO, 2012c).
As can be clearly seen in table 1, the higher chloride load in the test, the higher ZM performance, measured as time to reach red rust.
Table 1: Time to red rust appearance as a function of testing conditions in weeks (Autocoat, 2013).
Pen | Weekly chloride load (mg/cm 2 ) | HDG (*) 7 µm | ZM 7 µm | ZM / HDG |
---|---|---|---|---|
Volvo test | 4,5 | 3 | 5 | 1,7 |
New VDA test | 1,35 | 1,5 | 3 | 2 |
Renault ECC1 test | 1 | 2 | 6 | 3 |
VDA test | 13,6 | 1,5 | 12 | 8 |
Neutral salt spray test | 90 | 0,6 | 8 | 13 |
(*) HDG: Hot Dip Galvanized (zinc-based coating)
However, for other environments with other types of pollutants, the behaviour varies, and the differences in performance are not so obvious, as will be seen later. That´s why, regular Neutral Salt Spray test (NSS) (ISO, 2012c), which has a very high chlorine load, at present is not considered valid to check corrosion resistance in general. In addition, these tests are done in a continuous mode (continuous sprayed water during the entire duration of the test), which causes that corrosion products cannot be generated.
To avoid this, other types of accelerated corrosion tests has been developed, led mostly by the automotive sector, such as cyclic NSS tests, like is the case of Renault( D17 2028/--C / ECC1 cycles (Renault, 2007), Volvo STD1027,3371 (Volvo, 2010a), Volvo STD1027 (Volvo, 2010b), Volvo STD423 (Volvo, 2009). In this way, Galvazinc and Cetim (Galvazinc & Cetim, 2014) performed this type of test, using the referred Volvo( higher acid content test, in which 10 cycles of 24 h each, were done in a SO2 atmosphere and where the corrosion resistance, measured in zinc losses (µm), was slightly higher than standard post-galvanization. Table 2 shows the time distribution for one cycle and the test conditions. Table 3 shows the final corrosion results expressed in mass loss.
Table 2: 24 h cycle time distribution in Volvo( test according to STD1027 (Volvo, 2010b).
24 h cycle time distribution (h) | Conditions |
---|---|
4 | 50 ºC |
2 | 35 ºC and 100% RH(*) |
2 | SO2 cabin at 35 ºC - SO2 injected: 2 litres |
16 | -30 ºC |
(*) Relative Humidity
Table 3: Corrosion results expressed in coating mass loss for each material tested by Galvazinc & Cetim (Galvazinc & Cetim, 2014) in Volvo( test according to STD1027 (Volvo, 2010b).
Material tested | Coating mass loss ((m) |
---|---|
Regular pre-galvanized Z275 | 8,16 |
HDG post-galvanized | 10,2 |
HDG + Oxide | No observed losses |
ZM120 Magnelis( | 11,52 |
Table 4: ISO atmosphere corrosivity categories (ISO, 2012a).
Category | Corrosivity |
---|---|
Very low | |
C2 | Low |
C3 | Medium |
C4 | High |
C5 | Very high |
CX | Extreme |
Table 5: Corrosion rates for zinc, r corr , expressed in μm·a -1 for the first year of exposure for the different corrosivity categories ISO 9223 (ISO, 2012a).
Corrosivity category | r corr (µm·a -1) |
C1 | r corr ≤ 0.1 |
C2 | 0.1 < r corr ≤ 0.7 |
C3 | 0.7 < r corr ≤ 2.1 |
C4 | 2.1 < r corr ≤ 4.2 |
C5 | 4.2 < r corr ≤ 8.4 |
CX | 8.4 < r corr ≤ 25 |
Looking at the tests results, it can be stated that ZM coatings have in general, a good performance in harsh atmospheres with high humidity and high chloride load, but this performance is less obvious in SO2 / acid atmospheres or with low humidity. On the other hand, it is also important to mention that more and more, in many countries, mostly from advanced economies, the level of SO2 emissions has been drastically reduced, while NOx emissions have increased (Stockholm-Environment and health administration, 2006).
Finally, some publications also mention that in low CO2 atmospheres, ZM coatings are more affected in terms of corrosion than pure zinc coatings (LeBozec et al., 2013; Prosek et al., 2014b).
Relevant international standards covering ZM coatings
Standards to classify environments and corrosivity categories
With the exception of zinc-based metal coatings, for which the ISO 9223 standard (ISO, 2012a) (CEN, 2012b) and their corresponding parts, offer estimations of the corrosion rate for different environments, classified by corrosivity category (C1-CX), there is no standard at present with similar information, in terms of estimated corrosion rates for finishes based on ZM alloys. Therefore, in the present clause, only a summary of the aforementioned standards and their scope will be cited and briefly explained:
ISO 9223: Corrosion of metals and alloys. Corrosivity of atmospheres. Classification, determination and estimation (ISO, 2012a).
The scope of this standard states:
“This International Standard establishes a classification system for the corrosivity of atmospheric environments. It:
- defines corrosivity categories for the atmospheric environments by the first-year corrosion rate of standard specimens,
- gives dose-response functions for normative estimation of the corrosivity category based on the calculated first-year corrosion loss of standard metals, and
- makes possible an informative estimation of the corrosivity category based on knowledge of the local environmental situation.”
“…specifies the key factors in the atmospheric corrosion of metals and alloys. These are the temperature-humidity complex, pollution by sulphur dioxide and airborne salinity”.
It is the main ISO standard for zinc coatings corrosion classification of atmospheres and it establishes corrosivity categories, from C1 to CX, as shown in table 4.
It also gives an approximation on what the corrosion rates could be for a first-year exposure, based in the type of environment (table 5).
ISO 9224: Corrosion of metals and alloys. Corrosivity of atmospheres. Guiding values for the corrosivity categories (CEN, 2012a).
This standard shall be used in conjunction with ISO 9223. While ISO 9223 refers to corrosion values for the first year of exposure for the different C1-CX categories, ISO 9224 analyses those values for durations above one year.
It applies the master expression for corrosion processes, which obeys the following equation:
C (t) = A·t n (1)
Where t is the exposure time, expressed in years; A is the corrosion rate experienced in the first year, expressed in grams per square metre per year [(g/(m2·a)] or micrometers per year ((m·a-1); n is the metal-environment-specific time exponent, that depends on each metal and the particular atmospheric conditions (generally, n<1). There are guiding values in this standard for the n parameter.
ISO 9225: Corrosion of metals and alloys. Corrosivity of atmospheres. Measurement of environmental parameters affecting corrosivity of atmospheres (ISO, 2012b).
This standard determines the methodologies for the measurement of the parameters used to determine the type of atmospheric corrosivity, more specifically the humidity and temperature, the airborne pollutants and finally the SO2 and Cl- content.
ISO 9226: Corrosion of metals and alloys. Corrosivity of atmospheres. Determination of corrosion rate of standard specimens for the evaluation of corrosivity (CEN, 2012b).
