1. INTRODUCTION
Globally, the materials used in construction are exposed to incidents such as high temperature fires (Aboutaleb et al., 2017; Humaish et al., 2020).
Fire poses a serious threat to the life of structures (Memon et al., 2019). Cases such as the Plasco Tower in Tehran was the victim of a catastrophic fire, perceiving lateral displacements and bending moments in pillars for 3 and a half hours, leading to its imminent collapse (Akbar et al., 2020; Da Silva et al., 2020). For they show the serious problem, it brings after a severe exposure to direct fire (Bo et al., 2020). Thus, above 300 °C, concrete loses almost 30 % of its original value; furthermore, in the temperature range of 400 to 800 °C, most of the initial strength is lost, and between 600 to 800 °C, the compressive strength was almost nil, as mentioned in Calmeiro and Correia (2014) and Han et al. (2020).
In the environmental aspect, the rapid increase in the amount of industrial waste is one of the main reasons that has led countries to adopt stricter environmental and sustainable policies (Sangi-Gonçalves et al., 2022). However, it is necessary to estimate the effect of the use of bricks as concrete aggregate to implement it as a component of concrete (Moreno et al., 2019). Thus, the total or partial substitution of this component is a key challenge to address the negative environmental effects and costs associated with the aggregate extraction process, without significantly affecting the properties of concrete and mortar manufactured with them (Feijoo et al., 2021). In Peru, refractory waste from the replacement of bricks from local metal smelters leads to the accumulation of these materials around cities and dumps.
In the compilation of literary information on topics related to refractory concretes, it is mentioned that they have an adequate performance at temperatures up to 1 000 °C, as expressed by Bareiro et al. (2020). However, this leads to mechanical deterioration at the structural level, due to spalling of the concrete when exposed to fire as mentioned Carrizo et al. (2020) and Ma et al. (2018). Even so, many Latin American countries persist in improving their structures in the face of these phenomena caused by various factors (Flores et al., 2018). Thus, it is important to consider studies on these issues, since concrete shows considerable reductions in strength and elasticity when subjected to earthquakes, fire or chemical interaction, as expressed by Galvez et al. (2020). Due to the fact that in Latin America, specifically in Peru, there is not much information on this type of concrete with refractory materials as a substitute for fine aggregate.
Likewise, there have been several researches that show the reuse of this material in the preparation of concrete, such as the research of Liu et al. (2018), where they tested the mechanical behavior of concrete after exposure to elevated temperatures up to 800 °C, obtaining optimum results. On the other hand, other studies used ultra-high performance fibers before and after heat treatment in a temperature range from 400 °C, 700 °C and 1 000 °C, achieving optimum residual strength in compression and flexure, being developed by Sobia et al. (2015) and Cruz et al. (2015).
According to studies by Baradaran and Nematzadeh (2017), it was concluded that workability is affected with doses of 25, 50, 75 and 100 % of refractory material, with slump ranging from 70 mm to 55 mm. On the other hand, the specific surface area of materials such as refractory brick powder is relevant when it is lower than that of cement to attribute a better workability in concrete as expressed by Sevim et al. (2023). Consequently, a level of flowability is achieved using superplasticizer (Shirani et al., 2021). On the other hand, the density reduction was affected using pumice from 12.3 % to 41.5 %, for the treatments from 25 % to 100 % pumice, respectively due to the porous structure of pumice, which translates into light weighting (Uysal et al., 2004). According to Zeghad et al. (2017), the results show that concretes made with refractory bricks based on silica-zirconium have a slightly higher density than other concretes, due to the specific mass of the brick. However, the use of recycled refractory brick aggregate shows a decrease with the increase of the maximum substitution ratio of 18 %, as expressed by Khattab and Hachemi (2021).
Within the mechanical properties such as compressive strength, concrete calcined under fire at 800 °C for 20 minutes showed a compressive strength loss rate of 66.3 % (Shui-Jun et al., 2013). The investigation of Molay et al. (2019), found that at 28 days the concrete with limestone, quartzite and granite subjected to 25 °C and 650 °C for 2 hours, it was observed that the concrete with granite had higher resistance at all temperatures compared to the concrete with quartzite and limestone (Tufail et al., 2017). In addition, the studies of Zeghad et al. (2017) observed that the concretes with alumina based on ground refractory bricks show a higher value of strength at 93 MPa, but not exceeding the standard sample of 120 MPa. Ahn et al. (2016), noted that the strength of concrete decreases as the exposure temperature increases, retaining 19.5 % and 51.7 % of the original strength after exposure to 800 °C. By substituting 50% of fine aggregate by refractory material, the residual strength of concrete exposed to 800 °C improves, but showed higher reduction values above 200 °C, as mentioned by Baradaran and Nematzadeh (2017). Also, Varona et al. (2018) clarify that lower residual strengths were obtained after exposure to higher mechanical test ages, making dehydration deterioration at elevated temperature more detrimental. Therefore, it is recommended to replace coarse and fine aggregate with 20 % refractory brick aggregate, for the use in the production of concrete at room temperature (Hachemi et al., 2023).
