Forma sugerida de citación: Pérez-Salinas, C. F.; Núnez-Núñez, D. F.; Sanaguano-Salguero, H, R. y Sánchez-Quinchuela, L. F. (2021). «Diseño y construcción de un reactor discontinuo con recirculación externa para obtener biodiésel a partir de aceite de fritura en condiciones subcríticas». Ingenius. N.° 25, (enero-junio). pp. 32-40. doi: https://doi.org/10.17163/ings.n25.2021.03.
1. Introducción
La mayoría de los países del mundo están preocupados por la reducción de las emisiones de gases de efecto invernadero, aumentar las nuevas fuentes alternativas a los combustibles fósiles y recuperar el territorio deforestado con vegetación cultivable o no cultivable [1]. Para este propósito, la producción de biocombustibles es una alternativa tangible [2], [3], [4]. Se espera que el aumento en la producción de biocombustibles no solo contribuya a la conservación del medioambiente, sino también al desarrollo económico y social de los países productores [5].
Las técnicas convencionales para producir biodiésel utilizan reactores. Un reactor químico es un dispositivo complejo en el cual la transferencia de calor y masa, la difusión y la fricción pueden ocurrir junto con la reacción química bajo dispositivos de control y seguridad. Existen diferentes tipos de reactores según la forma de obtención, el tipo de flujo interno y las fases que albergan [6], [7], [8], [9]. En general, se busca conocer el tamaño y el tipo de reactor, así como el método de operación necesario para satisfacer la obtención del producto final [10].
Uno de los parámetros importantes que se ha pretendido mejorar es el tiempo de obtención del biodiésel. En estudios previos se encuentra reportes de tiempos que van desde los 20 a los 180 minutos [11], particularmente en aceites de residuos de cocina el tiempo de obtención es de 90 minutos.
En los últimos años, la atención se ha centrado en la búsqueda de materias primas diferentes de los aceites vegetales como la soja, la palma, etc. Esto se debe principalmente al costo de obtener la materia prima, que es aproximadamente el 70 % del costo total de obtener biodiésel. [6], [7], [8]. El aceite de fritura es otra fuente de materia prima, su ventaja sobre otras materias primas es que tiene la categoría de residuos. Esta característica le da una gran viabilidad porque contribuye a la reducción de la contaminación ambiental.
En Latinoamérica, el residuo de aceite de fritura tiene potencialidad de uso como fuente primaria para la producción de biodiésel [12]. Existe una industria amplia de comida rápida y tradicional que usa el aceite de fritura, pero después de su uso se convierte en un desecho. Ejemplos como en Colombia, el 35 % de 162 millones de litros de la producción anual de aceite de cocina se convierte en residuo desechado en alcantarillas [13], España produce 150 millones de litros anuales de aceite vegetal usado [14].
Por otra parte, en los sectores industrial, educativo y doméstico, existen innumerables productos y sistemas desarrollados para cumplir una función específica. Todos ellos emplean materiales de ingeniería seleccionados para conferir un rendimiento óptimo. El proceso de obtención de un producto pasa por tres macroprocesos: diseño, fabricación y pruebas de funcionamiento. La fase de diseño comienza con la determinación de los requisitos y restricciones para llevar a cabo posteriormente un proceso de selección de material [15].
En el desarrollo ingenieril de los últimos años, se han utilizado dos métodos para la selección de materiales: el tradicional y el gráfico. El primero se basa en el conocimiento y la experiencia del ingeniero, el segundo en mapas gráficos de materiales de ingeniería organizados por sus propiedades físico-mecánicas [16].
El método gráfico se desarrolló como un soporte muy importante en la fase de concepción y desarrollo del producto [17], [18]. El método gráfico de Michael Ashby ha tenido mayor utilidad en los últimos años. Es una metodología que sirve de guía en la selección de los materiales, contemplando los atributos que se relacionan entre sí mediante tablas de selección gráfica [18], [19]. Se utilizan índices de rendimiento, estos se refieren a agrupaciones de las propiedades de los materiales con el fin de maximizarlos o minimizarlos de acuerdo con el requisito específico. Se derivan de la función objetivo del sistema y se expresan mediante ecuaciones matemáticas.