This standard determines the way to know the different corrosivity categories according to ISO 9223, through a one-year test, from which the loss of mass can be known and thus classify the corrosivity of the atmosphere according to table 2 of said norm.
Its scope states that “…this International Standard specifies methods which can be used for the determination of corrosion rate with standard specimens. The values obtained from the measurements (corrosion rates for the first year of exposure) are intended to be used as classification criteria for the evaluation of atmospheric corrosivity according to ISO 9223. They can also be used for informative evaluation of atmospheric corrosivity beyond the scope of ISO 9223”.
ISO 12944-1: Corrosion protection of steel structures by protective paint systems. Part 1: General introduction (CEN, 1998).
It is a general introduction to the ISO 12944 series of standards, providing definitions and an introduction to each of the 8 parts in which the series is composed.
ISO 12944-2: Corrosion protection of steel structures by protective paint systems. Part 2: Classification of environments (CEN, 2017).
This part refers to the environments related to the corrosivity categories, which have been based on the ISO 9223 standard previously mentioned (C1 to CX). Likewise, each one of these categories is defined, based on the mass loss during the first year of standard specimen, as it was done in the ISO 9223 standard (see table 5).
Standards to classify continuously hot-dip coated steel flat products for cold forming
EN 10143: Continuously hot-dip coated steel sheet and strip - Tolerances on dimensions and shape (CEN, 2006).
This European Standard applies to continuously zinc (Z), zinc-iron alloy (ZF), zinc-aluminium alloy (ZA), aluminium-zinc alloy (AZ) and aluminium-silicon alloy (AS) hot-dip coated flat products made of low carbon and high strength steels for cold forming and of structural steels with a minimum thickness of 0,20 mm and a maximum thickness of 6,50 mm, delivered as sheet, wide strip, slit wide strip or cut lengths obtained from slit wide strip or sheet.
Example of designation:
Sheet EN 10143 - 0,80Sx1200Sx2500FS
EN 10346: Continuously hot-dip coated steel flat products for cold forming. Technical delivery conditions (CEN, 2015).
This is the standard that regulates the standardized designations and supply conditions of sheets and strips with hot dip galvanization in continuous for subsequent cold deformation, for thicknesses between 0,2 and 3 mm. The alloys based on zinc-aluminium / magnesium are those designated as ZA, AZ and ZM. However, the standard does not refer to other standards regarding corrosion of these finishes. In this way, it is important to bear in mind the definitions and composition that it makes in this regard and that are highlighted in table 6.
Table 6: Composition of zinc/aluminium/magnesium alloys according to EN 10346.
Alloy | Zn | Al | Mg | Si | Mischmetal | |
---|---|---|---|---|---|---|
ZA | Balance | 5% | - | - | Small amounts | |
ZM | Balance | 1,5% ( (Al+Mg) ( 8% ; Mg ( 0,2% | - | - | ||
AZ | Balance | 55% | - | 1,6% | - |
Example of designation:
Steel EN 10346 - DX53D+ZM100-M-B-O, where:
DX53D corresponds to the type of base material.
ZM100 identifies the type of coating and its mass (100 g/m2 in the 2 faces of the coated surface).
M-B-O corresponds to the type of surface finish, in this case we talk about a minimized spangle zinc solidification way (M), with an improved surface (B) and oiled treated surface (O).
Also, it is very useful to convert g/m2 to µm per side through equation (2) included in the referenced standard:
t z = m z / 2d(2)
Where, t z is the zinc coated thickness ((m); m z is the zinc coating mass of both surfaces (g/m2) and d is the zinc density (g/cm3), that for the case of ZM alloys used to be between 6,2 and 6,6 g/cm3.
In this case, it is relevant to mention that maximum available thickness for a ZM alloy is around 32 µm, that corresponds to a ZM430 (430 g/m2).
JIS G 3323: Hot-dip zinc-aluminium-magnesium alloy-coated steel sheet and strip (JIS, 2012).
This Japanese Industrial Standard specifies the steel sheet and strip and corrugated sheet manufactured by processing steel sheet into the shape and dimensions specified in JIS G 3316, which are coated to be of equal thickness on both surfaces by a hot-dip zinc-aluminium-magnesium alloy coating process. The zinc-aluminium-magnesium alloy composition by mass fraction is normally between 5,0-13,0% of aluminium, 2,0-4,0% of magnesium, 1,0% of other elements and the balance zinc.
Example of designation: Sheet SGMH 340
ASTM A1046: Standard Specification for Steel Sheet, zinc-aluminium-magnesium alloy-coated by the Hot-Dip Process (ASTM International, 2014).
This specification covers steel sheet in coils and cut lengths coated with zinc-aluminium-magnesium alloy by hot-dip process intended for applications requiring corrosion resistance and paintability. The steel sheet is produced in a number of designations, types, grades and classes designed to be compatible with differing application requirements. The coating bath composition and the method of estimating the coating thickness from the coating weight (mass) are given. Heat analysis of the base metal shall conform to the chemical requirements prescribed for carbon, manganese, phosphorous, sulphur, aluminium, copper, nickel, chromium, molybdenum, vanadium, columbium, and titanium. Bending properties of the base metal including minimum cold bending radio and cracks, and the coating bend test requirements are detailed.
Example of designation: Steel sheet CS Type A
Standard to classify steel wire products
This corresponds to standard EN 10244-2: 2009: Steel wire and wire products. Non-ferrous metallic coatings on steel wire. Part 2: Zinc or zinc alloys coatings (CEN, 2009).
This part of the standard specifies the requirement for coating mass, other properties and testing of zinc and zinc alloy coatings on steel wire and steel wire products of circular or other section. The standard classifies the mass requirements for the different diameters’ ranges, for zinc-based coatings and for aluminium alloys. It proposes also methods to test adherence and determine the mass of the coating; finally, there is a description of dipping test to check “…any significant eccentricity defect in the coating or any other significant uniformity defect…”.
Example of designation: ZM Class A
Differences between standards in terms of aluminium and magnesium content
According to the standards and designations referred in previous clauses, the different types of materials and coatings for zinc-aluminium-magnesium alloys can be summarized as described in table 7:
Table 7: Most relevant metallic alloys alternative to traditional zinc-based coatings.
Acronym designation | Content | Comments |
Z | Minimum content of 99% | Standard protection |
ZF | Between 8 to12% Fe after annealing - Balance Zn | Improved versus Z |
ZA | 5% Aluminium - Balance Zn | Improved Z + drawing properties |
AZ | 55% Aluminium-1,6% Si - Balance Zn | Good in acid/neutral atmospheres + aesthetics |
ZM | 0%<Al<13% 0,2%<Mg<8% Balance Zn | Good in harsh environments and salt atmospheres. Self-healing |
AS | Between 8 to 11% Si - Balance Aluminium | Good for high temperatures + good formability |
Figures 4 and figure 5, show respectively, the band of aluminium and magnesium composition in the three key standards that classifies ZM finishes shown previously. It shows the difficulty to standardize accurately each quality designation, due to the big existent range in terms of content for each element of the alloy composition.
