I. INTRODUCTION
THE constant technological development seeks to satisfy the basic needs of people, in addition to improving their lifestyle (1). Therefore, it is required that the research fields prioritize the development of new technologies, which are important in the analysis of the materials used in manufacturing or as machine elements. Carbon steel encompasses steel alloys that contain carbon. Generally, the prices of carbon steels are low, compared to other alloy steels, for this reason, they are frequently utilized in industrial of manufacturing environments (2). They are resistant to heat, which makes them ideal for manufacturing, hence, carbon steels are recommended for most applications (3). AISI 8620 steel is a low alloy steel, its main components are nickel, chromium, and molybdenum, being easy to weld by common procedures. It is a steel for carburizing, increasing its hardness on the surface, although it continues to have good core toughness. It is recommended to carburize at temperatures between 900 to 930 °C and then perform oil quenching to harden (4). The importance of heat treatment is that it allows for obtaining specific mechanical properties through the use and control of temperatures and times, to heat and cool the steel (5).
Feldiorean and Tiernan (6) studied the hardening process of AISI 8620 steel obtained by Metal Injection Model (MIM). Carburizing was done under a methane-nitrogen-methanol atmosphere for 135 minutes, followed by austenitizing heating at 830 °C to quench in oil. The hardness was controlled by tempering at temperatures of 130 and 170 °C for 60 minutes. After the heat treatments, the carbon content increased from 17% to 76% with a maximum layer depth of 0.51 mm. The hardness of the cemented and tempered steel reached 63.8 HRC, decreasing to 45.6 HRC with the maximum values of time and temperature for tempering.
The wear and mechanical properties of case-hardened AISI 8620 steel produced by powder metallurgy were analyzed by Erden and Aydun (7). The specimens were carburized at 925 °C for 4 hours, reaching an increase in the ultimate stress of 138.1%, but the elongation decreased by 64.7%. The maximum thickness of the carburized coating was 42.99 µm, a layer that increases hardness and resistance. In addition, this case-hardened steel presents greater resistance to wear and abrasion.
Kumar et al. (8) analyzed the thermal and metallurgical characteristics of the surface modification of AISI 8620 steel produced due to the TIG arc process. Through a thermal process, an average hardness of 50 HRC was obtained, starting from 15 HRC of the material in its base state. The elastic modulus reached a maximum of 205 GPa and the Poisson’s radius was 0.29. The obtained characteristic and dominant microstructures were martensite and bainite, as well as a slight presence of ferrite.
Studies of the degradation in the sliding wear behavior of case-hardened AISI 8620 steel at 100 °C in non-lubricated conditions were presented by Thirugnanasambantham and Ganesh (9). Using a scanning electron microscope, delamination and debris generation were observed as the dominant wear mechanisms of carburized AISI 8620. However, for steel without heat treatment, bow formation and adhesive fragments occurred in the form of loose fine wear particles. When applying a load of 150 N, the deformation area was greater in the untreated steel, with an increase of 0.1 mm.
A review of the case-hardening temperature and mechanical qualities of low-carbon content steels was presented by Wani and Kumar (10). For AISI 8620 steel it was shown that, with a longer carburizing time, the thickness of the hardened layer also increases. The wear resistance, as well as the ultimate tensile stress, are higher when carburizing, followed by water quenching. Carburizing is a heat treatment in a hermetic controlled-atmosphere box that is responsible for introducing carbon into a solid ferrous alloy. This process is carried out by heating the metal in a carbonaceous atmosphere, with a temperature higher than the transformation temperature, and for a certain period. After carburizing, the elements are cooled to harden the carburizing layer on the surface and the nucleus does not undergo any change (11). Therefore, the purpose of this investigation is to comparatively study the surface hardness of AISI 8620 steel heat-treated by carburizing using vegetable and coking coals.
II. MATERIALS AND METHODS
Minitab is a specialized software for the Design of Experiments, for obtaining the combinations of factors and levels, and determining the number of experiments to be developed. It has been considered to heat treat the AISI 8620 steel according to the indications of the supplier’s technical sheet (4). The experimental design responds to a 42 factorial design, with four factors and two levels, which are indicated in Table I.
