INTRODUCCIÓN
Los plásticos juegan un papel decisivo en la modernidad, estando presentes en prácticamente la totalidad de los campos de la vida del hombre1-5. De hecho, el consumo global de plásticos en 2018 llegó a los 359 millones de toneladas métricas6. Particularmente, la producción de polietilentereftalato (PET) en el mundo en 2016 llegó a los 50.01 millones de toneladas métricas, estimándose un ascenso hasta los 87.16 millones de toneladas métricas para 20227. Por sectores de mercado, el PET se ha convertido en el material de envase más usado a nivel mundial para las botellas de agua y refrescos, representando esta aplicación el 83-84 % del volumen consumido de PET en 20188.
Estos objetos, debido a su corta vida de servicio (normalmente inferior a un año desde su manufactura), pasan rápidamente a formar parte de la corriente de desechos sólidos. La principal desventaja de los desechos plásticos proviene del elevado volumen que ocupan y de su extremadamente lenta velocidad de degradación, lo que conduce a su acumulación. Un ejemplo alarmante de esta situación es la enorme marea de desechos plásticos que flotan en los océanos, ocasionando graves daños a los ecosistemas9. La revalorización de los desechos plásticos, es decir el reciclado y la recuperación de energía, constituyen importantes alternativas para darle otra vida a estos materiales y, al mismo tiempo, mitigar su impacto ambiental10. Así, en las últimas dos décadas se ha incrementado el interés por el reciclado de los desechos plásticos, y especialmente el del polietilentereftalato. De hecho, el reciclado del PET representa uno de los ejemplos más exitosos y difundidos del proceso de reciclaje de polímeros11.
La recuperación del PET se realiza predominantemente mediante el reciclado mecánico12. Este es un proceso rápido y de un coste moderado, que permite la completa recuperación del PET y su utilización para fabricar nuevos productos dirigidos a varias aplicaciones industria- les tales como el envasado de detergentes, cosméticos, alfombras, láminas, partes de autos o en nuevas botellas plásticas.
Sin embargo, en todos los casos la aplicación del polietilentereftalato reciclado dependerá fundamentalmente de las propiedades de la resina luego de su procesado. De hecho, la mayor dificultad enfrentada por todos los transformado- res durante el reciclado del PET es su degradación. El PET es un poliéster alifático-aromático termoplástico semicristalino obtenido mediante reacciones de policondensación a partir de etilenglicol y ácido tereftálico o dimetiltereftalato13. Por esta razón, al igual que ocurre para otros poliésteres orgánicos, su reacción de obtención es reversible y puede ocurrir la despolimerización, la que es acelerada por la presencia de agua, ácidos y/o por la temperatura14. El efecto final se caracteriza por una acentuada pérdida de propiedades del polietilentereftalato reciclado. Por tanto, el control de la degradación del PET durante los procesos de transformación constituye la clave para obtener un producto de buenas prestaciones.
Varios investigadores han centrado su atención en los efectos del proceso de transformación en el PET. Sheldon15 analizó la influencia de las condiciones de extrusión (velocidad de rotación/temperatura) en la cristalización del PET, encontrando que a elevadas velocidades de extrusión existe una tendencia a degradar las cristalitas u otras fuentes de nucleación, lo que afectó la velocidad de cristalización durante un posterior calentamiento. Curtzwiler y colaboradores16 prepararon varias láminas para estudiar la influencia del contenido de PET reciclado (de 0 a 100 %) en las propiedades fina- les. Los ensayos mecánicos demostraron que el contenido de PET reciclado incorporado altera significativamente las propiedades de los mate- riales estudiados cuando eran comparados con la resina virgen. Giraldi y colaboradores17 estudiaron nanocomposites de PET reciclado con contenidos de 2.5 y 5% de montmorillonita organomodificada, obtenidos mediante mezclado en fundido en una extrusora de doble husillos corrotantes a 250 y 150 rpm. Sobre la base de la influencia tiempo de residencia, encontraron que la velocidad de rotación de husillo puede optimizarse para conducir a la completa exfoliación de la nanoarcilla y, con esto, obtener las mejores propiedades mecánicas. Sin embargo, ninguno de ellos aborda los efectos sobre la estructura molecular del PET.
