INTRODUCCIÓN
El incremento de los procesos productivos en las industrias en los últimos años ha requerido de manera imperativa de diversas fuentes de energía, siendo la energía eléctrica la que destaca entre todas ellas, con el creciente uso de esta energía viene también el uso racional de la misma, puesto que los recursos naturales para su obtención son cada vez menores. Por lo cual el consumidor final debe transformarse en un ente activo capaz de tomar decisiones que le permita racionar el consumo de energía de manera consciente como lo mencionan López y Arias [1].
Según Poveda [2] solamente el 37 % de la energía primaria generada se convierte en energía útil, con lo cual es preciso tener en cuenta que la eficiencia energética principalmente pretende reducir y mantener el consumo de energía, reduciendo las pérdidas que se generan en toda la transformación del proceso, generando así, mejores hábitos de consumo y optimizando la tecnología para obtener mejores beneficios.
Ante este escenario O’Driscoll et al. [3] formula que es necesario adoptar medidas para concientizar sobre el uso racional de la energía eléctrica, además de las políticas de sensibilización, así como de sistemas que realicen informes de consumo que permitan el monitoreo continuo del consumo de energía y mediante un procesamiento de información, presentarla de manera simple y detallada.
En el 2014 ya se vislumbraba un futuro en el cual se use medidores inteligentes que implementen sensores de optimización de voltajes para mejorar el desempeño de la red eléctrica, todo esto con el fin de analizar y procesar datos para generar firmas de consumo [4], solo en Estados Unidos del mercado anual en redes inteligentes creció de USD. 42 millones en el 2014 a USD. 1 mil millones en el 2018, significando esto un ahorro en facturas de electricidad entre el 20 y 30 % según el tamaño del sistema [5], se espera que el mercado aumente a USD. 110.4 mil millones entre 2020 y 2026 [6].
La innovación de diseños de medidores inteligentes está determinado específicamente por el mercado, en Estados Unidos, el enfoque de los medidores se basa en la detección de fallas y el aumento de la confiabilidad de la red, mientas que en Europa se encuentra enfocado mayormente en el cumplimiento de regulaciones y la administración del consumo del usuario, siendo que para el 2020 un muestreo respecto a la implementación de medidores inteligentes espera que se instalen al menos un 80 % de los clientes del mercado europeo [7].
Fabricantes de medidores industriales, ofrecen equipos con perfiles de carga que pueden ser programables, además de medición de tiempo de uso y en ciertos modelos, protocolos de comunicación ZigBee [8] que se encuentra interconectada a la red doméstica del usuario, todo esto con el fin de obtener información que puede ser usada para programar límites de consumo de energía [9][10].
Bajo este concepto han surgido varios equipos y prototipos de medición electrónicos, basados en microcontroladores que hacen uso de la tecnología conocida como Lectura Automática del Medidor (AMR, por sus siglas en inglés) [11], este método permite integrar sensores destinados a la medición de los parámetros energéticos, ya sea de manera local o inalámbrica, para el procesamiento digital de señales como lo detallan Corral et al. [12], todo esto con el objetivo de brindar información para la toma de decisiones.
El prototipo planteado se basa en el propuesto por Xian-Chun et al. [13] el cual, es un diseño de medidor inteligente de energía estándar trifásico, completamente modular para la medición de calidad de la energía eléctrica, con despliegue de información en una pantalla, el mismo que cuenta con fuente de alimentación independiente y un microcontrolador que procesa la información y la muestra en una pantalla.
Para cotejar y tener un paralelismo en la medición de datos, el prototipo es comparado con un medidor industrial FLUKE 1735 [14], con el que se pretende calibrarlo para tener resultados con un error mínimo posible y poder utilizar el mismo como apoyo para una auditoría energética.
Una vez estructurado el prototipo y con el fin de encontrar posibles procesos donde exista un potencial ahorro energético, se realiza una auditoría energética, para así lograr una corrección de los procesos o la maquinaria que está realizando un gasto innecesario, lo que se traduce en un ahorro del costo en planillas de electricidad y mejoramiento en el funcionamiento técnico del sistema como lo explican Muñoz et al. [15]. Las acciones correctivas aplicadas conllevan en reducción de gastos por reparación de averías y correctivos no planificados.
A fin de optimizar un proceso y tener una mejora en el consumo de energía se debe realizar previamente una auditoría, la cual debe estar enfocada en identificar los fallos que requieran ser corregidos y ejecutar con ellos programas de eficiencia energética para mejorar el consumo y reducir gastos.
El contexto de auditoría energética es muy amplio y ambiguo, puesto que puede ir desde una inspección rápida para detectar pequeños problemas, hasta una investigación más detallada, con el fin de lograr los niveles de eficiencia solicitados. La auditoría energética es un proceso secuencial (ver Fig. 1) y debe cumplir varios procedimientos antes de elaborar un informe de actividades correctivas detalladas [15].