AISI 8620 steel was selected since it is a steel that requires carburizing because it is a material that has a lower percentage of carbon and low hardness. According to ASTM E-18 standard (12), the material to be experimented with must have a diameter of no more than 55 mm and a thickness of 10 to 16 mm.
Therefore, the dimension available in the local market, closest to the requirement is 50.4 mm (2”), a shaft that is going to be cut and machined to reach the established thickness. AISI 8620 steel was machined on a lathe to carry out processes, such as facing, to obtain a good surface quality and avoid possible reading errors in hardness tests. Figure 1 presents the result of the machined specimens and the measurement of surface roughness, following the indications of the ASTM E-18 standard, with which the standard thickness of 15 mm was established for all the specimens. Is recommended a surface finish with quality N5 equivalent to a roughness of approximately 0.4 µm.
The first step to develop the carburizing process is to put specimens inside the hermetic box, and then fill it with coal. Consequently, this box needs to be covered to introduce it into the furnace for heat treatments to increase its temperature until it reaches the austenitization phase of the AISI 8620 material, as indicated in figure 2. In this manner, the material absorbs the gases emanated by the coal (CO2), and it can increase the perlite area.
The carburizing experiments carried out were four, which had variations in temperature (880 and 950 °C), as well as in the carburizing time (6 and 8 hours). An inlet temperature of 200 °C and a holding time of 8 hours were established for all carburizing processes. The hermetic box with vegetable coal was entered into the heat treatment furnace with test specimens 1, 2, 3 and 4, until reaching the austenitization temperature of 900 °C. The procedure was repeated with the same carburizing environment for specimens 5, 6, 7 and 8, modifying the carburizing temperature to 950 °C.
The same methodology was repeated for the carburizing procedure with the hermetic box with coking coal. Test specimens 9, 10, 11 and 12 were treated until reaching a temperature of 900 °C. An austenitizing temperature of 950 °C was used for test specimens 13, 14, 15 and 16. Additionally, fiberglass wool was placed on the borders of the box to seal and retain the carburizing atmosphere.
The tempering process is required on steel to increase the surface hardness, which is obtained by heating the steel to the austenitization temperature, which is detailed in the material technical data sheet, and then it is cooled abruptly by making a temperature change. For this temperature change was utilized Durixol W25 oil, which is an oil specially manufactured for carrying out heat treatments. It has a rapid cooling characteristic since it has a property that supports high temperatures before proceeding to evaporate (13).
Was applied the direct cooling methodology, from the hermetic box, since the CO2 formed must be quickly separated from the surface, otherwise, it would act as a decarbonizer. In the case of carburizing with vegetable coal, it was difficult to control the carburizing atmosphere, more CO2 than CO is being formed (14). Tempering is a thermal procedure implemented for steels to improve their mechanical characteristics by increasing their temperature below the melting temperature. The objective of this thermal procedure is to reduce the weakness of the material by decreasing internal stresses (15). To finish the experimental stage, the measurement of surface hardness was carried out after the heat treatments, according to the ASTM E-18 standard. Figure 3 shows the specimens marked with the points where these measurements were made.
Figure 4 also shows the evidence of the values corresponding to the surface hardness of test specimens 3 and 13, which were thermochemically treated with vegetable and coking coal, respectively. A value of 58.3 and 24.5 HRC is observed for each of these specimens, which are close to the tabulated average values of 59.31 and 25.95 HRC for the carburizing with coking and vegetable coal, respectively.
III. RESULTS AND DISCUSSION
The Analysis of Variance (ANOVA) is implemented to verify the variability of each value by computing its variance. It is proposed to identify the measures that are involved in the experimental process and to determine greater surface hardness (16). Table II presents the defined levels and factors in the experiments, in addition to the obtained average hardness, based on the five measurements that the ASTM E-18 standard indicates.