In this context, the objective of this research was to evaluate the influence of replacing fine aggregate with refractory bricks waste (RBR) on the compressive strength of structural concrete exposed to four different temperature ranges, every 3 time intervals, respectively. This type of concrete constitutes an environmental alternative to waste refractory bricks. On the other hand, although there are recent reviews on the use of refractory waste in construction, there is a knowledge gap because they do not highlight the effect at shorter exposure times; moreover, on the three-factor statistical analysis of variance with respect to compressive strength. Therefore, this study provides a synthesis of the results and, the possibility of establishing the use of this material in areas where the availability of natural aggregates is limited or impractical and, discuss the possibility of using this material against this uncontrolled occurrence of fire in a structure.
2. MATERIALS AND METHODOLOGY
Ordinary Portland Cement Type I
Type I ordinary Portland cement was used according to ASTM C150 (2012), as seen in Table 1, the chemical and physical analyses of the cement used are given, respectively.
Aggregates and refractory brick residue
Fine and coarse aggregate from the quarry bank of the Lambayeque region, Peru, were used. Additionally, refractory brick residue obtained from a local company was used as fine aggregate. Some of the physical properties are shown in Table 2, and the gradations of the aggregates under ASTM C136 (2001), are shown in Figure 1.
Refractory brick residue
The refractory brick residue (RBR) was obtained from the recycling process of discarded refractory bricks from a metal smelting factory (used as lining). Figure 2 shows the different sizes of the aggregates used and of the refractory material itself.
Methodology
A control mix was made for a target strength of 210 kg/cm2 with no replacement of refractory brick waste fine aggregate labeled RBR0 and five mixes with replacement levels of 10 %, 20 %, 30 %, 40 %, and 50 % RBR labeled RBR10, RBR20, RBR30, RBR40, and RBR50, respectively according to American Concrete Institute 211.1 (1993) procedures. A constant water/cement (w/c) ratio of 0.71 was used and no superplasticizer was used in any of the mixes; the proportions are shown in Table 3. The research methodology is presented in a process flow diagram in Figure 3.
The natural aggregates and refractory brick residue particles were mixed in a dry state for approximately one minute, then cement was added and mixed for an additional one minute. Half of the mixing water was added to the mixer and mixed for an additional one minute. Subsequently, the specimens were demolded after one day of processing, then poured and cured in water at room temperature by complete immersion until the day of testing under supervised conditions in accordance with the regulations (ASTM C192M, 2015). Likewise, three test bodies were considered to obtain a statistical average, corresponding to each test to be evaluated, to be subjected to curing for 28 consecutive days, respectively.
a The compressive strength of the mixtures was obtained from unheated or room temperature specimens, at 28 days.
Procedure for heating experimental samples
The specimens were placed coded in the ordered temperature ranges and according to the exposure time of study. The incineration process of the specimens was carried out under constant supervision. The artisanal kiln operated with high pressure burners, the heating capacity of the kiln was limited, the heating rate was 80 °C/min at the beginning.
The artisanal furnace was capable of reaching temperatures up to 1 250 °C, with dimensions of 5 000 mm (length) x 1 300 mm (width) x 500 mm (height), consisting of a body with refractory brick walls and a rigid steel lid with a layer of refractory sand, to avoid heat losses. The evaluation of the evolution over time of the temperature inside the furnace was measured with a thermocouple (maximum measurement of 1 200 °C).
It should be noted that more accelerated cooling (by cold water spray or water immersion) results in even lower residual properties. A quench was performed after 24 hours. After the incineration process of the modified concrete specimens, the textures, cracking and spalling of the mass of each specimen were observed, as shown in Figure 4.
3. RESULTS AND DISCUSSIONS
The workability was affected by the inclusion of RBR in the concrete mixes, since it is a material with low absorption and a surface texture different from that of sand, which caused it to cover a larger surface, thus reducing its workability. The slump result for the standard mix (RBR0) was 88.9 mm, while the slump values for RBR10, RBR20, RBR30, RBR40 and RBR50 were 88.9, 81.3, 76.2, 63.5 and 50.8 mm, respectively, the reduction range being between 0 and -42.85 %. In fact, as the RBR content increases, the slump of the mixture with refractory material decreases. In addition, the superplasticizer additive was not used in any experimental mixture, the results are shown in Table 4.