Varios autores informan el uso de la técnica de Análisis de Elementos Finitos (FEA) para el diseño y verificación de reactores químicos sometidos a modelado multifísico [20], [21], [22], [23]. En estudios, como [24], [25], [26], mencionan que el diseño paramétrico proporciona a los sistemas mecánicos la posibilidad de sintetizar, simplificar y economizar el proceso de diseño, lo que permite amplificar y explorar las posibilidades de solución. En el presente estudio, se llevó a cabo un proceso de diseño y construcción de un reactor discontinuo con recirculación externa para obtener biodiésel del aceite de fritura en condiciones subcríticas, con el propósito de reducir el tiempo de producción dentro de un marco controlado y seguro que cumpla con los requisitos de ingeniería. Para el efecto, se procedió a la selección de materiales y la verificación de la resistencia bajo el régimen de tensión utilizando la técnica de elementos finitos.
2. Materiales y métodos
Se siguió la siguiente metodología: selección de materiales, diseño mediante el análisis de elementos finitos (FEA), construcción del sistema y pruebas de funcionamiento. Se resalta el hecho que el diseño del reactor se inició con observación de diseños previos para concertarle en un diseño completamente nuevo que permita la reducción del tiempo de obtención del biodiésel.
2.1. Selección de materiales
Se utilizó el método gráfico de Ashby, con la ayuda del software educativo CES EDUPACK. Se definió la función requerida, el objetivo y las restricciones en el reactor (Tabla 1). A partir de la ley de Hooke que expresa la tensión en la zona elástica (σ) es igual al módulo de Young (E) por su deformación (€) y la fórmula de la masa (m) de acuerdo con su volumen y densidad (ρ), se determinó el índice de rendimiento (Ecuación 1).
Tomando todas las funciones y restricciones iniciales para el reactor, se obtuvo la posibilidad de 600 alternativas de material de un total de 3900 opciones. El ajuste de la selección se realizó de acuerdo con las condiciones específicas de servicio (resistencia mecánica alta, buen comportamiento a temperatura elevadas y resistente a elementos químicos), disponibilidad local del material al menor costo posible y una densidad alta que permita una estabilidad del sistema al movimiento (Figura 1).
Las variables de entrada fueron: precio máximo de 10 USD, densidad entre 5000 y 8000 kg/m3, temperatura de servicio de 500 °C, resistencia a sustancias alcalinas y sustancias con pH superior a 7, capacidad de moldeo y maquinabilidad que dan como resultado 18 posibilidades de material enmarcadas en tres grupos: aceros inoxidables austeníticos, aceros inoxidables austeníticos recocidos y aleaciones de níquel.
2.2. Análisis por elementos finitos (FEA)
Una vez realizada la selección de materiales para el reactor, se selecciona el acero AISI 304 y la aleación de níquel para ingresar en diseño experimental FEA. Por otra parte, las dimensiones para el reactor discontinuo se plantearon para que obtenga una capacidad de recirculación continua de 1 litro. Se planteó un diseño factorial completo donde se tomó en cuenta los tres factores principales (restricciones/requerimientos) del reactor; la presión, temperatura y espesor de pared en tres niveles respectivamente. También se consideró una variable categórica (material) en dos niveles. La Tabla 2 muestra el diseño experimental. Los rangos de los valores de presión y temperatura se basaron en estudios de obtención de biodiésel en condiciones subcríticas y supercríticas.
Se llevó a cabo un análisis termomecánico mediante elementos finitos utilizando un modelo 2D simétrico multiparamétrico realizado en Ansys APDL para evaluar la resistencia mecánica del reactor a las condiciones internas de presión y temperatura especificadas en el diseño de los experimentos. Se utilizó una cuarta parte de la sección transversal debido a los dos planos de simetría existentes en el modelo, Figura 2. Para los dos materiales utilizados en este estudio se definió un modelo isotrópico lineal elástico de material, sus propiedades se muestran en la Tabla 3.

Figura 2. Geometría y condiciones límite de un modelo de reactor asimétrico de un cuarto de eje para un análisis termomecánico
El modelo se discretizó con elementos cuadriláteros PLANE182 en su versión axisimétrica; el tamaño del elemento para todos los casos se estableció en 1/5 del espesor de la pared del cilindro, ya que con este valor se aseguró una convergencia menor al 5 %. El modelo consta de 1830 nodos y 1520 elementos. Las condiciones límite para el análisis termomecánico estacionario se muestran en la Figura 2.