Por otra parte, Matayabas y colaboradores18 al estudiar nanocomposites de PET con una organoarcilla comercial (Claytone APA), extruidos a 280 °C, encontraron una disminución de la viscosidad del PET, lo que se intensificó con el aumento del contenido de arcilla. Un resultado similar fue encontrado por Fang y colaboradores19 cuando analizaron la influencia del contenido de carbonato de calcio (CaCO3) y los parámetros de extrusión en el comportamiento de un masterbach y en fundido del PET reciclado. Al aumentar tanto el contenido de CaCO3 como la temperatura de la cámara de la extrusora de 240 a 260 °C ocurrió una disminución de la viscosidad intrínseca. No obstante, en ambos casos la presencia de los rellenos inorgánicos no deja claro cuál es la relación entre la viscosidad del PET y las condiciones de transformación.
El presente trabajo comprende el empleo de un plastómetro para realizar una simulación de un proceso de extrusión, como vía para el estudio de la influencia de las condiciones de transformación en la viscosidad del polietilenterftalato (PET) procedente de botellas plásticas de desecho.
MATERIALES Y MÉTODOS
Durante la investigación se empleó acetona (MercK, Alemania), éter (AnalaR, Inglaterra) y fenol (AnalaR, Inglaterra), todos con un 99 % de pureza. El fenol fue destilado antes ser usado, mientras que el éter y la acetona se utilizaron tal y como se recibieron. El PET empleado se tomó de la reserva de botellas plásticas de desecho almacenada en la Empresa de Recuperación de Materias Primas de Holguín. A las botellas se les retiraron las tapas, etiquetas y demás materiales extraños. Por su parte, los restos de pegamento fueron cuidadosamente eliminados utilizando acetona, éter o agua. Seguidamente, se procedió al lavado, secado preliminar en estufa Electrothermal (Inglaterra) (80 °C/ 1h) y molido de las botellas en un molino desfibrador Nossen 8255 (Alemania). Las escamas de PET se sometieron a un tamizado, tomando para los ensayos la fracción que permaneció en el tamiz de 2mm. Finalmente, se realizó un secado de las escamas de PET a vacío a 100 °C durante 24 h en una estufa Memmert (Alemania), denominado PET-R. Además, con fines comparativos, se usó granza virgen de PET (PET-G) de la firma Intercontinental Polymers (η= 0.635 - 0.665 dL/g y Tf = 255 °C) 20.
Simulación del proceso de extrusión
Para evaluar los posibles efectos derivados de la degradación ocurrida durante las etapas de extrusión del PET-R, se realizó una simulación del procesado en un plastómetro para la determinación del Índice de Fluidez (Ceast, Italia). Los experimentos se realizaron sobre la base de un diseño experimental factorial 22, como vía para obtener la mayor cantidad de información con el menor número de experimentos posible21. Como variables independientes se tomaron la temperatura y el tiempo de retención del polímero dentro de la cámara de procesamiento, mientras que como variable respuesta se tomó la viscosidad intrínseca η. Se realizó una réplica, para un total de 8 experimentos.
La Tabla 1 muestra el diseño experimental completo utilizado. El rango de temperatura estudiado corresponde a la ventana de procesamiento utilizada por los transformadores del PET, mientras que el rango de tiempo de retención se basó en un estudio previo22. Por su parte, el procesamiento estadístico se realizó utilizando el software “STAT- GRAPH”.
Viscosimetría capilar
Las medidas se efectuaron en un viscosímetro capilar Cannon Ubbelhode, termostatizado a la temperatura de 50 ± 0.1 °C en un baño de agua. Como disolvente se utilizó fenol. Se preparó una disolución madre de una concentración aproximada de 0.5 g/100 mL por cada corrida experimental. Para ello, se pesaron aproximadamente 0.5 g del polímero y se colocaron en un vaso de precipitados al que se le adicionaron 100 mL de fenol. El beaker fue sellado y se colocó en un baño termostático (Bunsen, España) a 80 °C durante 1h, realizando agitaciones periódicas hasta completa disolución. De esta disolución, se tomaron 10 mL y se vertieron en el viscosímetro Cannon Ubbelhode, dejando transcurrir 30 min. para que la solución se equilibrara a la temperatura de ensayo. El resto de disoluciones se obtuvieron in situ directamente en el viscosímetro, realizando adiciones sucesivas de disolvente puro. Seguidamente, se midieron los tiempos de flujo que tarda cada disolución y del disolvente puro en pasar entre dos marcas situadas en el viscosímetro. La relación entre el tiempo de caída de la disolución y del disolvente puro corresponde a la viscosidad relativa (ηr). Por su parte, la viscosidad específica se obtuvo restando uno a ηr.
RESULTADOS Y DISCUSIÓN
Para la determinación de viscosidad intrínseca η de cada muestra se usaron las ecuaciones de Huggins23 y Kraemer24, Ecuaciones (1) y (2) respectivamente. Se ha encontrado que estas ecuaciones son válidas a bajas concentraciones y la extrapolación gráfica de cualquiera de ellas a concentración igual a cero proporcione el mismo valor o valores muy aproximados de η.