Example extracted from EN 10346: “Note 1 to entry: The composition of the bath is the sum of aluminium and magnesium from 1,5 to 8%, containing minimum of 0,2% magnesium and the balance zinc”.
Product standard regarding cable trunking systems
This corresponds to IEC 61537: Cable management - Cable tray systems and cable ladder systems (IEC, 2006), which states: “…this International Standard specifies requirements and tests for cable tray systems and cable ladder systems intended for the support and accommodation of cables and possibly other electrical equipment in electrical and/or communication systems installations...”
Table 8 shows the classification system of the different zinc-based coatings (class 0 to 8) and the different stainless-steel qualities (9A to 9D).
The main issue of this 2006 standard (edition 2), is that ZM finishes withstand much more than class 8, since the corrosion test is based in neutral salt spray tests. So, it is not possible to classify them applying this standard.
The new edition (edition 3) in which the IEC committee is working on (IEC, 2016), comprises extended corrosion classes: from Class 9 (1000 h in NSTT) to class 13 (>2500 h in NSTT). However, there are many discussions today about whether the salt spray test is the most appropriate to measure the corrosion resistance versus cyclic tests.
Zinc-Aluminium-Magnesium alloys offered in the market
Figure 6 shows the evolution in time of zinc-aluminium-magnesium alloys (Stahl, 2013). Today, there are many suppliers of ZM materials worldwide. Table 9 Table 9b, Table 9c, shows the main manufacturers, the product trademark and the main features of those products.
Figure 7 compares the differences in terms of aluminium and magnesium content, while figure 8 shows the sum of its contents, among the different suppliers. When it comes to corrosion.
Figure 9 shows a summary of the different corrosion resistance hours, based on Neutral Salt Spray Test (NSST).
As a conclusion to this section, it can be observed the high complexity of the global ZM offer, having different international standards, several commercial brands, many different coating compositions, different corrosion behaviours and very few direct equivalences between the available ZM products.
Trunking cable system manufacturers using ZM alloys
Table 10a , Table 10b shows a summary of the main trunking system manufacturers using ZM alloys.
Table 8: Classification for corrosion resistance according to IEC 61537 (IEC, 2006).
Class | Reference-Material and finish |
---|---|
0a | None |
1 | Electroplated to a minimum thickness of 5 µm |
2 | Electroplated to a minimum thickness of 12 µm |
3 | Pre-galvanized to grade 275 to EN 10327 and EN 10326 |
4 | Pre-galvanized to grade 350 to EN 10327 and EN 10326 |
5 | Post-galvanized to a zinc mean coating thickness (minimum) of 45 µm according to ISO 1461 for zinc thickness only |
6 | Post-galvanized to a zinc mean coating thickness (minimum) of 55 µm according to ISO 1461 for zinc thickness only |
7 | Post-galvanized to a zinc mean coating thickness (minimum) of 70 µm according to ISO 1461 for zinc thickness only |
8 | Post-galvanized to a zinc mean coating thickness (minimum) of 85 µm according to ISO 1461 for zinc thickness only |
9A | Stainless steel manufactured to ASTM: A 240/A 240M - 95a designation S30400 or EN10088 grade 1-4301 without a post-treatment b |
9B | Stainless steel manufactured to ASTM: A 240/A 240M - 95a designation S31603 or EN10088 grade 1-4404 without a post-treatment b |
9C | Stainless steel manufactured to ASTM: A 240/A 240M - 95a designation S30400 or EN10088 grade 1-4301 with a post-treatment b |
9D | Stainless steel manufactured to ASTM: A 240/A 240M - 95a designation S31603 or EN10088 grade 1-4404 with a post-treatment b |
a for materials which have no declared corrosion resistance classification. | b the post-treatment process is used to improve the protection against crevice crack corrosion and the contamination by other steels. |
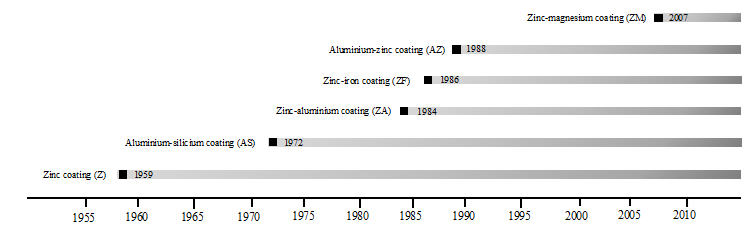
Figure 6: Evolution of metal alloys development in the European market. Source: Own illustration based on reference (Stahl, 2013).
Table 9: Main alloys based on zinc-aluminum-magnesium products existing in the market and their corresponding manufacturers, used in electrical conduits.