Se realizaron dos tipos de análisis de elementos finitos: uno térmico estacionario con las condiciones de temperatura y convección especificadas para obtener los desplazamientos y esfuerzos térmicos y luego un análisis estructural estático con las condiciones de frontera indicadas de tal manera que ambos estudios se acoplaron en un análisis multifísico. La validación del modelo de elementos finitos del primer tipo de análisis se realizó mediante la teoría de recipientes a presión de paredes delgadas (TWPVt) y se evaluaron las tensiones circunferenciales o tangenciales (SZ) y longitudinales o axiales (SY), porque esta teoría no tenga en cuenta las concentraciones de tensión, tales como cubiertas, agujeros o cambios abruptos en la sección transversal. En el segundo análisis de elementos finitos se evaluó la influencia de la presión y la temperatura y se compararon los resultados de la tensión de Von Misses equivalente con la tensión de fluencia de cada material para determinar el factor de seguridad del reactor (2).
Donde:
-
σe=Esfuerzo de Von Misses
σx=Esfuerzo normal en el eje X
σy=Esfuerzo normal en el eje Y
τ2 xy=Esfuerzo cortante en el plano XY
Según la teoría de los recipientes a presión de paredes delgadas (relación diámetro interno / espesor, mayor o igual a 10), existen dos tensiones principales que son función de la presión interna (p), el radio interno (r) y el espesor de pared (t). Estas son tensiones longitudinales o axiales y circunferenciales o tangenciales, sus fórmulas de cálculo son (3) y (4) respectivamente:
Tensión longitudinal o axial (SY):
Tensión circunferencial o tangencial (SZ):
2.3. Construcción del sistema
El reactor discontinuo (Figura 3) está constituido por un tanque, un tubo de circulación y una bomba de recirculación para la agitación de los reactivos. El tanque consta de un tubo cilíndrico de 280 mm de longitud, un diámetro interno de 71 mm y un espesor de pared de acuerdo con el espesor mínimo resultado del diseño (análisis FEM). El tanque está acoplado con un tubo de 1000 mm de largo por 12 mm de diámetro y una bomba de alta presión que gira a 250 rpm para recirculación y agitación. El reactor como el tubo se fabricará del material adecuado estudiado en el apartado 2.2 y que esté disponible al menor costo. El flujo de carga (3 l/min) es impulsado por un motor de la marca Motovario TXF005. Un termopar conectado al controlador de temperatura y un manómetro para medir la presión interna del recipiente se ubicaron en la tapa del reactor. La cubierta consta de una brida con junta de teflón. En la parte superior del reactor se colocaron dos medidores de presión Problock de 0 a 150 PSI. La temperatura del reactor es registrada por un controlador de temperatura Syscon AKC CB100.
2.4. Pruebas de funcionamiento
Las pruebas se llevaron a cabo a temperaturas de 160, 180 y 200 °C, con relaciones molares de metanol-aceite de 6:1 y 9:1, porcentaje de catalizador (NaOH) de 0,5 y 1 % y para un tiempo de reacción de 5 a 10 minutos para verificar la funcionalidad del reactor discontinuo con capacidad de recirculación continua de 1 litro, alcanzando presiones de 250 psi (condición subcrítica). Para la obtención del biodiésel crudo se someterá a una destilación y lavado con agua atomizada hasta que el agua de lavado se obtenga limpia. Una vez que se eliminen los productos secundarios, el biodiésel se calentará 105 °C durante 10 minutos para secar o eliminar el agua y los residuos de metanol. Una vez enfriado, se obtuvo un volumen de biodiésel refinado.
