INTRODUCCIÓN
The mechanical components of internal combustion engines that use reduced crude oil as fuel present wear due to friction, fuel quality, accumulated hours of operation, abrasive action of soot particles, due to the formation of acids due to the sulfur content of the fuel, high pressures and temperatures [1]. This causes a loss of operating efficiency by increasing the clearances between static and rotating components until the maximum permissible wear is reached, which leads to the cessation of the mechanism operation [2], [3]. Several of these engine components once they have finished their useful life due to wear, are feasible to recover to their original state through additive remanufacturing processes or thermal spray processes that allow obtaining high-quality components like a new spare part thus extending the product life cycle in the circular economy [4], [5]. The layer-by-layer additive remanufacturing processes that are popularly known as 3D printing represent a new technology that achieves good results in the circular economy [6]. This technology allows maintaining the properties of the additive material as well as the substrate and does not generate oxide during process [7]. On the other hand, several thermal spray processes produce high-quality fusion depositions, with the disadvantage that they can generate oxidation, thermal stress, and even phase changes in the filler material and the substrate if the application parameters of the process are not properly controlled [8].
The following is a brief review of the literature regarding the dimensional recovery of deteriorated engine components. Rahito et al [4] conducted a study of the principles and capabilities of using metal additive technology, in the remanufacturing and refurbishment of mechanical elements that have ended their useful life due to use, to achieve product life cycle extension in the circular economy. The study determined that the applicable additive processes for remanufacturing are direct energy deposition, powder bed fusion, and cold spray technology. The researchers conclude that AM technology is being used in more and more applications due to the excellent results obtained, such as obtaining elements with similar characteristics to new spare parts [9].
Permyakov et al. [3] developed a methodology for technological design, repair, and restoration of worn mechanical elements, using methods for improving the working layer of the element. The proposed technological process for the restoration of mechanical elements is a combination of surface plastic deformation and non-abrasive antifriction finishing treatment. With the application of this procedure, it is possible to restore the elements that have suffered wear due to use, prolonging their useful life. Peng et al. [10] developed a multicriteria study for the selection and application of the remanufacturing and restoration process of crankshafts, with an approach that considers the environmental, economic, and technical property impact by applying the fuzzy technique of order preference by similarity to the ideal solution. The study concludes that the most suitable methods for crankshaft restoration from the vision of the circular economy, based on the proposed criteria, in order of application are brush electroplating, plasma spraying, plasma arc coating, and laser coating applying these restoration methods, compared to their remanufacturing counterparts represent a saving of 50 % of the total cost, 60 % of energy and up to 70 % of materials.
Yin et al. [7] carried out a systematic review of the advances in the cold sputtering process technology (CSAM) for the additive manufacturing and repair of spare parts. This study has shown that the repair or manufacturing of elements with the CSAM process does not distort the properties of the addition material, does not generate oxide deposits, and preserves the characteristics of the substrate, obtaining elements with excellent physical and mechanical properties suitable for reuse [11] However, this method has disadvantages because the quality of the deposition depends on the kinetic energy, producing the addition of the material by the plastic deformation of the raw material particles, being necessary to perform a subsequent heat treatment to improve the quality additionally, the finish has a relatively high roughness, so machining must be performed to give the final finish to the element.
Xiang et al. [12] developed a method for the determination of the optimum moment to perform active remanufacturing of a mechanical element. As an illustrative example, the oil cylinder of a concrete truck that has suffered wear due to use was used. Active remanufacturing is based on remanufacturing or refurbishing a product before discarding it. The determination of the exact moment when remanufacturing should be performed is of vital importance because it facilitates the technique, reduces costs, and minimizes waste generation in line with environmental protection. The study considered the relationship between environmental impact and manufacturing cost throughout the product life cycle. Through the method developed it was determined that the right time for active remanufacturing is when the product performance begins to degenerate.
Barragán et al. [13] carried out analytical and experimental studies to determine the most suitable combination for the application of the additive manufacturing method called laser-directed energy deposition (L-DED). The variables analyzed are deposition speed, laser power, material flow rate, and inert gas flow. Applying the best-performing combination, they fabricated thin-walled structures and solid components using an L-DED head and a powder feed system. They deposited Inconel 625 on a substrate of AISI 304 material. The best results are related to higher particle concentration, quality depositions, and optimal cooling rates. Additionally, with this combination, they obtained a significant reduction in metal powder and gas consumption. The increase in mass flow generates an increase in coating hardness, i.e. these variables are directly related.