Como solución posterior a una auditoría energética, están los balances de fase y reconfiguración de alimentadores, según Ruiz et al. [16], este realiza un enfoque para minimizar los costos operativos y de inversión, basándose en la curva de carga del sistema en estudio, todo esto mediante el planteamiento a corto y mediano plazo de la operación de los equipos, obteniendo del mismo disminuciones en pérdidas de hasta un 10 %.
El objetivo del presente artículo es diseñar e implementar un medidor de energía eléctrica trifásico como herramienta para una auditoría energética, el cual permitirá realizar correcciones en focos de potencial ahorro energético, mediante el análisis de datos históricos tomados por el equipo, dichas propuestas deben estar acompañadas del consumo actual, el consumo estimado al aplicarla, la inversión necesaria y rentabilidad de la mejora.
MATERIALES Y MÉTODOS
Respecto al procesamiento de datos, se realizó mediante la tarjeta de control STM32f7 Discovery, la cual se muestra en la Fig. 2, esta tarjeta permite el desarrollo de aplicaciones debido a sus periféricos, su versatilidad y principalmente porque los procesadores de la serie STM32F7 proveen instrucciones para el procesamiento digital de señales en tiempo real.
Entre las principales aplicaciones se tiene: soporte de audio, soporte de video, conexión múltiple de sensores, seguridad y conectividad de alta velocidad; así como de la disposición de conectores Arduino para ampliar su Hardware [18].
Para el diseño del acondicionamiento del voltaje, este incluye un divisor de tensión como se observa en la Fig. 3, sabiendo que el voltaje máximo utilizado para el acondicionamiento es de 3.3 voltios pico - pico, la caída de voltaje en la resistencia RDRS no deberá sobrepasar este valor.
Para el cálculo de la caída de tensión, se utilizará la Ecuación 1 correspondiente a un divisor de tensión
Donde VRDRS es la caída de tensión en la resistencia RDRS (se asume 3.3 V, el valor máximo que puede medir el conversor AD del sistema microprocesador), VMAX es el voltaje máximo que se podrá medir (se asume 373.35 V, el voltaje pico-pico de la red eléctrica con un margen del 10 % en caso de sobre voltaje), RDR es la primera resistencia del divisor (se asume 120 kΩ, valor comercial de resistencia), RDRS es la segunda resistencia del divisor de tensión y en donde se realizará la medición.
Para calcular RDRS se utiliza la Ecuación 2:
Realizando los cálculos se obtiene el valor de RDRS de 1.07 kΩ se decide utilizar una resistencia estandarizada RDRS de 1 kΩ para el circuito.
El cálculo de la potencia se calcula mediante la Ecuación 3.
Con lo cual se obtiene que la disipación de la resistencia dada por RDR con un valor de 0.12 W y por RDRS es de 0.001 W. Se ha elegido resistencias de 1/4 de vatio al 1 % de tolerancia.
Para minimizar el ruido, se utilizará un amplificador operacional en modo diferencial con fuente externa de 1.65 V [19], el cual adecúa la salida de voltaje a los valores límites, que pueden ser leídos por el conversor AD, el circuito implementado se encuentra detallado en la Fig. 4.
Para el diseño del acondicionador de corriente, se debe calcular la resistencia de carga, la misma que es directamente proporcional a la corriente de línea, el principio de medición se puede observar en la Fig. 5.
En la Ecuación 4, se muestra la forma de calcular el valor de la resistencia .
Donde RIR es el valor de la resistencia de carga para el transformador de corriente, VMAX es el voltaje máximo que soporta el conversor AD (el valor es 3.3 V), IMax es la corriente pico - pico máximo que se entrega el transformador de corriente (100 mA para el transformador SCT-013-00) [20].
Realizando el cálculo se obtiene un valor de RIR de 33 Ω, para el diseño se utilizará una resistencia estandarizada, menor al valor calculado para obtener un margen de seguridad, el valor de resistencia seleccionado es de 27 𝜴.
Al igual que con el acondicionamiento de voltaje, el cálculo de la potencia se determina mediante la aplicación de la Ecuación 3, obteniendo un valor de potencia para RIR de 0.08 W, por esta razón se ha elegido resistencias de 1/4 de vatio al 1 % de tolerancia.
Como el sensor entrega valores positivos y negativos, se decide, al igual que con el acondicionamiento de voltaje, el uso de un amplificador operacional en modo diferencial, para adecuar los valores que entrega el sensor a los niveles de voltaje que trabaja el conversor AD del sistema micro procesado [19], el circuito implementado se observa en la Fig. 6.