Raw material manufacturer (RMM 1 ) | Trade name | Designation | Zinc | Aluminum | Magnesium | Others | Declared corrosivity category |
---|---|---|---|---|---|---|---|
Arcelor Mittal( | Magnelis( | Steel sheets or strips (Arcelor Mittal, 2013c) | 94% | 3% | 3% | - | C5-15 years C5M-20 years >200 h/(m |
Arcelor Mittal( | Zagnelis( (15) | Steel sheets or strips (Rich Clausius & Arcelor Mittal, n.d.) | 93.3% | 3.7% | 3% | - | N.D.1 |
Arcelor Mittal( | Aluzinc( | Steel sheets or strips (Arcelor Mittal, 2013a) | 43.4% | 55% | 0% | 1.6% Si | C4-15 years ±100 h/(m |
Arcelor Mittal( | Crapal(2 | Steel wire (Arcelor Mittal, 2013b) | 95% | 5% | 0% | - | 1000 h NSS1 |
Arcelor Mittal( | Crapal(4 | Steel wire (Arcelor Mittal, 2013b) | 95% | 5% | 0% | - | 2000 h NSS1 |
Arcelor Mittal( | CrapalOptimum( | Steel wire (Arcelor Mittal, 2013b) | 92% | 5% | 3% | - | 2500 h NSS1 |
Arcelor Mittal( | CrapalPremium( | Steel wire (Arcelor Mittal, 2012), (Arcelor Mittal, 2013b) | N.D.1 | N.D.1 | N.D.1 | N.D.1 | 4000 h NSS1 (310 g/m2) |
Arcelor Mittal( | Crapal(Color7 | Steel wire with pigmented organic coating (Arcelor Mittal, 2013b) | 92% | 5% | 3% | - | 2500 h NSS1 |
Corus Tata( | Magizinc( | Steel sheets or strips ZMA100 - ZMA200 (ZMA140 replacing Z275) (Tata Corus, 2012), (Tata Corus, 2010), (Tata Corus, 2016), (Tata Corus, 2009) | 96.8% (9) | 1.6%(9) | 1.6%(9) | Pure Zinc crystals surrounded by MgZn2/Zn and Al (8) | 1000÷1200 h NSS1 (140 g/m2) |
Mazzoleni( | Galvalid( | Steel wire (Mazzoleni, 2016) | 95% | 5% | 0% | Misch metals | 500÷600 h NSS1 (15 µm) |
Bekaert( | Bezinal( | Steel wire (Bekaert, n.d.) | 95% | 5% | - | Bekaert know-how | 1000 h NSS1 (75 g/m2) |
Bekaert( | Bezinal(2000 | Steel wire (Bekaert, n.d.) | 95% | 5% | - | Bekaert know-how | 2000 h NSS1 (75 g/m2) |
Bekaert( | Bezinal(3000 | Steel wire (Bekaert, 2010) | 95% | 5% | - | Bekaert know-how | 5000 h NSS1 (Class A16) 3000 h NSS1(Class B16) |
Table 9: continuation
Raw material manufacturer (RMM 1 ) | Trade name | Designation | Zinc | Aluminum | Magnesium | Others | Declared corrosivity category |
---|---|---|---|---|---|---|---|
Salzgitter Flachstahl( | Stroncoat( | Steel sheets or strips (Salzgitter Flachstahl, n.d.) | 96-98% | 1-2% | 1-2% | - | 2 to 6 times higher than standard zinc coatings |
Salzgitter Flachstahl( | StronSal( | Steel sheets or strips (Salzgitter Flachstahl, 2016) | 96-98% | 1-2% | 1-2% | - | 2 to 6 times higher than standard zinc coatings |
U.S. Steel Kosice( | Zinkomag( | Steel sheets or strips (U.S. Steel Kosice, 2015) | 98.4-98% | 0.8-1% | 0.8-1% | - | 200 h NSS1 until appearance of red corrosion (50 g/m2 per side) |
U.S. Steel Kosice( | Zinkomag Plus( | Steel sheets or strips (U.S. Steel Kosice, 2015) | 96-96.4% | 1.8-2% | 1.8-2% | - | >1000 h NSS1 (150 g/m2 per side) |
Voelstalpine( | Corrender( | Steel sheets or strips (Voelstalpine, 2015), (Voelstalpine, 2016) | 96% | 2.5% | 1.5% | - | >1300 h ZM90 NSS1 (Voelstalpine, 2016) |
Voelstalpine( | Colofer(Corrender | Steel sheets or strips (Voelstalpine, 2015), (Voelstalpine, 2016) | 96% | 2.5% | 1.5% | Organic coating 10 | - |
One Steel( | Zalcote( | Steel wire (OneSteel, 2016) | 95% | 5% | 0% | - | N.D.1 |
Maccaferri( | Galmac(4R | Steel wire (Maccaferri, 2015) | not ref | not ref | 0% | Misch metals11 | ≈2500 h NSS1 |
Posco( (group Nisshin Steel) | PosMAC(12 | Steel sheets or strips (Posco, n.d.) | 94.5% | 2.5% | 3% | - | Superior to 120 cycles NSS1 (140 to 275 g/m2) |
Wheeling Nisshin(12 (group Nisshin Steel) | ZAM( 12 | Steel sheets or strips (Nisshin Wheeling, n.d.) | 91% | 6% | 3% | - | >2500 h NSS1 (0,3 oz/ft2 in one side) |
Wheeling Nisshin(12 (group Nisshin Steel) | Galvalume( 13 | Steel sheets or strips (Nisshin Wheeling, n.d.) | 45% | 55% | 0% | - | >2500 h NSS1 |
USS( (United States Steel Corporation) | Galvalume( | Steel sheets or strips (United States Steel Corporation (USS), 2015) | 45% | 55% | 0% | Silicon 14 | N.D.1 |
Stahl( | WZM Wupperman( | Steel sheets or strips (Stahl, 2013) | not ref | not ref | not ref | not ref | Between 800 and 1000 h for an average coating of 20 μm |
Bluescope Steel( | Zincalume( | Steel sheets or strips (Bluescope Steel, 2013) | 43.5% | 55% | 0% | 1.5% Si | 4 times more resistant than a standard galvanized with the same thickness. Tests performed but results not declared. |
Stramit( - Building products | ZAM( 12 | Steel sheets or strips (Stramit, 2012) | 91% | 6% | 3% | - | 4 times more resistant than a standard galvanized with the same thickness. NSS and mass loss tests performed. |
Ruukki( | Galfan( | Steel sheets or strips | not ref | not ref | not ref | not ref | N.D.1 |
SSAB( | Alucinc( | Steel sheets or strips | 43.4% | 55% | 0% | 1.6% Si | C4-15 years ±100 h/(m |
Technology derived from the project “Galfan” (See “Producers” in: http://galfan.com (3)) | Galfan( | Steel sheets or strips Steel wire | 95% | 5% | 0% | - | No detailed technical information on corrosion resistance is cited |
Magni( http://magnicoatings.com/?lang=es | Magni( | Depending on application (see Magni( webpage) (Technology applicable to parts and accessories) | not ref | not ref | 0% | not ref | No detailed technical information on corrosion resistance is cited |
Table 9: continuation
Raw material manufacturer (RMM 1 ) | Trade name | Designation | Zinc | Aluminium | Magnesium | Others | Declared corrosivity category |
---|---|---|---|---|---|---|---|
Dacromet( technology (based in laminar zinc and aluminium technology (zinc/aluminium flakes)) | Dacromet( Dacromet( 320 (Grade A and grade B)16 Dacromet( 500 (Grade A and grade B)16 Dacroblack( 15 (12 µm) | Depending on the application and the providers of this technology 5 (Group, n.d.) (Technology applicable to parts and accessories) | not ref | not ref | not ref | Cr+3 ó Cr+6 passivated | According to NOF Metal coatings (Group, n.d.), for Dacromet( 320: >240 h w/o white corrosion, >600 h w/o red corrosion (Grade A) >240 h w/o white corrosion, >1000 h w/o red corrosion (Grade B) |
SSAB( | Alucinc( | Steel sheets or strips | 43.4% | 55% | 0% | 1.6% Si | C4-15 years ±100 h/(m |
Geomet( Technology (based in laminar zinc and aluminium technology (zinc/aluminium flakes)) | Geomet( Geomet( 321 (Grade A and B)16 Geomet( 500 (Grade A and B)16 Geomet( D/360 (3 to 15 µm) | Depending on the application and the providers of this technology 5 (Galol S.A., n.d.-b), (NOF Metal Coatings Group, n.d.) Alternative Technology to Dacromet( Chrome free. (Technology applicable to parts and accessories) | not ref | not ref | not ref | Chrome free passivated | According to NOF Metal coatings / Galol (Galol S.A., n.d.-b), para Geomet( 321: >240 h w/o white corrosion, >720 h w/o red corrosion (>24 g/m2) >1000 h w/o red corrosion (>36 g/m2) |
Deltatone Technology( (based in laminar zinc and aluminium technology (zinc/aluminium flakes)) | Deltatone( | Depending on the application and the providers of this technology6 (Galol S.A., n.d.-a) (Technology applicable to parts and accessories) | not ref | not ref | not ref | Admits post-treatments (Delta-seal(, Delta-seal GZ(…) | Between 480 h and 960 h (8 and 12 µm), test NSS ISO 9227 Deltatone( 9000 (Galol S.A., n.d.-a) |
BIEC International Inc 13 http://www.galvalume.com | Galvalume( | Depending on the application and the providers of this technology (BIEC, 2016) | 45% | 55% | 0% | - | 30 years before the first appearance of red corrosion, according to BIEC (BIEC, 2016) |
ThyssenKrupp( | ZM Ecoprotect( | Coating mass between 70 and 300 g/m2 | 99% | 1% | 1% | - | Salt Spray test 1000 h ZM140 |
Nippon steel & Sumitomo Metal corporation http://www.nssmc.com/en/product/sheet/superdyma_introduction.html | SuperDymaTM | Coating weight K18 | 86% | 11% | 3% | Trace amount of _Si | Salt Spray Test 2000 H Cycling corrosion test (JASO M609-91method) 180 cycles |
RMM: Raw Material Manufacturer; N.D.: Not declared; NSS: Neutral Salt Spray test, not ref: Not Referenced.