After carrying out the experiments with the heat treatments and the thermochemical carburizing treatment, the external hardness calculations were made for all the specimens, which was important to carry out the validation of these obtained values. A normality test is then required by using specialized software. Figure 5a analyzes the coherence of the distribution of carburized coal coking hardness values focused on a normal distribution curve, guaranteeing that the obtained values are correct and measured adequately. For the normality study of the obtained hardness values, it considered a confidence interval of 95 %, obtaining a high probability that the real values found follow a normal distribution. Figure 5b presents the same normality test for the surface hardness by vegetable coking carburizing.
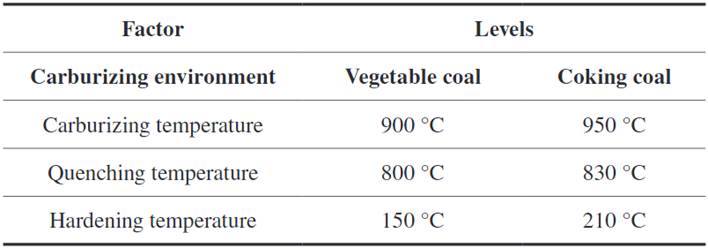
Fig. 5 Normality test of hardness measurements a) coal coking carburizing, b) vegetable coal carburizing.
Figure 6 graphically presents the main effects to identify the differences between the means. Therefore, a great significance is observed for the mean carburizing factor, considering this as the main effect. In contrast, the carburizing and tempering temperatures have a slight difference, and they come to present a significance, but with less influence. Finally, the quenching temperature between the analyzed levels does not present significance, being practically a straight line.
Figure 7 shows how each factor interacts with the others. It is confirmed that the carburizing environment is the most significant and is influenced by the carburizing and tempering temperature. Visually, a slope generated by the modification of these factors is evident.
The distribution diagram indicates the influence of the discontinuities found on the response variable. The mean value data of 2.2 was taken as a reference to verify the level of significance, hence, any factor that exceeds this limit has an influence. Figure 8 allows to observe that the carburizing environment is statistically the most significant. The carburizing and tempering temperature factors are also over the limit, therefore, they are going to be significant. Finally, the quenching temperature has not reached the limit, allowing to affirm that it does not influence surface hardness after heat treatments and thermochemical treatment.
IV. CONCLUSIONS
The application of thermochemical carburizing treatment is required before its use, to improve its mechanical properties and prolong the useful life of the elements manufactured with this steel. A thermochemical carburizing treatment has been carried out, using different elements, such as vegetable and coking coal, to generate different carburizing atmospheres and identify which of them obtains the best results. These carburizing processes were carried out for two hours at the limit values indicated by the manufacturer, from 900 to 950 °C. It is required to perform a one-stage carburizing, that is (after the carburizing time) the specimens must be immediately cooled in oil, to be quenched. Minitab was used as specialized software for the elaboration of an orthogonal arrangement matrix, considering as factors the temperatures for carburizing, quenching, and tempering, each factor with two levels. The experimental design responds to a 42 factorial design with 16 experiments. In addition, the indications of the ASTM E-18 standard for the measurement of surface hardness were considered, requiring the preparation of the material according to the established dimensions.
After the experimental measurement of hardness, the data was statistically analyzed by using an analysis of variance (ANOVA). It was defined that the quenching temperature does not influence the surface hardness, while the carburizing and tempering temperatures do have significance, with a value of 1.34% and 0.032%, respectively. The factor that most influenced this experimental study was the material used in a carburizing environment, with a value of 98.62%. From this analysis, it can be stated that vegetable coal requires control for the generation of the carburizing atmosphere, otherwise, as was the case, it acts as a decarburizer.
Therefore, coking coal can be used as an element for the generation of carburizing atmosphere since a maximum relative error of 3.86% was obtained between the experimental values and data presented by the manufacturer. Conversely, vegetable coal does not have a positive effect on the improvement of the mechanical properties of the steel, since the obtained hardness values after the heat treatments were, 25.95 HRC, on average. The manufacturer indicates that, for 150 and 210 °C, the hardness to be obtained must be between 62.5 and 60 HRC, values that do not resemble those obtained using vegetable coal as a carburizing environment.