Donde, ηsp es la viscosidad específica y kH y kK son las constantes de viscosidad de Huggins y Kraemer. En ambos casos, se requiere la determinación de sus viscosidades relativas (ηr) de una serie de soluciones, base para el cálculo de ηsp/c, la cual es extrapolada a concentración cero para obtener a η. En este procedimiento se consume una gran cantidad de tiempo, esfuerzo y materiales. Por esta razón, varios autores han propuesto ecuaciones alternativas que permiten encontrar η a partir de una sola determinación para una concentración conocida del polímero. Entre estos, Solomon y Ciuta (25) derivaron una relación para la determinación de η a partir de un solo punto a partir de la combinación de las Ecuaciones (1) y (2):
La aplicabilidad de la Ecuación (3) ha sido estudiada por varios investigadores. Elliot y colaboradores26 la emplearon para determinar η de muestras comerciales y experimentales de poli-propileno y polietileno en decalina. Por su parte, Abdel-Azim y colaboradores27 la usaron para estudiar varias muestras de polióxido de etileno y de polietilenglicol, así como poliestireno, utilizando benceno como disolvente. En ambos casos, se encontró que la ecuación de Solomon y Ciuta (Ecuación 3) proporcionó valores aceptables de η.
Los valores de η obtenidos para todas las corridas experimentales, empleando las Ecuaciones (1) a la (3) se muestran en la Tabla 2. Como puede apreciarse en los datos de la Tabla 2, los valores de η determinados según la extrapolación gráfica de Huggins y de Kraemer se encuentran en buen acuerdo, si bien los últimos son ligeramente superiores que los primeros. Por su parte, el uso de la Ecuación (3) conjuntamente con el método clásico de la determinación en, al menos, tres puntos y la extrapolación gráfica se consideran suficientes para establecer si la ecuación de Huggins es aplicable al sistema polímero-disolvente dado27. Esto es, si los valores de η obtenidos por extrapolación gráfica concuerdan con la η obtenida por la Ecuación (3) entonces la relación de Huggins es aplicable. En este caso, independientemente de las condiciones experimentales, los valores de η obtenidos de las ecuaciones propuestas por Huggins y por Solomon y Ciuta (Tabla 2) concuerdan. Esto le brinda soporte a la selección de los valores de η derivados de la ecuación de Huggins para el análisis del diseño experimental seguido en esta investigación.
Tabla 2 Datos del diseño experimental 22 elaborado para el estudio del efecto producido por los factores tiempo de retención y temperatura.
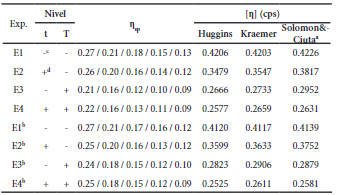
Mediante un análisis de regresión lineal aplicando el software de procesamiento estadístico STATGRAPH se obtuvo la siguiente ecuación del modelo ajustado: η=0.325875-0.058025A-0.02015B+0.01185AB (4)
Donde A corresponde a los valores de temperatura en °C, B al tiempo en minutos y la multiplicación AB corresponde a la interacción de ambos factores.
Por su parte, la Tabla 3 muestra el análisis de varianza (ANOVA) para η. En ella se particiona la variabilidad de η en piezas separadas para cada uno de los efectos y se prueba su significancia estadística. Todos los efectos que tengan un valor P inferior a 0.05 son estadísticamente significativos con un nivel de confianza de un 95 %. En este caso, el tiempo, la temperatura así como la interacción entre ambos factores ejercen un efecto significativo sobre η. Además, el elevado valor encontrado del coeficiente R2 de un 99.44% indica que el modelo explica satisfactoriamente la variabilidad observada de η.
Para evaluar la influencia de cada factor estudiado en el diseño experimental se realizó la comparación de dos experimentos donde el segundo factor permaneció constante (Tabla 2). Así, la disminución de η ocasionada por el incremento de la temperatura fue del orden del 30 %, mientras que el incremento del tiempo tuvo un efecto variable. A la temperatura de 260 °C, se observó una disminución de η de un 15 % con el incremento del tiempo de residencia. Sin embargo, a 280 °C el mismo incremento de tiempo sólo ocasionó una disminución del 7 % de η.
Por su parte, en la Figura 1 se representan los valores de η para cada muestra experimental, así como también las viscosidades determinadas a muestras de granza virgen de PET (PET-G) y de las escamas de botellas de PET (PET-R) antes de ser introducidas en la cámara del plastómetro de Índice de Fluidez.