These results are similar to Baradaran and Nematzadeh (2017), workability was affected reporting similar significant reductions with slump ranging from 85, 70, 65, 60 and 55 mm as a function of replacing 0, 25, 50, 75 and 100 % refractory material in the concrete mix, respectively. Refractory brick dust is relevant when it is less than that of cement to attribute better workability in concrete (Sevim et al. (2023). Consequently, a level of flowability will be achieved by using superplasticizer (Shirani et al., 2021).
Fresh unit weight test
Table 4 shows the results of the fresh unit weight sample where its internal behavior varies significantly with the inclusion of RBR. When compared with the control specimen and the experimental specimen with 10 % RBR, the density went from 2 372 to 2 345 kg/m3, a percentage change of -1.14 %, while with the maximum dose of 50 % RBR, it suffered a percentage change of -2.45 % with respect to the standard specimen. It should be clarified that the specific gravity of the refractory material was 2.34, being lower than the specific gravity of the fine aggregate, which was 2.51, directly influencing the density of the concrete.
As mentioned in Uyal et al. (2004), when adding other types of aggregates such as pumice in replacement doses every 25 % to 100 %, its density decreases to 1 329 kg/m3 from 2 270 kg/m3, the value of the reference sample. Now using refractory brick, above 50 % substitution, the reduction in concrete density is less than 10 % (Khattab and Hachemi, 2021). The characteristics of refractory brick such as alumina-based, magensium-based or silica-zirconium-based give slightly higher density compared to conventional concrete (Zeghad et al., 2017).
Compressive strength
The compressive strength results were determined using the requirements of ASTM C39M, with specimens subjected to room temperature (Approx. 29 °C) and specimens with the effect of elevated temperatures after 28 days of curing as shown in Figure 5.
In Figure 5(a), the effect of RBR on the compressive strength subjected between 400 °C to 600 °C was observed, where less affectation was obtained in the specimens, they had a slight spalling after 5 minutes of being placed in the oven, this test group did not present abrupt explosions of the concrete mass and the cracking is faint in the external faces of each specimen. With the experimental samples of 10 % to 30 % of RBR, they represented resistance variations between 2.83 % and 12.57 %; however, with the samples of 40 % to 50 % of RBR, they suffer detachment of their mass in the middle zone of each specimen, but suffer resistance variations between 12.92 % and 8.14 % with respect to the sample RBR0. It is observed that during 15 minutes there is not much degradation of the concrete when exposed to fire, even between 800 - 1 000 °C the minimum resistance reaches 163 kg/cm2 (RBR0) and the maximum of 184 kg/cm2 (RBR40).
As shown in Figure 5(b), the results of the specimens exposed to 30 min times at different temperatures varied. The specimens with refractory material substitution are stronger than their control specimen, indeed the highest strength for specimen RBR40 was 189 kg/cm2 (13.37 %), at the temperature range 400 - 600 °C. However, with ranges between 600 - 800 °C and 800 - 1 000 °C the strength increases are between 4 % and 9 %, respectively, for specimen RBR40. Similarly, it had results to investigations on fire calcined concrete at 800 °C in 20 min, where its compressive strength loss rate was 66.3 % (Sui-Jun et al., 2013). In Figure 5(c), it was observed that the experimental specimens at higher temperature for 60 minutes, the strengths had a maximum of 71 kg/cm2 which represents 14.44 % with respect to the RBR0 sample. However, they already show a low resistance value compared to lower exposure times.
Regarding previous research on the use of aggregates as a substitute for other, Arioz (2007) mentions that this reduction was very pronounced beyond 800 °C, the effects of the w/c ratio and the type of aggregate on the relative strength of concrete decreases as the exposure temperature increases, the effect of high temperatures on concrete strength was more pronounced for concrete mixes produced by river gravel aggregate. Meanwhile, the study shows that brick refractory in replacement of fine aggregate, indicates that it performs better than conventional aggregates. In other studies, Baradaran and Nematzadeh (2017) objects that the results showed that brick refractory aggregate and aluminate cement improve the residual compressive strength to double beyond the temperature of 800 °C.