(2) According to IEC 61537 Edition 3 Committee draft (IEC (International Electrotechnical Commission), 2016)
(3) According to Galfan Technology Center “A proprietary zinc alloy coating (5% aluminium) with improved corrosion resistance and formability compared to zinc alone. Galfan has been around since the International Lead Zinc Research Organization (ILZRO) obtained worldwide patents on this new alloy for anti-corrosion coating in 1981. This grew from an ILZRO-organized project co-sponsored by Arbed, Cockerill Sambre, Usinor and Sacilor (and now all part of Arcelor), British Steel, Fabrique de Fer de Maubeuge (now all part of Corus), New Zealand Steel, and Stelco (Canada) at Centre de Recherches Metallurgiques in Belgium.It was discovered that by combining 95% zinc with nearly 5% aluminium plus specific quantities ofrare earthmischmetal could be reliably used in the hot-dip coating process, and conferred substantially improved performance to the end-product. Licenses to use the revolutionary Galfan® technology were granted to manufacturers worldwide.” (Galfan Technology Center Inc., n.d.). Of the manufacturers cited on the Galfan official website for the electrical conduits sector, it should be noted: Grupo Arcelor, Corus Group Plc, Voest Alpine Stahl Linz, Galvstar LLC…
(4) Magni ( does not specify in its technical information the detailed composition of its coatings, although the most frequent refer to zinc-based coatings with an organic "Top" layer based on aluminium.
(5) Geomet ( y Dacromet ( are registered trademarks of the company NOF Metal Coatings, whose technology is applied by other companies. For instance, Geomet ( 321 and Geomet ( 500 from the company “Galol” (www.galol.com). This technology is based on a water-based coating based on sheets of zinc and aluminium, passivated inside an inorganic matrix, without chromium (neither hexavalent nor trivalent), and which arose as an alternative to the original Dacromet ( eliminating the use of Chromium, in compliance with the European Directives ReACH and RoHS (Galol S.A., n.d.-b).
(6) For instance, Deltatone ( 9000 from the company “Galol” (www.galol.com). This technology is based on an organic coating based on sheets of zinc and non-hydrogenating aluminium, which offers excellent protection against corrosion (Galol S.A., n.d.-a). It is a non-electrolytic protection system, for all types of metal parts, threaded or not, especially steel parts.
(7) Crapal ( finishes coated with a layer of pigmented resin to prevent the fall of zinc oxides into the earth. Used primarily for agricultural use or to offer different aesthetics (Arcelor Mittal, 2013b).
(8) According to the only statement found in the Tata Corus bibliography about the composition of Magizinc ( (Tata Corus, 2012, 2016). Also in his brochure "Magizinc - The metallic coating of the future", a brief mention is made in this way: “MagiZinc is a zinc coating that incorporates a small fraction of magnesium and aluminium” (Tata Corus, 2010).
(9) According to the internal report of Tata Corus 2007-2008 (Tata Corus, 2009). This information is not publicized in the official Magizinc ( technical brochures
(10) According to Voelstalpine brochure (Voelstalpine, 2015) for which no information is offered about the content of the additional organic coating of Colofer ( Corrender.
(11) According to Maccaferri brochure (Maccaferri, 2015): The GalMac ® 4R coating also has the presence of "MischMetals" (MM) that allow a more authentic bond between Zinc (Zn) and Aluminium (Al).
(12) PosMAC is the original brand of the Korean company Posco, for its alloys of zinc-Aluminium-Magnesium, which was later acquired by Nishin, whose brand for that product is ZAM ( . Wheeling Nisshin is a subsidiary of Nisshin Steel in the United States, following the acquisition of the wheeling company group. Stramit also markets this product.
(13) Galvalume ( is a registered trademark of BIEC international, Inc. According to the BIEC website: “BIEC International Inc. is the worldwide licensor of the technology and know-how associated with 55% Aluminium-Zinc alloy coated sheet steel (better known as GALVALUME). A measure of the success of this program is the fact that virtually all of the major steel companies worldwide have become licensees of BIEC. Today, BIEC is the acknowledged leader in technologies associated with 55% Al-Zn coated sheet Steel”(BIEC, 2016).
(14) “A small but important addition of silicon is included in the coating alloy. It is added not to enhance the corrosion performance, but to provide good coating adhesion to the steel substrate when the product is roll-formed, drawn, or bent during fabrication” (United States Steel Corporation (USS), 2015).
(15) Zagnelis ( is the adaptation of Magnelis ( to the automotive sector. This is what Arcelor Mittal indicates on its website: “Zagnelis™ has been specially designed to improve corrosion protection of vehicles, while satisfying OEMs' specifications regarding manufacturability” (Rich Clausius & Arcelor Mittal, n.d.).
(16) Grades according to EN 10244-2(CEN (European Committee for Standardization), 2009). In this way it has that a grade A corresponds to a thickness of 5 to 8 microns, while a grade B of 8 to 10 microns.
Table 10: Main trunking system manufacturers using ZM alloys (standard or wire cable trays).