The remanufacturing of complex geometries is very costly and requires advanced technology to achieve a reliable result. Zhao et al. [14] developed a methodology for the remanufacturing of compressor blades, which includes reverse engineering, surface modeling, recovery by additive processes with direct laser, and final machining. First, the point cloud is obtained through a scanner, then an adaptive reconstruction is performed, and the 3D digital model of the part is obtained [15], where the damage or wear can be located, with which the additive recovery process is determined through laser and subsequent milling operation with multi-axis equipment. This procedure was effective, so the results show that the applied procedure of reverse engineering, additive process with laser, and subtractive milling is an effective solution for blade remanufacturing. This methodology can be applied to the remanufacturing of other elements with complex geometries.
Shrivastava et al. [16] performed an analysis of the repair of aerospace components through the directed energy deposition (DED) process, applying Inconel 718 material. The study focused on identifying the challenges encountered in the repair process through the DED process from the geometrical and metallurgical point of view of the component. Some problems were observed, such as the existence of micropores near the edge of the repaired component and the variation of the microstructure, about the increase of the deposition height, which influences the increase of the preparation cost of the component before the final use, despite which it is concluded that the DED technique is a cost-effective alternative in the recovery of high-value elements, compared to the replacement by a new component.
The purpose of this study is to analyze and find the most suitable additive remanufacturing method to recover used spare parts that have reached the end of their useful life from Mitsubishi Man 18V 40/54 internal combustion engines, contributing to the circular economy and the environment, in addition to saving economic resources. This document presents four sections. In the first section, an exploration of the state of the art of technological advances in additive remanufacturing is carried out. In the second section, the results and methods used are presented, focusing on the mathematical models applicable to the development of the study. In the third section, the results obtained are analyzed using comparative tables and graphs. Finally, in the conclusions section, the results are mentioned, where the most adequate method is determined in technical, economic, and environmental terms to carry out the dimensional recovery of the spare parts of motors for electric power generation that have finished their useful life.
MATERIALS AND METHODS
The research is carried out in a generation plant with 6 generators driven by Mitsubishi Man 18V 40/54 internal combustion engines. Table 1 shows the main characteristics of these engines.
The mechanical components of internal combustion engines wear due to the physical operating conditions. Additionally, acid formation occurs due to the sulfur content of the fuel, which causes corrosive wear [17]. This war results in decreased operating efficiency due to increased clearances between static and rotating components. Wear occurs whenever there is rotary motion between two contacting elements [18]. In the production line, the failure of certain components can lead to a total shutdown [19]. If a potential failure is detected, it is necessary to perform maintenance immediately before triggering serious damage [20]. Optimization of maintenance plans leads to significant benefits in increasing the reliability of equipment and systems [21], [|22]. In the power industry, the reliability of power plants is crucial to meet demand [23]. To keep motors in optimal operating condition, spare parts and consumables are necessary to comply with the established maintenance plan.
Determination of the elements to be recovered
In Mitsubishi Man 18V 40/54 internal combustion engines, various elements experience wears due to the operating conditions to which they are subjected, for example, the exhaust box, the fuel cam, and the cylinder liner, among others. However, some of these element’s show wearing more frequently, which requires their replacement at relatively short intervals. Fig. 1 shows a Pareto diagram, which shows the relationship between the average period in which spare parts show non-recoverable wear and the number of elements per engine, which allows determining the spare parts to be remanufactured as part of this study:
Considering the period in hours in which the elements show wear outside the admissible range, the number of elements for each engine, and other factors such as the delivery time of the new spare part from the supplier, the elements that will be part of this study have been determined and they are the exhaust box which is the element that is installed in the cylinder head and on which the exhaust valve is mounted (See Fig. 2) and the exhaust valve which is the element that is synchronously driven by the camshaft through the rocker's arm opens and closes which allows the thermodynamic cycle of the engine to be fulfilled (See Fig. 3). These elements suffer wear in the contact surfaces between the valve and the exhaust box, it is this area that will be recovered to the original dimensions.
Remanufacturing strategies
The proposed remanufacturing method consists of several processes. In general, it starts with the collection of wear information of the element to be remanufactured through reverse engineering (RE) technology. For reverse engineering, a 3D laser scanner is used to obtain the geometry of the worn element. Through the RE system, the geometric reconstruction of the element is achieved, which is the basis for the subsequent application of the directed energy deposition (DED) method and final subtractive machining through a CAD/CAM system. Fig. 4 details the process.
Process of obtaining the 3D models of the worn elements
Internal combustion engines work at high temperatures and pressures; in the case of analysis, the fuel used has a relatively high percentage of sulfur (1 % v/v). Because of prolonged periods of operation, various components tend to experience wear, deformation, and even breakage. It is important to note that each of these defects can be unique, even if they affect identical engine elements. Therefore, the proposed remanufacturing process must have the ability to adapt to these variations by specifically addressing each type of deterioration.