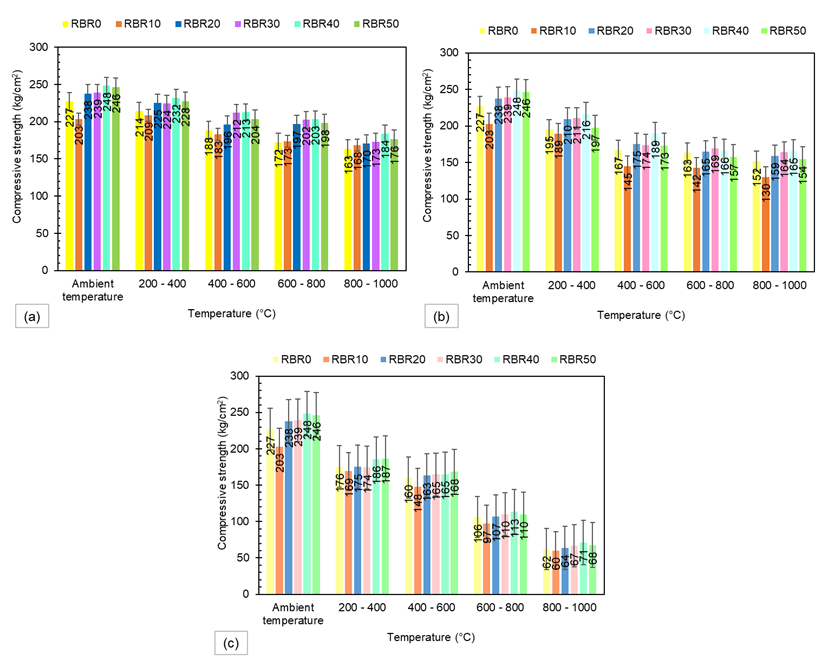
Figure 5 Effect of RBR on the compressive strength of concrete exposed to high temperatures a) at 15 minutes of breakage, b) at 30 minutes of breakage, c) at 60 minutes of breakage
Results of studies indicate that concrete with aggregates fully or partially replaced with recycled concrete aggregate (RCA) exhibits good performance under elevated temperatures and can be considered comparable to conventional concrete, furthermore disintegration was observed when concrete with RCA was heated up to 750 °C. The results of residual mechanical properties tests show some variation between concretes made with different percentages of RCA substitution as focused by the studies of Sarhat and Sherwood (2013). However, research according to Abbu et al. (2022) constant the exposure of concrete to higher temperatures has two main effects on compressive strength: when lightweight concrete mixtures were heated to 250 °C and 350 °C, their strength increased; however, when heated to 450 °C, most of the mixtures lost some of their original strength.
Three-Factor Analysis of Variance statistical model
As shown in Figure 6, we know that the p-value of significance associated with the interaction of the three factors under study, recorded a value less than 0.05, (p = 6.18 x 10-13 < 0.05), affirming that there is a significant effect of the interaction of the three factors on the variable compressive strength, as well as the best combination of levels in the factors Time (minutes), Temperature and Mixture that maximizes the compressive strength based on the visualization of the box plot and the post hoc Tukey's multiple comparison post hoc test. Meanwhile, samples: RBR0, RBR10, RBR20, RBR30, RBR40, RBR50 for the statistical analysis respectively. The analysis corresponds to mix RBR40, at room temperature °C, at 15, 30 and 60 minutes, reaching an average resistance of 248.33 kg/cm² in each combination. The Three-Factor Analysis of Variance test was applied for compliance with normality of the residuals (Shapiro Wilk, p = 0.3943 > 0.05), finding a significant effect in the interaction (p = 6.18 x 10-13 < 0.05).
4. CONCLUSIONS
This research presents the results of an experimental study conducted to evaluate the influence of refractory brick waste as a replacement of fine aggregate for the production of structural concrete against exposure to high temperatures, showing relevant findings on the compressive strength of concrete against temperature ranges and exposure times. It also promotes the generation of research due to the lack of knowledge of this type of sustainable studies applied in Peru. Based on the results obtained in this study, the following conclusions can be drawn: Workability and fresh unit weight were affected up to 50 % replacement of the refractory material. It is recommended that a superplasticizing admixture be used in future studies to improve workability so that it does not become a limiting factor in the application of the study. It is concluded that from 20, 30 and 40 % RBR in concrete exposed at 800 - 1 000 °C had significant increases on compressive strength at 28 days. However, using doses of 10 and 50 % RBR, its compressive strength decreased below that of the control sample under room temperature as well as exposure to different temperatures. As findings, it was observed that the low RBR content (up to 40 %) constitutes a technically viable alternative in the construction industry. In addition, the use of RBR has a sustainable impact to the extent that refractory brick waste is reused and overexploitation of fine aggregates from Peruvian quarries is avoided.