CTM1 | CTM1 Trade Mark | RMM2 | Trade Mark RMM2 | Designation given by CTM1 | RMM2 declared corrosion resistance class according to IEC 61537 |
---|---|---|---|---|---|
Schneider Electric( | Zn+ | Arcelor Mittal( | Magnelis( | Steel sheets and strips | 8 |
Schneider Electric( | Zn+ | Arcelor Mittal( | Magnelis( | Steel wire | 8 |
Obo Betterman( | Double Dip | Thyssen Krupp( | - | Not declared 3 | ( 8 (4) |
Mavil( (Gewiss group) | High Protection HP | Arcelor Mittal( 5 | Unknown 5 | Unknown 5 | 9 (6) (1000 h) |
Mavil( (Gewiss group) | Uses the trademark (Magni() | Magni(http://magnicoatings.com/?lang=es | Magni( | Not declared | Not declared |
Mavil( (Gewiss group) | Uses the trademark “Geomet(” | Geomet( technology | Geomet( | Not declared | ( 8 (7) |
Mavil( (Gewiss group) | Uses the trademark “Deltatone(” | Deltatone( technology | Deltatone ( | Not declared | Not declared |
Legrand(8 | - | Geomet( technology | Geomet( | Not declared | Not declared |
Pemsa( | Black C8( | Own developed formula | - | Not declared | 8 |
Oglaend( Systems | There is no standard offer | There is no standard offer 11 | There is no standard offer | There is no standard offer | - |
Axelent(9 | There is no standard offer | There is no standard offer | There is no standard offer | There is no standard offer | - |
B-Line( (Cooper Industries - Eaton group) | There is no standard offer | There is no standard offer | There is no standard offer | There is no standard offer | - |
MP Husky( | There is no standard offer Just Aluminum | There is no standard offer (MP Husky, 2015) | There is no standard offer | There is no standard offer | - |
Table 10: Continuation
CTM1 | CTM1 Trade Mark | RMM2 | Trade Mark RMM2 | Designation given by CTM1 | RMM2 declared corrosion resistance class according to IEC 61537 |
Cope( | There is no standard offer Just Aluminum | There is no standard offer (Cope, 2015) | There is no standard offer | There is no standard offer | - |
Techline | There is no standard offer Just Aluminium | There is no standard offer (TechLine, 2009) | There is no standard offer | There is no standard offer | - |
Tolmega( (Niedax( group)10 | Uses the trademark “Geomet(” | Geomet( 500B (Geomet( technology) | Geomet( | Not declared | ( 8 |
Tolmega( (Niedax( group)10 | Zinc+ | Unknown | Unknown | Not declared | ( 8 |
Basor(12 | There is no standard offer Aluminium in the range “Basor Trays” | There is no standard offer | There is no standard offer | There is no standard offer | - |
Niedax(13 | Uses the trademark “Geomet(” | Geomet( technology | Geomet( | There is no standard offer | - |
Niedax(13 | Aluminium | Unknown | Unknown | Unknown | - |
CTM: Cable Trunking systems Manufacturer
RMM: Raw Material Manufacturer
According to Obo Betterman ( (Double Dip) brochure: “Double Dip” process for sheet metal is still so new that it has not yet been described in standards (Obo Betterman, 2012)
A specific corrosion class is not specified in the Obo Betterman ( brochure, but it is indicated that it is superior, at equivalent thickness, to conventional hot dip galvanizing: “Dip can be classified in the highest corrosion class. In the still valid product standard DIN VDE 0639 a corrosion protection classification is described, while a revised classification will follow in the newly published IEC/EN 61537 (9:2001) (Obo Betterman, 2012).
In Mavil ( catalogue (Mavil (Gewiss group), 2015) it is indicated “A 4 time stronger coating than the HDG (Hot Dip Galvanized) - at equivalent thickness. Certified by Arcelor Mittal ( ”
According to IEC 61537 standard, Edition 3 Committee Draft (IEC (International Electrotechnical Commission), 2016).
According to Mavi ( l catalogue: “Revêtement non électrolytique de lamelles de zinc. Le revêtement est obtenu par application de lamelles de zinc et éventuellement d'aluminium avec un apport de chaleur. Cette finition est essentiellement utilisée pour la boulonnerie dédiée aux applications utilisant la finition GAC. L'aspect est gris argent. Geomet remplace Dacromet suite à l'interdiction d'utilisation du Chrome 6 en France”(Mavil (Gewiss group), 2015).
According to Legrand ( http://www.legrand.us/cablofil/tech_resources/tg-materialsandfinishes.aspx#.V3kjf1fV6i4: Geomet is a treatment based on zinc and aluminium. As it does not contain any chromium VI (hexavalent), it complies with the RoHS Directive. Offering protection equivalent to GC, it is used for small accessories and fixings which are difficult to hot dip galvanize.
According to Axelent ( technical brochure (Axelent, 2014): “Only Hot Dip galvanized will on some parts be replaced by Zinc/Nickel (DIN 50979). Zinc/Nickel is electrolytically inorganic corrosion-resistant coatings that meet most requirements for extremely corrosive environment. Zn-Ni containing 12-15% nickel in the layer and provides good corrosion protection even in thin layers. Along with a polished or black passivation can be more than 720 h (according to ISO 9227, NSS) to the base metal corrosion is achieved. Zinc/Nickel can be used together with aluminium”. In this way, a reference is made to a nickel-based coating, very little used in the sector of metallic electrical conduits.
According to Tolmega ( catalogue, for its finish Geomet ( : “Geomet components are very thin strips of zinc and aluminium into a mineral binder. This structural passivation allows a better corrosion resistance than hot-dip galvanization (saline spray test ISO 9227: 1000 hours). In the same way, for its Zinc+ finish: “This special zinc protection process allows a better corrosion resistance than hot-dip galvanization (saline spray test ISO 9227: 1500 hours). Appearance: silk finish. No droplets after drying” (Tolmega (Niedax group), 2015).
According to Oegland ( general catalogue (extract of finishes and types of materials)(Oglaend, 2016).
Basor ( just offers an aluminium cable tray range in its Basor Trays range (Basor Electric, 2015).
According to Niedax ( general catalogue, Geomet ( is used for small parts and components (Niedax, 2015).
Accelerated and field corrosion tests on ZM alloys
Accelerated and field tests description and main conclusions
Patina project (de Rincón et al., 2009). This paper presented a comparative evaluation of Al, Zn and Al-Zn coatings on carbon steel in a very aggressive coastal atmosphere in Venezuela, with high wind velocities. The main conclusion of the article was, in general, that a better behaviour is observed with zinc coatings alloyed with aluminium, in types of atmospheres with an aggressive coastal environment. TLR (thickness loss rate), for the alloy with 5% aluminium, is significantly lower than the rest of coatings in Zn (never higher than 15 µm).
Other research works (Panossian et al., 2005), arrived to similar conclusions, confirming that coatings based on zinc or zinc alloys with a high aluminium content (above 15%), only provide effective cathodic protection against corrosion, in atmospheres with a high concentration level of chlorine ions, while alloys with high zinc content, the cathodic protection acts from the beginning in all cases.