3. Resultados y discusión
3.1. Resultados numéricos y analíticos
Los resultados del análisis estructural estático se muestran en la Tabla 4. El acero inoxidable AISI 304 y la aleación de níquel Ni 800 tienen un módulo de elasticidad y una relación de Poisson muy similares, lo que significa que los resultados del esfuerzo (SY) y circunferencial (SZ) prácticamente no varían, lo que cambia es el factor de seguridad, definido como la relación entre el esfuerzo de fluencia del material y el esfuerzo equivalente máximo alcanzado. Es importante tener en cuenta que en este análisis el factor de seguridad solo se obtuvo con las tensiones circunferenciales y longitudinales, lo que no necesariamente representa un estado tensional completo del punto analizado. Según los resultados del modelo de elementos finitos, concuerda satisfactoriamente con la teoría de los recipientes a presión de pared delgada. El error máximo fue de aproximadamente 4,2 %.

Tabla 4. Comparación de las tensiones longitudinales σl (SY) y circunferenciales σt (SZ) del análisis de elementos finitos (FEA) y la teoría de los recipientes a presión de pared delgada (TWPVt)
3.2. Influencia del reactor de presión interna y temperatura
El estudio del acoplamiento termomecánico de una cuarta parte de la sección transversal del reactor se utilizó para determinar la influencia de la presión interna y la temperatura. Las Tablas 5, 6 y 7 muestran la influencia de la presión interna para una condición de temperatura constante de 160 ºC. La leyenda del color se separó para el acero inoxidable AISI 304 y la aleación de níquel Ni800, ya que tienen un límite elástico diferente. El color rojo en la Tabla 4 significa que el material excede el límite elástico y existe la posibilidad de deformaciones permanentes que conducen a la falla del biorreactor. La escala de deformación con respecto a la condición no deformada es la misma para cada caso.
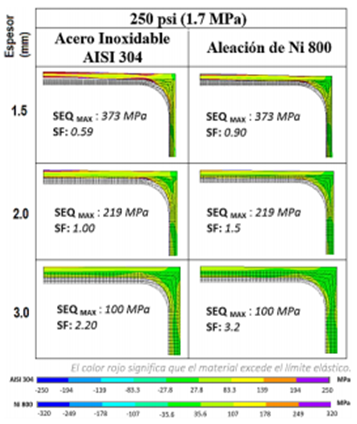
Tabla 5. Análisis numérico de la influencia de la presión interna del reactorTemperatura constante = 160 ºC y presión interna 250 psi (1.7 MPa)

Tabla 6. Análisis numérico de la influencia de la presión interna del reactorTemperatura constante = 160 ºC y presión interna 700 psi (4,8 MPa)
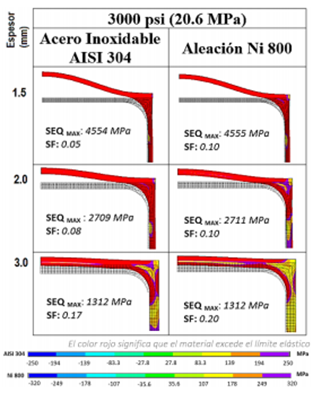
Tabla 7. Análisis numérico de la influencia de la presión interna del reactorTemperatura constante = 160 ºC y presión interna 3000 psi (20,6 MPa)
El análisis de elementos finitos muestra resultados similares de tensión equivalente de Von Misses para ambos materiales, debido a que el módulo de elasticidad y la relación de Poisson son muy similares; sin embargo, los factores de seguridad son diferentes debido a que existe una diferencia entre su límite de elasticidad de alrededor de 100 MPa. El esfuerzo máximo de Von Misses alcanzado fue mayor para espesores de 1,5 mm de pared del reactor y mínimos para espesores de 3 mm. Para una presión interna de 250, 700 y 3000 psi, el esfuerzo máximo de Von Misses fue de 373, 1058 y 4555 MPa, respectivamente.
Con las condiciones del modelo de elementos finitos axisimétricos desarrollado en este estudio, se verifica que para el caso del acero inoxidable AISI 304 el diseño solo es seguro hasta condiciones subcríticas de presión de 250 psi y un espesor mínimo de 2 mm donde un factor de seguridad de 1,00 fue obtenido. El factor de seguridad se calcula como la relación entre el esfuerzo elástico del material y el esfuerzo equivalente máximo alcanzado.