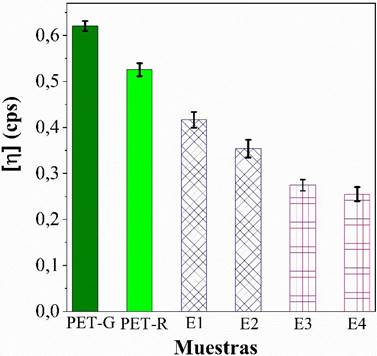
Figura 1 Valores de η determinados mediante Huggins para muestras de los experimentos 1 al 4, de granza virgen de PET (PET-G) y de las escamas de botellas de PET (PET-R).
En todos los casos, la viscosidad intrínseca de las muestras de PET que han experimentado, al menos, una etapa de procesado fue menor que la de la granza virgen (Figura. 1). Así mismo, al comparar las muestras de los experimentos 1 al 4 (todos con 2 etapas de procesado) con el PET-R (1 etapa de procesado), se puede apreciar que el incremento del número de etapas de procesado condujo a una disminución adicional de η.
De acuerdo con la ecuación de Mark-Houwink (Ecuación 4), existe una relación directa entre la viscosidad intrínseca y la masa molecular de un polímero. Por tanto, esta disminución observada de η estaría indicando una reducción significativa del tamaño molecular de las cadenas de PET, trayendo consigo un deterioro de las propiedades mecánicas del material reciclado (28).
Esta reducción del peso molecular puede tener lugar durante la transformación del PET, fundamentalmente, mediante procesos de degradación térmica, hidrolítica y/o termo-oxidativa. Las reacciones de degradación térmica e hidrolítica se han estudiado extensivamente29-31. La degradación térmica ocurre mediante un proceso iónico, en el cual, inicialmente, ocurre la transferencia de un hidrógeno β-CH seguido por la ruptura de la cadena y el origen de compuestos vinílicos y carboxílicos. También, puede ocurrir como consecuencia de un proceso de rearreglo molecular generando productos oligoméricos cíclicos. Por su parte, las reacciones de hidrólisis originan grupos terminales carboxilo e hidroxilo. Algunos investigadores29 la han catalogado como un mecanismo auto-catalítico, potenciado por el incremento en el número de grupos carboxilo terminales. Esta es una reacción extremadamente sensible32 y tiene lugar a partir de un contenido de agua ligeramente superior a 0 ppm.
En el caso de la degradación térmica oxidativa, se considera que se produce por la reacción del oxígeno con el PET a elevadas temperaturas31. El mecanismo exacto de la degradación oxidativa del PET es muy complejo y no está claro, pero se ha propuesto que transcurre por medio de radicales libres. El paso inicial de este mecanismo, conduce a la formación de hidroperóxidos en los enlaces del dietilenglicol de las cadenas del polímero. Estudios demuestran que las unidades de dietilenglicol son particularmente reactivas y se combinan con el oxígeno para formar hidroperóxidos (temperaturas por debajo de 200°C)33. A temperaturas mayores (~Tf); estos se descomponen dando lugar a una serie de reacciones que concluyen con la ruptura de la cadena. Sin embargo, este no es el único efecto ya que también traen consigo la ramificación de las cadenas y la formación del dióxido de carbono (CO2). Estos últimos efectos se explican por la descarboxilación del radical carboxilo seguida por la adición del grupo fenilo resultante a otro anillo aromático, como se muestra en la Figura 2. De ese modo, en las muestras procesadas a 280°C podría estar ocurriendo entrecruzamiento, lo que traería consigo un incremento de la viscosidad del PET, enmascarando la disminución de η derivada de las reacciones de escisión de cadena.
CONCLUSIONES
Se estudió la influencia de las condiciones de procesamiento en el polietilentereftalato reciclado, obteniéndose por primera vez la ecuación del modelo ajustado por regresión lineal para la viscosidad intrínseca η. Los factores estudiados, temperatura de procesamiento y tiempo de residencia, así como su interacción presentaron dentro del rango estudiado un efecto significativo con un 95 % de confianza. Si bien en todas las corridas experimentales se observó una disminución de la viscosidad, indicando una reducción del tamaño molecular, el incremento de la temperatura ocasionó la mayor reducción de η en aproximadamente un 30 %.
Así, la determinación de η constituye una vía útil para optimizar el proceso de reciclaje del PET. De cara a un proceso de reciclado, para minimizar los procesos de degradación durante su transformación en fundido y el consecuente deterioro de las propiedades del PET, se recomienda mantener un perfil de temperaturas que no supere los 260 °C así como mantener un tiempo de residencia igual o menor a 10 min.