Galvatech 2011 (Schouller-Guinnet et al., 2011; Thierry et al., 2011). In this event, two-research works were introduced related to the new zinc-aluminium-magnesium alloys. Here, they performed different field tests for a period of two-years in different French environments (marine and rural).
Research works by N. Le Bozec et al. (LeBozec et al., 2012; 2013). Field corrosion tests were performed for zinc and zinc-aluminium-magnesium alloys, in three different environments (rural, urban and coastal) located in France, Austria and Germany.
Nordic Galvanizers (LeBozec et al., 2013; Nordic Galvanizers, n.d.), performed a field test in cooperation with Swerea KIMAB (Swerea Kimab, 2014) comparing black steel, hot-dip galvanized (coating thickness 68 µm), ZnAlMg materials (Zn6Al3Mg), continuous zinc coating (20 µm), stainless steel and aluminium coupons in different tunnels, exposed to splash from car traffic and reference site (marine) environments during 2 years in Sweden. Conclusions were that, in marine reference sites, for the first and the second year of exposure, ZnAlMg alloys have half the corrosion rate compared to HDG. In traffic tunnels reference sites ZnAlMg alloys showed close to 30% less corrosion rate than HDG first year exposure and equal results for the second year.
French Corrosion Institute (Autocoat, 2013; LeBozec et al., 2013), performed a study to promote the novel ZM coating in the automotive industry through corrosion mechanism. It was also investigated:
- the relation between coating composition and microstructure in corrosion performance.
- the surface oxide on paint adhesion in order to optimize or eliminate phosphating process.
- the corrosion stability of ZM using accelerated corrosion test accepted by automotive industries (VDA 621-415, N-VDA [VDA233-102] and Volvo( STD 423-0014).
- the perforation corrosion in confined areas and on field exposure tests (Brest - Marine, Dormund - Industrial/Urban and Linz - Continental).
- the mechanical properties of formability and joining.
- the long-term corrosion properties on vehicle exposure (truck driving 2 years in Switzerland).
Different suppliers were used: Voestalpine(, Ruuki( and TKSE( comparing different coatings: Electrogalvanized (GE), Continuous HDG (GI), Galvannealed (GA) and Galfan( (Galf) (7µm thickness for all).
Conclusions were that, for open panels, in marine reference sites (Brest), ZM, after 2 years exposure, had 20-45% less corrosion rate than pre-galvanized. In urban references (Linz), ZM, after 2 years exposure had 45-65% less corrosion rate than pre-galvanized. In Industrial references (Dortmund), ZM, after 2 years exposure had 25-50% less corrosion rate than pre-galvanized. For hem flanges, in marine reference sites (Brest), ZM, after 2 years exposure, had 10-20% more corrosion rate than pre-galvanized, with only ZMA 1.5 showing a better corrosion rate. In Urban references (Linz), ZM, after 2 years exposure had much more corrosion rate than pre-galvanized. In Industrial references (Dortmund), ZM, after 2 years exposure had 0-40% more corrosion rate than pre-galvanized. Finally, CO2 content in the atmosphere had an impact on the ZM alloys: the more CO2 content in the atmosphere, the lower corrosion rate.
Arcelor Mittal Global R&D in collaboration with Peil, Ummenhofer and Partner (IPU, 2013), ordered an expert’s report to test, compare and assess the corrosion resistance of the following metallic coatings for the classification into corrosion protection classes, according to DIN 55928-8:
ZM - Magnelis® with a coating mass of 90, 120, 250 and 310 g/m2
AZ185 with a coating mass of 185 g/m2
Z275 with a coating mass of 275 g/m2
Three types of tests were performed: (1) Resistance against neutral salt spray test; (2) Resistance against condensation of water; (3) humid, sulphur dioxide atmosphere.
Conclusions were that, in NSST, ZM alloys performed better than pre-galvanized (Z) and aluminium-zinc alloys (AZ). In condensation of water test, Magnelis® provides a higher resistance compared with AZ. The humid and sulphur dioxide atmosphere test showed a better corrosion resistance effect than AZ or the pre-galvanized product.
The report recommends Magnelis® C4 for 15 years maintenance plan on open surfaces, avoiding it in confined areas, like hem flanges.
Galvatech 2015 (R&D, 2015), where Arcelor Mittal presented a work, to describe to what extent the ZM alloy, ZnMg3Al3.7, can be considered as an alternative to standard HDG zinc-based coatings or to AZ coatings for structural applications. It was focused on the high level of corrosion protection of uncoated cut edges brought by this solution and on its potential to substitute heavier HDG-Zn coatings.
Conclusions were that on Magnelis®, a cut edge self-healing phenomenon is occurring even in environments presenting very low chloride content, and in some cases, for high steel thicknesses, up to 5 mm in NSST. A similar result was achieved on outdoor field exposures in the rainfall test; however, on rural environments (chloride-free environment), self-healing phenomenon could only be observed in thinnest steel gauges.
In real exposure sites, Magnelis( showed a 2.3-3.1 better corrosion rate than pre-galvanized products.
M. Salgueiro et al. (2015a), performed a field test to check the role of electrolyte composition in the nature of corrosion products and relative corrosion rate. This brought corrosion values in three different locations: marine (France), rural (France) and urban (USA). The main conclusions were:
It is proven the better performance of ZM alloys in high chloride content environments, but its performance is lower in more neutral atmospheres, which was evidenced by tests carried out using distilled rain water as an electrolyte.
The corrosion products are key for the corrosion process and those are quite dependant on the electrolyte, as well as on the alloy composition. This has been proven after the analysis of the tests run.
The performance of ZM alloys using rain water electrolyte is much lower than using NaCl.
Tomandl and Labrenz (Tomandl & Labrenz, 2016), conducted a field test in Sweden, China and Mexico to compare the performance against corrosion between zinc and ZM alloys, in maritime environments.
Summary of results
Table 11 shows a summary of all the field tests results, while table 12 , table 12b, table 12c, table 12d, shows the accelerated tests results. Both tables contain the sources from which the results have been obtained.
The corrosivity category (C1 to CX) has been determined considering the corrosion rate of zinc finishes for the first year of exposure, according to ISO 9223 (see table 5). In those cases, in which more than one zinc coating is tested, the worst case (higher corrosivity rate) has been chosen.
Long-term corrosion
To conclude, an estimation of the long-term corrosion behaviour, based in the field tests values referred in the previous clause is presented, with the methodology categorized in 3 sections:
Grouping of the field corrosion results per corrosivity class according to ISO 9223 (C1 to CX)
Calculation of the long-term corrosion expression based in equation (1)
Corrosion graph evolution
Grouping field corrosion results per category class
Table 13 groups the different corrosion rate results for ZM alloys, by corrosivity category and differentiating values for year 1 and year 2. An average of these values has been calculated for each category. These will be the values used in the next step for the determination of the long-term corrosion function. Values in bold letters have been considered out of the normal range and they have been discarded for the calculations. Table 14 gives the same information but for ZA alloys.