Obtaining accurate geometrical data on the elements destined for remanufacturing is critical. It is therefore imperative to employ a suitable system to obtain 3D models with accurate information. In this context, it has been chosen to use a 3D laser scanner, whose specifications are detailed in Table 2, has been selected after considering several physical variables applicable to the process, such as the number of complex details of the elements and the required appreciation. Once the element has been scanned, a point cloud is generated and processed to obtain the 3D model.
Errors often occur during the scanning process of the worn elements due to light interferences, complicated geometries, and hardly visible areas, resulting in inaccurate data. Therefore, it is necessary to perform processing the data obtained by the 3D scanner through software in this case, the VX Model software has been used. The process to obtain the final 3D model is divided into some steps that are detailed below: debugging of the point cloud data, filling of unneeded details, and optimization in the use of computational resources. With this, results are obtained in less time. The 3D models obtained with the scanner are shown in Figs. 5 and 6. Fig. 5 shows the exhaust box, which is the element in which the valve is housed, the guides, the fastening system, and the valve turning system. In addition, at the top, the seating track can be seen, which is the area that contacts the exhaust valve and hermetically seals the engine combustion chamber in each cylinder. The seating track is subjected to the temperature of the combustion chamber (500 °C +- 10 %).
Fig. 6 shows the exhaust valve, which is the element that is directly exposed to the combustion chamber of the engine and performs the opening and closing in a synchronized manner through the camshaft to allow the combustion process in the chamber and subsequent evacuation of the exhaust gases to the manifold. The exhaust valve has in the upper part of the shaft, a mechanism that allows this element to rotate 10 degrees clockwise in each opening process. Like the exhaust housing, the valve is subjected to temperatures of around 500 °C and pressures between 110 and 120 kg/cm2. In the lower part of the exhaust valve is located the seating track, which is the area that contacts the exhaust box and performs the hermetic seal in the combustion chamber.
Fig. 7 shows the assembled assembly where the seating tracks and the arrangement of the housing and exhaust valve when in operation can be seen.
The exhaust valve box and valve are elements that are exposed to high temperatures and pressures, as well as chemical corrosion due to the formation of sulfuric acid (H2SO4) during the combustion process inside the chamber due to the sulfur content of the fuel. Additionally, it must be considered that the exhaust valve opens and closes 200 times per minute because the engine works at 400 revolutions per minute (RPM) continuously. Therefore, the proper selection of the filler material for the additive remanufacturing of the seating tracks is essential.
Verification of the remanufacturing feasibility of the used spare part
Fig. 8 details the process to determine the feasibility of spare parts recovery:
Remanufacturing process through Directed Energy Deposition (DED)
Directed energy deposition (DED) consists of the application of additional raw material in the form of powder or wire on a substrate. To perform this application, an energy source is placed on the substrate, which can be a laser beam, an electron beam, or a plasma. In this way, a small melt pool is formed, and the material is continuously deposited layer by layer. The deposition is performed by a computer-controlled head based on the CAD file of the element being remanufactured [24]. When the filler material enters the melt pool, it melts instantaneously increasing the volume of the liquid material. When the laser moves away, the molten material becomes solid [25]. The melting zone is protected from oxidation by shielding gas, the gas is usually argon [26].
The DED process adapts to the surface conditions of the substrate, which is an important feature for repairing components. The case and exhaust valves, which are the subject of this study, have a high manufacturing cost. Remanufacturing is a substantial cost and time savings compared to a new replacement [27]. Each of the power sources produces different characteristics in the application related to the size of the elements that can be processed, the resolution of the details, and the rate of additional material disposition. For the present study, considering the dimensional characteristics and complexity of the elements to be remanufactured, laser-directed energy deposition (L-DED) was the most suitable process.
L-DED technology is suitable for the repair of worn elements, it also minimizes erosion or future damage of the repaired part [28]. The application of additional material in powder form requires a laser power of 500 to 1000 W [24]. In the case of the application of additional material in the form of wire, the power must be higher which produces lower-quality surface finishes, this is a disadvantage, according to the study conducted through a literature review, the most appropriate is the L-DED process with addition material in powder form for this case study. The parameters for the application of the L-DED process in the additive remanufacturing of used spare parts are fundamental to obtaining successful results. These parameters include the selection and optimization of laser temperature, material deposition rate, metal powder flow rate, laser power, and beam diameter, among others. In addition, it is necessary to consider the characteristics of the material used, such as its thermal conductivity, mechanical strength, and physical properties, to determine the ideal parameters. The control of these parameters will ensure the structural integrity of the remanufactured parts and guarantee their correct operation once installed [29].