Seleccionados los sensores y calculados algunos parámetros de resistencias y fuentes de alimentación se puede acoplar todo en un solo módulo, en la Fig. 7, se observa el diagrama de bloques del prototipo, en donde se aprecia de manera general las conexiones y distribución que tienen los módulos que conforman este equipo.
Con los acondicionamientos implementados, se establece un intervalo de tiempo de 200 ms, en el cual se tomaron 3072 datos instantáneos de voltaje y corriente, estos datos se almacenan en la tarjeta de control para ser procesados mediante la implementación de las siguientes ecuaciones:
Voltaje RMS:
Donde: 𝒗 𝑹𝑴𝑺_𝟐𝟎𝟎𝒎𝒔 es el voltaje RMS en 200 ms, 𝒗 𝒌 es el voltaje instantáneo [21].
Corriente RMS:
Donde: 𝒊 𝑹𝑴𝑺_𝟐𝟎𝟎𝒎𝒔 es la corriente RMS en 200 ms, 𝒊 𝒌 es la corriente instantánea [21].
Potencia activa:
Donde, 𝑷 𝟐𝟎𝟎𝒎𝒔 es la potencia activa en 200 ms, 𝒗 𝒌 el voltaje instantáneo, 𝒊 𝒌 la corriente instantánea [21].
Potencia reactiva:
Donde, 𝑸 𝟐𝟎𝟎𝒎𝒔 es la potencia reactiva en 200 ms, 𝒗 𝒌− 𝑵 𝟒 el voltaje instantáneo atrasado un cuarto de periodo, 𝒊 𝒌 la corriente instantánea [21].
Potencia aparente:
Donde, 𝑺 es la potencia aparente, 𝒗 𝑹𝑴𝑺 el voltaje RMS, 𝒊 𝑹𝑴𝑺 la corriente RMS [21].
El cálculo de armónicos se realiza mediante la Transformada Rápida de Fourier (FFT), para aplicar la misma, es necesario tener un número de muestras igual a una potencia de dos (2n). Por esta razón, para realizar la FFT se toma valores instantáneos de voltaje y corriente cada 3 muestras, que permite obtener 1024 valores de cada señal en 200 ms, con estos valores y con la ayuda de la FFT se realiza el cálculo de los armónicos de orden 0 al 9 de voltaje y corriente [21].
THD voltaje:
Donde, 𝑻𝑯𝑫 𝒗 es la distorsión armónica total de voltaje, 𝒗 𝒌 es la magnitud del armónico k, 𝒗 𝟏 es la magnitud del primer armónico de voltaje [21].
THD corriente:
Donde, 𝑻𝑯𝑫 𝒊 es la distorsión armónica total de corriente, 𝒊 𝒌 es la magnitud del armónico k, 𝒊 𝟏 es la magnitud del primer armónico de corriente [21].
RESULTADOS
Para comprobar la funcionalidad del prototipo, se realizaron pruebas comparando el equipo con un analizador industrial marca FLUKE, para lo cual se utilizaron cargas resistivas e inductivas conectadas a la red trifásica para adquirir diferentes niveles de corriente, además de otros parámetros necesarios.
Con el fin de minimizar errores en el prototipo con los datos obtenidos en las pruebas realizadas se obtuvieron constantes de calibración las cuales fueron agregadas a la programación del prototipo con el fin de minimizar los errores en la toma de datos. Una vez calibrado el prototipo, se compararon los datos con los obtenidos por el analizador industrial FLUKE, los cuales se pueden observar en las Tablas 1 y 2.
Se puede corroborar que después de la calibración realizada en el prototipo, el error porcentual de cada fase no supera el 0.25 % [21].
Tabla 2: Mediciones de corriente en las fases A, B y C y en el neutro, después de ser calibrado el prototipo
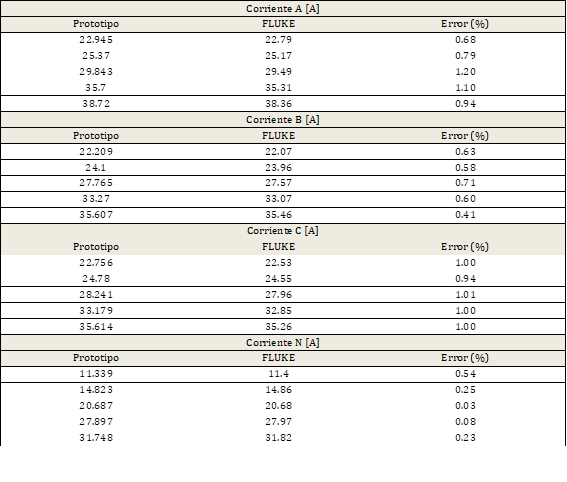
Al igual que con el voltaje, una vez realizadas las calibraciones en corriente, se puede observar que el error porcentual del prototipo no supera el 1.2 % [21].