Calculation of the long-term corrosion function
Corrosion function will be determined for each corrosivity category, by applying equation (1), as the general expression for corrosion processes (Chenoll-Mora et al., 2018). These are the steps followed for the determination:
Identify yearly corrosion for the first year of exposure (parameter A estimated as the average of the different corrosion values in the tests done).
Identify corrosion for the second year of exposure (estimated as the average of the different corrosion values in the tests done).
Calculate the cumulated corrosion for the second year of exposure, C (2) by adding the yearly corrosion value first year (A) and yearly corrosion value second year.
Substitute C (2) and A in equation (1) and clear n parameter.
Determine the long-term corrosion function by substituting n and A parameters in equation (1)
Graphic representation
The corrosion function will be represented graphically for a period of 100 years.
Results
Five cases have been analyzed for ZM alloys for corrosivity categories C2 to CX and one specific case for ZA alloys for corrosivity category C3. The above mentioned categories were chosen, as they provided a large number of corrosion values of our analysis. In that sense, according to table 13, there are no values for category C1 in the ZM alloys. Table 14, for ZA alloys, only indicates that category C3 has a representative amount of values to arrange the calculation. Our methodology can thus be extended to other categories in future works, when having more long-term corrosion values.
As an example of our approach, the corrosivity category C3 for ZM will be described as follows:
For C3 ZM data (table 13):
Corrosion at first year of exposure: A. This is calculated as the average of the recorded values for Y1. So, A = 0,68 µm.
Corrosion at second year of exposure. This is calculated as the average of the recorded values for Y2. It corresponds to 0,56 µm.
And with these data the following steps can already be applied:
Cumulated corrosion at second year of exposure: C (2). This is calculated by adding year corrosion value first year and year corrosion value second year:
C (2) = 0,68 + 0,56 = 1,24 µm.
Substituting C (2) and A in equation (1), n can be cleared:
C (t) = A·t n ; C (2) = A·2 n ; 1,24=0,68·2 n ; 2 n = 1,823; n = log 1,823/log2 = 0,866
And finally, the long-term corrosion expression for ZM alloys in C3 environments is determined by:
C (t) = 0,68·t 0,866 (3)
All results calculated for each case are presented in table 15. The graphic representation of long-term corrosion expression is shown in figure 10 for all ZM alloys cases and in figure 11 for the ZA alloy.
In this way, it is possible to estimate the corrosion resistance of a given ZM or ZA alloy, just by knowing its thickness. For instance, for a ZM thickness of 20 µm in a C3 environment, the approximated corrosion resistance in years is calculated, either using the graphs or applying equation (3):
20 = 0,68·t 0,866
And once resolved, t = 49,6 years
3 Results and discussions
A complete review of alloys based in Zn-Al-Mg has been made, looking at all relevant aspects of the topic: characterization, structure and composition, corrosion behaviour, standards and designations, key raw material suppliers and market offer, key electrical trunking manufacturers and market offer and finally, field tests research and accelerated corrosion tests.
The review has been complemented with a methodology to estimate the long-term corrosion resistance of these alloys. The equations calculated with this method have to be carefully taken, since they are based in the actual limited field tests values. In the next years, more field tests values will be available, and this research work should be complemented, having much more statistical values, so to have a better accuracy in this long-term calculation.
In any case, our results can serve as a reference point to project engineers and other professionals, who need to determine the best choice of material based on ZM alloys and can also evaluate the advantages and disadvantages of these new alloys compared to traditional zinc-based coatings:
ZM finishes don´t have the issue of sharp edges and aesthetics of traditional post-galvanized finish.
ZM finishes have better performance in sodium chloride-containing atmospheres, with high humidity or high condensation of water. In open panels, the corrosion rate can be up to 65% lower than for a pre-galvanized finish.
Traditional zinc-based coatings have a better performance in low CO2 content atmospheres.
In acid atmospheres or with other type of pollutants (urban or industrial areas) the performance of ZM alloys is less relevant, so, a deeper analysis has to be done. This is for instance the case of traffic tunnels, where there´s a high component of pollutants coming from vehicle combustion.
The performance of ZM finishes decreases in hem flanges for all type of environments because of the affection of the bending process to its chemical structure. This has to be considered when choosing the type of metallic accessories to use, for instance in an electrical installation.
On cut edges, self-healing phenomenon is occurring even in environments presenting very low chloride content, and in some cases for high steel thicknesses up to 5 mm in NSST. However, on rural environments, chloride-free environments, the self-healing phenomenon could be only observed in thinnest steel gauges. Thus, especial attention has to be payed when having parts with cut edges.
Alloys with a high aluminium content (above 15%), only provide effective cathodic protection against corrosion, in atmospheres with a high concentration level of chlorine ions, while alloys with high zinc content, the cathodic protection acts from the beginning in all cases.
In general, the annual corrosion rate of the second and subsequent years is lower, due to the effect of the corrosion products. That´s very important to be considered in the maintenance works. Also, in places where this corrosion products would be removed (for instance in rainy places), it has to be considered that corrosion resistance will be lower than in dry environments.
Corrosion behaviour in this type of alloys is also logarithmic. This has to be considered when choosing the right thickness of the coating and can be clearly observed in the methodology charts.
At the time of choosing the right type of coating, it is very important to consider, not only the corrosion resistance rate, but also the thickness. For instance, even ZM alloys for specific environments have better corrosion rates, the current commercialized materials only offer thicknesses up to 32 microns (430 g/m2). In the end, it is up to the project engineer to make calculations, according to the expected life duration of the installation and the corrosion rate, to properly choose the type of coating and its thickness.
4 Conclusions
The rapid development and application of alloys based on zinc-aluminium-magnesium, as an alternative to traditional zinc-based coatings in recent years, has generated a significant amount of information in all areas and in a very scattered way (composition, structure, qualities, regulations, corrosion, etc.). This dispersion hinders their correct understanding and application, especially in the face of the dilemma about its usage in front of traditional coatings. The present research work solves this problem, gathering and structuring all this information, and providing engineers and final users, a complete guideline with the key features of these type of coatings and the restrictions to use them in different types of environments.
A specific part of this review work has been focussed in corrosion, where there are many types of tests but with a high dispersion. All tests found have been consolidated and we have shown the way to calculate long-term corrosion resistance based in the results of this field tests, being applied in different corrosivity categories. Included also, is the logarithmic behaviour of the corrosion function for corrosion products.
All in all, the decision about what type of coating should be chosen, will depend on several aspects, buy mostly on the conditions of the environment, and not always is obvious that these alloys can directly substitute zinc-based coatings. A previous analysis has to be done based on the given guidelines. Finally, the thickness of the commercial products offered in the market today are also relevant, since, even the behaviour of ZM alloys can be better (slow corrosion speed), or sometimes it can be compensated by the high thickness that can be reached in traditional zinc-based coatings.