Para la aleación de níquel Ni800, la presión interna se puede aumentar hasta 700 psi y un grosor de 3 mm, donde el factor de seguridad es 1,10. Para condiciones de presión interna supercrítica (3000 psi), los factores de seguridad son inferiores a 1,00 en todos los casos, lo que indica que el material tiene una probabilidad muy alta de falla. Para esta condición, la pared de espesor del reactor debe incrementarse drásticamente. Las Tablas 8, 9 y 10 muestran la influencia de la temperatura para una condición de presión interna constante de 250 psi.
Se puede verificar que para ambos materiales las tensiones equivalentes máximas tienen una variación mínima con el aumento de temperatura 160, 200 y 400 ºC; por lo tanto, en este modelo los resultados solo están influenciados por el cambio en la presión interna. Se presume debido a dos factores: el gradiente de temperatura es mínimo en la pared del reactor debido a la condición estable que se alcanza con el fluido térmico interno (biodiésel) y el flujo convectivo externo (fuego). Por otro lado, ninguna de las temperaturas alcanzadas excede las temperaturas de servicio de los materiales, 850 ºC en el caso del acero inoxidable AISI 304 y 816 ºC en la aleación de níquel Ni800. Por lo tanto, es importante desarrollar un análisis de fatiga en una próxima investigación para estimar la vida útil del reactor.
3.3. Pruebas de funcionamiento
Con el prototipo desarrollado según el apartado 2.3 y las consideraciones del análisis numérico (FEM), se procedió a la realización de las pruebas de funcionamiento en laboratorio. Una vez ejecutado el procedimiento establecido en la metodología, se obtuvo un volumen de biodiésel refinado de color amarillo transparente. Se analizaron las densidades de biodiésel (menor densidad es mejor) obtenidas tomando como referencia temperaturas de 160 °C, 180 °C y 200 °C utilizadas para la transesterificación (Figura 4). En la comparación de las medias de los resultados del biodiésel se encontraron diferencias estadísticamente significativas; la mayor densidad se dio a 200 °C (0,89 g/ml), mientras que a 160 °C y 180 °C la densidad fue de 0,88 g/ml. El tiempo de obtención del biodiésel comienza de 5 a 10 minutos, siendo estable para obtenerlo después de 8 minutos.
4. Conclusiones
El método gráfico de selección de material permite reducir el tiempo de selección del material. La gran cantidad de opciones para la fabricación de un reactor hace imprescindible la necesidad de un refinamiento en la selección al determinar las condiciones de servicio, tales como gradientes de temperatura, rangos de presión, ataques químicos, pH y consideraciones como el costo y la disponibilidad del material.
Se realizó un análisis multiparamétrico de elementos finitos simétricos en eje 2D utilizando un software Ansys APDL para evaluar la resistencia mecánica del reactor. Su análisis nos permite determinar la influencia de las variables en el comportamiento termomecánico del reactor. Los resultados muestran que el diseño solo es seguro hasta condiciones subcríticas de presión de 250 psi y un espesor mínimo de 2 mm en el caso del acero inoxidable AISI 304 donde un factor de seguridad de 1.00. En el caso de la aleación de níquel Ni800, la presión interna se puede aumentar hasta 700 psi y un espesor mínimo de 3 mm donde el factor de seguridad es 1.10. En las condiciones límite de este modelo, la temperatura no tiene influencia en el estrés equivalente de Von Misses.
En función del diámetro y la longitud de la sección tubular, se obtuvo un volumen de 38,48 cm3, que representa el 3,47 % del volumen total del reactor, por lo que se consideró insignificante. Por otro lado, el flujo de recirculación durante la operación del reactor manejado por la bomba es de 3 l/min; en tal virtud, el fluido que pasa a través de la tubería tiene un tiempo de residencia (sección cilíndrica / flujo de la bomba), igual a 0,026 min (1,6 segundos), siendo evidente el efecto del comportamiento del flujo del pistón en la sección tubular, no es significativo con respecto al proceso de reacción que ocurrió en el tanque del reactor.
A través del proceso de reacción, se observó que, a mayor temperatura, más jabón se forma, lo que aumenta la densidad del biodiésel. Sin embargo, estos valores relacionados con la densidad del biodiésel obtenido en condiciones subcríticas están dentro del estándar europeo que establece un rango mínimo de 0,86 g/ml y un máximo de 0,90 g/ml. Esta calidad de biodiésel se logró en un tiempo aproximado de 5-8 minutos.