Selection of filler material
The exhaust valve is subjected to temperatures of around 500 °C, produced in the combustion chamber of the engine. The pressures at this point are in order of 110 to 120 kg/cm2. The exhaust box is subject to similar conditions. The material of manufacture of the exhaust box and valve is Nimonic 80A. This superalloy is widely used in diesel engines, especially in exhaust valves [30]. The selected filler material must meet the characteristics of compatibility with the material of manufacture of the housing and exhaust valve and must also withstand the operating conditions of these elements. The proper selection of the filler material is fundamental to avoiding difficulties due to the differences between the physical and mechanical properties of the filler material about the substrate. These differences in material properties can cause residual stress that result in cracks and spalling [31].
Two materials have been determined that meet the necessary characteristics for the operating conditions of the spare parts to be remanufactured in the present study, these are INCONEL 625 and INCONEL 718. The material Inconel 625 is used in industry in environments with temperatures ranging from -150 to over 1000 °C [32]. This alloy has excellent yield strength, fatigue, and creep resistance characteristics as well as excellent resistance to oxidation, corrosion, and frictional wear in aggressive environments. Table 6 shows the values of the properties described. Table 4 details the chemical composition of this material. Inconel 718 material has good creep resistance and increased fatigue resistance at temperatures up to 700 °C. Inconel 718 has a higher tensile strength than Inconel 625. The elongation is 8% lower than Inconel 625 [33], [34]. In addition, Inconel 718 has higher strength at elevated temperatures and has good resistance to frictional wear, hot corrosion, and fatigue. Table 3 shows the composition of this material.
In general terms, these materials show differences in density, tensile strength, corrosion resistance, oxidation resistance, thermal conductivity, coefficient of thermal expansion, and elastic modulus. Table 3 shows the results of the mechanical characteristics of tensile strength and yield strength obtained for Inconel 625 and Inconel 718 materials after having been applied on a substrate through the DED process.
From the results shown in Table 3, it can be concluded that the Inconel 718 material presents superior mechanical properties after being applied on a substrate through the DED process; however, these mechanical properties are not determinant in the case of this study according to the operating circumstances of the parts studied.
Final machining process with CAD/CAM
Through the reverse engineering process and post-processing with SOLIDWORKS design software, the three-dimensional models of the parts have been obtained, considering all their measurements and characteristics. The geometries of the elements to be repaired are shown in Figs. 9 and 10.
From these models, the machining program is generated using CAM software. Once the recovery process of the used part through L-DED has been completed, the final machining of the part is carried out. With the appropriate programming, the movements and tools needed to perform the machine are determined. Subsequently, the machining operation is carried out using computer numerical control (CNC) machine tools that perform the programmed movements. This guarantees a high level of precision and repeatability in the final machining process. Once the machine is completed, the recovered spare part to standard dimensions reaches the required specifications and is ready to move on to the verification and quality control stage [37].
RESULTS
Geometry reconstruction
The housing and exhaust valve objects of remanufacture, which are part of the internal combustion engine for electric generation. Fig. 11 shows the surfaces that show wear and that will be remanufactured.
The wear presented in the seating tracks of the housing and exhaust valve are not uniform, therefore, prior to the start of the L-DED remanufacturing process, it is necessary to carry out a process of material removal of the seating tracks with the use of a machine tool. This process is carried out following established parameters and tolerances, thus ensuring the correct repair of the seating tracks in the housing and exhaust valve. From the verification performed to fifteen valves and exhaust boxes, it is determined that on average the depth of surface imperfections is in the order of 0.1 to 0.6 mm on the entire surface of the seating track of both the exhaust box and the valve. To start the remanufacturing process, the material is initially removed using a lathe on the 0.7 mm seating tracks. This process is carried out without altering the angles of the seating tracks, thus achieving the uniformity of the substrates to be able to apply the L-DED process in series applying the same parameters to all the elements to be remanufactured. Fig. 12 shows the surfaces of the seating tracks of the valve (a) and housing (b) respectively.
Remanufacturing of the elements with L-DED
The L-DED process, according to the present study represents the most suitable additive remanufacturing technique in contrast to conventional techniques and also uses the precision of a laser to deposit filler material on a substrate, in this case, Inconel 625. The precision of the laser for the deposition of material in powder form generates a uniform microstructure with improved properties, which makes L-DED a technique that provides a practical and relatively inexpensive solution for the remanufacturing of worn engine parts for power generation. The remanufactured material resulting from this process achieves a high density.