Los valores de error obtenidos en la Tabla 1 y 2 son comparados con la norma EN 50160 [22] de calidad de energía, en la cual se establece un máximo de ± 5 % para mediciones de voltaje.
Los valores mostrados en la Tabla 3 fueron obtenidos mediante una iteración de datos, corrigiendo de esta manera el error que presenta el prototipo al momento de la medición de potencia activa y reactiva. Con los datos obtenidos por el prototipo y el analizador FLUKE, se obtiene una regresión lineal de las lecturas, de donde se adquiere constantes para la calibración, así como valores de offset que serán sumados al valor adquirido por el prototipo.
Realizadas las correcciones en la programación, se ha conectado el prototipo y el analizador FLUKE a la red trifásica para adquirir los valores de voltaje RMS de las fases A, B y C. Los valores fueron tomados simultáneamente en intervalos de tiempo de 10 minutos entre lecturas, los cuales se muestran en la Fig. 8.
Se puede apreciar en la Fig. 8, que los valores de las lecturas del prototipo y el analizador FLUKE usado como referencia son similares, teniendo valores que no superan el 0.18, 0.35 y 0.31 % de error para las fases A, B y C, respectivamente [21]. Respecto a las corrientes, al igual que con las mediciones de voltaje, los valores de corriente fueron tomados en intervalos de tiempo de 10 minutos, para estas mediciones, progresivamente se fueron colocando cargas, con el fin de aumentar el consumo y medir diferentes valores de corriente RMS.
Se puede apreciar en la Fig. 9, que los valores de las lecturas de corriente del prototipo y el analizador FLUKE usado como referencia son similares, teniendo valores que no superan el 1.38, 0.71, 1.13 y 0.53 % de error en fases A, B, C y N, respectivamente [21].
En la Fig. 10, se aprecia las lecturas de valores de potencia activa tanto en el prototipo como en el analizador FLUKE (referencial), se puede observar que el error entre ambos no supera el 4.73, 8.82 y 3.08 % de error en las fases A, B y C, respectivamente [21].
Se puede visualizar en la Fig. 11, que los valores de las lecturas de potencia aparente del prototipo y el analizador FLUKE usado como referencia son similares, teniendo valores que no superan el 2.05, 0.97 y 1.79 % de error en fases A, B y C, respectivamente [21].
Se puede apreciar en la Fig. 12, que los valores de las lecturas de potencia reactiva del prototipo y el analizador FLUKE usado como referencia son similares, teniendo valores que no superan el 7.69, 5.85 y 14.29 % de error en fases A, B y C, respectivamente [21].
En la Fig. 13, se observa las lecturas de THD de voltaje adquiridas por el prototipo y el analizador industrial FLUKE usado como referencia, en el cual se muestra que el THD de voltaje calculado no supera el 8.8, 5.75 y 8.08 % de error en las fases A, B y C, respectivamente. Así mismo, en la Fig. 14, se visualizan las lecturas de THD de corriente, en la cual se observa que el error no supera el 7.6, 4.4, 4.5 y 9.2 % de error en las fases A, B, C y N, respectivamente [21].
CONCLUSIONES
El diseño y la implementación del prototipo de medición trifásico de energía es satisfactorio, permitiendo adquirir datos que se asemejan a los adquiridos por un medidor trifásico industrial, el error en las mediciones no supera el 10 % comparándolo con el medidor FLUKE comercial utilizado en auditorias y mediciones energéticas, se puede concluir que el prototipo es muy acertado en cuanto a la adquisición de datos, con lo cual se puede ratificar que las mediciones tomadas por el prototipo desarrollado, se encuentran dentro de los parámetros y se puede utilizar el mismo para una auditoría energética.
Considerando que el prototipo se ha desarrollado con elementos de bajo costo, para poder acceder a una acreditación normada para su uso comercial, el mismo debe ser calibrado y restructurado tanto en software y hardware para poder realizar una correcta adquisición de datos, todo esto para poder cumplir con los parámetros de la Norma IEC 61000-4-30 [23] y norma EN 50160 [22].
El uso de la transformada rápida de Fourier para el análisis de los datos obtenidos fue de utilidad en la implementación del software de procesamiento de datos, es importante tener en cuenta que, para emplear esta estrategia, se debe considerar el periodo de muestreo, el número de muestras y el periodo de agregación de los datos para el procesamiento.
Respecto a una posible mejora en el sistema, se propone el uso de una FPGA como sistema microprocesado, todo esto con el objetivo de tener la posibilidad de ejecutar rutinas en paralelo y poder realizar un aumento en la frecuencia de toma de datos, con esto se puede evitar el conflicto al momento de ejecutar las rutinas.