Inconel 625, being an outstanding alloy of nickel, chromium, and molybdenum with good resistance to corrosion and oxidation under extreme temperature and pressure conditions, is ideal for application in the recovery of internal combustion engine exhaust valves and housings for power generation, since these elements are subjected to high pressure and temperature conditions. This material is also used in the aerospace, chemical, and energy industries due to its excellent mechanical attributes and thermal resistance. The application of Inconel 625 through the L-DED process presents a uniform microstructure, and improved properties compared to conventional remanufacturing methods. The application of Inconel 625 material through the L-DED process presents a homogeneous microstructure with superior characteristics to a conventional process. In the L-DED process, each layer is deposited perpendicular to the previous layer in a 0, 90, 0, 90 pattern, thus minimizing residual stresses.
The process in its application generates layers of about 250 µm thickness, the laser diameter is in the order of 850 µm, and the feed speed of the head is about 6.66 mm/s. The diameter of the Inconel 625 powder is between 45 to 90 µm. The overlap between each track is 25% of the width, i.e. 212.5 µm, so the lateral feed rate of each track is about 637.5 µm. The width of the exhaust box seating track is 8.7 mm and the exhaust valve is 8.0 mm. The diameter of the exhaust box seating track is 119.5 mm and the diameter of the exhaust valve seating track is 120 mm. In the case of the exhaust box, it is necessary to make 14 tracks to cover the width of the seating track and for the valve, 13 tracks should be made with the L-DED head. With the process data, taking into consideration that an initial material removal machining of 0.7 mm depth of the seating tracks will be carried out and that the remanufacturing time with the L-DED process of an exhaust box is 3943 s. The remanufacturing time with the L-DED process of an exhaust valve is 3677 sec.
Final machining
Once the machining process is finished, as part of the finishing quality check, the surface roughness is measured, which shows a value of 0.284 and 0.287 µm of average roughness Ra for the box and exhaust valve, respectively. The MITUTOYO SURFTEST SJ-210 equipment was used for this process. Fig. 13 shows the measurement process of the settling track of the exhaust box (a) and exhaust valve (b):
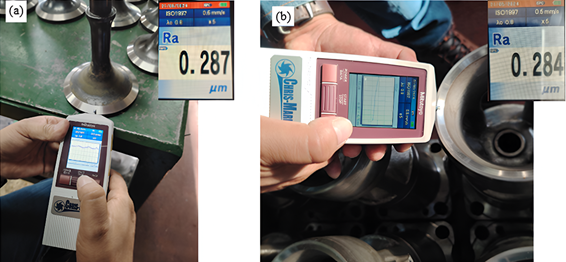
Figure 13: (a) Measurement of the roughness in the exhaust valve. (b) Measurement of the roughness in the exhaust box.
As an additional step prior to the assembly of the spare parts in the engines, a check is made of the seating between tracks with the use of the ink called Prussian Blue. The correct coupling between the tracks is verified, which should not be less than 30% between the surfaces in contact. Once this check has been carried out, the assembly of the housing - exhaust valve assembly is carried out for subsequent assembly on the engine. Fig. 14 shows the process of checking the seating (a) and the remanufactured and assembled exhaust valve housing assembly ready for installation on the engine (b):
CONCLUSION
The study presented a remanufacturing methodology for internal combustion engine components for power generation. The 3D models were obtained through a non-contact laser scanner and CAD software. For the repair process, the study of the application of L-DED technology was carried out, and then the application of final machining with machine tools was studied until the dimensions of an original spare part were obtained. The results have shown that the composite remanufacturing method, which is based on reverse engineering for the digitization of the models, the addition of material through L-DED, and final subtractive machining, is an effective solution for the dimensional recovery of worn spare parts that have ended their useful life due to use and this same methodology can be applied to other elements of engines and industry in general.
The L-DED technique allows for the restoration of used parts, achieving superior finish quality and a significant reduction in surface defects. The results also showed a decrease in remanufacturing costs compared to the purchase of new parts. The remanufacturing times with L-DED are 3943 and 3677 s for the case and exhaust valve respectively, to this must be added the time required for the preparation and final machining, however, it is demonstrated that with the application of this process, ready-to-use spare parts will be obtained in a reduced time compared to the manufacture of new elements. In terms of energy efficiency, the L-DED process uses a reduced amount of energy compared to other common techniques. Overall, the results of the L-DED remanufacturing process demonstrate its effectiveness as a cost-effective and sustainable alternative for the recovery of used spare parts.